Update(MM/DD/YYYY):10/17/2008
Porous Ceramics with Fine Micrometer-size Pores Fabricated Using Ice
- Realization of combined ultrahigh porosity and high strength -
Points
-
Porous ceramics with over 90% porosity and yet sufficient strength for practical use
-
Simple manufacturing method that is compatible with all types of ceramics and has minimal environmental load
-
Easy control of the size of the pores and porosity
-
A wide range of expected applications, including wastewater recycling and filtering toxic particles from exhaust gasses
Summary
Manabu Fukushima (Research Scientist) and Masayuki Nakata (former Post-Doctoral Research Scientist) et al. of the High-Performance Component Processing Group (Leader: Yuichi Yoshizawa), the Advanced Manufacturing Research Institute (Director: Hideto Mitome) of the National Institute of Advanced Industrial Science and Technology (AIST) (President: Hiroyuki Yoshikawa) have developed a manufacturing technology for ultrahigh-porosity ceramics that have fine, micrometer-size pores, utilizing ice.
The characteristic feature of this manufacturing process is the application of frozen jelly (gel) to the manufacture of porous ceramics. The newly developed gel is composed of a small amount of ceramic powder and a polymer that can hold a large amount of water. When this gel is frozen, ice crystals are formed, which become the source for the fine pores. When this frozen gel is dried (to remove the ice) and sintered, a ceramics with a porosity of over 90% and micrometer-size fine pores is obtained (gelation-freezing method). Because the water (ice) contained in the gel is used to form the pores, the porosity can be controlled by changing the amount of water held in the gel. In addition, because the sizes of ice crystals change with the freezing temperature, the sizes of the pores can be accurately adjusted. Since the method uses the slip casting technique, it can be used to form the complicated shapes used in actual products. It is expected that the porous ceramics will be used for a wide range of applications, for example, in filters and catalyst supports.
With this method, high-porosity porous ceramics were successfully manufactured from silicon carbide, cordierite, alumina, and zirconia, showing that the method is independent of the type of ceramic material used. The obtained porous ceramics have a maximum porosity of 93% and still have sufficient strength to be compatible with not just handling but also machining processes such as cutting and polishing. In addition, the method does not require expert craftsmanship, thereby allowing rapid technology transfer to the industry.
The results are to be presented at the 21st Fall Meeting of the Ceramic Society of Japan to be held in Kitakyushu (September 17 and 18), and at the Materials Science & Technology Conference & Exhibition (MS&T'08) to be held in Pittsburgh, PA, U.S.A. (October 8).
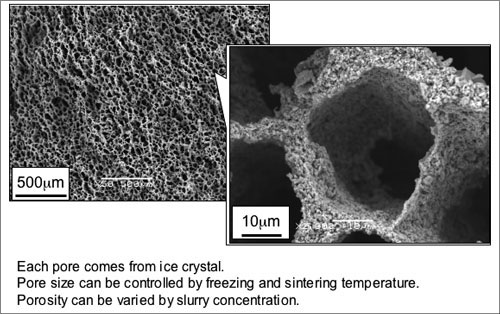 |
Ultrahigh porous silicon carbide (with porosity of 90%) by using gelation-freezing method.
|
Social Background for Research
Porous materials have fine pores (voids) and are used in filters for wastewater and exhaust gas management as well as in environmental detoxification components such as catalyst supports. Since porous ceramics are superior to plastics, resins, and metals in terms of their resistance to heat and corrosion, they can be used in severe environments. In recent years, it has been expected that porous ceramics will be used in a greater number of applications such as in wastewater recycling (filtering toxic substances from wastewater and reusing the water in industries, etc.), which is important from the viewpoint of the efficient use of resources, and in filters removing harmful particles in exhaust gasses from industries and automobiles.
While porous ceramics are conventionally manufactured by sintering raw ceramic powders at a non-densifying temperature, the maximum porosity obtainable is limited to approximately 50 - 60%. Higher porosity levels can be obtained by the addition of large quantities of pore formers such as resin beads and carbon, which are then removed by oxidation. This method is detrimental in that the fine pores formed after the removal of the pore former exist separately, with little interconnection between the pores. Another method is to immerse ceramic slurry into commercially available sponge, which is then removed by oxidation. However, the pore size cannot be controlled and the obtained material is extremely fragile. Furthermore, these methods are also detrimental to the environment in that they generate large amount of carbon dioxide and other toxic gases during the oxidation process.
History of Research
The Advanced Manufacturing Research Institute of AIST has been involved in research and development on higher-order structural control in ceramic components for many years. At an early stage, the institute focused on the above-mentioned problems with the methods for manufacturing porous ceramics, and it has seen steady progress in its efforts to establish a manufacturing method that not only addresses these problems but is also environment-friendly.
