Update(MM/DD/YYYY):06/13/2007
Development of Large-Scale Production Technology of Anti-Reflective Lens using Nanoparticles
- Lowering the production cost of high-performance lenses by dies with nanostructure -
Points
-
Manufactured dies with nanostructure for lenses with anti-reflective properties by using metallic nanoparticles.
-
Embossed nanostructures even on complex shaped, large area die surface.
-
It would be possible to offer anti-reflective lens or liquid crystal panel, meter panel of automobile etc, at a lower cost.
Summary
Kazuma Kurihara (Research Scientist) and Takashi Nakano (Team Leader) of Super-RENS Technology Team, the Center for Applied Near-Field Optics Research (Director:Junji Tominaga) of the National Institute of Advanced Industrial Science and Technology (President: Hiroyuki Yoshikawa) (referred to as AIST, hereinafter) successfully developed a mass production technology of nanostructure embossed anti-reflective lens by using metallic nanoparticles in collaboration with Ito Optical Industrial Co., Ltd. (President: Hiroshi Ito) (referred to as IOI, hereinafter) and Tokai Seimitsu Kogyo Co.,Ltd. (referred to as TSK, hereinafter).
This manufacturing technique of the anti-reflective lens, uses dies with nanostructure which is made by an etching method using the nanoparticles as a mask which is formed only by vacuum process. It is also possible to make nanostructure, which gives anti-reflective property, even in complex-shaped die surface. As the die which is made with this technology can be used in injection molding, mass-production of high-performance lenses became possible.
As the conventional multilayered membrane coating process, necessary for providing anti-reflective properties to the lens, can be avoided, further reduction of unit price per lens is expected by this process. By using this technology, higher performance of lenses with small radius of curvature etc, is expected, which was not realized by the conventional process. It will be applicable in the compact camera or camera phones which are in high demand recently.
We plan to exhibit the sample product in the booth of SIM Optical Co., Ltd. at the Lens Design and Manufacturing Expo 2007 to be held in Pacifico Yokohama, on 25-27 April, 2007.
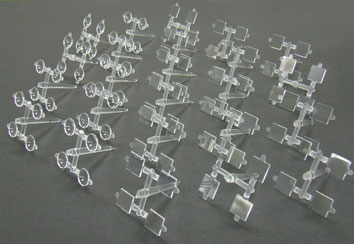 |
|
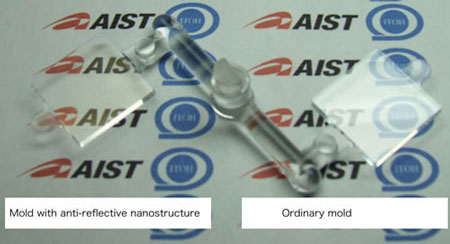 |
Injection-molded products
|
Social Background of Development
Recently, we observed flourishing development of a new device which uses the characteristic phenomena of fine structure of nanometer-scale. Applications, for example, to anti-reflective nanostructure which is nanometer-scale structure smaller than the wavelength of light put on the surface of an optic device, photonic crystal controlling the direction of light artificially by a nanostructure pattern, and 1/4 wavelength plate fabricated in the surface of other optical components etc.
As the anti reflective structure in that can reduce reflectance at a wide angle range / wide wavelength region compared with the conventional technology, application in higher efficiency of solar cells, higher brightness of displays, and higher performance of optic lens is expected. It is also anticipated that the technology is applied to optical devices such as the lenses with small radius of curvature or aspheric lenses etc., to which the conventional multilayered membrane technology cannot provide enough anti-reflective properties.
Manufacture of such a nanometer size microstructure requires a technology depicting a minute pattern which is generally known as lithography. Till now, short wavelength light such as vacuum ultra violet light (light lithography method, interference exposure) or an electron beam (electron beam lithography method) etc. are used in the technology. But as the price of these lithography devices are extremely high, it becomes a cause of high expenses in small lot/ various kinds of optic lens industry. In the manufacturing of anti-reflective structures, a technology that can produce it for a low price is demanded. Thus, application of the conventional lithography technology is particularly difficult. Therefore, the nanostructure anti-reflective lens die manufacture technology/ production technology is of high demanded as it is a low cost, simple procedure that does not use an expensive device.
History of Research
AIST is promoting research and development of the next generation high-density optical disk, following Blu-ray and HD DVD. AIST is also deploying the result of optical disk research and development into other industrial fields. The nanoparticle fabrication technology obtained from optical disk development in AIST has been merged with the die production technology/the molding technology of IOI and TSK. AIST and IOI have carried out joint research in order to develop large-scale production technology of anti-reflective lens with nanometer sized fine structures, at low cost, in a simple method without using an expensive device for its productions.
Details of Research
The production technology for anti-reflective lens which has been developed, is a process to manufacture nanostructure-embossed die that uses metallic nanoparticles (fig. 1) made only by vacuum process as mask for etching. That is why it is possible to manufacture nanostructures with anti reflective properties even on complex shaped die surface. In addition, as it is possible to make nanostructures on the stainless steel which are die materials for injection molding, large-scale production was realized. Figure 2 illustrates the manufacturing process of die with anti-reflective nanostructure. First, nanoparticles are formed on die surface under vacuum. After that, the nanoparticles are used as mask for etching method, we manufacture nanostructures on the surface of die for anti-reflective lens. By performing injection molding or cast molding using the die for anti-reflective nanostructured lens, it is possible to mass produce high-efficiency lens.
