- Starting sample shipment of wide (300 mm in width) commercial magnesium alloy sheets press-formable at room temperature -
Michiru Sakamoto (Deputy Director) of the Materials Research Institute for Sustainable Development (MRISUS) (Director: Mamoru Nakamura) and Yasumasa Chino (Leader), Kazutaka Suzuki (Senior Research Scientist) and Xinsheng Huang (Research Scientist) of the Group for structural metals design, MRISUS, the National Institute of Advanced Industrial Science and Technology (AIST) (President: Tamotsu Nomakuchi), Mamoru Mabuchi (Professor) of Kyoto University, and Hitachi Metals, Ltd. have jointly developed a new rolling process, which can provide a wide (300 mm in width) commercial magnesium alloy sheet (including AZ31 alloy) with excellent room-temperature formability comparable to aluminum alloy sheets (Fig. 1).
It is known that room-temperature formability of a magnesium alloy sheet is much lower than those of steel and aluminum alloy sheets. Thus, in the conventional press-forming process of a magnesium alloy sheet, the sheet and dies must be heated (above 250 °C). In the newly developed rolling process, a commercial magnesium alloy sheet is rolled at about 100 °C higher temperature than that in the conventional rolling process (lower than 400 °C). The magnesium alloy sheet produced using the new rolling process exhibits a significantly weak crystal orientation, resulting in the excellent room-temperature formability comparable to those of aluminum alloy sheets. This means that a conventional press-forming machine without heating equipment can be used to press the new magnesium alloy sheets and that significant cost reduction and enhanced productivity can be expected. In addition, since composition of the new magnesium alloy sheet is the same as those of commercial magnesium alloy sheets, conventional surface treatment processes and joining processes are readily applicable.
The details of the development will be presented at the 280th Symposium on Technology of Plasticity, held on January 29, 2010, at Campus Plaza Kyoto.
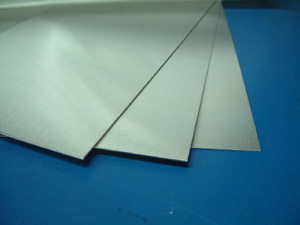 |
Figure 1 Photograph of the commercial magnesium alloy (AZ31 alloy) sheets processed by the new rolling process (width: 300 mm, thickness: 0.6 mm). |
Magnesium alloys are promising light-weight structural materials due to their high specific strength, high specific stiffness, and an abundance of resources. Now, utilization of cast magnesium alloy products is expanding, particularly in the automobile industry and the consumer electronics industry (e.g., laptop PC and cellular phone, etc.). Hereafter, development of rolled magnesium alloy sheets which can be made into parts by press-forming will be required because they are the essential material for constructing further large light-weight components. However, since rolled magnesium alloy sheets exhibit poor room-temperature formability, press-forming must be carried out at elevated temperature (above 250 °C), where installation of additional equipment for heating the sheet and dies is inevitable. This is the main reason for significant cost increase in press-forming of magnesium alloy sheets.
Since realization of the press-forming with a conventional machine without heating equipment would result in significant processing cost reduction and improved productivity, the development of new technology is aspired.
AIST has been conducting research on the control of magnesium alloy composition to develop a new magnesium alloy sheet with high room-temperature formability. Recently, AIST found that a hot-rolled magnesium-zinc alloy with dilute content of cerium exhibits excellent room-temperature formability equivalent to those of aluminum alloys. (This topic was press-released on September 16, 2008, and details were published in a journal, Materials Transactions, Vol.49 (2008) p.1710 and p.2916.)
Some problems, however, have come up, namely conventional surface treatment and joining processes cannot be applied to the new magnesium alloy, because there is a large deference in composition between the new magnesium alloy and commercial magnesium alloys (AZ31 alloy, etc.). These problems make it difficult to put the new magnesium alloy into practical use.
In order to resolve these problems, research and development in a new rolling process improving room-temperature formability of commercial magnesium alloy sheets without any change in their composition have been continued.
It is known that magnesium shows much poor ductility compared with aluminum and steel due to its crystal anisotropy. Figure 2 shows main deformation mechanisms of magnesium and their critical resolved shear stresses (CRSSs) at various temperatures.
