The Laboratory for Film Chemistry (LMC) of the National Institute of Advanced Industrial Science and Technology (AIST), an independent administrative institution, has succeeded in developing a flexible, translucent and self-supported gas barrier film through compact lamination of clay crystal platelets. The newly developed gas barrier film is expected as gas barrier materials used under wide range of temperatures, which had been hardly available up to now.
In the prior art, heat-resistant gas barrier film was prepared by the use of engineering plastic, or if necessary, through composite processing, surface modification or lamination. The usage of the conventional gas barrier material, however, was limited up to 350 °C.
The LMC-AIST successfully prepared a gas barrier film of uniform thickness without a pinhole nor other defects at a high degree of reproducibility, by using clay which was added to engineering plastics for upgrading the gas barrier performance as main ingredient of the film, and by optimizing composition of clay materials and additives, as well as preparation process. A flexible and translucent gas barrier film can be prepared through the compact lamination of clay crystal layers of thickness around 1 nm each (1 nm = 1/1,000,000,000 m). A clay crystal layer of nanometer thickness is adequately flexible and transparent. The compact lamination of clay layers provides a translucent film with light scattering suppressed. The thickness of resultant film is comparable to that of copy paper, 3~100 μm (1 μm = 1/1,000,000 m), and can be made much thicker by layering the film together. The size of the film is unlimited. Besides, it is also possible to create a protective film by coating metal surface with the clay film. The gas permeability of the film at room temperatures to hydrogen, oxygen, nitrogen and other inorganic gases is lower than the detection limit: much lower than the oxygen permeability of conventional engineering plastic (18, for Nylon 6) and comparable to that of aluminum foil (0). Besides, the gas barrier performance of the film remains unchanged up to temperatures as high as 1000 °C, much higher than the melting point of aluminum foil (660 °C).
The heat-resistant gas barrier film will be useful as gaskets around automobile engine, sealant materials for piping in chemical plant, fuel-sealing materials around rocket and jet engines, separating film solid electrolyte fuel cell, constituting hopeful heat-resistant gas barrier materials.
 |
Photo. 1. Outlook of translucent gas barrier film (Dimensions: 10 cm (W) x 10 cm (L).
|
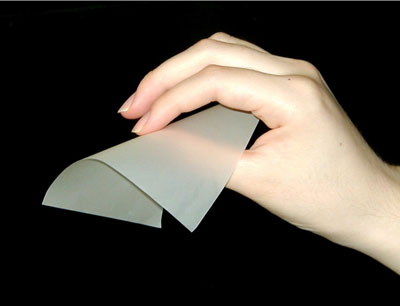 |
Photo. 2. Outlook of flexible gas barrier film
|
In many fields of chemical industry, involving various production processes under higher temperatures, it is essential to provide means for preventing liquid or gas from leaking out of pipe joints by use of gaskets or welding. Gaskets made from flexible organic polymer materials, such as Teflon, is often used. However, organic gaskets cannot withstand temperatures higher than 350 °C, and beyond that temperature range, metal gasket is to be used. Since metal gasket is less flexible than that of organic polymer materials, a mechanism to fasten with greater force is needed, which makes gasket vulnerable. For this reason, gasket (gas barrier materials) of higher heat resistance and better flexibility has been sought for.
In the past decade, a number of heat-resistant gas barrier materials have been developed, and one of means to solve the problem is to add a small amount of clay to engineering plastics for upgrading heat-resistance, mechanical strength and gas barrier performance. In this case, increasing the contents of clay crystal tends to improve both heat-resistance and gas barrier property. This suggests that with gas barrier materials containing clay as main body, it may be possible to prepare gas barrier materials of superior heat-resistance, gas barrier property and flexibility to those of conventional materials. However, neither gas barrier materials based on clay crystal nor process to prepare them have been established up to now.
The LMC-AIST has been engaged in the study on the hydraulic barrier property of specimens made of pressed clayey soils. In the course of this study, it was found that clay crystal could be compacted into a film of uniform thickness by molding. Through a reversal of thinking, it has been attempted to prepare a gas barrier film based on clay crystal, in place of upgrading the performance by using clay as main constituent, and efforts have been paid to R&D of method and conditions for the preparation.
A translucent and flexible gas barrier film was successfully prepared by use of novel technique to make compact lamination of clay crystal layers of thickness about 1 nm each and diameter hundreds of nm. The clay materials were either natural clay or synthesized one, and a small amount of additive was added, if necessary, to upgrade flexibility. Thin clay crystal layer is flexible and does not absorb light, and compact lamination of such layers results in translucent film with light scattering suppressed. The resultant film was as thick as copy paper (around 3~100 _m), and it is possible to prepare a thicker film by layering the film together. The dimension of film is unlimited. Moreover, it is also possible to create a protective film by coating metal surface with clay crystal in the similar way. The gas permeability of the film at room temperatures to hydrogen, oxygen, nitrogen and other inorganic gases is lower than the detection limit: much lower than the oxygen permeability of conventional engineering plastic (18, for nylon 6) and comparable to that of aluminum foil (0). Besides, the gas barrier performance of the film remains unchanged up to temperatures as high as 1000 °C, much higher than the melting point of aluminum foil (660 °C).
The gas barrier film emits no waste byproduct in the process of production and is friendly to the environment because key ingredient is clay.
Clay may be either natural or synthetic, and the production cost is comparable to that of ordinary engineering plastics.