Nozomu Mishima (Leader), Tsuneo Kurita (Research Scientist), and others of the Environmentally Conscious Design and Manufacturing Group, the Advanced Manufacturing Research Institute (Director: Hideto Mitome), the National Institute of Advanced Industrial Science and Technology (AIST) (President: Hiroyuki Yoshikawa) have developed a combined laser and electrochemical machining system that can machine a microscopic metal tube with a diameter of less than 100 µm into a complex shape. Machining of high-value added devices can be realized by applying the technology, for example, to catheters or stents for brain surgery or to contact probes for inspection of high-density electronic circuits, for which no existing microscopic complex machining technology has so far been applicable.
Existing machining technologies have several problems: machining is sometimes impossible because the minute tube to be machined and the working tool come into contact with each other at a point other than the machining position; a tube of too small a diameter cannot be machined because it is easily bent by the tool contact force during machining; and finally, a general problem in any minute tube machining technology is that the tube cannot be precisely held. As a result of these problems, it has been difficult to machine a metal tube of a diameter of less than 300 µm into a complex shape.
The newly developed system adopts a non-contact laser machining technology in which the tube is not subjected to force during machining. As the same laser light source is used for both machining and measurement, no displacement appears between the measured and the machined positions, and the laser beam is irradiated on the precise position by means of an error-compensation—even if the target tube has holding-position errors in rotating center and slope. Through electrochemical finish machining, the heat-affected layer inherent to laser machining is removed to provide a smooth surface. Once attached, the machining workpiece does not need to be detached during the two-step processes, and a stainless tube the size of a human hair can be machined into a complex shape.
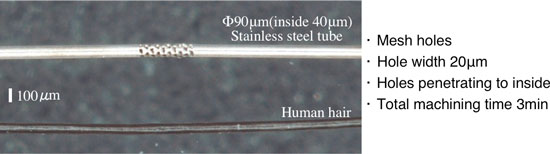 |
Laser and electrochemical complex machining |
Medical instruments such as catheters and stents require microscopic diameters of less than 200 µm to meet the needs of brain surgery. In the electronics industry, contact probes for the inspection of high-density electronic circuits urgently require diameters of less than 100 µm due to the recent scaling down of circuits. Despite the requirement for medical and electronic applications, it has been difficult to machine microscopic metal tubes of a diameter of less than 300 µm into complex shapes.
Electro-discharge or mechanical machining technology has so far been used for the machining of microscopic tubes. There are, however, a few serious problems: (1) it is difficult to finely control the relative position between the microscopic tube and the machining tool (electrode); (2) machining is sometimes impossible because the tube and the working tool make contact at a point other than the machining position; (3) machining of a microscopic tube with too small a diameter is difficult with mechanical machining because force must be applied during machining and a change in the tube shape may occur as a result. Now while non-contact laser machining can overcome this problem because no force is needed for machining, it has an inherent problem in that the relative position between a microscopic tube and a laser beam cannot be very well set or detected. Furthermore, there is another problem common to all machining technologies, namely that a microscopic tube cannot be precisely held. Thus there has been a pressing need to develop a new machining system that can solve the problems mentioned above in machining a microscopic tube into a complex shape.
AIST has long been studying a complex machining technology in which multiple machining tools, each of which is well-suited for machining a target object, are set up in the same system to be used simultaneously or sequentially, and so once a machining target is put in the system, multiple high-efficiency high-precision machining tools are used to machine the target without removing the workpiece. Specifically, AIST has developed or constructed prototypes of: "complex machining technologies" in which mechanical, electro-discharge, electrochemical, and beam machining technologies are combined; "desktop multiprocess machinery" in which each individual module contains a machining tool and the machining combination can be modified by exchanging modules; and "ion-controlling desktop machine tool" in which multiple machining steps are performed in a device by means of controlling the electrical conductivity of the machining liquid.
Based on the concept of combined machining, in the newly developed laser and electrochemical complex machining system, a microscopic tube, which is difficult to machine mechanically, is machined into a complex shape by laser and electrochemical machining technologies combined within one system, and high-efficiency high-precision machining is realized without detaching the workpiece once it has been set in a machine. Figure 1 shows the developed laser and electrochemical complex machining system. By using the system, high-value added tubular devices of diameters of less than 300 µm can be fabricated efficiently, a level of work that other machining technologies cannot achieve.
