- Cobalt- and nickel-free positive electrode materials for lithium-ion secondary batteries -
Mitsuharu Tabuchi (Senior Researcher), Ionics Research Group, the Research Institute for Ubiquitous Energy Devices (Director: Tetsuhiko Kobayashi) of the National Institute of Advanced Industrial Science and Technology (AIST; President: Tamotsu Nomakuchi), has developed two types of new oxide material (namely, Li1+x(Fe0.3Mn0.7)1-xO2 and Li1+x(Fe0.3Mn0.5Ti0.2)1-xO2) for the positive electrode of lithium-ion secondary batteries in collaboration with Junji Akimoto (Leader), Crystal and Materials Processes Group, the Advanced Manufacturing Research Institute (Director: Nobumitsu Murayama) of AIST and Junichi Imaizumi (Manager), Technology Development Team 5, Technology Development Department of Tanaka Chemical Corporation (Tanaka Chemical; President: Tamotsu Tanaka). Approximately 30 % of the total amount of transition metals in these newly developed oxide materials is made up of iron, which is a low-cost and resource-wise abundant metal.
The researchers have produced these positive electrode materials by optimizing their chemical composition and using a wet chemical method that includes a reductive calcination process. The initial cycle efficiency at room temperature (normalized discharging capacity value at the lower limit voltage of 2.0 V in the left side graph) has been improved drastically to approximately 80 %; this is equivalent to the performance of conventional positive electrode materials.
These newly developed materials assure high initial charge and discharge capacities of approximately 250 mAh/g or higher (right side graph). They offer a performance equivalent to that of conventional positive electrode materials and yet do not contain rare metals, cobalt and nickel. Therefore, the new materials are expected to contribute to resource saving and cost reduction for lithium-ion secondary batteries used in electric vehicles etc.
Details of this technology will be presented at the "52nd Battery Symposium in Japan" to be held in Edogawa Ward, Tokyo from October 17 to 20, 2011. This research has been conducted as part of "Development of High-performance Battery Systems for Next-generation Vehicles (Li-EAD project) - R&D of novel and high-capacity positive electrode material consists of low-cost constituent oxides (FY2007 - FY2011)" project commissioned by the New Energy and Industrial Technology Development Organization.
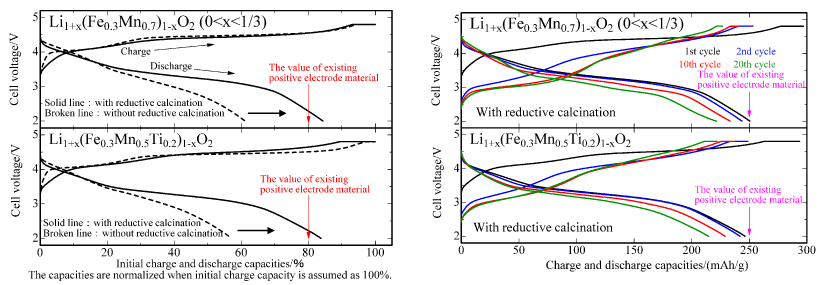 |
Comparison of initial charge/discharge characteristics of two types of newly developed positive electrode material (left)
and charge/discharge cycle characteristics for up to 20 cycles (right) |
With growing awareness of energy savings and resource conservation in recent years, electrical vehicles and hybrid vehicles are drawing attention and the use of these vehicles is becoming more widespread. The amount of electrical power stored and discharged per unit weight of a battery (energy density) of lithium-ion secondary batteries is much superior to that of other secondary battery systems. Therefore, a lithium-ion secondary battery is one of key storage devices with high potential for vehicle applications. Studies are also being conducted on the applications that require large-size storage batteries, such as stationary energy storage systems in combination with renewable energy, for example wind power and solar power generation systems.
Improved performance and cost reduction without compromising safety are required for lithium-ion secondary batteries for vehicles. To reduce cost, the constituent materials of the battery must be replaced with less expensive materials. Among the constituents, the positive electrode material that serves as the lithium ion supply source is the most expensive constituent. Furthermore, the positive electrode material is the key constituent that determines battery capacity and operating voltage. Hence, there is a strong demand for the development of low-cost and high-performance positive electrode materials.
For lithium batteries, AIST has been researching positive electrode materials that contain iron, the most inexpensive and abundant metal, and titanium, which were previously considered difficult to use. Through that research, AIST has developed lithium manganese-based oxide materials for positive electrodes. The basis of the materials is lithium manganese oxide (Li2MnO3) that contains a large quantity of lithium (AIST press releases on October 21, 2004 and November 6, 2006). In order to bring the discharge voltage (3 V) of these materials closer to that of existing positive electrode materials (4 V), AIST and Tanaka Chemical have jointly developed an iron- and nickel-substituted lithium manganese-based (FNM-based) oxide material for positive electrodes (Li1+x(Fe0.2Ni0.2Mn0.6)1-xO2; average discharge voltage of 3.5 V) (joint press release of AIST and Tanaka Chemical on August 17, 2009).
