Update(MM/DD/YYYY):12/05/2011
Soft Thermoelectric Conversion Devices Fabricated by Printing
- Conversion of slight differences in temperature in the environment into electric power -
Points
-
Thermoelectric conversion devices are formed on a flexible film substrate by printing.
-
The devices are highly flexible and can be installed on objects of various shapes.
-
This flexibility and the reduced cost of the thermoelectric conversion devices are expected to help disseminate energy harvesting.
Summary
Kouji Suemori (Researcher), Functional Display Device Team (Leader: Satoshi Hoshino), the Flexible Electronics Research Center (Director: Toshihide Kamata) of the National Institute of Advanced Industrial Science and Technology (AIST; President: Tamotsu Nomakuchi), has developed a technology for printing thermoelectric conversion devices onto flexible substrates such as plastic films and papers. The technology adds high flexibility to the thermoelectric conversion devices by turning them into film devices, allowing their installation to be unrestricted by the shapes of the objects onto which they are installed. In addition, the printing technology enables cost reduction in the manufacturing process, as well as resource savings.
To promote the use of thermoelectric conversion devices, which convert thermal energy into electrical power, it is essential to enhance conversion efficiency, reduce costs, and improve the convenience of the devices so that they can be installed on waste heat generating objects of various shapes. The researcher conducted R&D of a technology for the fabrication of flexible thermoelectric conversion devices by using a printing process, which is a low-cost manufacturing process. He has discovered that a printable composite material, in which a carbon material is dispersed into a resin matrix at a nanometer-level, has more than 1.5 times the power-generation capacities of conventional printable materials. He has also found that printing the devices on a film substrate by using a solution of this material as an ink creates a thermoelectric conversion film device with excellent temperature-difference power generation. The developed thermoelectric conversion film device is expected to help disseminate energy harvesting, which uses waste heat from instruments and equipment, as well as body heat, as an energy source and converts the heat into electrical power. It should also contribute to the safe supply of electrical power.
Details of the technology will be presented at AIST Open Lab to be held in Tsukuba on October 13 and 14, 2011.
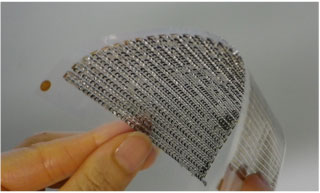 |
Figure : Thermoelectric conversion film devices fabricated by printing |
Social Background of Research
Energy-harvesting technologies, which convert various forms of energy existing in the environment, such as heat, vibration, and electromagnetic waves, into electric power, are technologies that utilize familiar energy sources in daily life by converting the energy sources into electrical power effectively and safely. The technologies are expected to be widely popularized in the form of local power sources that do not require the charging or replacement of batteries and are used as power sources for portable electronic communications devices, sensor network terminals, and personal medical and health-care equipment.
Among the energy-harvesting technologies, thermoelectric conversion devices, which directly convert thermal energy including body heat and waste heat from instruments and equipment into electrical power, are the most familiar energy-conversion devices and are expected to be used more extensively. Currently thermoelectric conversion devices are fabricated mainly with rare metals such as bismuth and tellurium. There are issues relating to the widespread use of waste heat by using thermoelectric conversion devices. They include: (1) the difficulty in cost reduction and mass production of devices, because the main ingredients are rare metals, which are scarce resources with considerable price fluctuations; (2) the devices currently being used have little flexibility and formability, making installations on uneven sources of waste heat and heat radiation difficult; and (3) the difficulty in increasing the area of the devices for mass-conversion of energy.
To solve these problems and to widely popularize the use of energy harvesting by thermoelectric conversion, a new thermoelectric conversion material that is not restricted by resource availability and allows flexibility, large area, and cost reduction, and establishment of the technology for highly productive device fabrication are desired.
History of Research
In order to strengthen market competitiveness in the areas of information terminals and energy equipment, AIST has been working to develop flexible devices, which are lightweight, thin, free-form, and drop-resistant and a highly productive manufacturing technology for flexible devices. Recently, it has been devoting efforts to developing a printing technology for device manufacturing. The technology allows high-speed production and low-cost and energy-saving manufacturing of devices, because printing processes do not require vacuums or high temperatures. The present researcher focused on thermoelectric conversion devices, because printing processes are effective in manufacturing the devices and the devices are highly compatible with a need of society, namely safe and convenient energy supply. He has succeeded in the printing of flexible thermoelectric conversion devices for the first time in the world.
