Update(MM/DD/YYYY):03/12/2013
Development of New Rolling Process for Improving Room-Temperature Formability of Damping Magnesium Alloy Sheets
- Expansion of application range of magnesium alloy sheets as damping components -
Points
-
Texture control of damping magnesium alloy sheets
-
Current rolling machines are available for production of damping magnesium alloy sheets with excellent room-temperature formability.
-
Contribution to cost reduction and high productivity of magnesium alloy products as damping components
Summary
Kazutaka Suzuki (Senior Researcher), Huang Xinsheng (Researcher), Motohiro Yuasa (Researcher), and Yasumasa Chino (Leader), Group for Structural Metals Design, the Materials Research Institute for Sustainable Development (Director: Mamoru Nakamura) of the National Institute of Advanced Industrial Science and Technology (AIST; President: Tamotsu Nomakuchi), have developed a new rolling process for improving room-temperature formability of a damping magnesium alloy (M1 alloy) in collaboration with Mamoru Mabuchi (Professor), Kyoto University (President: Hiroshi Matsumoto).
In the new rolling process, while a conventional rolling machine is used, the room-temperature formability of magnesium alloys is improved by controlling the annealing temperature and the rolling temperature. The sheet rolled by the new process exhibits excellent room-temperature formability close to that of aluminum alloys (Erichsen value: 7.9) (Fig.1), because the magnesium crystals in the texture of the sheet are less aligned than those of the conventional rolled sheets. The sheet rolled by the new process exhibits not only excellent room-temperature formability but also good damping capacity. Thus, it is expected that magnesium alloy products as damping components can be easily processed by the press-forming at room temperature.
Details of this study will be published in Materials Transactions (Advanced View) of the Japan Institute of Metals on February 1, 2013.
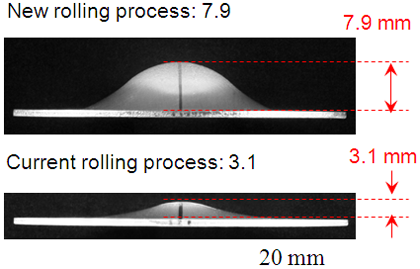 |
Figure 1 : Results of Erichsen test for M1 alloy sheets processed by the new rolling process
and current rolling process(high temperature rolling process)
|
Social Background of Research
Magnesium alloys are promising light structural materials due to their lowest density among practical metals, high specific strength, and high Clarke number, namely abundant resources. Now, utilization of magnesium alloy products is expanding, particularly in automobile industry and consumer electronics (e.g. laptops and cell phones) industry. Besides, magnesium has the highest specific damping capacity among practical metals, and their application as damping components, such as speaker diaphragms and acoustic cable shielding, is increasing.
Now, most of magnesium alloys used as structural components includes additional elements such as aluminum and zinc, which dissolve in magnesium and improve their mechanical and corrosion properties. However, dissolution of the other elements in magnesium significantly deteriorates their damping capacity. Thus, damping capacity of commercial magnesium alloys such as AZ31 alloy have much lower value compared with those of pure magnesium. Therefore, at present, commercial magnesium alloys or damping magnesium alloys (including pure magnesium) are appropriately selected depending on their usage.
It is known that room-temperature formability (at from 0 to 30 °C) of pure magnesium and magnesium alloys is much lower than that of aluminum alloys and steels, and it is very difficult to make press-formed products at room temperature. Concerning to commercial magnesium alloys (AZ31 alloys), press-formed products with complex shape can be processed by warm press forming (at from 250 to 300 °C). Besides, some new rolling processes for improving room-temperature formability have been proposed. On the other hand, it has become a problem that ductility of pure magnesium and damping magnesium alloys is not so improved at higher than 250 °C. Thus, damping magnesium alloys with improved room-temperature formability are expected.
History of Research
AIST and Kyoto University have conducted a joint research to improve room-temperature formability of magnesium alloy sheets. To date, the researchers found that a hot-rolled Mg-Zn alloy with dilute content of cerium exhibits an excellent room-temperature formability equivalent to that of aluminum alloys (AIST press release on September 16, 2008). Besides, they found the new rolling process for improving room-temperature formability of commercial magnesium alloy sheets (high temperature rolling process), where they are rolled at about 500 °C, just below the melting point (AIST press release on January 26, 2010).
However, the above methods are appreciable to magnesium alloys with dissolved elements with high concentration, and they are not applicable to damping magnesium alloys. In the present study, the researchers have focused on the research and development to improve the room-temperature formability of damping magnesium alloys.
