The researchers have developed a technique to apply electroless plating directly to moldable intermediate materials used for manufacturing CFRP, making it possible to form a metal film with excellent adhesivity. As a result, the lightning strike resistance of CFRP has been improved greatly.
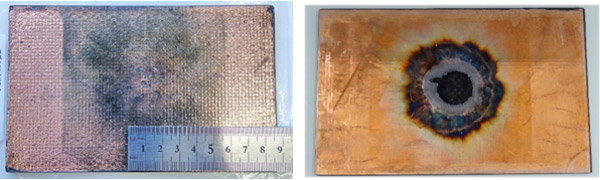 |
The result of a lightning strike test conducted on copper plating formed on CFRP (left) and the result of a lightning strike test for comparison conducted on copper foil of the same thickness affixed to CFRP (right) |
The researchers performed stabilizing treatment so as not to inactivate the plating solution on an intermediate material sheet of carbon fibers that had been impregnated with a heat curing plastic, called “prepreg”. This treatment enabled immobilization of a palladium colloid catalyst and electroless copper plating on the prepreg. CFRP with a copper plating film on the surface can be easily prepared by laminating the prepreg that has a copper plating film with unprocessed prepregs. Lightning strike tests on the fabricated CFRP showed that lightning strike resistance was greatly improved.
Lightning strike resistance is a necessity for aircraft, automobiles, the blades of wind turbines used for wind power generation, etc., which are applications of CFRP, so a metal mesh is formed on the surface of CFRP to impart conductivity against strong electric current of lightning strikes. Although attaching a metal mesh to the surface can be performed on aircraft etc., there are problems such as the complexity of the molding process and the weight increase of the materials, so there is demand for an alternative solution.
AIST plans to continue evaluating lightning strike resistance using larger impulse currents, and elucidate the mechanism of lightning strike resistance.