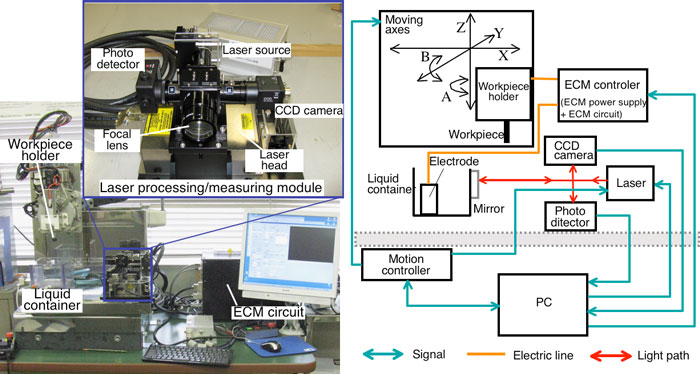 |
Fig. 1 Developed laser and electrochemical complex machining system |
The newly developed technologies are as follows:
1) Laser machining technology with holding position error correction
As laser machining is a non-contact process, it is intrinsically difficult to set and detect the relative position between the machining target (microscopic tube) and the laser-irradiated position. Ordinary practice is to use another laser light source, independently of the one used for machining, for measuring the relative position and the posture of the workpiece (microscopic tube). Note that if another laser light source is used, the light axis must be adjusted against the laser beam used for machining; the adjustment of light axes requires a high level of expertise and, in addition, precise adjustment is difficult, and the error is directly reflected in the error in machining and measured positions. If the wavelengths for the machining and measuring lasers are different, they cannot share the same optical path because the refractive indexes of optical parts including lenses may vary. The use of two optical systems for machining and measuring results in increased system size and complexity, and creates a major problem. The newly invented system uses a single laser light source for both machining and measurement. Figure 2 shows the setup of the optical system for laser machining/measurement adopted in the developed system. In this optical system, no displacement appears between the machined and the measured positions because the same light source is used both ways. Therefore, even for an extremely minute tube in which the holding position cannot be kept constant, the holding position is corrected through stage movement, and the laser is irradiated precisely to the required position. Significant downsizing of the system is realized without adding an additional optical system for measurement/observation.
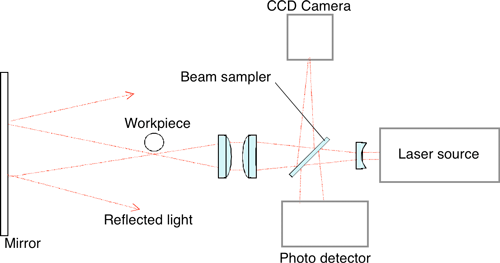 |
Fig. 2 Optical system for laser-beam machining and measurement |
2) Electrochemical machining technology with holding position error correction
In the newly invented system, electrochemical finish machining is performed to remove the heat-affected layer caused by laser machining. In electrochemical machining, control of the gap between workpiece and electrode is important. Furthermore, rotation of the microscopic tube is required during electrochemical machining. In the new system, the gap between the tube and electrode is maintained at a constant amount by synchronizing the rotation of the tube based on the result of above-mentioned posture measurement. This mechanism realizes high-precision control of finish machining and of machining amount.
Through the combined use of microscopic laser machining (shape machining) and microscopic electrochemical machining (finish machining), the elimination quantity in and the machining time of finish machining is minimized in machining, for example, catheters or stents for brain surgery or contact probes for inspection of high-density electronic circuits; thus, higher machining efficiency is realized.
3) Development of control software
Control software has been developed to realize laser and electrochemical machining with holding position error correction. Figure 3 shows the control panel of the software. The newly developed software has an automatic detection capability for posture measurement, and the laser and electrochemical machining processes are controlled via the panel.
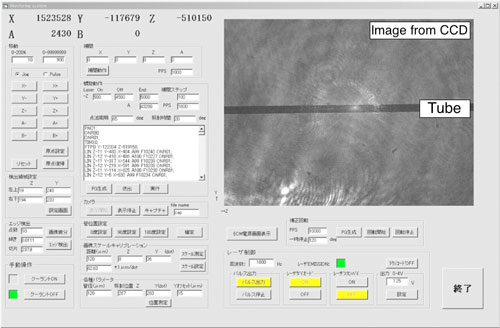 |
Fig. 3 Control panel of the control software for laser and electrochemical complex machining system |
4) Machining of a microscopic tube into a complex shape
To substantiate the effectiveness of the system, the surface of a microscopic stainless steel tube with an outer diameter of 120 µm and an inner diameter 40 of µm is micro-machined using the combined laser measurement/machining and electrochemical machining techniques. Figure 4(a) shows the spiral groove formed on the tube. A holding error is expected in the microscopic tube, and the tube edge position can vary as the tube rotates. The developed system has the capability of measuring the tube position/posture by means of a laser measurement system, and of correcting a holding position error, and so the laser-irradiated position can smoothly move in synchronization with the tube rotation. The focal point of the laser beam always agrees accurately with the tube edge, and machining to a complex shape is achieved as shown in the figure. Figure 4(b) shows the result of electrochemical finish machining following the laser machining. Electrochemical machining removes the heat-affected surface layer generated inconveniently during laser machining, and makes the surface smooth.
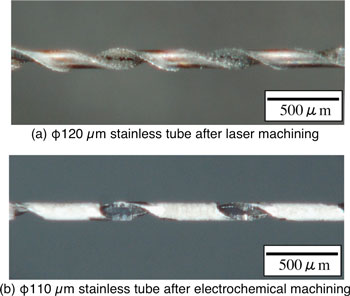 |
Fig. 4 Laser and electrochemically machined stainless steel microscopic tubes
(a) φ120 µmΦ stainless steel tube after laser machining, (b) φ110 µmΦ stainless steel tube after electrochemical machining |
The newly developed laser and electrochemical complex machining system makes it possible to machine the surface of a stainless steel tube the size of a human hair into a complex shape using the laser measurement/machining and subsequent electrochemical machining.
By applying the system to the machining of, for example, catheters for brain blood vessels, new highly functional surgical instruments will be developed.
The newly developed system shall be used to machine practical medical and electronic parts into complex shapes in order to demonstrate the effectiveness of the developed technology. Business organizations will be invited to take part in collaborative research, and we will push ahead with the commercialization of the combined machining system and of laser measurement/machining modules to improve the machining efficiency of existing devices and to create new devices.