Update(MM/DD/YYYY):03/06/2009
Development of a High-efficiency Micro Fuel Cell Module
- A great step toward realizing high-power small-size solid oxide fuel cell systems -
Points
-
A micro solid oxide fuel cell (SOFC) module of size 1 cm3 operates at low temperatures of 450 - 550°C.
-
A power density of larger than 2 W/cm3 is obtained at a temperature of 550°C on air supply by natural diffusion.
-
Small-size, lightweight, portable SOFC systems, which can start and stop rapidly, could be realized.
Summary
Masanobu Awano (Leader), Toshio Suzuki (Research Scientist) and others of the Functional Assembly Technology Group, the Advanced Manufacturing Research Institute (Director: Hideto Mitome), the National Institute of Advanced Industrial Science and Technology (AIST) (President: Hiroyuki Yoshikawa), have developed a micro fuel cell module with small-sized tubular solid oxide fuel cells (SOFC), in collaboration with NGK Spark Plug Co., Ltd. (NGK). The micro fuel cell module has a size of 1 cm3 with small-size tubular SOFCs of diameters ranging from millimeter to sub-millimeter, and achieves the power density of larger than 2 W/cm3 at 550°C.
Compared to other types of fuel cells, SOFCs offer many advantages such as the highest energy conversion efficiency among all fuel cells, high reliability as they are made solely from solid materials, easy handling, and direct use of hydrocarbon fuel. Previously, however, SOFCs required operation temperatures of 800 - 900°C, and so their application was limited to large-scale stationary power supplies. There have been strong demands for the development of SOFCs operable at lower temperatures to enable their application in small-size portable power supplies.
AIST has been involved in developing cubic micro SOFCs in collaboration with NGK; further, to meet the demand for extremely compact fuel cells, this collaboration has successfully developed the micro fuel cell module by optimizing the module design and ceramic electrode microstructure. As a result, the module requires negligible amount of power for feeding air into the porous solid and allows air supply by natural diffusion; thus, a fuel cell system of significantly improved efficiency and reduced size will be achieved by using the newly developed module. In future, this technology will find wide applications in power supplies for small-size portable electronic devices.
The results of the study will be presented at "nano tech 2009" that will be open on February 18–20, 2009, and at "FC EXPO 2009" that will be open on February 25–27, 2009, both of which will be held at Tokyo Big Sight.
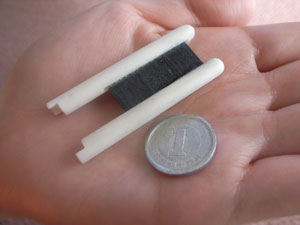
Newly developed micro SOFC module
|
|
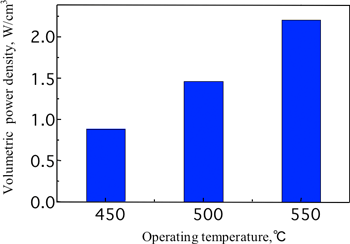
Results of the micro SOFC module performance test
|
Social Background for Research
Fuel cells generate electrical energy directly from the chemical reaction between hydrogen and oxygen; further, they do not emit CO2 and offer high energy-conversion rates. They are recognized as a clean energy source; research and development activities are being conducted to lead fuel cells toward practical application. Fuel cells are classified on the basis of their constituent materials into polymer electrolyte fuel cell (PEFC), molten carbonate fuel cell (MCFC), phosphoric acid fuel cell (PAFC), solid oxide fuel cell (SOFC), and so on. PEFCs have low operating temperature of 100°C and are already developed for home and automobile applications.
On the other hand, SOFCs offer the highest power generation efficiency and reliability compared to other types of fuel cells because they are made from solid materials only. It allows easy handling and the use of hydrocarbon fuel. However, it requires high operation temperatures of 800 - 900°C, and so, its application has been limited to large-scale power generators.
Therefore, there is a great demand of high-efficient SOFCs which lower operating temperatures to 500 - 700°C with rapid start-up and stop features so that their application could be realized in dispersed power sources for home use, power sources for portable electronic devices, and automobile auxiliary power unit.
History of Research
A ceramic reactor, which electrochemically converts material and energy, is considered to contribute to solve a number of environmental issues, and one of promising application is an SOFC. The downsizing and integration of ceramic reactor components are expected to realize a high-performance ceramic reactor with high thermal shock resistance. Further, the application of the downsized and integrated reactors to SOFC is expected to realize lower temperature with rapid start-up and stop operations. Therefore, the aim of our study was the development of high performance SOFC that has high resistant to thermal shock at operation temperatures of 650°C or below.
Various ceramic electrolyte and electrode materials have been developed for decreasing operating temperature. However, a solution to the problem of thermal strain attributable to rapid start-up and stop in the conventional flat-type fuel cells was not solved.
