Update(MM/DD/YYYY):12/04/2009
Micro-tubular Solid Oxide Fuel Cell Integrated Compact Modules Operable at Low Temperatures
- Potential applications include domestic power supplies and auxiliary power units of automobiles -
Points
-
Micro-tubular solid oxide fuel cells are integrated to realize prototype modules capable of generating powers of 50 to 200 W.
-
An output power of over 50 W (volumetric power density: 2 W/cm3) with a power generation efficiency of over 40% is obtained using the module comprising 90 cells.
-
The developed module integration technology offers good prospects of realizing higher power generation capacity of up to several hundred watts.
Summary
The Functional Assembly Technology Group (Leader: Yoshinobu Fujishiro), Advanced Manufacturing Research Institute (Director: Norimitsu Murayama) of the National Institute of Advanced Industrial Science and Technology (AIST) (President: Tamotsu Nomakuchi), Fine Ceramics Research Association (President: Taro Kato) and NGK Spark Plug Co., Ltd. (President: Norio Kato) (FCRA-NGK), and Toho Gas Co., Ltd. (Toho Gas) (President: Taku Saeki) have developed highly integrated high-performance micro-tubular solid oxide fuel cell (SOFC) modules that would broaden the range of SOFC applications.
The existing applications of SOFCs are limited because the cells are operated at high temperatures of over 800°C. It has been desired to realize SOFC modules capable of rapid (start-and-stop) operation. In this study, we have developed SOFC modules generating several tens to hundreds of watts of power, which are compatible with various system requirements. Power generation tests were carried out to examine the connection of gas manifolds, current collections, and various characteristics of the modules. The tested module consisting of two integrated micro-tubular SOFC units (a total of 90 cells) produced an output of over 50 W with a power generation efficiency of over 40% and a volumetric power density of 2 W/cm3. Further, a 200-W-class module was built by assembling eight integrated units. Thus, the basic fabrication and evaluation techniques for larger modules generating powers of up to several hundred watts have been established (see Figure below). The applicability of the SOFC modules to auxiliary power units (APUs) and small-sized cogeneration systems will be tested using the 200-W-class module.
The study is a part of the "Advanced Ceramic Reactor" project of the New Energy and Industrial Technology Development Organization (NEDO) and the result will be reported at the 22nd Fall Symposium of the Ceramic Society of Japan, to be held at Ehime University on September 16, 2009, and at the 11th International Symposium on SOFCs, to be held in Vienna, Austria, on October 6, 2009.
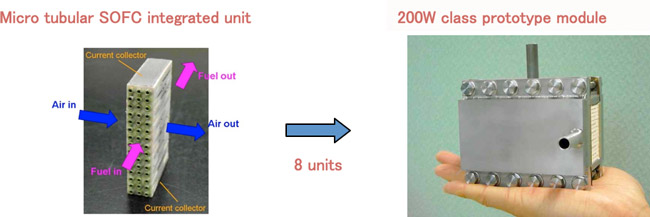 |
Highly integrated micro-tubular SOFC module |
Social Background for Research
Many types of fuel cells have been developed in attempts to achieve high power generation efficiency and greatly reduce CO2 emissions, which cause global warming. Among these fuel cells, SOFCs that consist of ceramic components exhibit the highest efficiency. Since SOFCs, unlike other types of fuel cells, are operated at high temperatures (800–1000°C), exhaust heat can be used for fuel reforming and hot water storage, and the overall energy efficiency of the system can be very high. Further, it has been confirmed that SOFCs exhibit greater long-term stability than other types of fuel cells. However, because the SOFCs are operated at high temperatures, their applications have been limited to power generation systems in which the thermal cycle and load variation can be kept small. Therefore, SOFCs for rapid start-and-stop operation at temperatures below 650°C have been desired so that they can be used in a wide range of applications such as domestic dispersed power sources, power sources for mobile electronic devices, and APUs in automobiles. In such circumstances, micro-tubular SOFCs were proven to show a great promise for realizing rapid start-and-stop operation. One of the problems, however, was the difficulty in integrating these tubular cells to realize small, highly efficient SOFCs generating powers ranging from several watts to several kilowatts, for which there is a great demand in industry (Fig. 1).