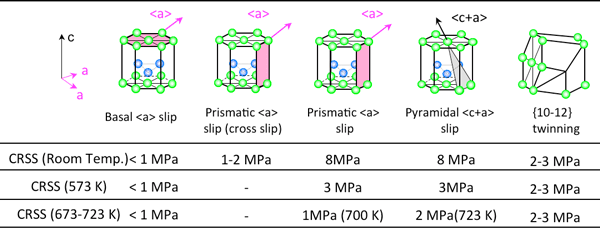 |
Figure 2 Deformation mechanisms of magnesium and their critical resolved shear stress at various temperatures |
Main deformation mechanisms of magnesium are composed of three slips (basal, prismatic and pyramidal slips) and twinning (such as {10-12} twinning). The deformation of magnesium along c-axis is attributed to the pyramidal slip. Since CRSS of the pyramidal slip is much larger than those of the other deformation mechanisms at room temperature, it is difficult to deform magnesium in the c-axis direction (vertical direction in Fig. 2) at room temperature.
In general, when a compressive stress vertical to the c-axis direction is imposed on a magnesium crystal, upper half of the magnesium crystal is rotated on {10-12} plane. This deformation mechanism is called {10-12} twinning. When {10-12} twinning occurs, the basal plane is rotated about 90° as shown in Fig. 3 (left). Since a compressive stress is inevitably imposed on a magnesium alloy during a rolling process, {10-12} twinning is easily occurred during the rolling process if the c-axes of magnesium crystals are aligned parallel to the rolling direction (blue frame in Fig. 3). On the contrary, {10-12} twinning hardly occurs, if the c-axes are aligned perpendicular to the rolling direction (red frame in Fig. 3). Consequently, a rolled magnesium alloy exhibits a strong crystal orientation, in which the c-axes are aligned perpendicular to the rolling direction (and basal planes are aligned parallel to the rolling direction.) When a magnesium alloy sheet exhibits the strong crystal orientation, basal and prismatic slips (cross slip), which are the main deformation mechanisms of magnesium crystals at room temperature, can operate along the rolling and width directions, but not along the thickness direction. Therefore, the rolled magnesium alloy sheet hardly deforms along the thickness direction, resulting in a fracture at an initial stage of the press-forming at room temperature. Thus, it is recognized that the press-forming of magnesium alloy sheets at room temperature is extremely difficult.
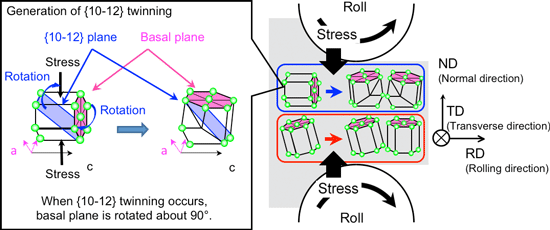 |
Figure 3 Texture formation of rolled magnesium |
For the reason described above, it is important to prevent the formation of the strong crystal orientation during rolling process in order to improve room-temperature formability (Fig. 4). Namely, it is necessary to control the orientation of crystals during the rolling process and to form a crystal orientation which allows basal and prismatic slips (cross slip) to operate along the thickness direction.
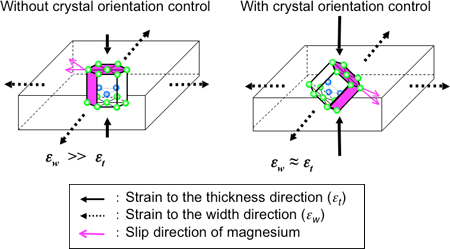 |
Figure 4 Relationship between crystal orientation and room temperature formability |
The new rolling process is characterized by high rolling temperature, which is about 100 °C higher than that of a conventional rolling process (below 400 °C). Pole figures of basal plane of the AZ31 alloy sheets processed by the new rolling process and by the conventional rolling process (rolling temperature: 390 °C) are shown in Fig. 5.
