Update(MM/DD/YYYY):04/17/2014
Mass Production Technology for Single-Wall Carbon Nanotubes
– Returns the fruits of AIST’s research in nanotechnology to society –
Points
-
Industrial production plant developed to verify mass productivity with production speed 100 times faster than the conventional method
-
High-quality, high-purity single-wall carbon nanotubes synthesized in this plant to be introduced to the market in 2014
-
Develop the market for R&D use of cutting-edge materials through the promotion of public-private collaboration and accelerate application research by private enterprises
Summary
Takeshi Saito (Leader) and others of Direct Injection Pyrolytic Synthesis Team, the Nanotube Research Center (Director: Sumio Iijima) of the National Institute of Advanced Industrial Science and Technology (AIST; President: Ryoji Chubachi), have transferred a seed technology of AIST, the Enhanced Direct Injection Pyrolytic Synthesis (eDIPS) method, for the manufacture of single-wall carbon nanotubes (SWCNTs), a cutting edge nanotechnology material, to Meijo Nano Carbon Co., Ltd. (MNC; CEO: Takeshi Hashimoto) and have verified the mass productivity of SWCNTs using the eDIPS method through the development of an industrial production plant through a collaborative project between the two parties.
In the present study, various reaction conditions in the developed industrial production plant using the eDIPS method were optimized to attain a production speed 100 times that of the conventional high-quality carbon nanotubes (CNTs) manufactured and marketed by MNC. Based on this result, in 2014 MNC will become the first Japanese manufacturer to introduce SWCNTs synthesized by the chemical vapor disposition (CVD) method to the market. This will enable high-quality, high-purity samples to be placed in mass quantity on the R&D-use market and is expected to accelerate studies for commercial use of SWCNTs.
This can also be considered to be a model case of the return of R&D results conducted by a public research organization to society through collaboration and joint R&D with private companies.
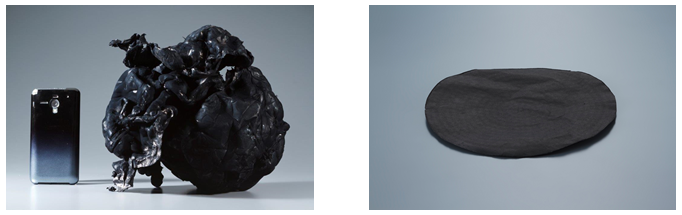 |
(Photo) : A lump of SWCNTs synthesized in the developed industrial production plant (compared to a smartphone) (left)
and high-purity (99 % or higher) SWCNTs processed into sheet form (15 cm diameter) (right) |
Social Background of Research
SWCNTs known for their outstanding characteristics such as being 20-times stronger than steel, 10-times higher thermal conductivity of copper, half the density of aluminum and 10-times more carrier mobility of silicon, are expected to be used in a wide range of applications and many research projects have been carried out globally with them as one of the most promising materials in nanotechnology.
However, mass production of SWCNTs has been difficult and SWCNTs currently available on the market face many problems for their use as a sample product for R&D use, with many structural defects, low purity, and disparity in quality, which have hindered the practical application of SWCNTs.
History of Research
AIST developed the eDIPS method, a type of CVD method, in 2006 as the outcome of the “Nanocarbon Applied Products Creation Project” funded by the New Energy and Industrial Technology Development Organization for research in high quality CNT synthesis technology and has verified that high-purity SWCNTs that require no refining can be synthesized using small-scale equipment (AIST press release on May 11, 2006). AIST has been conducting technical transfer of this eDIPS method, a superb SWCNT synthesis technology, to private enterprises aiming to return the fruits of research to society but the marketing of high-quality SWCNTs was not achieved and remained as an issue.
On the other hand, MNC has been manufacturing and marketing SWCNTs mainly manufactured by the conventional arc discharge method. However, mass productivity was low with the arc discharge method and synthesized SWCNTs faced problems such as high degrees of amorphous carbon and graphitic carbon impurities. Although developments in refining and separation technologies were being made to improve the purity of SWCNTs, MNC felt the need for R&D to produce high-purity, high-quality as-grown SWCNTs with high mass productivity.
This time, AIST and NMC conducted a collaborative project for the verification of mass production technology using the eDIPS method as a core technology and the development of an industrial production plant by combining the eDIPS method of AIST together with various technologies of MNC in SWCNT manufacturing.
Details of Research
Future Plans
Joint research will continue, aiming at further improvement in mass production technology and streamlining. AIST and MNC will supply high-purity, high-quality SWCNTs to companies and research institutions wishing to develop applications and peripheral technology, thereby contributing to product development utilizing CNTs. (Fig. 4)
Furthermore, companies seeking for collaboration to increase production scale and/or to develop a variety of applied products will be solicited. AIST and MNC expect to actively couple these with MNC’s SWCNT dispersion technology, coating technology, and semiconductor type/metal type SWCNT separation technology to establish corporate partnerships and collaboration structures for the industrialization of CNTs.
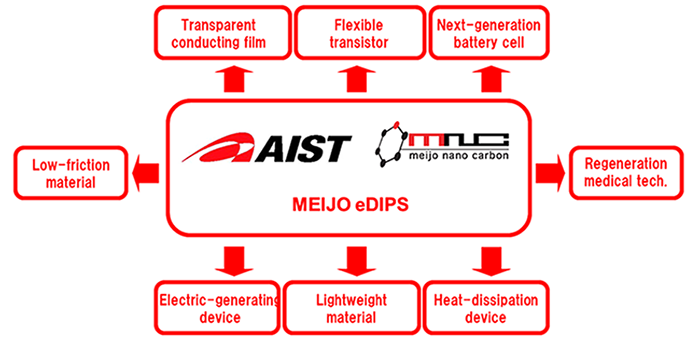 |
Figure 4 : Anticipated SWCNT applications |