Update(MM/DD/YYYY):12/16/2009
Microwave-assisted Polymer Synthesis
- First commercial plant for mass production of lactic acid polymer using a microwave heating -
Points
-
Development of the world's first commercial plant of microwave-assisted polymer synthesis process
-
Achievement of mass production of a polymer with consistent quality by greatly reducing the manufacturing time
-
Achievement of 70% reduction in CO2 emissions as compared to the conventional heating method
Summary
Kazuhiko Takeuchi (Senior Research Scientist) and Ritsuko Nagahata (Senior Research Scientist) of the Renewable Plastics Group (Leader: Masao Kunioka), the Research Institute for Innovation in Sustainable Chemistry (Director: Masaru Nakaiwa) of the National Institute of Advanced Industrial Science and Technology (AIST) (President: Tamotsu Nomakuchi), the New Energy and Industrial Technology Development Organization (NEDO) (Chairman: Seiji Murata), GLART Inc. (GLART) (President and Chief Executive Officer: Hiroshi Yamaguchi), and Shikoku Instrumentation Co., Ltd. (President/Director: Yukio Shinomiya) jointly developed a device for the mass production of polymers using microwaves and practically applied to an energy-saving process for polymerization of lactic acid for the first time in the world.
The use of microwave heating for the synthesis of organic compounds and polymeric materials is expected to offer many advantages, including substantial reduction of reaction time, reduction of the amount of wastes generated, energy savings, and reduction of CO2 emissions. Although many studies have been conducted on microwave heating for such synthesis, there are few examples of its practical use. AIST has developed highly efficient techniques for producing organic compounds and polymeric materials by using microwaves. This joint research has resulted in an increase in the efficiency of energy use by improving irradiation methods and developed a safe device in which leakage of microwaves is prevented. Therefore, practical use of this technology is now within sight.
GLART had previously been producing oligolactic acid, a functional food material, by using multiple small-scale production lines with electrothermal heaters. Introduction of the developed device resulted in mass produced polymers with consistent quality and a 70% reduction of CO2 emissions as compared to the conventional method due to significant decrease in manufacturing time and energy consumption.
A part of this study was obtained in the research entitled "Investigation on extremely rapid synthesis of bio-based polymers by microwave" (Research representative: Ritsuko Nagahata, Senior Research Scientist), supported by a NEDO Industrial Technology Research Program in 2006.
Details of this technology will be presented at the Third Symposium on Japan Society of Electromagnetic Wave Energy Applications, held on November 19 and 20, 2009, at Tokyo University of Science (Kagurazaka Campus), and will also be presented at Chemical Plant Engineering Show (INCHEM TOKYO 2009), held on November 18 to 20, 2009, at Tokyo Big Sight.
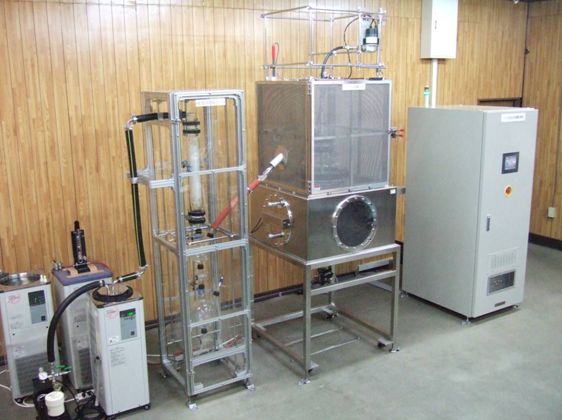 |
Microwave-assisted polymerization process
Plant for microwave-assisted polymer synthesis |
Social Background for Research
In general, manufacturing of industrial chemicals such as organic compounds and polymeric materials often involves reactions carried out at high temperature for a long time, use of large amounts of organic solvents, and generation of harmful wastes as by-products. As one of the countermeasures against global warming, there is an urgent requirement for the development of technologies that can reduce CO2 emissions in manufacturing processes of industrial chemicals by improving their production efficiency. Since the production of polymeric materials such as polyester, in particular, requires reactions to be carried out at high temperature and for a long time, it is desirable to develop energy-saving production processes that do not generate wastes.
