Yoshihiro Aiura (Leader) and Hiroshi Bando (Chief Senior Researcher), Oxide Electronics Group, the Electronics and Photonics Research Institute (Director: Satoshi Haraichi) of the National Institute of Advanced Industrial Science and Technology (AIST; President: Ryoji Chubachi) have developed a compact ultra-high-vacuum prober unit incorporating a variable-temperature thin-profile sample stage with a maximum heating temperature of 900 °C, in collaboration with Riko International Ltd. (President: Koshin Miyata).
Lately, in the research fields for innovative electronic devices based on new materials and new principles, the need for electrical property evaluation under extreme environmental conditions, including ultra-high-vacuum, ultra-low-temperature, and high-temperature, is increasing. The temperature range of the compact, sample-temperature-variable, ultra-high-vacuum prober unit developed this time ranges from -123 °C to 900 °C, while being able to make measurements under ultra-high-vacuum conditions, to the order of 10-8 Pa, and is expected to contribute to research in these fields.
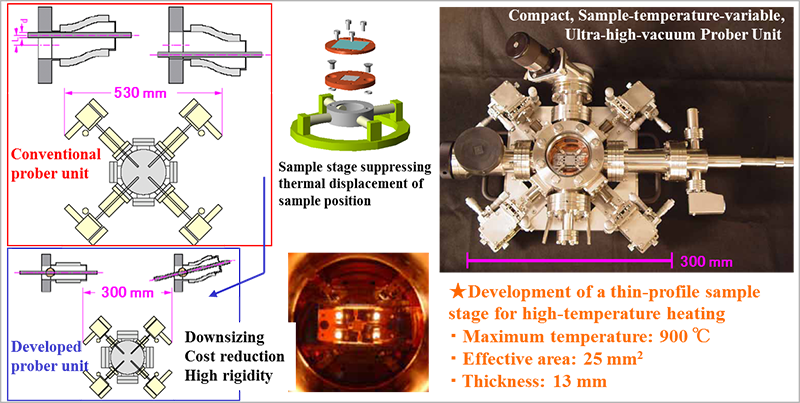 |
Features of the compact, sample-temperature-variable, ultra-high-vacuum prober unit developed this time |
Downsizing, faster processing, higher functionalities, and energy conservation are being required for information processing equipment. Integration, as well as heat generation, will inevitably increase and thermal operational conditions are becoming more demanding. Development of high-efficiency energy transformation technology and high-reliability devices that work securely under extreme conditions, such as around automobile engines, inside nuclear power plants, or in outer space, is being required. Performance evaluation under high-temperature conditions is essential for the development of electronic devices that respond to these needs, especially for the development of devices using a wide-gap semiconductor such as silicon carbide and diamonds. On the other hand, in the development of novel devices, the use of new materials different from conventional silicon materials, such as printed thin-film circuits, organic thin films, functional oxide films, metallic quantum thin wires, and superconductors, is being investigated. For their performance evaluation, there is a need to conduct operational tests quite often after prototype production under compounded extreme environmental conditions, in an ultra-high-vacuum or under a gaseous environment, and under high-temperature and ultra-low-temperature conditions, without exposing the sample to the atmosphere.
However, with conventional prober units, evaluation was usually made in the temperature range of -20 °C to 150 °C, and a high vacuum of around 10-5 Pa. Therefore, prober units that meet the requirements of today’s electronic device R&D sites, enabling performance evaluation under extreme environmental conditions, for temperatures of 500 °C or higher and ultra-high-vacuum in excess of 10-5 Pa, were required.
AIST has previously developed a compact prober unit that can measure electrical properties in ultra-high-vacuum (ultimate vacuum 3 x 10-8 Pa), high-temperature heating and ultra-low-temperature cooling (minimum 10 K, maximum 900 °C) environments. This unit utilized an indirectly heated heating mechanism using metallic filaments, but faced reliability issues when designed to have a thin-profile, coupled with the serious problem of thermionic emissions from the filament disturbing the measurement of minute currents. In the present study, with the adoption of high-temperature compatible ceramic heaters, a thin-profile sample stage with a maximum heating temperature of 900 °C has been developed by establishing a method to concurrently raise the temperature to provide sufficient heat contact and heat uniformity while guaranteeing the freedom of thermal expansion.
