Yuji Kasai (Senior Research Scientist) and others of the Adaptive System Research Group (Leader: Tetsuya Higuchi), the Information Technology Research Institute (Director: Satoshi Sekiguchi) of the National Institute of Advanced Industrial Science and Technology (AIST) (President: Hiroyuki Yoshikawa) have developed a serial bus communication system that uses just a single cable to connect a control unit with the many sensors and actuators of an industrial machine. The research project is funded by the Semiconductor Engineering Center (Chief Executive: Shuichiro Maruta) of Kitakyushu Foundation for the Advancement of Industry Science and Technology (FAIS) (President: Tadamasa Anan).
The system employs a simple protocol enhancing real-time and robust communications and its prototype interface is built with commodity devices easily found in the market at low price. The system developed is robust to external noise and realizes fast communication. In the prototype system the communication delay is less than 0.2 ms and the transmission speed is 2 Mbps. The effectiveness is confirmed by tests using the prototype interface.
The system is expected to improve productivity by reducing wiring works in the manufacturing process, to allow the production equipment to get lighter and smaller, and to cut down cost for maintenance.
 |
Features of the system:
Robustness to noise: communication restarts within 0.3 ms
Speed: delay is 0.2 ms or less
Production cost: 10-20% of existing technologies
|
An example of the serial bus communication system |
Several hundred or more sensors, actuators, and motor-drivers are used in an industrial machine such as industrial robots and semiconductor-manufacturing equipment. The number of signal cables to connect them often exceeds a thousand (Fig. 1). A large portion of time in the production process for industrial machine is utilized for wiring components. That is the reason why wire-saving serial-bus technologies have long been desired in the field.
A serial-bus system called CAN has been employed inside some types of automobile but has hardly been used for the equipment in the semiconductor and the robot industries owing to the following reasons:
(1) Lack of robustness to noise: switching actuators on and off generates noise in cables and causes communication failures.
(2) Communication delays occurring frequently impede running real-time.
(3) The use of complicated communication protocols makes interfaces expensive.
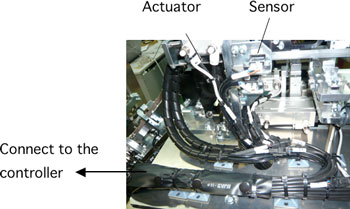 |
Fig. 1 Conventional wiring |
Massive amount of cables interconnect a controller, sensors, and actuators. |
AIST has already developed a prototype for evaluating fundamental technology over the 10-gigabit Ethernet and worked on the standardization project for the specifications of the Ethernet (IEEE802.3an). It has, therefore, been ready for another development in high-speed data-transmission technology based on the achievements mentioned earlier.
FAIS has been promoting research and development in the advanced technology in Kitakyushu region and plays an active role as an intermediate between business and academy by bridging institutes and enterprises. FAIS has received requests for developing a technology in wire-saving in the machine from manufacturing firms in the semiconductor industry in Kitakyushu City and worked around the problem with priority in the past years.
AIST, for its part, started a funded research to meet the needs.
The three major points of this research are: cost, robustness to noise, and speed (real-time communication capability). These are the real demands from the industrial machine industry.
Figure 2 shows the scheme and application of the developed wire-saving technology with a serial bus communication system. In this system, a single serial bus cable connects multiple interfaces, and the controller communicates with multiple sensors, actuators, and motor-drivers via the single cable and interfaces. A communication protocol is installed in the interface and controls serial bus communication. The serial bus cable consists solely of a single cable with two signal and two power wires.