Lactic acid polymers such as polylactic acid and oligolactic acid are produced from raw materials obtained by fermenting biomass resources such as corn and sugarcane. Such polymers have good transparency and are used as bio-degradable polymeric materials for agricultural mulch-films, greenhouse films, and cases of home electrical appliances. Owing to the bio-degradability of lactic acid polymers, they are also used for functional food materials and medical materials such as sutures, artificial bones, and controlled-release drug preparations. A lactic acid polymer is synthesized by condensation polymerization of lactic acid. The reaction generally requires mineral acids such as sulfuric acid and tin compounds as catalysts and is carried out at high temperature for a long time due to the low reactivity of lactic acid. However, since lactic acid polymers used for medical purposes and functional foods directly enter the human body, it is preferable to prevent the use of toxic catalysts as much as possible. Therefore, in spite of the fact that the polymers have low molecular weight, they have thus far been produced without catalysts and require a long time, resulting in the production process having low energy efficiency. In addition, since a long reaction time easily generates by-products having different structures, closest attention has been paid to producing high-quality polymers. With this background, efficient mass-production processes with low environmental loads, which produce polymers with consistent quality, have been called for.
History of Research
Since microwaves can heat substances directly, rapidly, and uniformly, they have not only been used in domestic microwave ovens but also found wide applications in industry. AIST has noticed the usefulness of microwaves in syntheses of organic compounds and polymeric materials in early times and has conducted researches on highly efficient manufacturing processes that employ microwaves. AIST has focused on the synthesis of polyester which would be accelerated by using microwave-irradiation. The reaction is expected to be accelerated, as the raw materials of the reaction, carboxylic acid and alcohol, and released water molecules have high polarity. AIST developed a highly efficient production process for polyester using microwave-irradiation, in which the reaction time was reduced to about one-tenth.
GLART has been manufacturing oligolactic acid as a functional food. However, GLART desired to replace the conventional manufacturing process with a new manufacturing process that is highly efficient and can be used to mass-produce a high-quality product in order to cope with increasing demand and for high-quality products. For this purpose, GLART and AIST decided to jointly develop a new manufacturing process, to which AIST's microwave polymerization technology is applied.
Details of Research
A lactic acid polymer is synthesized by condensation polymerization of lactic acid. The reaction generally requires mineral acids such as tin compounds and sulfuric acid as catalysts and is carried out at high temperature for a long time due to the low reactivity of lactic acid. AIST found that by applying microwave irradiation to the polymerization of lactic acid, the reaction proceeded relatively fast without catalysts such as tin compounds and sulfuric acid and applied for a patent for this process. It is considered that the reaction proceeds fast because microwaves efficiently heat the polar intermediates of the reaction. Application of this technology to the synthesis of oligolactic acid that GLART usually produces markedly accelerated the reaction and greatly reduced the amount of required energy as compared to the conventional method using an electrical heater.
Next, to practically apply this method, AIST started to develop a new device for the mass production of polymers using microwaves in cooperation with Shikoku Instrumentation Co. Ltd. A reaction vessel was designed, in which microwaves were absorbed as efficiently as possible by precisely controlling the distribution of the electromagnetic field of microwaves. In addition, since the reaction system in this method becomes highly viscous, a technology for handing of viscous liquid was also developed. Further, reliable safety measures against concerns such as leakage or discharge of microwaves were developed and installed in the device. As a result, the practical mass-production device was realized.
Since the lactic acid polymer produced by this device is intended to be used for medical treatment and functional foods, quality control of the product is extremely important. Consistent high quality was achieved by determining a reaction condition under which high-quality polymer is produced.
By irradiating aqueous solution of lactic acid, which is the raw material, with 6 kW and 2.45 GHz microwaves, the developed device can synthesize oligolactic acid more rapidly than the conventional method can. The production scale is approximately 20 kg per batch, and high efficiency and consistent quality are ensured. GLART, which had previously been producing oligolactic acid by operating multiple small-scale production lines with electrothermal heaters for a long time, introduced this device and achieved stable, brief mass production of the polymer with quality equal to or higher than the quality of the product produced by the conventional method. In addition, because of reduction in the amount of required energy, the device achieved a 70% reduction of CO2 emissions as compared to the conventional method and contributed to the reduction of environmental loads. Since the developed device needs a shorter reaction time than the usual heating method does, the device employing microwaves barely generates by-products having different structures. It can be said that the approach of utilizing microwaves is suitable for synthesizing materials for functional foods.
Future Schedule
AIST will extend the application of this technology to not only esterification and condensation polymerization but also other synthesizing processes of various organic compounds and polymeric materials, distillation and extraction processes. AIST also hopes to contribute to progress green technologies in the chemical industry by achieving, for example, (1) a considerable reduction of CO2 emissions by reducing the amount of energy required for chemical processes, (2) disuse of solvents, (3) green chemistry by reduction of wastes, and (4) improvement in quality of products.