Researchers: OKADA Shusuke, Senior Researcher, and TAKAGI Kenta, Leader, Magnetic Powder Metallurgy Research Center
By developing rotary heat treatment technology specialized for a reduction-diffusion reaction, the researchers have developed technology for fabricating samarium-iron-nitrogen magnet powder with high coercivity of 30 kOe or more at room temperature, without the use of heavy rare earth elements, in collaboration with TDK Corporation.
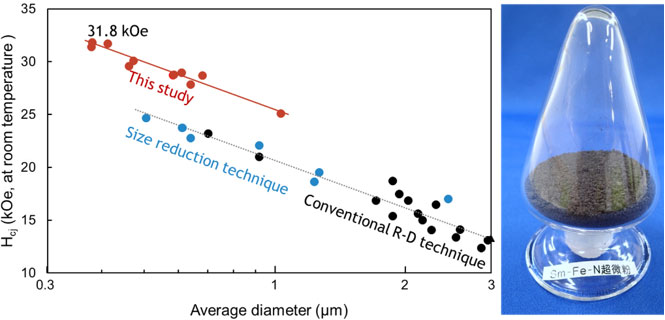
Relationship between particle diameter and room temperature coercivity of samarium-iron-nitrogen (Sm2Fe17N3) fine magnet powder synthesized using the developed process and the conventional processes (left), and photograph of the developed magnet powder (right)
The internal temperature of automobile driving motors rises to around 200 °C, which requires high residual magnetization and heat resistance. The coercivity of currently used neodymium-iron-boron magnets (neodymium magnets) decreases dramatically at high temperatures, so a heavy rare earth element, such as dysprosium and terbium, is added to provide heat resistance. However, the heavy rare earth elements are expensive and the supply is unstable, so heat-resistant high performance magnets that do not use heavy rare earth elements are demanded.
In order to increase the coercivity of samarium-iron-nitrogen magnet powder, it is necessary to achieve a uniform reduction-diffusion reaction system. Therefore, the researchers have developed rotary heat treatment technology that enables simultaneous multiphase agitation and heat treatment in an airtight space. Furthermore, they combined this technology with a previously developed particle size reduction technique and realized the high coercivity Sm2Fe17N3 powder of approximately 32 kOe at room temperature and approximately 11 kOe at 200 ºC, which is the criterion for automobile driving motor applications. This is an unprecedented level of high coercivity with rare earth-iron magnets that do not use heavy rare earth elements. As the developed magnet powder has good heat resistance, it is expected to help realize magnets with performance exceeding that of neodymium magnets in high temperature environments.
The researchers intend to enhance the dispersibility of the developed magnet powder to improve the orientation and the residual magnetization. Technology for sintering the developed magnet powder will also be developed.