- Power generation with low-temperature direct reforming of methane fuel has been demonstrated for the first time in the world -
Toshio Suzuki (Senior Researcher), Functional Integration Group (Leader: Yoshinobu Fujishiro), the Advanced Manufacturing Research Institute (Director: Norimitsu Murayama) of the National Institute of Advanced Industrial Science and Technology (AIST; President: Tamotsu Nomakuchi), Nigel Sammes (Professor) of Colorado School of Mines in the USA, and others have developed a micro solid oxide fuel cell (a micro-SOFC) with a catalyst layer that can use various hydrocarbon fuels through direct reforming. This technology allows power generation by direct reforming of methane fuel at temperatures lower than 450 °C.
Typically, SOFCs are operated at high temperatures of 700 to 1000 °C and have the highest energy-conversion efficiency among the various types of fuel cells. However, their use is limited to applications such as large and stationary power supplies. AIST has been conducting research and development of micro-SOFCs for application in high-demand, compact power supplies. For such applications, technology for using hydrocarbon fuels is of great importance. However, hydrocarbons are not sufficiently reformed at operating temperatures below 600 °C until now, making it difficult to generate electricity directly by using them as fuel. Thus, lowering the operating temperature has been a large issue.
We have developed a technology for direct reforming of a methane-steam fuel at low temperatures by forming a nanometer-scale ceria-based layer as the reforming catalyst on the inner surface of a tubular micro-SOFC with a nickel-based fuel electrode (anode). In addition, for the first time in the world, we have demonstrated the electricity generation by directly reforming the fuel at a low temperature of 450 °C. The developed cell structure allows design and application of reforming catalysts suitable for various hydrocarbon fuels. Use of the new fuel-cell technology is expected to lead to the early development of compact SOFC systems that can directly use hydrocarbon fuels at low temperatures and reduce fuel-cell startup energy.
Part of these results has been published in a British scientific journal, Energy & Environmental Science. Details will be presented at the 35th International Conference and Exposition on Advanced Ceramics and Composites, to be held from January 23 to 28, 2011 in Florida, USA.
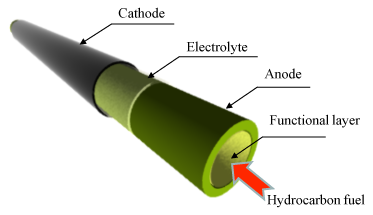 |
Figure 1: Schematic of the cell |
A fuel cell is a device that directly converts fuel to electrical energy. Fuel cells are expected to be the next-generation energy sources because of their high energy-conversion efficiency. Various types of fuel cell have been developed by using different materials; of these cells, SOFCs have the highest energy-conversion efficiency. Since SOFCs consist of ceramics and are operated at high temperatures (700 to 1000 °C), their application has been limited to large power generation systems. New applications of SOFCs are being developed in high-demand areas including distributed power sources for residential applications, power supplies for mobile electronic devices, and auxiliary power units for vehicles. Key technologies for the development of these applications are (1) a micro-SOFC modularization technology that allows quick start and (2) a multi-fuel technology that allows low-temperature operation with hydrocarbon fuels. In SOFCs with the conventional nickel-based anode, hydrocarbon fuels are not sufficiently reformed at temperatures below 600 °C, making it difficult to generate electricity directly by using hydrocarbon fuels. To downsize SOFC systems, high-performance SOFC technology needs to be developed to realize direct reforming of hydrocarbons at the anode and generate electricity at low temperatures of 500 to 600 °C.
Aiming at the application of SOFCs to small, high-demand power sources, AIST has been conducting research and development of modularization of micro-SOFCs to improve their quick-start capability and reduce component costs. In the "Ceramic Reactor Development Project (FY2005 - 2009)" of the New Energy and Industrial Technology Development Organization, AIST conducted research on the practical application of high-power, thermal-shock-resistant SOFCs that operate at temperatures below 650 °C, and we developed bundling/stacking technology for quick-start micro-SOFCs by using ceria- and zirconia-based materials. In the current study, we aimed at a new micro-SOFC that allows direct reforming of methane fuel.
The performance of SOFCs quickly falls as the operating temperature is lowered. To solve this problem, we developed a new electrode technology that enables a high power density of 1.0 W/cm2 at low temperatures of about 600 °C using hydrogen (AIST press release on September 10, 2009). However, the operating temperature needed to be further lowered to reduce the startup time and energy of SOFC systems. Compact SOFC systems that use energy-dense hydrocarbon fuels need to be developed for plactical use. However, unlike with the hydrogen fuel, the use of hydrocarbon fuels such as methane substantially reduces power-generating performance because of the low catalytic activity of the anode at temperatures below 600 °C; it is difficult for the reforming reaction to occur at these temperatures. This problem needed to be solved.
With this in mind, we have developed a technology for direct on-anode reforming by improving the tubular micro-SOFC technology developed over the years and adding a catalyst layer to the anode to allow the direct use of hydrocarbon fuels. In a conventional planar cell, an interconnect material is connected to the surface of the anode to collect electric current, making it difficult to form a fuel-reforming layer directly on the cell. Therefore, in planar fuel cell systems, the fuel reformer is located near the SOFC module. In tubular micro-SOFC systems, electric current is collected from the end surface of the anode tube, allowing a functional layer of various compositions to be added to the surface of the anode.