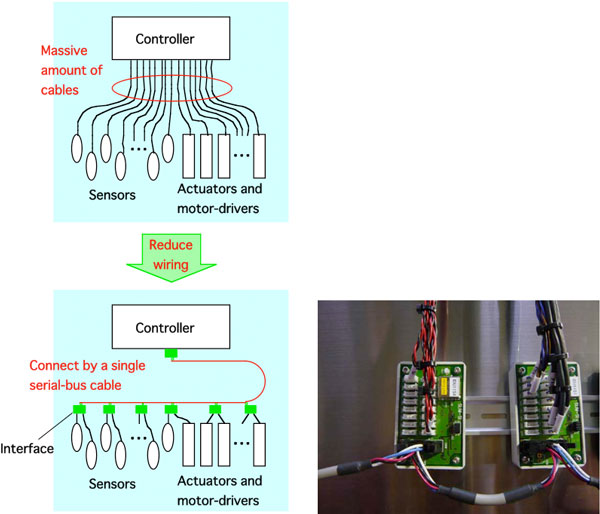 |
Fig. 2 Illustration of how the new serial bus technology changes the configuration inside the machine and an example of the applications using the new serial bus technology. |
The features of the system are as follows:
(1) The developed simple communication protocol with real-time capability and robustness provides for excellent noise-proof communication. Even when the communication has to temporarily stop due to extremely powerful noise, communication can restart within 0.3 ms after the noise disappears. This eliminates communication failures of serial buses caused by noise, which used to be a major issue, and enables fast, stable communication.
(2) Fast communication is realized with real-time capability (in the prototype, communication delay is 0.2 ms or less and the transmission speed is 2 Mbps). This is the result of the invented communication protocol based on a time-triggered control. Thus the problem with time delay in communications on a machine running at high speed is solved.
(3) The prototype interface is assembled with electronic parts that are commercially available and inexpensive, and production cost is 1/5-1/10 that of the existing systems with conventional technologies. This is the result of the simple protocol and the intelligent communication program. The new system with new architecture can be built inexpensively and improves practicality.
(4) The serial bus communication system allows the use of existing control software. The number of wires can be greatly reduced simply by replacing a multitude of wires with the new system. The system prevents faulty wiring and saves time for inspection of wiring, and so work hours for wiring, which account for the majority of the manufacturing hours of industrial machines, are greatly reduced. We expect increased productivity, a reduction in size and weight, and easier maintenance.
(5) The technology can be applied to a wide range of industries whose products consist of a number of sensors, actuators, and motor-drivers. Typical application will be possible to industrial robots, car electronics and humanoid robots in the laboratory.
We have actually implemented the prototype system into a machine that is produced by Kasuga Manufacturing, Co. Ltd. (President: Tadasu Okazumi), a manufacturer of industrial machinery in Kitakyushu City. The machine used for the evaluation of the system developed comprises of approximately 300 sensors and actuators to handle semiconductor chips at high speed and requires real-time capability as a must. The excellence of the system has successfully been demonstrated through the test. Figure 3 shows a photograph of the machine.
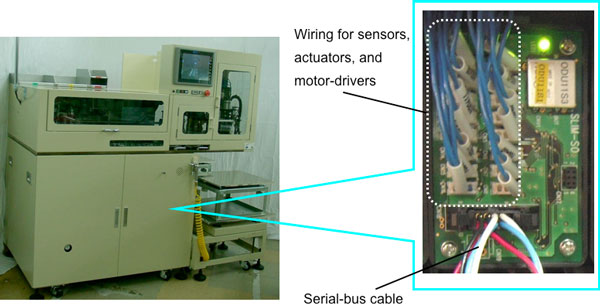 |
Fig. 3 The semiconductor chip inspection system (left) used for the evaluation of the new system and an interface part of the system (right). |
Although the prototype system is made of electric parts that are commercially available and inexpensive, the invented communication protocol and the intelligent communication program in the new system have achieved the required performance such as transmission speed of 2 Mbps and communication delay of less than 0.2 ms. It is expected that the use of a CPLD or an on-chip technology with the new serial bus system will improve the performance in the communication speed ten times faster or even further.
We are trying to refine functions to be implemented into the system and planning to launch the new version of the system in the production system in a year. The upgraded system we are developing is expected to improve productivity, to down size the machine and to ease maintenance. We are also going to make an effort for the protocol we developed to be a standard in the serial communications not only in Japan but internationally.