Kouichi Hamamoto (Researcher) and Yoshinobu Fujishiro (Leader) of Functional Integration Group, the Advanced Manufacturing Research Institute (Director: Norimitsu Murayama) of the National Institute of Advanced Industrial Science and Technology (AIST; President: Tamotsu Nomakuchi), have developed a ceramic electrolyte sheet with high lithium ion conductivity at room temperature.
A significant reduction in grain-boundary resistance of the developed ceramic electrolyte sheet, which has been difficult to realize, has been achieved utilizing a new sintering process. The sheet shows high overall conductivity (1×10-3 S/cm) at room temperature. The thin large-area sheet can be manufactured more energy efficiently than conventional products. Therefore, its use as a ceramic electrolyte for an all-solid lithium ion battery with high safety is expected. The film has excellent water resistance, meets requirements as an electrolyte material for lithium-air batteries expected to be next-generation storage batteries, and is expected to accelerate the development of high-performance rechargeable batteries.
Lithium ion batteries are widely used in small and portable information terminal devices due to their excellent characteristics including high energy density and high voltage. In the near future, large-scale lithium ion batteries will be broadly used in transportation equipment such as automobiles, power storage, load leveling, industrial machines, and machine tools, necessitating further safety. Solid electrolytes are considered to be effective in improving the safety of lithium ion batteries. Among solid electrolytes, the application of ceramic electrolytes is expected due to their high density, superior incombustibility, and long-term stability. Currently, while sulfide-based ceramic electrolytes are favorable because their lithium ion conductivity equals that of organic electrolytes, problems linked to size remain, such as the low mechanical strength of thin films. Also, the application of the sulfide-based ceramic electrolytes in lithium-air batteries, the next generation of high-performance batteries, is considered difficult due to low water resistance.
An LTAP-based glass ceramic electrolyte having a NASICON type crystal structure has been developed as a material having an exceptionally high water resistance among the ceramic electrolytes. In existing products using this material, the overall conductivity as a polycrystalline substance is as low as 1×10-4 S/cm at room temperature due to the low lithium ion conductivity at the grain boundary between crystal particles, though the conductivity inside the crystal particles is high. Increased conductivity, therefore, is desired for practical use. Further, the manufacture of the electrolyte needs to be more energy efficient and it is difficult to make a thin and flat large-area sheet of the material.
Focusing on ion conductive ceramics, AIST is conducting research on new hybrid power source technology applicable to next-generation automobiles and small power sources for mobile units. It developed high efficiency energy-conversion technologies capable of using various kinds of fuel such as a high performance micro SOFC using oxide ion conductive ceramics (Science 2009, AIST TODAY, No.08, Vol. 11, 2011). In the present research, the researchers have developed a manufacturing process technology for the water-resistant large-area ceramic electrolyte sheet demonstrating high lithium ion conductivity at room temperature for use in the innovative rechargeable batteries. The rechargeable batteries will be used in combination with the energy-conversion technologies developed by AIST.
The researchers focused on LTAP-based water-resistant ceramics having a NASICON type crystal structure aiming at application to lithium-air batteries which have an energy density theoretically far greater than that of lithium ion batteries as well as to all-solid lithium ion batteries. In conventional processing, the row material of LTAP-based glass ceramic electrolyte having a NASICON type crystal structure is melted at around 1400°C, and the powder formed by vitrification is used for the electrolyte sheet or electrolyte substrate manufacturing. In this research, the powder crystallized at low temperature while using a solid-state reaction is used directly as the starting material for manufacturing the electrolyte sheet. A sintering technology using phase separation has also been developed. These have led to the manufacture of a large-area LTAP-based glass ceramic electrolyte sheet having a NASICON type crystal structure and much higher manufacturing energy efficiency. At the same time, the process significantly reduces grain-boundary resistance of crystals that has been a problem with ceramic electrolytes and achieved the overall conductivity of the polycrystalline electrolyte close to the inherent ion conductivity within the crystals. The developed ceramic electrolyte sheet (Fig. 1) not only demonstrates a high overall conductivity (1×10-3 S/cm) at room temperature (Fig.2), it provides high water resistance and high thermal stability up to 800°C.
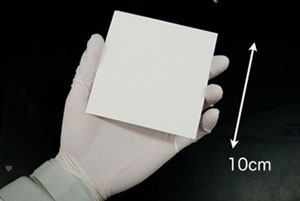 |
Figure 1 : Developed ceramic electrolyte sheet |
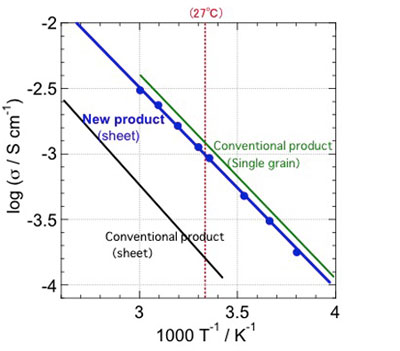 |
Figure 2 : Temperature dependence of lithium ion conductivity of ceramic electrolyte sheets |
The ceramic electrolyte sheet has sufficient strength against bending stress; a ceramic electrolyte sheet 80 µm thick was unbroken after repeated bending (curvature radius of approximately 5 cm) (Fig.3). Because of its flexibility, the ceramic electrolyte sheet is expected to withstand external stresses, such as those caused by vibration when used as the power source for automobiles.
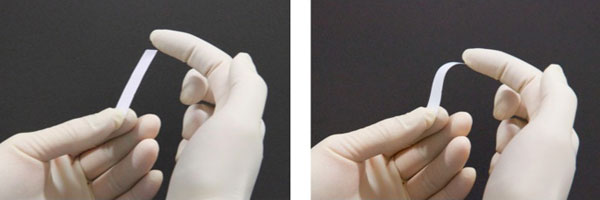 |
Figure 3 : Flexibility of the ceramic electrolyte sheet |
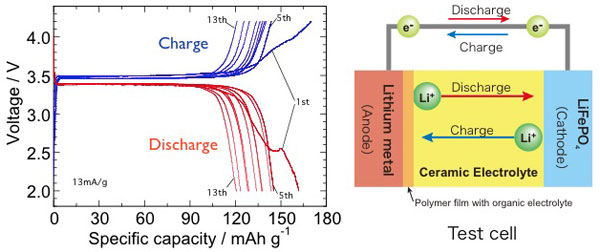 |
Figure 4 : Charge–discharge performance of the test cell |
A coin type lithium ion battery was fabricated by applying an olivine type lithium iron phosphate cathode to the developed ceramic electrolyte sheet, then using an organic electrolyte liquid-containing polymer film and a metal lithium foil anode to confirm that the developed sheet functions as a solid electrolyte for a storage battery. Through the charging/discharging cycle tests, the coin cell demonstrated a discharge capacity of approximately 85% of the theoretical capacity of the lithium iron phosphate in the fifth cycle, and the developed sheet was confirmed to effectively function as a solid electrolyte (Fig. 4).
The developed ceramic electrolyte contains titanium, known to cause degradation when metal lithium is directly brought into contact with the electrolyte. Therefore, devising such as the use of organic electrolyte liquid-containing polymer is needed in the manufacture of current storage batteries. The research and development will focus on trial manufacture and the practical use of the all-solid lithium ion battery and the lithium-air battery by applying this manufacturing process to electrolyte materials with high durability against metal lithium that are considered not practical because of their low ion conductivity and realizing a high lithium conductive protective film with corrosion resistance.