The developed tubular micro-SOFC uses ceria-based ceramics as the electrolyte, nickel-ceria-based ceramics as the anode, and lanthanum-cobalt-ceria-based ceramics as the air electrode (cathode). A tubular micro-SOFC 1.8 mm in diameter was fabricated by adding a nanometer-scale ceria-based reforming catalyst layer to the inner surface of the anode (Fig. 2).
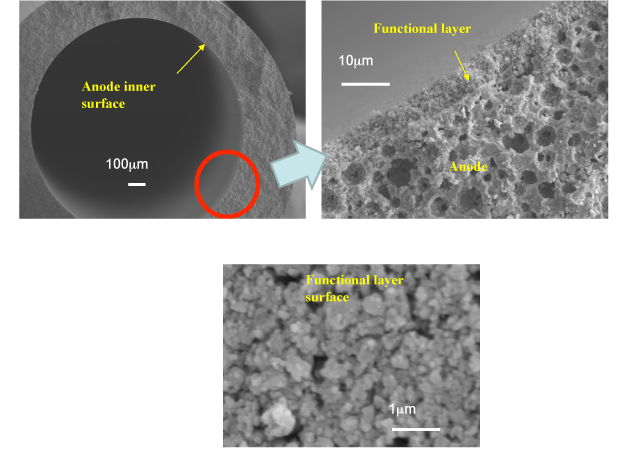 |
Figure 2: Cross-section of the tubular micro-SOFC with a nanometer-scale ceria-based reforming catalyst layer, and the surface of the catalyst layer |
Micro-SOFCs with and without a ceria-based catalyst layer as the functional catalyst were tested by using a methane-steam mixture at a temperature of about 450 °C. The micro-SOFC with the catalyst layer gave a dramatic improvement in power-generation performance compared with the micro-SOFC without the catalyst layer. For the first time in the world, we have demonstrated the electricity generation at such low temperatures (below 500 °C) by directly reforming methane-based fuel (Fig. 3). Without the ceria-based catalyst layer, in the direct use of the methane-based fuel, the voltage generated was as low as 0.6 V at about 450 °C (Fig. 3) and the power density was a few milliwatts per square centimeter. The power density with the catalyst layer increased to 0.1 W/cm2—a practical level and about 30 times the density without the catalyst. In addition, power densities of 0.4 W/cm2 and 0.45 W/cm2 were achieved at about 500 °C and 550 °C, respectively (Fig. 4). Currently, we are conducting research and development of electrodes with layers of different catalysts to achieve a power density equal to, or greater than, that for hydrogen fuel at low temperatures using various hydrocarbon fuels including methane.
In the developed micro-SOFC, the functional catalyst layer was formed by the slurry-coating process. Use of this process makes it possible to add a catalyst layer suitable for various hydrocarbon fuels. In addition, the catalyst layer and the cathode can be sintered at the same time, providing cost benefits. We believe that this new fuel-cell technology will accelerate the realization of compact SOFC systems that can directly use various hydrocarbon fuels at low temperatures.
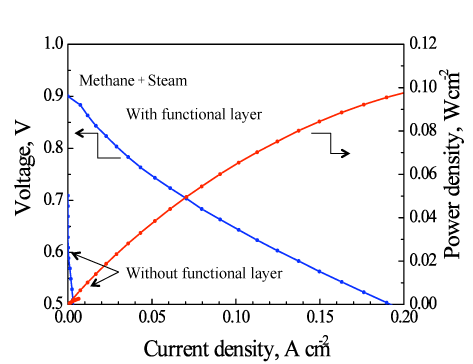 |
Figure 3: Comparison of the power generation performances of tubular micro-SOFCs with and without the catalyst layer at about 450 °C |
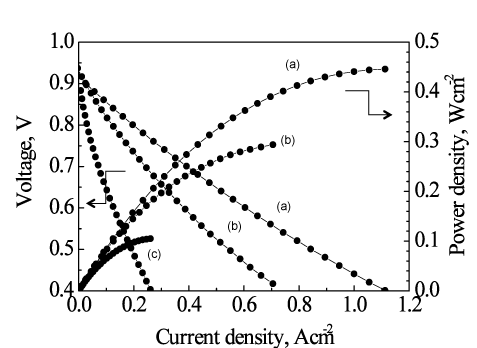 |
Figure 4: Operating-temperature dependence of the power generation performance of the tubular micro-SOFC with the catalyst layer directly using a methane-steam mixture at about (a) 550 °C, (b) 500 °C, and (c) 450 °C |
In the next step, we will design and optimize the catalyst layer for various hydrocarbon fuels and apply the SOFC modularization technology developed over the years to the new tubular micro-SOFC. Our aim is to reduce startup energy, develop compact SOFC systems with quicker startup times, and promote their use as small, fuel-flexible power sources for next-generation vehicles and mobile devices.