- Rapid, precise, and easy simulation of droplet shapes on hydrophilic/hydrophobic patterned surfaces -
Yuki Noda (AIST Postdoctoral Fellow), Hiroyuki Matsui (Collaborating Visitor from the graduate school of frontier sciences, the University of Tokyo), Tatsuo Hasegawa (Deputy Director) and others of the Flexible Electronics Research Center (Director: Toshihide Kamata), the National Institute of Advanced Industrial Science and Technology (AIST; President: Ryoji Chubachi), have developed a software for rapid, precise, and easy simulation of ink droplets printed on substrates that has surfaces patterned with wettability (hydrophilic/hydrophobic pattern).
The developed program allows numerical simulation, with the use of a commercial personal computer, of the shapes of ink droplet placed on a flat substrate surface that includes discontinuous boundaries between hydrophilic and hydrophobic areas, whereas such a simulation has been difficult so far. It is expected that the software would greatly accelerate the research and development of the "printed electronics" which is dedicated to manufacture a variety of information terminal devices through the printing technologies, and that the software could be also applied to the analytic technologies for various liquid processes using solid surfaces.
The developed droplet shape simulation software, "HyDro", has been released on July 31, 2013, via a Web page (available for free, https://sites.google.com/site/hydroenglish/).
|
Operation screen for the droplet shape simulation software, "HyDro", that runs on a personal computer |
The "printed electronics", which applies printing technologies to the manufacture of electronic devices, has attracted considerable attentions. It is expected that fairly small electronic circuits could be fabricated by applying microdroplet of electronically functional ink (that dissolves or disperses semiconductors or metals) on substrate surfaces, followed by spreading, drying, and solidifying of the ink microdroplet on the substrates. For this purpose, it is required that the shapes of tiny ink droplets (with a volume of several picoliters to several tens of nanoliters) on substrates must be predicted accurately.
In recent years, a method to form a high resolution pattern of hydrophilic areas showing high ink wettability on top of low-ink-wettable, hydrophobic surfaces, to control wetting of ink precisely, and thereby to print high resolution ink patterns attracts attentions as a useful method to attain high resolution patterning that exceeds the resolution limit of conventional printing technologies. However, it has been difficult to predict droplet shapes by conventional numerical simulation techniques, because the surface free energy that characterizes surface wettability varies discontinuously on the substrate surfaces that include hydrophilic/hydrophobic boundaries. For example, it should be impossible to obtain the exact shape by a conventional simulation technique, or to predefine the initial droplet shape freely, or extremely long computational time should be necessary for a calculation method to trace the time evolution of droplet shape; all of the existent numerical simulation techniques are not satisfactory to the engineers in their workplaces.
AIST has been promoting the research and development of the printed electronics technology in a wide range of aspects. A part of the research and development has focused on the print production technologies of very fine electronic circuits by the formation of a fine hydrophilic pattern on a hydrophobic surface, on the simple simulation techniques for predicting wetting phenomena of a tiny droplet on top of solid surfaces that include the hydrophilic/hydrophobic boundaries (Langmuir 28, 15450 (2012)), and also on the confirmation of the validity of the simulation techniques using the inkjet printing technique (J. Appl. Phys. 114, 044905 (2013)).
This study is supported partly by the Japan Science and Technology Agency through Strategic Promotion of Innovative Research and Development Program, as "Development of Flexible Display based on AM-TFTs Manufactured by Printing Processes with New High-Performance Polymer Semiconductors" (FY 2009 - 2018), and also partly by the Japan Society for the Promotion of Science through the Funding Program for World-Leading Innovative R&D on Science and Technology, as "Quantum Science on Strong Correlation" (FY 2009 - 2013).
When a tiny droplet is placed on top of solid surfaces that show uniform wettability, the droplet generally takes a sphere shape which is cut off by a plane. The angle θ between the solid surface and droplet surface is called as the "contact angle" (Fig. 1) which is used as an important fundamental index for the wettability. For example, the contact angle becomes small on wettable surfaces with high surface energy (i.e., hydrophilic surfaces), while the contact angle becomes large on dewettable surfaces with low surface energy (i.e., hydrophobic surfaces).
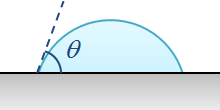 |
Figure 1: Contact angle θ |
On the other hand, droplet shapes become complicated on solid surfaces with non-uniform wettability, as the shapes are determined by the local contact angles at respective positions on the solid surfaces. Particularly, it is hard to predict the droplet shapes on solid surfaces that include discontinuous variation of wettability such as hydrophilic/hydrophobic boundaries. This is because the gradient descent (GD) method which is a widely-utilized technique for the droplet shape simulation assumes smooth variation of surface free energy that determines the surface wettability.
In this study, the researchers developed droplet shape simulation software, "HyDro", with the use of hybrid energy minimization technique in which the calculation is conducted separately for the droplet surface touching the substrate surface (contact lines) and the other parts of the droplet surface. In HyDro, the calculation is conducted, based on a fundamental principle that the droplet is settled into the lowest (or minimum) energy state at the equilibrium. In the conventional GD technique, the solution for a droplet shape that affords lowest surface energy is searched, using the slope of surface free energy for whole droplet surface including solid-liquid contact lines. Therefore, if the surface free energy includes a discontinuity due to the hydrophilic/hydrophobic boundary, the solution search becomes difficult, where the surface shape solution is not converged into a final droplet shape even after taking a vast number of calculation steps. On the other hand, it is unrealistic and difficult to apply the direct search technique in which the solution search is executed randomly for the whole droplet surface, because huge calculation time is required. In order to solve the issue, the researchers separated the droplet surface into the contact line touching the substrate and the other part, and apply the direct search technique to the former and the GD technique to the latter. It enables us to settle the convergence problem, and also to minimize the calculation load which causes a serious issue in the direct search technique. Figure 2 shows an example, presenting the difference of solution convergence for the droplet shape simulation; a droplet deposited on a predefined rectangular-shaped hydrophilic area is simulated by the developed (HyDro) technique and the conventional (GD) technique (Note: Amount of calculation at each step is almost similar with each other).