Details of Research
With the aim of creating a high-performance thermoelectric conversion film device, the researcher investigated a thermoelectric conversion material that can be made into a thin film and has found that a carbon-polymer composite material, which is a mixture of a carbon material such as carbon nanotubes (CNTs) and a polymeric material at a nanometer-level, has high thermoelectric conversion performance. The requirements for high-performance thermoelectric conversion materials include high electrical conductivity and low thermal conductivity in addition to a large Seebeck coefficient, which indicates the ability to generate voltage by using heat. Because of their strong intermolecular forces, carbon materials such as CNTs aggregate into bundles and granules when the materials are simply dispersed into polymeric materials. To give the CNT-polymer composite material high electrical conductivity, the aggregation of CNTs must be prevented and CNTs must be dispersed into the polymer at a nanometer-level. For this purpose, various dispersing agents are generally used to prevent the aggregation of CNTs before they are dispersed. However, when the CNT-polymer composite material is used in thermoelectric conversion devices, the presence of residual dispersing agent reduces the ability to generate voltage and, therefore, dispersing agents cannot be used easily. To overcome this issue, the researcher has developed a technology for dispersing CNTs into a polymer solution by applying a mechanical dispersion method instead of using dispersing agents. The developed CNT-polymer composite material has been made into ink by adjusting the material so that it dissolves in a solvent. A thermoelectric conversion material made of the composite material with CNTs dispersed at a nanometer-level was fabricated by printing a pattern using the ink, drying, and sintering (Fig. 1). The fabricated composite material, which was free from the decrease in voltage generation caused by dispersing agents, had a Seebeck coefficient of 0.13 mV/K; this was about three times larger than that of the material fabricated by using a conventional method.
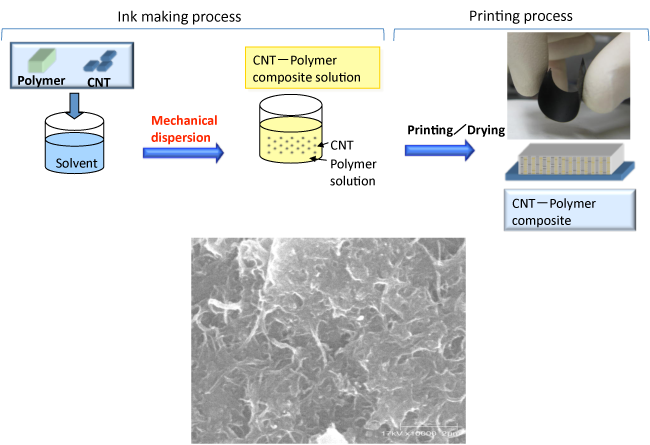 |
Figure 1 : The fabrication method of the CNT-polymer composite material (top), and an electron microscope image of its surface (lower) |
To attain high conversion efficiency of thermoelectric conversion devices, it is important to increase the electric conductivity of the constituent material while keeping the thermal conductivity low. High performance of the CNT-polymer composite material was obtained by controlling the microstructure within the material through the control of drying and sintering processes. Because both high electrical conductivity and low thermal conductivity were achieved, the developed material shows a thermoelectric conversion performance that is more than 50% higher (thermoelectric figure of merit ≈ 0.03) than that of a CNT-polymer composite material fabricated by using a conventional method. At this moment, this figure is the world’s highest for a thermoelectric conversion material that can be formed by printing.
A flexible thermoelectric conversion film was fabricated by the drying and the sintering processes after the pattern of the CNT-polymer composite material is formed on a 20-µm-thick plastic film substrate through a stencil-printing process using the ink described above (Fig. 2). The flexible thermoelectric conversion film has 1000 devices, each 0.5 mm wide × 0.8 mm long × 0.3 mm thick, connected in series. The thermoelectric conversion film sustained no mechanical damage when it was bended at a radius of curvature of 5 mm, and it was confirmed that the film was highly adaptable to the installation on curved or spherical surfaces. In addition, it demonstrated excellent temperature-difference power generation, even with a small temperature difference between a room temperature of 25 °C and body temperature of 36 °C. This confirmed that effective thermoelectric conversion devices could be manufactured.
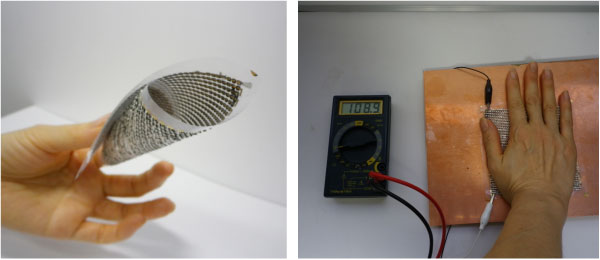 |
Figure 2 : A flexible thermoelectric conversion film fabricated by using a printing process (left) and its electrical power-generation ability (right) |
A temperature difference created by placing a hand on the film installed on the 10 °C plate generated voltage of 108.9 mV. |
Future Plans
The researcher aims to develop a thermoelectric conversion material that has performance comparable to that of conventional solid thermoelectric conversion materials and can be printed onto film substrates. He will do this by improving the performance of the CNT-polymer composite material through controlling the microstructure of the material. At the same time, the device structure will be further optimized aiming at improved thermoelectric conversion efficiency. In addition, he plans to seek private companies and conduct collaborative research to address the issues in product commercialization.