– A breakthrough in wiring materials for miniaturized and high-performance devices –
Kenji Hata (Prime Senior Researcher), the Nanotube Research Center (NTRC; Director: Sumio Iijima) of the National Institute of Advanced Industrial Science and Technology (AIST; President: Ryoji Chubachi), Takeo Yamada (Leader), CNT Application Team, NTRC, AIST, and Chandramouli Subramaniam (Post-Doctoral researcher), Technology Research Association for Single Wall Carbon Nanotubes (TASC; President: Naozumi Furukawa), have developed a composite of single wall carbon nanotubes (single wall CNTs) and copper that exhibits similar electrical conductivity as copper and a 100-times higher ampacity than that of copper.
Copper and gold wires have been used to supply power to electronic devices which are widely used in society. The material and cross section of a wire are factors that determine the amount of current which can pass through the wire. The shrinking volume of electronic devices has resulted in reduction in the size of wiring within these devices. This limits the amount of current that can pass through the wiring.
Utilizing organic and aqueous electroplating of copper ions, copper and single wall CNTs synthesized using the Super Growth method were made into a composite (CNT-Cu composite) for wiring. This composite is light and exhibits unprecedentedly high electrical conductivity and ampacity. In addition, the composite retains high electrical conductivity at high temperatures. Thus, this material is expected to be a wiring material in miniaturized and high-performance electronic devices.
This study was conducted as a project, the “Development of innovative carbon nanotube composite materials for a low carbon emission society” (FY2010 – 2014, Project Leader: Motoo Yumura, AIST) commissioned by the New Energy and Industrial Technology Development Organization (NEDO).
Details of this study have been published in a British scientific journal, Nature Communications, on July 23, 2013.
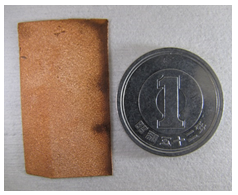 |
(Photo) : Photograph of the developed CNT-Cu composite |
Electronic devices have been undergoing progressive miniaturization to provide increased portability and enhanced functionality for applications in all scenes of society.
There have been tremendous advancements in miniaturizing electrical components such as transistors and memory devices. However, there has been very little progress in the miniaturization of wires that supply power to these components. As devices are being miniaturized, the current density flowing through wires is increasing and is reaching the limits of conventional wiring materials. The current density in devices is predicted to exceed ampacities of copper and gold in 2015, according to International Technology Roadmap for Semiconductors. In contrast, carbon-based materials exhibit high ampacities and can endure that increased current density. However, they possess poor electrical conductivity and a new wiring material with high electrical conductivity is demanded.
AIST participates in TASC and has conducted application development of single wall CNTs synthesized by the Super-Growth method with higher specific surface area than other single wall CNTs in the “Development of innovative carbon nanotube composite materials for a low carbon emission society” project (FY2010 – 2014) of NEDO. AIST has developed a conductive rubber material in an AIST-TASC joint project that aims to promote integrated materials of single wall CNTs and existing materials and their practical applications.
In the present study, the researchers have developed a composite material using CNTs, a type of carbon-based material, with high ampacity and copper, a widely used wiring material, with high electrical conductivity.
The CNT-Cu composite is fabricated by electroplating of copper. The challenge in achieving the uniform CNT-Cu composite is to efficiently penetrate and uniformly fill copper into the matrix of CNTs. Conventional aqueous electroplating of copper fails to achieve this due to the hydrophobic nature of CNTs. Furthermore, electroplating of copper using an organic solution at high current density (50-100 mA/cm2) also fails to fill copper, with preferential copper deposition on the surface of the CNT matrix. In this study, the researchers fabricated the composite material by electroplating using an organic solution of copper and subsequent aqueous electroplating.
Vertically aligned super-growth single wall CNTs are made into a horizontally aligned CNT matrix. The next step constituted the uniform deposition of copper seeds into the CNT matrix by filling the matrix with an organic solution of copper and slow electroplating at low current density (1-5 mA/cm2). As the deposited seeds are copper and copper oxide, the matrix was washed and then the copper oxide seeds are reduced to form copper seeds by heating in a hydrogen atmosphere. Next, the matrix was filled with cupper by the conventional aqueous electroplating. After this electroplating, the matrix was washed and heated in a hydrogen atmosphere. Thus, the uniform CNT-Cu composite was fabricated by forming copper seeds in the CNT matrix by slow electroplating using an organic solvent, which has an affinity with CNTs, and subsequent electroplating using aqueous solution, which has an affinity with copper (Fig. 1).
