- Dispersion of boron nitride fine particles results in dramatic improvement in resistance to thermal shocks -
Hideki Hyuga (Researcher) and others of Ceramic Mechanical Parts Processing Group (Leader: Hideki Kita), the Advanced Manufacturing Research Institute (Director: Norimitsu Murayama) of the National Institute of Advanced Industrial Science and Technology (AIST; President: Tamotsu Nomakuchi), in collaboration with Mitsui Mining & Smelting Co., Ltd. (Mitsui Kinzoku; President and Representative Director: Sadao Senda), have developed a silicon nitride ceramic material which displays significantly higher resistance to thermal shocks and strength at high temperatures than conventional silicon nitride ceramics.
Using silicon nitride (Si3N4) as a base, a material with significantly increased resistance to thermal shocks was developed by forming a grain boundary phase with high thermal conductivity and dispersing almost amorphous nanometer-order particles of boron nitride (BN) in the grain boundary phase. While the strength of conventional silicon nitride ceramics declines at a temperature difference of 1,000 °C, there was almost no deterioration in the strength of the developed material even when heated to 1,400 °C in an electric furnace and dropped into water ten times. In addition, the material displayed the same level of strength in high-temperature bending tests conducted in air at 1,200 °C as at room temperature.
In many cases, the characteristics of ceramics achieved in small test pieces are no longer obtained when the object is increased in size, and this hinders the practical use of the ceramics. However, in the case of the developed material, optimization of the sintering conditions enabled an identical structure and properties to be obtained in a comparatively large part (diameter: 82 mm; length: 370 mm) as in a test piece. In addition, it was possible to sinter samples that were close in form to actual products.
Part of the results was used in “Development of Revolutionary Energy-saving Ceramics Manufacturing Technology,” a project commissioned by the New Energy and Industrial Technology Development Organization. The results will be presented at the 3rd International Congress on Ceramics (ICC3) to be held in Osaka from November 14 to 18, 2010.
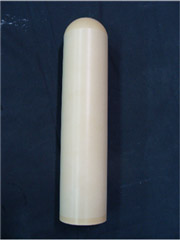 |
Figure 1 : Prototype tube-shaped part for use in molten metal processing (diameter: 82 mm; length: 370 mm) |
There is a global movement towards the regulation of emissions of carbon dioxide, and it is essential to reduce heat energy loss in the production processes employed in the steel and the nonferrous metals industries and to extend the maintenance intervals of cast parts. In order to respond to these needs, silicon nitride ceramics with excellent heat and corrosion resistance are used as a material for protecting tubes, ladles, stalks, heater tubes, and other parts employed in casting processes for aluminum and other metals. However, while silicon nitride displays excellent high-temperature and thermal-shock characteristics, it possesses insufficient heat resistance and resistance to thermal shocks to enable it to be used in casting iron, etc., where it would be exposed to higher temperatures and more severe thermal shocks than in aluminum casting processes. Given this, the realization of silicon nitride ceramics possessing superior thermal characteristics and the ability to be used in the manufacture of large products and products with complex shapes was desired.
(1) Reducing the coefficient of thermal expansion, (2) reducing the elastic modulus, and (3) increasing the thermal conductivity are known as methods of increasing resistance to thermal shocks, and to date this property has been improved by the individual application of these methods. However, the simple application of individual methods has not enabled the realization of a material with a resistance to thermal shocks exceeding 1,200 °C. A further problem is the fact that when a secondary phase is added in order to reduce the elastic modulus, densification does not proceed unless hot pressing or other pressure sintering methods are used, and large products and products with complex shapes cannot be formed.
AIST and Mitsui Kinzoku have collaborated in research and development with the goal of increasing the resistance to thermal shocks and heat resistance of conventional silicon nitride ceramics. In this study, the increase in heat resistance and thermal conductivity of the grain boundary phase in silicon nitride ceramics and the reduction of the elastic modulus of the phase through the addition of a secondary phase were combined, in order to suppress declines in strength at room temperature and to achieve increased thermal conductivity and a reduced elastic modulus simultaneously and thus develop a material with superior heat resistance and resistance to thermal shocks.
