Kiyoshi Yase (Deputy Director) of the Photonics Research Institute and Hirobumi Ushijima (Leader) of the Bio-Photonics Group, the Photonics Research Institute (Director: Masanobu Watanabe) of the National Institute of Advanced Industrial Science and Technology (AIST) (President: Hiroyuki Yoshikawa), and the Japan Chemical Innovation Institute (JCII) (President: Kunio Nakajima) have jointly succeeded in fabricating a flexible electronic device by printing an array of organic thin-film transistors (organic TFTs) onto a plastic film (Figure 1).
By using a large-area, high-precision printing technique based on the microcontact printing method, we successfully realized patterning with lines/spaces = 1 µm/1 µm over a 6-inch diameter. We also successfully printed an organic TFT array using poly(3-hexylthiophene) as the semiconductor and silver nanoparticles as the electrodes on a plastic substrate.
The operational electrical device was fabricated by a printing method in which all the materials were converted into inks, and no vacuum processes were necessary. The results represent a major step toward commercially viable processes for producing flexible displays and organic devices by large-area high-speed printing methods such as roll-to-roll printing. It also contributes to the realization of an ubiquitous information society.
The results of this study are to be announced at the 11th International Conference on Electrical and Related Properties of Organic Solids, to be held in Poland on July 13–17, 2008.
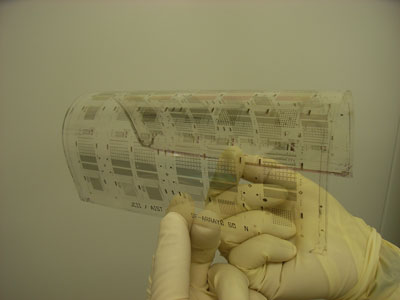 |
Figure 1. Organic thin-film transistor array fabricated entirely by printing process on a flexible plastic film
|
The importance of display devices as an interface between humans and machines is growing along with the remarkable development of information technology (IT). However, current methods for manufacturing displays require multiple processes that include photolithography and vacuum deposition, and thus are energy inefficient. On the other hand, printing techniques are material-efficient and can be performed at room temperature and moderate atmosphere. The production of electrical device by printing would realize low-cost and environmentally friendly devices. For portable devices, such as mobile phones, breakage caused by shock is a serious problem. Therefore the realization of low-cost and low-environment-load flexible displays is recognized as an essential component in the creation of a sustainable IT-based society.
Since FY2006, AIST and JCII have jointly pursued developments in array technology based on printing methods, along with development of inks for organic TFTs. The microcontact printing method using silicone rubber as a stamp is refined for high-definition large-area printing. The technology permits patterning of 1.0-μm-wide lines and spaces on 6-inch-diameter substrates. These developments allow organic TFT arrays using poly(3-hexylthiophene) as the semiconductor and silver nanoparticles as the electrodes to be printed onto flexible polymeric substrates.
The research and development was conducted as a part of the "Technological Development of Superflexible Display Components (FY2006 - FY2009)" sponsored by the New Energy and Industrial Technology Development Organization (NEDO).
The TFT array is an essential device for driving displays such as electronic papers and liquid-crystal displays. To fabricate such semiconductor devices by printing, each material needs to be turned into an ink. Consequently, soluble organic semiconductors are required. However, organic semiconductors are less efficient than inorganic semiconductors in terms of their charge mobility. TFTs based on organic semiconductors need special design features such as short channel length between electrodes. In the case of the organic semiconductor poly(3-hexylthiophene), which was used in this study, channel length between the source and the drain electrodes of the organic TFT has to be 5 µm or less. This exceeds the limits for patterning by widely used printing methods such as ink-jet and offset printing. Therefore, a new patterning technology, the microcontact printing method, was introduced for fabricating organic TFT arrays.
Previously, applications of the microcontact method were limited to areas of only a few square centimeters, and use of the technique to print larger areas was thought to be extremely difficult. The reason for this problem was in the nature of poly(dimethylsiloxane) (PDMS, silicone rubber), the material widely used in microcontact printing. PDMS suffers from low dimensional accuracy as a result of swelling by substances such as halogenated hydrocarbons and aromatic hydrocarbons. Also, PDMS become electrically charged and attract dust during removal from a silicon mold. By eliminating these problems and adjusting its hardness, a new PDMS, optimal as a microcontact printing material, was developed. Further, to improve the reproductivity of the microcontact printing, a platen type microcontact printer and associated manufacturing equipment for stamps were developed. By using these equipments and an ink comprising a solution of a low-molecular weight organic compound, rhodamine (a fluorescent dye), in an organic solvent, we succeeded in printing the world’s smallest pattern on a large area. In this pattern, lines 0.8 μm wide with 0.8 μm spaces were printed on a area of 6 inches in diameter. This result showed that not only is the microcontact method capable of high-precision printing, but that organic semiconductor devices could be produced by large-scale high-precision printing.
To fabricate an organic electronic device by printing, it is necessary to convert materials for organic semiconductors, electrodes, bus-lines and insulators into inks. In this study, inks for the conductive materials were made from nanoscale silver particles and poly(3,4-ethylenedioxythiophene)-co-poly(styrenesulfonic acid) (PEDOT-PSS), and poly(3-hexylthiophene) (P3HT) was used as the organic semiconductor material. The surface of the PDMS stamp was treated in order to permit uniform application of the ink. This treatment permitted the printing of a pattern with line and space widths of 1.0 µm onto 15-cm-square flexible films of conventional plastics, such as poly(ethylene naphthalate) (PEN) or polycarbonate (PC) (Figure 2).
|
Figure 2. Silver nanoparticle patterns fabricated by microcontact printing (upper left and right: optical microscopic images, lower left and right: atomic force microscopic images).
|
Furthermore, modification of microcontact printing process itself was examined to optimize the quarity of resulting devices, considering the properties of the inks and the precision requirements of each process. A flexible organic TFT array was fabricated by printing all of gate electrodes, gate insulating films, source and drain electrodes, semiconductor and passivation films using the improved micro-printing method (Figure 3).
This study has demonstrated the possibility of low-cost fabrication of lightweight shock-resistant display, and paved the way for the application to the production of a cellular-phone unit and a mobile-computer display. It also raises the possibility of producing widely used devices, such as radio-frequency identification (RF-ID) tags, at a low cost by an environmentally friendly printing process.
|
Figure 3. Optical microscopic image of the 100 ppi organic thin-film transistor array fabricated entirely by printing process (pixel size: 254 μm).
|
We will develop the technology to permit the fabrication of an organic TFT array that can drive a high-resolution display (200 pixel per inch: pixel size 120 µm) entirely by printing processes, and develop flexible displays. We will also pursue the low-cost production of lightweight shock-proof displays that could contribute to the realization of the ubiquitous information society.