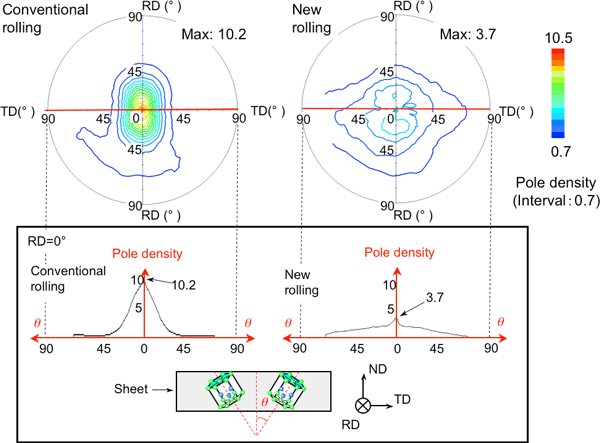 |
Figure 5 Pole figures of basal planes of AZ31 alloy sheets processed by conventional rolling and new rolling (upper) and orientation distribution of basal planes relative to the TD when orientation distribution of basal planes relative to the RD is set to 0° (bottom). |
Pole figure of basal plane represents the orientation distribution of basal planes relative to a set of directions (RD: rolling direction and TD: transverse direction). When the orientations are concentrated to a specific angle, pole density at the angle shows high value. For simplicity, the orientation distribution of basal planes relative to the TD is shown in the bottom of Fig. 5, where the orientation of basal planes relative to the RD is set to 0° (red line in Fig. 5 top). The pole figures of basal planes of both magnesium alloy sheets exhibit the same tendency, where the high pole density is observed at TD=0°, indicating that the major part of basal planes is distributed parallel to the sheet surface. However, the pole density of the magnesium alloy sheet processed by the new rolling process (3.7) is much smaller compared with that of the magnesium alloy sheet processed by the conventional rolling process (10.2). It means that the high temperature rolling contributes to remarkable suppression of the orientation of basal planes along the sheet surface. As a result, the AZ31 sheet processed by the high temperature rolling can deform along the thickness direction, and exhibits significant room-temperature formability (Erichsen value=8.0) equivalent to that of an aluminum alloy sheet (5083 aluminum alloy: Erichsen value=8.5), as shown in Fig. 6.
One reason for the suppression of orientation of basal planes by the high temperature rolling is the temperature dependence of CRSSs of a magnesium crystal. As shown in Fig. 2, temperature dependence of CRSSs of non-basal slips (prismatic slip and pyramidal slip) are much higher than those of basal slip and {10-12} twinning. CRSSs of basal slip and {10-12} twinning in the temperature range from room temperature to 300 °C are smaller than those of the non-basal slips. CRSSs of non-basal slips significantly decrease at temperatures higher than 450 °C, and exhibit almost the same value as CRSSs of basal slips and {10-12} twinning. This means that rolling at high temperature (around 500 °C) promotes activation of non-basal slips and suppression of {10-12} twinning during the rolling, resulting in the retardation of the strong crystal orientation.
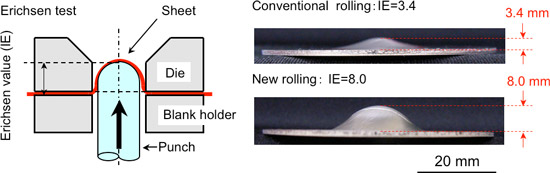 |
Figure 6 Schematic of Erichsen test (left) and results of Erichsen test for AZ31 alloy sheets processed by conventional rolling and new rolling (right) |
In the new rolling process, room-temperature formability of a commercial magnesium alloy sheet can be significantly improved without modifying its alloy composition. This means that conventional surface treatment processes and joining processes are readily applicable to the new magnesium alloy sheets.
In late January 2010, Hitachi Metals, Ltd. (Yasugi works) will started the sample shipment of commercial magnesium alloy sheets (AZ31 alloy sheets) with 300 mm width and 0.3-0.6 mm thickness processed by the new rolling process. When the new magnesium alloy sheets are taken to the market, ordinary metalworking factories can press-form magnesium alloy sheets by using a conventional press-forming machine. Thus, application range of the press-formed magnesium alloy sheets is expected to be drastically expanded.
Study on the practical use of the new magnesium alloy sheets will be cooperatively carried out with metalworking businesses aiming at a wide range of applications of the sheets.