- Poly(propylene carbonate) composite surpassing general-purpose polymers in elastic modulus -
Hiroshi Shimizu (Leader) and Li Yongjin (Research Scientist), the Nanostructured Materials Group, the Nanotechnology Research Institute (Director: Nobutsugu Minami) of the National Institute of Advanced Industrial Science and Technology (AIST) (President: Hiroyuki Yoshikawa) succeeded in greatly improving the mechanical properties, including elastic modulus and strength, of plastic (aliphatic polycarbonate) made from carbon dioxide (CO2), previously far from practical use, by blending with other plastics. Plastic with excellent mechanical properties, that is 2.4 GPa of elastic modulus and 17.9 MPa of strength, has been developed by using a composite of poly(propylene carbonate) (PPC), a kind of aliphatic polycarbonate made from CO2 and propylene oxide, and other plastics (see Figure). The PPC composite is a high-performance material demonstrating not only improved mechanical properties but also increased heat resistance, and it is expected to be a viable alternative to petroleum-based general-purpose plastics, such as polyethylene, polypropylene, and polystyrene.
In PPC made from CO2, fixed CO2 accounts for 43% by weight. Although the ratio of fixed CO2 decreases to about 30% by weight by blending with other plastics to enhance its performance, this PPC composite has an advantage over general-purpose plastics in terms of reduced CO2 emission. In Japan, the amount of CO2 emitted from power plants and ironworks has reached a level of 500 million tons per year, calling for the urgent establishment of technologies for separation and fixation of CO2. Wide use of the newly developed PPC composite as an alternative to general-purpose plastics is expected to contribute to global warming prevention and lead to reduced dependence on petroleum resources.
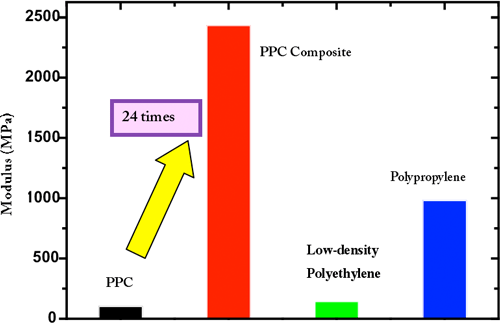 |
Figure Modulus data for PPC, PPC composite, and general-purpose plastics |
A synthetic scheme in which plastics are produced from CO2, which was discovered 40 years ago by Prof. Shohei Inoue (currently Professor of Tokyo University of Science), is receiving renewed attention as a technology for fixing and utilizing CO2, which is one of the measures to prevent global warming. While technological development of aliphatic polycarbonate has been at the basic research level in Japan, pilot plants for PPC production were built by the national budget and commercial mass production of PPC has already started in China. However, the mechanical properties of the produced PPC is still far from practical use and its appearance is similar to soft, sticky rubber rather than plastic, and, therefore, extensive improvement is required.
AIST has been developing techniques for mixing plastic materials at the nanometer level and dispersing nanometer-size particles and fillers such as carbon nanotubes into resins. On July 11, 2006, AIST released a polymer-blending technique that uses a high-shear flow field, which achieved nanometer-level mixing of immiscible polymers.
This time, we searched for effective ways to improve the mechanical properties of PPC. Taking into consideration the basic concept of improved material, we aimed at keeping the ratio of CO2 in the PPC composite at about 30 wt%. We hoped to greatly improve the mechanical properties by adding aliphatic polyesters as second and third ingredients, thus controlling the microstructure of the PPC composite.
While the weight-average molecular weight (Mw) of the PPC used in this study reached 447,000, the glass transition temperature (Tg) was as low as 30°C. In addition, poor heat resistance resulted in pyrolysis at 200°C. Its appearance was similar to clear rubber, and it was so sticky that the samples stuck together. It was an unsuitable polymer for practical use.
By adding an aliphatic polyester (X) to this PPC, a polymer blend (composite) was prepared. In addition, another polymer blend was also prepared by adding the second ingredient polymer X and a small amount (2–20 wt%) of another aliphatic polyester (Y), or the third ingredient.
Figure 1 shows the stress-strain curves of the developed PPC composites, which differ in composition. Properties, including elastic modulus, obtained from the stress-strain curves and dynamic viscoelasticity measurements are shown in Table 1. Low-density polyethylene (LDPE) and polypropylene (PP), which are general-purpose plastics, are also listed for comparison.
PPC without additives shows rubber-like features including extremely low elastic modulus and high elongation at break (%) (Curve 1 in Fig. 1). A polymer blend prepared by mixing the PPC and aliphatic polyester X at a ratio of 70 to 30 shows about 15 times as high an elastic modulus, although the elongation at break decreased slightly (Curve 2 in Fig. 1). Another polymer blend prepared by adding aliphatic polyester Y in addition to the second ingredient X shows 24 times as high an elastic modulus at an optimum composition (Curve 5 in Fig. 1). By blending the polymers, the glass transition temperature (Tg) of composites increased by almost 10°C and the heat resistance was greatly improved.
Such enhancement of mechanical properties may stem from the inner structure of the PPC composite, and the finest inner structure may have formed at a composition of PPC/X/Y = 70/30/5.
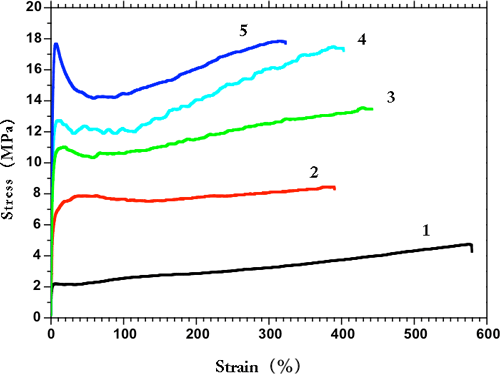 |
Figure 1 Stress – strain curves of PPC and PPC composites
|
[Curve 1: pure PPC, Curves 2 to 5 : PPC composites, (2 : PPC/X=70/30, 3 : PPC/X/Y=70/30/2.5, 4 : PPC/X/Y=70/30/10, 5 : PPC/X/Y=70/30/5)] |
Table 1 Mechanical properties at room temperature (25°C) |
|
We continue to pursue further improvement of the properties of PPC composite and also plan to apply the PPC composite to not only general structural materials but also film and packaging materials by making the most of its transparency and gas-barrier property, and to evaluate its performance as a practical material. We intend, therefore, to conduct active technology transfer to companies with an interest in this technology.