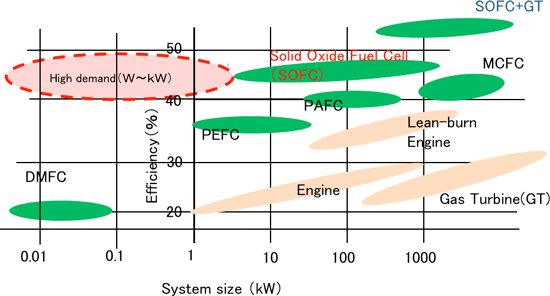 |
Fig. 1 Trends in fuel cell development and demand for small-scale SOFCs |
History of Research
As part of a NEDO project, the Advance Ceramic Reactor Project (FY2005–FY2009), AIST, FCRA-NGK, and Toho Gas have collaborated to realize SOFCs that satisfy requirements such as operation at temperatures below 650°C, high power output, and rapid start-and-stop operation. The collaboration has developed high-performance micro-tubular SOFCs capable of rapid start-up, whose diameters are in the millimeter or sub-millimeter range. Techniques have been established to fabricate an integrated unit (cube), which is of the size of a sugar cube and can generate powers of over 2 W/cm3 at the low temperature of 550°C (press release on March 29, 2007). To improve the performance of integrated units and modules, technologies for upgrading micro-tubular SOFCs were further studied, and one of related reports was published in the US journal "Science" (August 14, 2009).
For practical applications of systems with the high-performance micro-tubular SOFCs, it was considered necessary to increase the scale of integration, and establish and verify integration techniques for realizing arbitrary electrical connections to satisfy output requirements, as well as module technologies including manifold connections. AIST, FCRA-NGK, and Toho Gas have developed techniques for integrating the micro-tubular SOFCs and fabricating prototype modules. We have also evaluated power generation capabilities to prove the effectiveness of the adopted fabrication techniques. AIST assumed the responsibility of evaluating the basic performance of each module element; on the basis of this result, FCRA-NGK designed and fabricated modules, and Toho Gas evaluated the completed modules.
Details of Research
In this study, micro-tubular SOFCs, which are inherently capable of rapid start-and-stop operation, are highly integrated. Gadolinia-doped ceria and scandia-stabilized zirconia were selected for an electrolyte of the cell, both of which are excellent ion-conducting materials. The power generation performance was examined with a 50-W-class module. To be more precise, a module is assembled using multiple integrated units of the 15-to-30-W class (3 in parallel, 9–15 in series) comprising components with excellent size accuracy to meet a target power output. To realize a 50-W-class module, two integrated units (Fig. 2), each consisting of 3 micro-tubular SOFCs in parallel and 15 in series, are connected in parallel (the module contains 90 cells). This module is proved to generate an output power of over 50 W with a power generation efficiency of over 40% and a power per unit volume of 2 W/cm3 (per integrated unit; Fig. 3). It is also confirmed that even higher output power can be obtained under lesser fuel utilization rate. Further, a 200-W-class module has been assembled and is now being evaluated. Although the 200-W-class module comprises eight integrated units and is complex, the completion of the power generation unit with gas manifolds and a current collecting structure increases the prospects for higher power outputs, and indicates that we have taken a significant step forward to a wider range of SOFC applications.
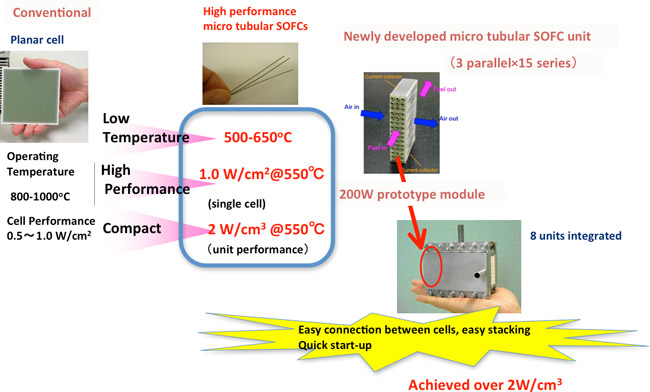 |
Fig. 2 Development of small, high-efficiency SOFCs and modules |
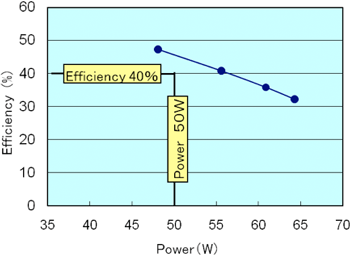 |
Fig. 3 Power generation test results for 50-W-class modules |
The degree of the integration per unit volume (electrode area) in the SOFC modules developed in this study is the highest level, and the developed technologies can be applied to realize smaller and more powerful energy sources. Since the basic component of the modules, i.e., an integrated unit, can generate a volumetric power density of 2 W/cm3, the present technology is proved to be effective for the fabrication of highly integrated micro-tubular SOFC modules.
Future Schedule
The developed micro-tubular SOFC module technology will help accelerate the expansion of applications of SOFCs, module volume ranging from several ten cm3 (applications involving power generation of several tens of watts, such as power sources for mobile electronics devices) to several thousand cm3 (of several kilowatts, such as domestic power sources and APUs of automobiles).
We will further improve the cell and module structure, perform tests under various operating conditions, and improve the module performance with the aim of developing high-performance SOFC modules that are robust to thermal shock, capable of rapid start-up, and readily compatible with a variety of system requirements.