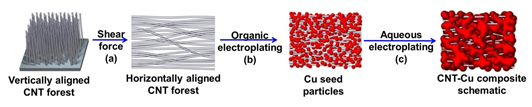 |
Figure 1 : Schematic illustration of the composite fabrication processes
Vertically aligned single wall CNTs were made into horizontally aligned CNTs,
uniform seeds of copper were formed in the CNT matrix by electroplating using an organic
solvent, and the uniform composite of copper and CNTs was fabricated by aqueous electroplating. |
CNT-Cu composite, copper and gold specimens of similar size and shape for comparison were prepared and the changes in their resistivity with current density were examined. Copper and gold specimens broke at current density of 10 x 106 A/cm2. On the other hand, the CNT-Cu composite endured up to 690 x 106 A/cm2 (Fig. 2). The ampacity is defined as the maximum current density at which the resistivity of the material is constant. This value was found to be 6.1 x 106 A/cm2 and 6.3 x 106 A/cm2 for copper and gold, respectively. In contrast, the ampacity of the CNT-Cu composite was 600 x 106 A/cm2. Thus, the developed CNT-Cu composite has ampacity that is 100-times higher than copper and gold, which are conventional wiring materials.
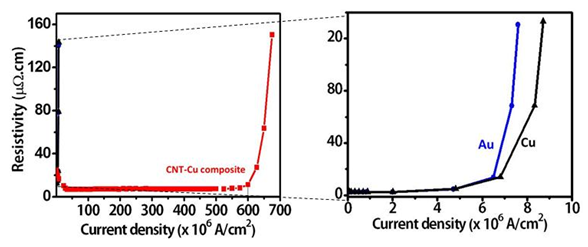 |
Figure 2 : Current density dependence of resistivity for CNT-Cu composite (red), copper (black) and gold (blue)
As the current density was increased, the shape of wire was deformed, resistivity was
increased, and finally the wire broke. The CNT-Cu composite endures up to 100-times
higher current density than copper and gold. |
Further, the room temperature electrical conductivity of the CNT-Cu composite is 4.7 x 105 S/cm and is comparable with pure copper (5.8 x 105 S/cm). The decrease in electrical conductivity of the CNT-Cu composite was less than copper and the conductivity exceeded that of copper above 80 °C and was double it at 227 °C (Fig. 3).
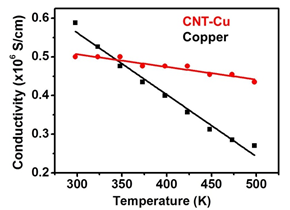 |
Figure 3 : Temperature dependence of electrical conductivity for the CNT-Cu composite (red) and copper (black)
The CNT-Cu composite retains electrical conductivity at high temperatures compared to copper. |
Fundamentally, electrical conductivity arises from weak inter-atomic bonds as in the case with metals and large ampacity demands a material with strong inter-atomic bonds as seen in carbon-based materials. Thus electrical conductivity and ampacity constitute mutually exclusive properties (Fig. 4). While the CNT matrix is filled with copper resulting in high electrical conductivity, CNTs cover copper grains, suppress the atom diffusion at the interfaces, and achieve high ampacity. In addition, the high CNT volume fraction (45 vol%) of the composite resulted in low density of 5.2 g/cm3. This value is smaller than copper (8.9 g/cm3) and gold (19 g/cm3) and the composite is expected to reduce device weight.
 |
Figure 4 : Comparison of electrical conductivity and ampacity of the CNT-Cu composite and existing materials
The CNT-Cu composite exhibits excellent electrical conductivity and ampacity. Existing materials lack that feature. |
The researchers aim to develop a large-area process and fabricate wire-shaped composite. Application development will be promoted through collaboration with companies interested in commercialization of the composite. For this purpose, the CNT-Cu composite will be exhibited at AIST Open Lab held on October 31 and November 1, 2013, at AIST Tsukuba.