Details of Research
It is known that magnesium shows poor ductility due to its crystal anisotropy. At room temperature, there is a large anisotropy in deformation resistance depending on the deformation direction of the crystal. As shown in Fig. 2, deformation resistance parallel to the basal plane (direction) is small, but deformation resistance parallel to the prismatic plane (direction) is very large. In general, a strong basal texture, in which the c-axis is aligned perpendicular to the rolled surface, is formed in a magnesium alloy sheet during rolling. When a magnesium alloy sheet exhibits the strong basal texture, the deformation along a-axis (basal slip) cannot operate along the thickness direction. Thus, it is recognized that press forming of magnesium alloy sheets is extremely difficult at room temperature. For the reason described above, it is important to prevent the formation of strong basal texture during rolling process and create a texture in which the basal slip in the thickness direction can occur easily in order to improve room-temperature formability.
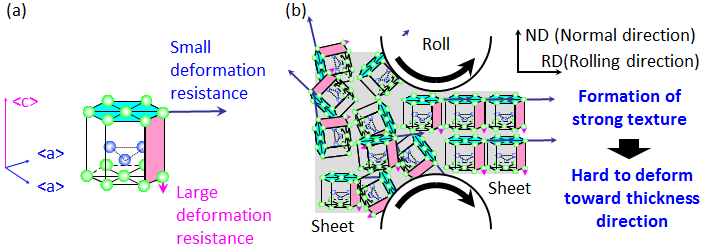 |
Figure 2 : (Left) Anisotropy of magnesium crystal at room temperature (Right) Texture formation of magnesium during rolling process |
In the new rolling process, formation of the strong basal texture in rolled damping magnesium alloy (M1 alloy) can be suppressed by the repetition of high temperature annealing (at around 500 °C) and warm temperature rolling (at around 200 °C). Pole figures of the basal plane of the M1 alloy sheet processed by the current rolling process (high temperature rolling process at 500 °C) and the new rolling process are shown in Fig. 3. The pole figure of the sheet by the new rolling process exhibits the tendency, indicating that the most part of basal plane is inclined at 15° toward the rolling direction and the pole density of the sheet shows much smaller value. It means that the new rolling process contributes to the suppression of the formation of the strong basal texture. As a result, the M1 alloy sheet by the new rolling process can deform to the thickness direction, and exhibits the improved room-temperature formability (Erichsen value=7.9), which is close to that of aluminum alloy sheets (5083 aluminum alloy: Erichsen value=8.5), as shown in Fig. 1.
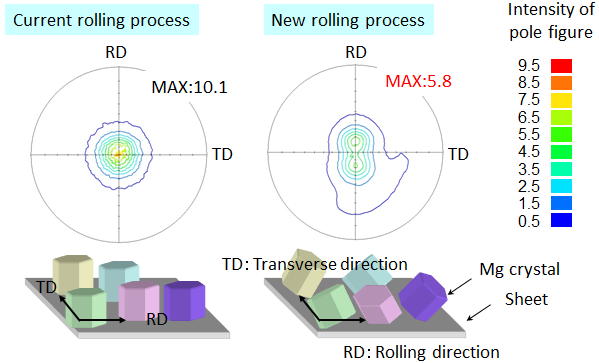 |
Figure 3 : (Top) Pole figures of basal plane of M1 alloy sheets (Bottom) Schematic view of crystal orientation of the rolled sheets |
Figure 4 shows the damping capacity (internal friction) of pure magnesium, M1 alloy, and AZ31 alloy. AZ31 alloy has relatively good damping capacity among commercial magnesium alloys, but the internal friction of AZ31 alloy is only about 30% of that of pure magnesium. On the other hand, the internal friction of M1 alloy is about 70% of that of pure magnesium regardless of the formation of the strong basal texture. It is suggested that the new rolling process can improve room-temperature formability of damping magnesium alloy (M1 alloy) without deterioration of their damping capacity.
The application of the new rolling process enables the production of magnesium alloy products with not only high damping capacity but also high room-temperature formability. Thus, it is expected that the application range of magnesium alloy sheets with high damping capacity as damping components will be expanded.
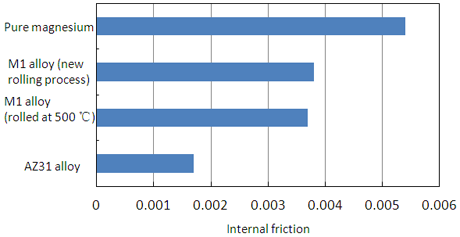 |
Figure 4 : Internal friction of pure magnesium, M1 alloys and AZ31 alloy |
Future Plans
Feasibility study of the new rolling process for damping magnesium alloy sheets will be cooperatively carried out with companies.