To achieve further cost reduction and higher performance, it is desirable to develop a positive electrode material that does not contain nickel, which is the most expensive material among all the constituent metals. For that reason, the researchers have developed positive electrode materials such as iron-substituted lithium manganese oxide (FM-based) and iron- and titanium-substituted lithium manganese oxide (FMT-based).
The initial cycle efficiency at room temperature is particularly important for positive electrode materials and an efficiency of at least 80 % is required for commercial use in the potential range of a conventional positive electrode of 2.0 V to 4.8 V. The researchers applied the new fabrication technology to develop two types of positive electrode material (FM-based and FMT-based materials) in order to realize higher capacity, high initial cycle efficiency, and reduction of cycle degradation for lithium-ion secondary batteries. This technology can optimize the metallic element composition ratio and chemical composition.
Regarding the metallic element composition ratio, both FM-based and FMT-based materials have an iron content of 30 % among metallic elements other than lithium, because it is the optimal amount of iron from the standpoint of charge and discharge characteristics, and Li1+x(Fe0.3Mn0.7)1-xO2 (0<x<1/3) has been selected for the FM-based positive electrode material composition. It has been observed that the charging and discharging capacities tend to drop when iron content is higher than 30 % and that the charge and discharge cycle characteristics tend to degrade when iron content is lower than 30 %.
The manganese content of the FMT-based positive electrode material has been reduced to 50 % from the amount contained in the FM-based material (70 %) because of the 20 % titanium added to the FMT-based material, and Li1+x(Fe0.3Mn0.5Ti0.2)1-xO2 (0<x<1/3) has been selected as the composition of the FMT-based positive electrode material. The researchers have selected this composition based on two factors. 1) When titanium is introduced, the charging and discharging capacities have a tendency to drop. AIST's fabrication method (to be described later) can be applied to minimize this amount of drop in the charging and discharging capacities. 2) A report of the Argonne National Laboratory in the U.S. indicates that elution of some manganese content occurs when a carbon negative electrode is used and that this will cause a significant drop in the charging and discharging capacities during the charge and discharge cycle. The drop in capacity during the cycles can be minimized by reducing the manganese content.
A new fabrication technology was used to optimize the chemical composition. Based on the wet chemical method (co-precipitation and calcination method: conventional fabrication technology) that can produce materials with uniform metal distribution, the reductive calcination process was performed, in which the sintered powder with an organic compound was sintered at low temperature (400 °C). The reductive calcination was performed in order to control the valence state of iron ions so that they had a trivalent state only. Unlike FNM-based materials that contain nickel, this newly developed fabrication technology is an easier manufacturing method on the industrial level because it does not require the hydrothermal reaction process after producing the co-precipitate.
Figure 1 shows the initial charge and discharge characteristics of newly developed positive electrode materials at 30 °C in the same potential range (2.0 V to 4.8 V) as that of an existing positive electrode material (cobalt- and nickel-substituted lithium manganese-based oxide, Li1.2Co0.13Ni0.13Mn0.54O2, CNM-based material). The CNM-based material is considered to be a promising next-generation high-capacity Li2MnO3-based positive electrode material.
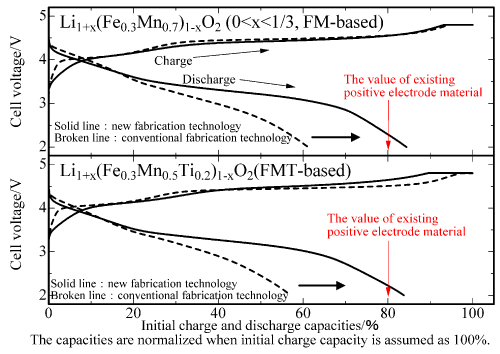 |
Figure 1 : Comparison of initial charge and discharge characteristics of two types of newly developed positive electrode material
(Metallic lithium is used as the negative electrode material; potential range: 2.0 V to 4.8 V) |
In Fig. 1, the initial charging capacities are normalized as 100 %. The charge and discharge capacities of this newly developed FM-based positive electrode material are 297 mAh/g and 251 mAh/g, respectively. It achieves an initial cycle efficiency of 84 %. The charge and discharge capacities of the new FMT-based material are 294 mAh/g and 246 mAh/g, respectively. It achieves an initial cycle efficiency of 84 %. In other words, both FM-based and FMT-based positive electrode materials show favorable characteristics. When the positive electrode materials are fabricated by the conventional method, which does not use the reductive calcination process, the initial cycle efficiency of the materials is low (approximately 60 %). Therefore, it is assumed that the new fabrication method that uses the reductive calcination process has a significant effect in bringing about such drastic characteristics improvement.