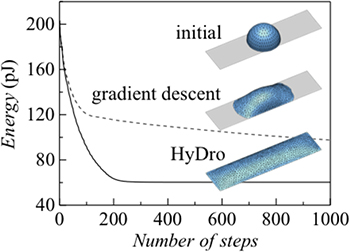 |
Figure 2: Comparison of solution convergence between HyDro and the GD technique |
HyDro works on commercial personal computers with any operating system (Java Runtime Ver.6.5 or the later version is necessary). In the use of HyDro, users are supposed to partition solid surface into some areas depending on the wettability, and to define contact angles on the respective area, as presented by gray (hydrophilic) and white (hydrophobic) areas in Fig. 3. Then the users are supposed to assume an appropriate initial shape of the droplet (like a hemisphere as presented in the left of Fig. 3), and to start the energy minimization calculation. In the calculation, HyDro transforms the droplet shape slightly in the each step, leading to the lower energy droplet shape through the step-by-step processes. When the state reaches the lowest (or minimum) energy state, the calculation will finish (Fig. 3 right). In the simulation, it is assumed that the droplet is composed of liquid with uniform density and surface tension. It is possible to assume arbitrary-shaped hydrophilic/hydrophobic patterns made on flat surfaces; complicated patterns, such as stripe, comb, check, and curvilinear patterns, can be assumed.
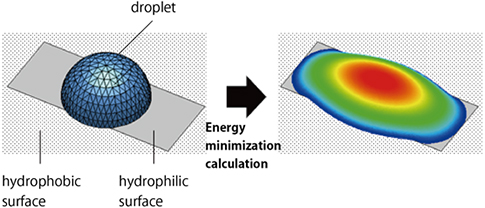 |
Figure 3 : Initial shape (left) and final shape (right) of droplet after energy minimization calculation |
In order to investigate the validity of simulated results with HyDro, the researchers conducted a tiny droplet deposition by an inkjet printing technique on a 1-mm square hydrophilic area which is surrounded by hydrophobic surface (Fig. 4). They compared the experimental and simulated results in terms of the nonwetting area ratio of the dry regions around rectangular corners of the hydrophilic area, and found that the experiments are very accurately reproduced by HyDro (Fig. 4(c)).
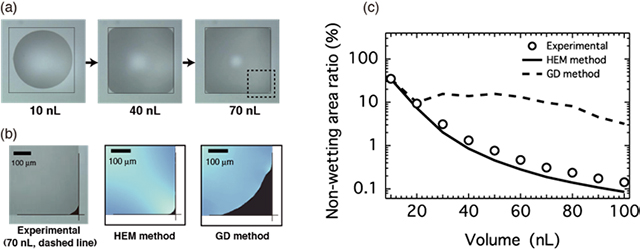 |
Figure 4 : (a) Appearance of ultrapure-water droplet deposited on a square (1 mm × 1 mm) hydrophilic area. (b) Enlarged view of right bottom in (a) with 70 nL deposition (left), simulated result by HyDro (middle), and simulated result by the GD method (right). Nonwetting region around the rectangular corner is painted black. (c) Relation between the nonwetting area ratio and droplet volume both for the experimental and simulated results. |
By the use of HyDro, rapid, precise, and easy simulation of an ink droplet shape placed on top of a complicated hydrophilic pattern has become possible, although this has been difficult to be executed so far. For example, HyDro can simulate exactly the overspreading effect from the hydrophilic area into the hydrophobic area when a sharp-bent pattern is used (Fig. 5). Thus it would be possible to use this software for the design and defect analysis of high-resolution, printed wiring.
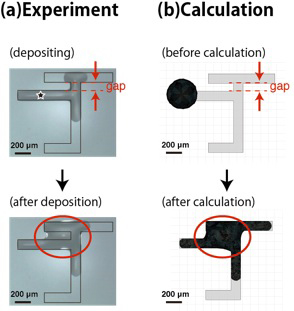 |
Figure 5 : Appearance of ultrapure water droplet deposited by inkjet printing technique on a sharp-bent hydrophilic pattern on a substrate (left), and the result of numerical simulation by HyDro (right) |
Furthermore, it is possible to make mapping analyses of surface free energy (or wettability) distribution using HyDro. The measurement for the analysis is composed of inkjet printing of droplets on a solid surface, gradual increase of the droplet volume, and measurement of droplet contact lines at the respective volume by a digital microscope camera. Then the droplet shapes with the observed contact lines are simulated by HyDro, by which the variations of contact angles along the contours are calculated backward, leading to obtain the distribution of contact angles (Fig. 6).
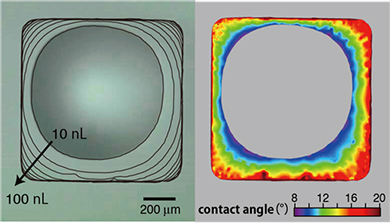 |
Figure 6 : Variation of contact lines (left) and distribution of contact angles (right) |
The researchers will further develop the manufacturing technologies of high resolution metal wiring, electrodes, and semiconductor layers by printing of electronically functional inks, with the help of the developed simulation technology.