AIST, in cooperation with NGK, attempted to develop tubular micro SOFCs and related technologies of integration and succeeded in the fabrication of cell bundles that enable rapid start-up and stop (AIST press release, March 29, 2007) (Fig. 1).
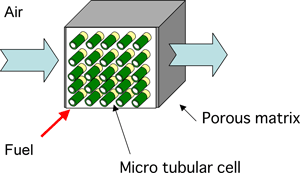 |
Fig. 1 Conventional cubic micro SOFC |
The targets of the tubular micro cell bundles were several 100 W - 1 kW systems and additional technical issues had to be solved in order to realize micro SOFC modules for small-size several W - several 10 W fuel cell systems. Among these technical issues, optimization of the cell position, air passage and thermal balance, which are in tradeoffs, was the most important issue.
This study was carried out as part of the project entitled "Development of Ceramic Reactor" of the New Energy and Industrial Technology Development Organization.
Details of Research
AIST, in cooperation with NGK, has developed a high efficient micro SOFC module using high-performance tubular SOFC of sub-millimeter diameter that can function as a ceramic reactor (Fig. 2). By optimizing the inner structure and the alignment of micro SOFC bundles of this module, the power needed for air supply is minimized, and the thermal balance is easily controlled. The module works with high efficiency even if the supply of air is via natural diffusion. Fuel is fed to the stack through a fuel feed manifold; the air flows along the module surface and is fed into the stack by natural diffusion.
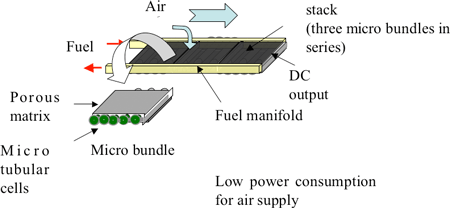 |
Fig. 2 Newly developed micro SOFC module |
The micro-tubular cell adopted in this study is a tube of 0.8-mm diameter, and uses ceria-based ceramic electrolyte, nickel ceria-based ceramic for the anode, and lanthanum cobalt ceria-based ceramic for the cathode. To form a micro bundle, the micro-tubular cells are integrated in the porous structure made of lanthanum cobalt ceramic. Figure 3 shows a stack (0.6 cm3) in which three 10 × 10 × 2 mm micro SOFC bundles (made of five integrated micro-tubular cells) are connected in series.
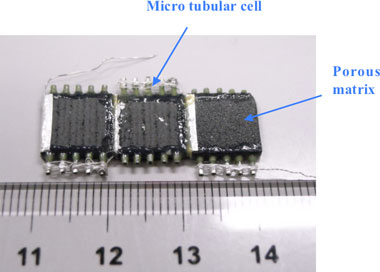 |
Fig. 3 Micro SOFC stack (0.6 cm3) |
A micro SOFC module is obtained by attaching a fuel manifold to this stack structure (Fig. 4).
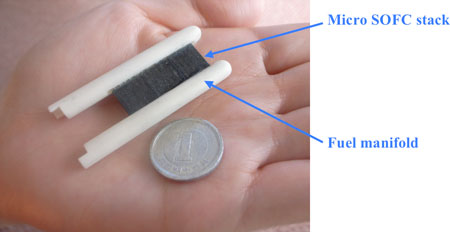 |
Fig. 4 External appearance of a micro SOFC module |
Hydrogen at a temperature of 450 – 550°C was input into the module and power density of 0.88 - 2.2 W/cm3 (450 - 550°C) was confirmed (Fig. 5).
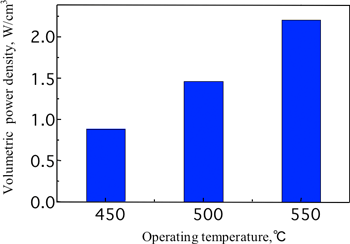 |
Fig. 5 Result of micro SOFC module performance test |
The stack weighs only about 2 g, and provides an excellent power output per weight. With the development of the micro SOFC module, there is a high possibility that portable power sources for small-size electronic devices can be realized, assuming that a several-10 W system can be obtained by stacking adequate number of the modules to fulfill the requirements of electric output power.
Future Schedule
We will pursue additional integration and optimization on the module structure of the newly developed micro SOFC module, and conduct performance verification tests. The target of our research and development activities is a high-output, small-size, high-efficiency SOFC system that is shock-resistant and allows rapid start-up and stop operation.
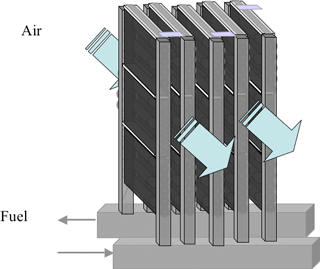 |
Fig. 6 Schematic diagram of a 10-W class module (total volume ≈20 cm3) |