Koichi Hamamoto (Post-Doctoral Research Scientist) of the Functional Assembly Technology Group (Leader: Masanobu Awano), the Advanced Manufacturing Research Institute (Director: Hideto Mitome) of the National Institute of Advanced Industrial Science and Technology (President: Hiroyuki Yoshikawa) (hereinafter referred to as AIST) has developed a high-sensitive NOX sensor with a rapid response.
Conventional NOX sensors do not have sufficient robustness or heat resistance in the harsh environment of engine exhaust gases. To solve this problem, a multi-chamber sensor that uses a solid oxide electrolyte (oxygen-ion conductor) has been developed. This, however, inherently does not give a high-speed response, because it has a rather complicated structure and it measures NOX concentrations by combining multistep electrochemical reactions. This poses a problem in relation to the purification of exhaust gases and reduction of fuel consumption.
The newly developed sensor has extremely high selectivity toward NOX molecules as a result of precise control of the nanostructure of the sensing electrode that detects NOX. This structural improvement to the electrochemical cell gives the speed of response for the direct detection of NOX molecules that is five times as fast as that of a conventional sensor and the detection sensitivity that is doubled.
The control of engine combustion with the aid of the high-performance sensor is expected to reduce NOX emissions, particularly from diesel vehicles, thereby contributing to preserving the atmospheric environment and reducing carbon dioxide emissions.
The results of this research are scheduled to be presented at the 16th International Conference on Solid State Ionics, to be held in Shanghai, China, on 2nd–6th of July.
|
Fig. 1: The sensor array with the multilayer sensing electrode.
|
Strenuous efforts are being made to develop lean-burn technologies for gasoline-fueled vehicles to comply with societal demands for reducing CO2 emissions and better fuel consumption. However, although lean-burn engines produce less CO2 emissions, they produce more NOX emissions than conventional engines. Existing three-way catalysts cannot be used to eliminate NOX emissions under lean combustion because of the high concentration of oxygen in the exhaust gases. Instead of the three-way catalyst, a practical lean-burn engine uses a NOX storage–reduction catalyst system.A NOX trap material in this catalyst absorbs NOX during lean-burn condition. When the catalyst becomes saturated with NOX, a rich spike (excessive fuel supply) is generated in the engine, and this excessive amounts of fuel reduces and purifies the absorbed NOX.
In the current system, the timing of when to add the rich fuel spike is based on the estimated amount of absorbed NOX obtained by means of model studies on the production of emission gases under normal operating conditions. Because the system does not rely on direct detection of the NOX concentration in the emissions, it is necessary to verify that it functions correctly under various operating conditions.
At the same time, there is a trade-off between emissions of NOX and those of unburned carbon (particulate matter: PM). Because emissions of PM increase if those of NOX are controlled. It is necessary to control NOX emissions at the regulated limit by using a NOX sensor, thereby minimizing emissions of PM. Therefore, the development of a small, high-performance, onboard NOX sensor capable of rapid and precise detection is highly desired. Such a sensor should permit monitoring of NOX emissions that are constantly changing, and would improve fuel economy by minimizing the number of rich fuel spikes required, thereby realizing highly efficient control of NOX emissions and reduction of fuel consumption.
AIST successfully developed a high-performance electrochemical reactor with a solid oxide electrolyte and achieved drastic improvements of selective NOX reduction even under a high oxygen partial pressure, where decomposition of NOX had previously assumed to be impossible (AIST Today, June 2006 issue). In this electrochemical reactor, a self-assembled nanostructure was formed in a catalytic electrode to create a reaction site of highly selective adsorption and decomposition of NOX molecules.
With the aim of utilizing the high selectivity of the electrochemical NOX purification reactor in a sensor, we examined the optimal structure and production methods for the electrode; as a result, we developed a high-performance sensor for NOX.
