Update(MM/DD/YYYY):10/24/2011
Roll to Roll Production of a Heat-resistant Film with Very High Thermal Dimensional Stability
- Shrinkage of only 0.04% even after heating at 350 °C -
Points
-
A film material with excellent thermal dimensional stability and heat resistance has been developed by combining clay and polyimide.
-
Because the dimensions of the film do not change after heating, it can be used as printable electronics substrates.
-
Also having a high water vapor barrier property, the film material is expected to be used as solar cell back sheets.
Summary
Takeo Ebina (Leader), Advanced Functional Materials Team, the Research Center for Compact Chemical System (Director: Takaaki Hanaoka) of the National Institute of Advanced Industrial Science and Technology (AIST; President: Tamotsu Nomakuchi), and Manabu Yoshida (Senior Researcher), Printed Electronics Device Team, the Flexible Electronics Research Center (Director: Toshihide Kamata) of AIST, et al. have developed a heat-resistant film made of clay and polyimide in collaboration with Sumitomo Seika Chemicals Co., Ltd. (Sumitomo Seika; President: Yusuke Ueda) and Takashi Yamashita (Associate Professor), Department of Pure and Applied Chemistry, Faculty of Science and Technology, the Tokyo University of Science (TUS; President: Akira Fujishima).
AIST has been studying “Claist®,” a film material with clay as the principal component, and working to put it to practical use. Through the current research, the researchers collaboratively developed a heat-resistant film improving the fragility of “Claist®” and established a process for producing the roll film. Characterization of the produced film confirmed its excellent thermal dimensional stability, heat resistance, etc. not found in conventional plastic films and in addition a high water vapor barrier property.
This film is expected to be used in various applications, including substrates for printable electronics and back sheets of solar cells.
Details of this technology will be presented at the sixth Clayteam seminar to be held in Sendai on September 1, 2011 and at the AIST Open Lab to be held in Tsukuba from October 13 to 14, 2011.
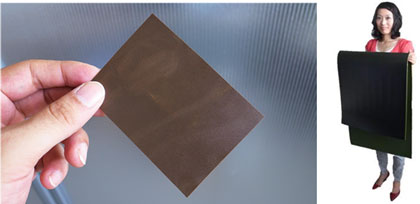 |
Figure : Newly developed heat-resistant film (in roll form on right)
|
Social Background of Research
Because “Claist®”, the clay film developed by AIST, is flexible and has a high gas and water vapor barrier properties, heat resistance, and noncombustibility, it is expected to be used in such applications as food and pharmaceutical packaging, transparent sheets for displays and solar cells, back sheets of solar cells, and a hydrogen seal material. However, because that film is difficult to continuously produce as a roll and fragility and difficult handling are among its issues, it cannot be distributed at low cost as an industrial material and putting it to practical use has been problematic.
At the same time, the information and communication terminals that are characterized by being lightweight, thin, and resistant to drop impact, i.e. flexible devices, are attracting interest in recent years. The devices nearly always have plastic substrates, but making these substrates noncombustible has been difficult. Moreover, these substrates are subject to expansion and contraction owing to heating and cooling processes, respectively, which makes processing them into delicate shapes challenging and necessitates the development of materials whose dimensions do not change even after heating. Polyimide is a heat-resistant plastic, but it has not been able to meet market needs because it undergoes large dimensional change by heating and has a poor water vapor barrier property.
History of Research
Since developing “Claist®” (AIST press release on August 11, 2004), AIST has performed joint research with universities, research institutes, and private enterprises to put “Claist®” to practical use. In May 2010 it established “Clayteam”, an AIST consortium, to further promote industry-academic-government collaboration, and it accelerates and expands the development of the clay film (AIST press release on September 13, 2010). Sumitomo Seika, which has been expanding into the development of highly functional materials such as the materials related to renewable energy technologies, focused on the clay film technology of AIST and began joint research.