In conventional prober units, the probe holder was fixed to the XYZ translation mechanism that controls the stage position in three dimensions. The same probe movement mechanism is used for conventional sample-temperature-variable prober units with cooling and heating sample stages allowing the creation of high vacuum in the unit for thermal insulation by the mere addition of a bellows to maintain air-tightness while moving the probe holder. As a result, it required a bellows with a large inside diameter greater than the amount of traverse movement of the probe (direction perpendicular to the length of the probe holder) and the prober unit remained large (700 mm square or larger) and heavy (several hundred kg) to manage the suction by vacuum acting on the cross-sectional area of the bellows.
The developed compact, sample-temperature-variable prober unit uses a wobble-stick type lever system with universal joints installed at the connection with the XYZ translation mechanism, with a ball bearing installed in the entrance of the vacuum chamber to control the position of the probe holder. This allows the inside diameter of the bellows to maintain the hermetic seal of the vacuum chamber to be about the same size as that of the bearing ball and therefore, the suction by vacuum is also weak. As a result, performance levels higher than conventional units have been achieved with a significantly compact and light (300 mm square, less than 20 kg) unit at a lower cost (Fig. 1). Lightening and downsizing have enabled it to be added to a branch part of an existing sample preparation apparatus allowing the sample to be transferred without exposure to the atmosphere for in situ evaluation. In addition, since a fulcrum has been added midway along the probe holder, the rigidity (in inverse proportion to the cube of the length of the holder) has vastly increased, improving the vibration tolerance of the probe position.
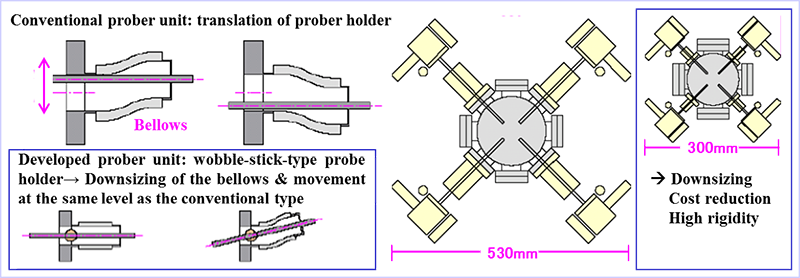 |
Figure 1 : Downsizing, lightening, and cost reduction of prober unit using wobble-stick-type probe holder |
As shown in Fig. 2, the sample stage is supported by low thermal-conductive thin-walled stainless steel tubes positioned radially from the center of the unit, to suppress thermal displacement of the sample stage position by cooling or heating. This enables continuous evaluation of thermal dependency of the device characteristics without the need to compensate for the probe position. In the case of ultra-low temperature cooling or high-temperature heating of the sample stage, heat exchange with surrounding materials by black-body radiation is an issue. This time, the shape of the shield plate surrounding the sample stage have been designed taking into consideration the radiation balance between the parts at room temperature and the sample stage, achieving both sample heating and cooling performance and ease of observation.
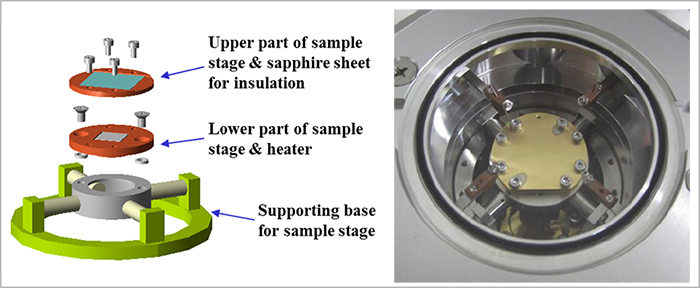 |
Figure 2 : Sample stage supporting mechanism suppressing thermal displacement
by its symmetrical structure enabling continuous measurement of thermal dependence |
In the present study, a heating mechanism reaching 900 °C incorporating high-temperature ceramic heaters was developed. However, this heater was originally designed for heating under atmospheric conditions and faced issues in heat uniformity, contact with the sample stage, thermal expansion differences, etc., when it was used in a vacuum. These issues have been overcome by coating the heater with a high melting point metal film, and by maintaining contact between the sample stage and the heater using a spring supporting mechanism. This has resulted in the development of a thin-profile sample stage heating mechanism with an effective area of 25 mm square, a thickness of 13 mm, and a maximum heating temperature of 900 °C.
In the future, a mechanism to move the sample stage horizontally will be installed to accommodate large-area wafer samples, and further advancement of compact high-vacuum prober technology will be pursued, such as enabling measurements in high-frequency regions and Hall effect measurement under ultra-high-vacuum conditions.