The initial focus was on the thermal conductivity of the grain boundary phase of silicon nitride ceramics. The grain boundary phase is usually amorphous, and is one of the causes of declines in the thermal conductivity of the material. Ytterbium oxide (Yb2O3), which would form a grain boundary phase with high thermal conductivity when it crystallized, was used as the sintering aid to make up the main constituent of the grain boundary phase. The thermal conductivity of the material was increased by controlling the amount of Yb2O3 and the sintering method and crystallizing the grain boundary phase during sintering. In addition, by controlling the amount of boron nitride fine particles added as the secondary phase, the elastic modulus was reduced and the stress generated when the material receives a thermal shock was relaxed at the boron nitride particles, thus any generated micro-cracks do not propagate when the material is subjected to further thermal shocks (Fig. 2).
 |
Figure 2 : Schematic illustration of the microstructure of the developed material |
The silicon nitride ceramic formed using this method displays an unprecedented level of resistance to thermal shocks, with no deterioration in strength even when exposed to thermal shocks of 1,400 °C. The material maintained its initial level of strength when subjected to repeated thermal shock tests (Fig. 3).
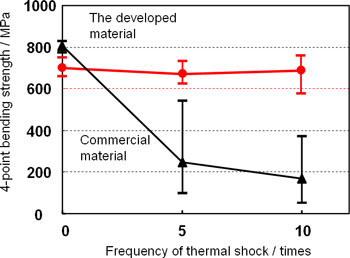 |
Figure 3 : Strengths after thermal shock tests at 1,400 °C |
In order to realize these thermal properties, it was found to be necessary that the crystallized grain boundary is a specific crystal phase (Yb4Si2N2O7) (Fig. 4) and the added boron nitride particles exist as fine particles in the grains and in the grain boundaries in an appropriate dispersion state in order to prevent the grain boundary from becoming origins of cracks (Fig. 5). In addition, when the optimum amount of boron nitride particles is added, the room-temperature strength of the material does not decline significantly at high temperatures like conventional thermal shock-resistant materials and the material exhibits both high strength at room temperature and excellent resistance to thermal shocks. High-temperature bending tests conducted at 1,200 °C in air showed that the developed material maintained the same level of strength as at room temperature due to the formation of a crystalline Yb4Si2N2O7 grain boundary that tends not to soften at high temperatures. It is necessary to control the sintering conditions for this material extremely strictly, and to date it has only been possible to produce samples of the same size as test pieces. However, optimization of the sintering conditions has enabled sintering of the material to achieve identical performance to a test piece in comparatively large parts such as the protecting tubes, ladles, stalks, and heater tubes used in molten metal processing. This has significantly increased the potential for the material to be employed in the manufacture of actual parts.
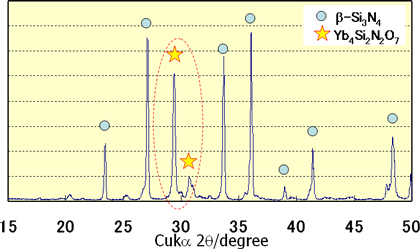 |
Figure 4 : X-ray diffraction pattern of the developed material |
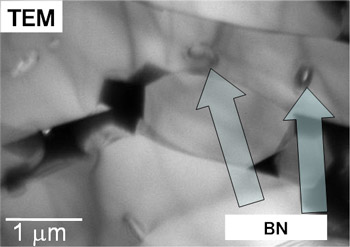 |
Figure 5 : Transmission electron microscope image of the obtained sintered body |
In the future, technologies for the practical use of the developed material as large parts not only in aluminum casting processes but also in zinc, cast iron, and iron and steel casting processes in which the parts will be exposed to more severe conditions.