The results were obtained by controlling the nanostructure of the sensing electrode and by using a scandium-stabilized zirconia (ScSZ) ceramic with a high oxygen ionic conductivity as the electrolyte. The resulting electrode and electrolyte were shown to be applicable in a mixed-potential sensor that shows a high detection capability and a rapid response for nitric oxide (NO) molecules, even at 300 °C.
The sensor that we actually built was a single chamber electrochemical cell measuring about 1 cm x 2.5 mm x 300 nm. We formed the zirconia ceramic on the silica (SiO2) substrate by the pulsed laser deposition method (Figure 2).
Figure 1 shows a sensor array containing four sensors. This sensor shows a change in electromotive force of about 100 mV for 1000 ppm of NO gas diluted by nitrogen gas containing 5% oxygen at 350 °C: this is the highest level of detection yet achieved for NO gas, a substance that is normally difficult to detect (Figure 3).
As shown in Figure 4, optimizing the nanostructure of the sensing electrode realized a response speed that is less than 5 seconds for a 90% response. (Judging from the measurement conditions, the actual detection speed is estimated to be faster than the measurement.) Detection by a device without optimized structure requires more than 1 minute at the temperature above 600 °C. The mixed-potential sensor has slow response at the low-temperature range, where the rate of adsorption and desorption of the gas is slow, because the response speed of the sensor depends on the gas adsorption (desorption) capability. This is why the mixed-potential sensor is rarely used for temperatures as low as 300 °C.
The dramatic enhancement in performance is the result of the following two improvements.
1) The perforation associated with formation of nano-nickel particles by the reduction of catalytic electrode is effective in providing a reaction space for a highly selective NOX decomposition in the reactor, but it causes slow response of the sensor. We suppressed forming of the porous structure in the sensing layer by thinning the thickness (less than 100 nm).
2) We packaged most part of the reference electrode into the electrolyte to prevent the adsorption and desorption of gas on the open surface of reference electrode, which causes slower sensor response.
Multiple-chamber limiting current sensors, which are under active development, allow for a relatively high precision of detection, but the very low current value makes the system complicated and expensive. Furthermore, it does not allow for easy detection of NOX levels of less than 100 ppm, as required for monitoring the performance of a catalyst. Our newly developed NOX sensor technology, on the other hand, is capable of detecting small amounts of NOX in a simple structure.
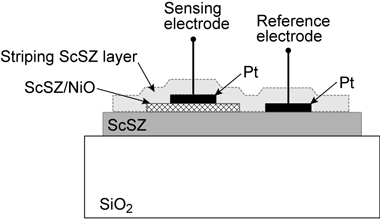 |
Fig. 2: Schematic illustration of the prepared electrochemical cell for NOX detection.
|
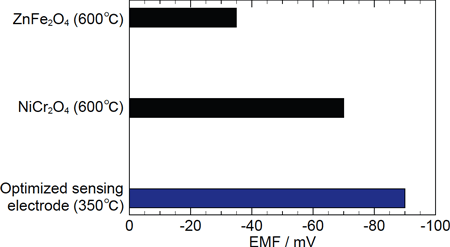 |
FIg. 3: Comparison of three different sensor responses for 1000 ppm NO.
|
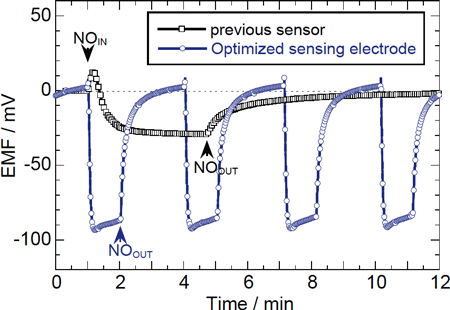 |
Fig. 4: Transient response of the cell for 1000ppm NO in N2 (5%O2) at 350 °C. (total gas flow rate; 300 ml/min)
|
We will continue our efforts to develop the cell structure to allow for an even higher sensitivity and faster response in NOX detection. We will also conduct further research by evaluating the effects of coexistent gases and the robustness of our cell, and we will make any improvements that are necessary for product realization of the sensor.