This research discovered, from among the many combinations of clay and plastic, a heat-resistant film with dramatically improved handling as compared to the conventional clay film. This discovery was combined with TUS Associate Professor Yamashita’s knowledge of polyimide and further improvements in handling and understanding of excellent film characteristics have been achieved. The research has resulted in the prospect of continuous production of rolls of the film required as industrial sheet material.
Details of Research
Clay films were prepared with many different combinations of clay and plastic, since there is no particular limit on the kind of clay and plastic used. The results indicated that mixing specially processed non-swelling clay and polyimide at an optimal ratio yields a strong film with improved fragility. The film showed little difference in size before and after heat treatment and a markedly improved water vapor barrier property. In general, it is considered good if plate-like clay crystals about 1 nm thick are mixed in a completely isolated state with the plastic in a nano-composite material of clay and plastic, and the polarities of clay crystals and plastic need to be close to each other. The non-swelling clay used in this research is non-polar, so it would not have a good affinity with polyimide, a polar plastic, but because of an improved mixing technique, etc., the researchers were able to realize a film material with the excellent properties of clay and the good handling property of polyimide.
This film was produced by casting a raw material paste, then drying the solvent and subsequently heating the material. The paste was prepared by dispersing specially processed non-swelling clay in a solvent in which polyimide was dissolved. Until now, as a large amount of solvent is required to achieve a uniform raw material paste, the time required for drying made continuous production difficult. However, the use of specially processed non-swelling clay made it possible to reduce the amount of solvent. The researchers furthermore ran the trials repeatedly in production equipment with a furnace capable of temperatures up to 350°C, establishing production methods and conditions for rolls of the film up to 50 cm wide with thicknesses from 30 to 120 µm.
The newly developed film (80 µm thick) was heat-resistant at 450°C and showed very little shrinkage (0.04%) after heating from room temperature to 350°C. These characteristics enable production of very fine electronic circuits on the film with such methods as printing (Fig. 1). Additionally, the newly developed film has a low linear thermal expansion coefficient (the ratio of change in length to increase in temperature) of approximately 10 ppm/°C, the highest level of noncombustibility among plastic materials, about the same electrical insulation as polyimide, even lower moisture absorbency than polyimide, and other characteristics. This film material has a water vapor barrier property sufficient for use as the back sheet of crystal silicon solar cells (developed film in Fig. 2), the researchers also succeeded in aligning the clay crystals parallel to the film surface and further improving the water vapor barrier property (improved developed film in Fig. 2).
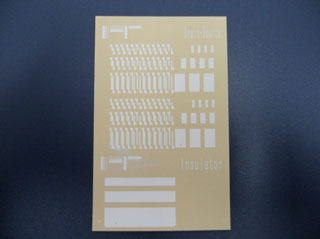 |
Figure 1 : Example of electronic circuits drawn
by a printing method on the developed film (film size 8 cm×5 cm) |
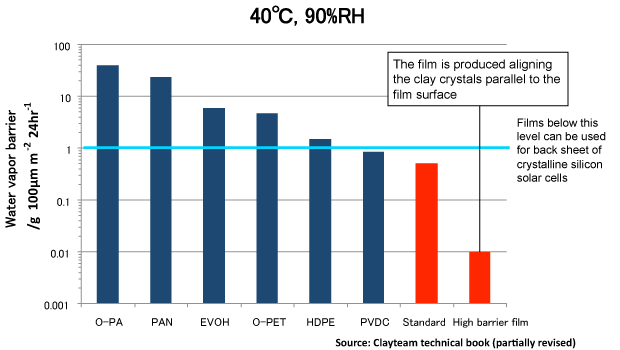 |
Figure 2 : Comparison of water vapor barrier properties of typical films |
Future Plans
The researchers aim to conduct a wider range of performance evaluation of the newly developed material, evaluate long-term durability, establish a mass-production system, and have commercial products available within six months. Additionally, Sumitomo Seika will begin supplying test samples and the researchers will explore applications using the properties of the film. Specifically, they are currently examining use in printable electronics substrates, sensor substrates, storage batteries, power electronics materials, and other applications. The researchers plan to evaluate durability and weather resistance in regards to the application as back sheets of solar cells.