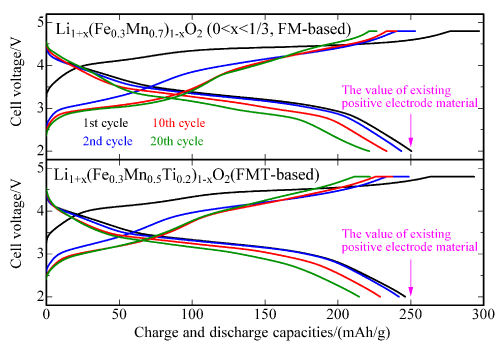 |
Figure 2 : Comparison of charge and discharge cycle characteristics of two types of newly developed positive electrode material for up to 20 cycles at 30 °C
(Metallic lithium is used as the negative electrode material; potential range: 2.0 V to 4.8 V) |
Figure 2 shows the charge and discharge cycle characteristics of the newly developed positive electrode materials for up to 20 cycles. The charge and discharge curves indicate similar features from the second cycle to the 20th cycle. A high percentage of the initial discharging capacity is retained after 20 cycles (88 % for the FM-based material and 87 % for the FMT-based material). Based on these two factors, it has been confirmed that the newly developed materials have high potential as positive electrode materials in lithium-ion secondary batteries.
Table 1 summarizes the results of the investigation on whether or not the newly developed positive electrode materials are superior in performance and cost to the existing positive electrode material (CNM-based material) and the previously developed positive electrode material (FNM-based material). Literature values for the charge and discharge data of the CNM-based material are used. The discharge energy density is equal to the product of average discharge voltage and initial discharging capacity. The raw material cost is calculated according to the chemical formula of each material and cost of raw material reagents.
Table 1 : Comparison of initial charge and discharge characteristics and costs of the newly developed positive electrode materials,
the existing positive electrode material, and the previously developed positive electrode material |
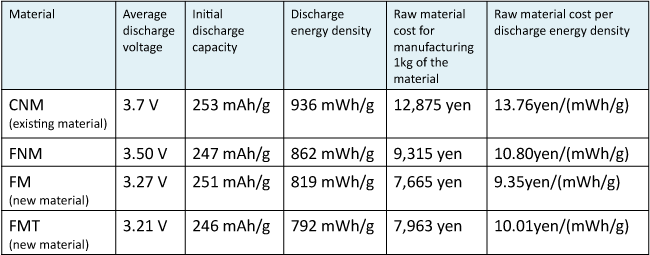 |
As indicated in Table 1, the newly developed materials have a discharge energy density inferior to those of the CNM-based and FNM-based materials. However, the raw material cost for manufacturing 1 kg of the new materials is lower than those of the CNM-based and FNM-based materials. Therefore, the raw material cost per energy density of the new materials is also lower. Considering this point, the FM-based and FMT-based new materials as well as the previously developed FNM-based material are promising as materials for the positive electrode. Compared with the existing CNM-based material, the estimated values for reducing the raw material cost per energy density of FM-based and FMT-based materials are 32 % and 27 %, respectively.
This calculation does not include the processing cost required for the production processes. Therefore, the reduction effect on the actual production cost will be lower than the above values. If the newly developed materials can be produced at the same processing cost of CNM-based materials, it will be possible to obtain low-cost positive electrode materials consisting only of resource-wise abundant metallic elements. For that reason, the newly developed materials are expected to contribute to saving resources and reducing the cost of lithium-ion secondary batteries used in electric vehicles etc.
Figure 3 shows the result of the charge and discharge cycle tests of the FMT-based material using carbon as a negative electrode, which is used in commercial lithium-ion secondary batteries.
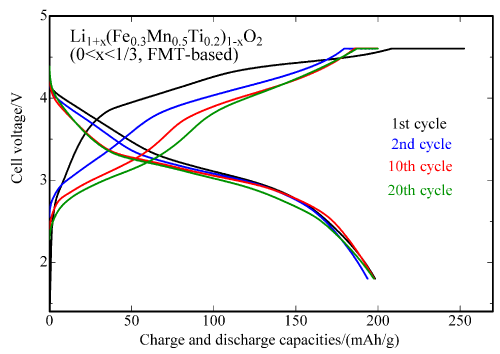 |
Figure 3 : Charge and discharge cycle characteristics of the newly developed FMT-based positive electrode material for up to 20 cycles at 30°C
(Carbon is used as the negative electrode material; potential range: 1.8 V to 4.6 V) |
Figure 3 shows that there is almost no drop in the charge and discharge capacities of the FMT-based material containing titanium from the second cycle to approximately 20 cycles. Thus, the FMT-based material is promising as a positive electrode material that can demonstrate superior charge and discharge characteristics when it is used in commercial batteries. So far, the cycle characteristics obtained for the FM-based material are not as good as those of the FMT-based material. As the initial charge and discharge capacities of the FM-based material are higher than those of the FMT-based material, the researchers is aiming for improving the cycle characteristics of the FM-based material by conducting detailed research in fabrication conditions.
The researchers are going to make efforts toward achieving higher capacity and reducing cycle degradation in order to improve the charge and discharge characteristics of the newly developed materials. At the same time, they will work on the kilogram-order fabrication technology and aim at supplying these materials to the industrial sector including battery manufacturers by 2013.