Details of Research
The manufacturing method uses a frozen gel containing a small amount of ceramic powder and a large amount of water to fabricate porous ceramics (galation-freezing method). The ice crystals formed within the frozen gel are then removed and the resulting product is sintered to afford a porous ceramic with ultrahigh porosity (Fig. 1). Because water (ice) is the source of the fine pores, the porosity can be controlled by adjusting the amount of water in the gel. The developed gel can hold a large amount of water, which makes it possible to enhance the porosity to approximately 93%. In addition, the fine pore diameter can be adjusted by changing the freezing temperature. The gel freezing process is the same simple procedure as freezing jelly in a household refrigerator. Therefore, anyone with a casting mold and a freezer could easily fabricate high-porosity ceramics; no professional expertise is necessary.
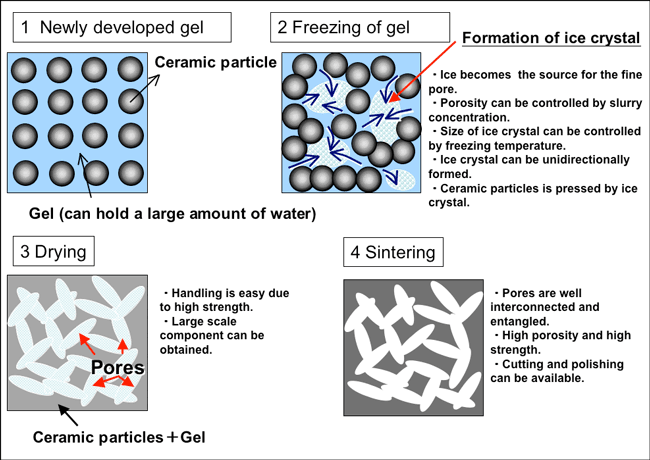 |
Figure 1. Fabrication process of ultrahigh-porosity ceramic.
|
Fig. 2 is a photo of porous silicon carbide with a porosity of 90% fabricated using the developed method. Since the porous ceramics can be formed using a casting mold, it is possible to create shapes (bar, cylinder, plate, etc.) that are quite similar to those of the actual products. The ceramics (with over 90% porosity) can be machined (e.g., cutting and polishing ) after sintering. In addition, the dried or degreased materials can be easily handled. It is assumed that such highly strong castings are obtained because the raw ceramic particles are densified during the freezing process.
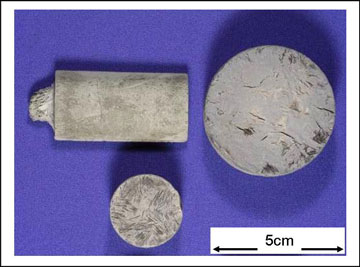 |
Figure 2. Photograph of porous silicon carbide with porosity of 90%.
|
The electron micrographs in Fig. 3 are of porous cordierite with a porosity of 87% fabricated by freezing at –50°C (left) and –20°C (right), followed by drying and sintering. The fine pores seen in these photos are presumed to be the vacant spaces left after the removal of the ice crystals. The pore size can be controlled by changing the freezing temperature. When frozen at a low temperature, it is possible to create the very fine pores seen in the left photo. These porous ceramics were found to have a maximum compressive strength of 4 MPa.
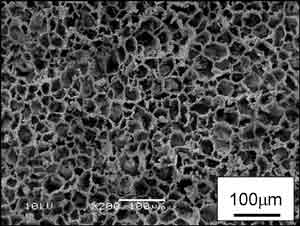 |
|
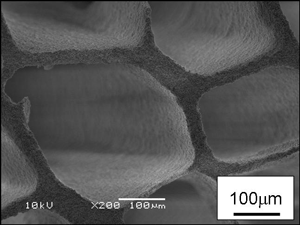 |
frozen at -50°C, dried and sintered |
|
frozen at -20°C, dried and sintered
|
Figure 3. SEM micrograph of porous cordierite.
|
This method, which uses water, is environment-friendly and can lead to dramatic reductions in the emission of carbon dioxide and other gases compared with methods that use resin-based pore formers or sponge.
As described above, we have successfully produced ultrahigh-porosity ceramics using a simple, environment-friendly gelation-freezing method. We believe our achievement is one step forward toward the realization of high-performance porous ceramics that can be used for a wide range of applications.
Future Schedule
We will attempt to further improve the properties of the materials by enhancing the interconnection between the fine pores, reducing the sizes of the pores, and so on. This technology is applicable to all powder materials - oxides and non-oxides - and will easily allow the mass production of cheap ceramics that have high porosity and sufficient strength for machining, without requiring large, specialized equipment. In the future, we wish to expand the range of applications by using these porous ceramics in not only filters and catalyst supports but also in parts requiring various pore diameters and porosities, such as absorbents and absorbing materials, fuel cell components, shock absorbers, heat insulation materials, and biomaterials, as well as for reducing the weight of existing components. We can provide samples of the porous ceramics, and we definitely hope to develop new products in collaboration with the industry.