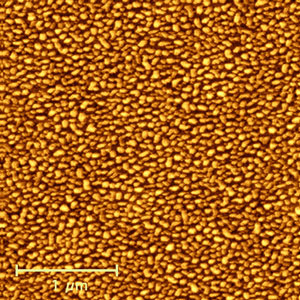
figure 1 metallic nanoparticles
|
|
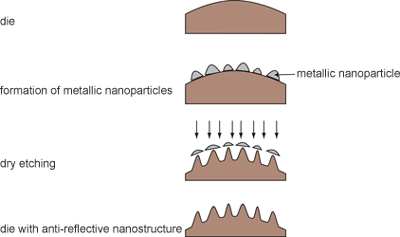
figure 2 manufacturing process of a die with anti-reflective nanostructure.
|
Figure 3 shows the manufactured dies with anti-reflective nanostructure. It is possible to make nanostructures on both convex and concave surfaces, and realization of die for anti-reflective lens is confirmed. In addition, injection molded objects manufactured with nanostructure-embossed dies are shown in figure 4. Figure 4 (a) is an injection molded object made with a plane surface die, (b) injection molded object made with lens die. If we compare anti-reflective nanostructured molds with ordinary molds, light of the fluorescent lamp is strongly reflected by the ordinary molds.(figure 4(a)) It is difficult to read the letters of the following (figure 4(a) right side), but compared to (figure 4(a) left side) which is an injection mold made with anti-reflective nanostructure , the light reflection is suppressed and the letters are clearly visible. Letters are also clearly visible through injection molded lens with anti-reflective nanostructure.(Figure 4(b)) A cast molded lens of a diameterΦ50mm is shown in figure 5. Possibility of getting anti-reflective properties same as injection molds is confirmed. It is recognized that the technology is easily applied to large area operations. Figure 6 shows optical properties of the molds. Reflectance was reduced, and transmittance was improved at the same time. As shown above, it was concluded that this technology can manufacture nanostructures using metallic nanoparticles, make anti-reflective nanostructures directly on the die using only vacuum process, which could be used in injection molding. Also, the molds displayed the required optical characteristics. Therefore, it is not only possible to eliminate the manufacturing of the multilayered membrane necessary in the conventional process, as it is possible to realize same kind of lens by injection molding, so further price reduction and high performance is expected.
In this way, low-cost large-scale manufacturing of anti-reflective lens, liquid crystal panel and meter panel of automobile etc. will be realized. It will be possible to add anti-reflective property to Display panels, lenses for digital camera, which our country is famous for, andalso to automobile parts at low cost. And thus, we can make valuable contribution in the internationally competitive field of product development.
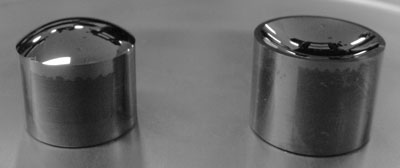 |
figure 3 dies with anti-reflective nanostructure. left:convex right:concave
|
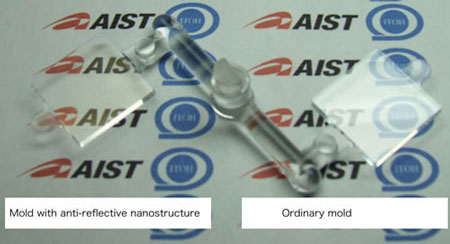
(a)
|
|
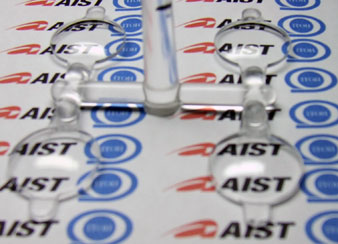
(b)
|
figure 4 Injection molded objects
(a) injection molded with flat die (b) injection molded with lens die
|
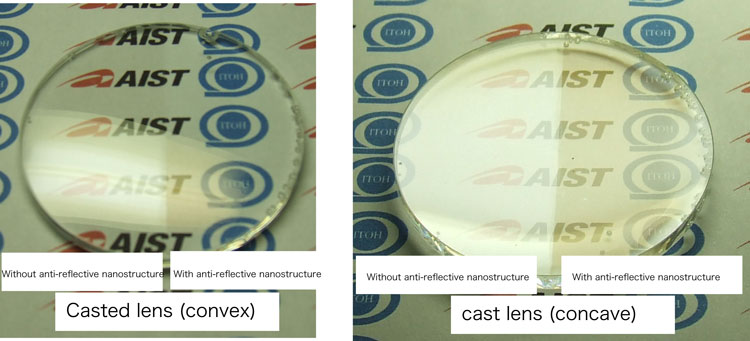 |
figure 5 casted lenses of 50mm diameter
|
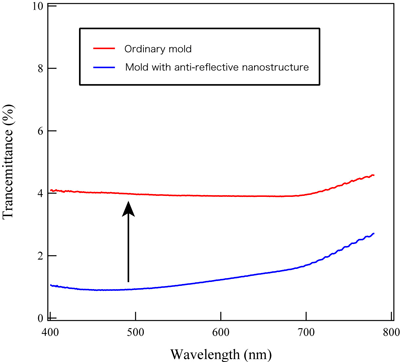 |
|
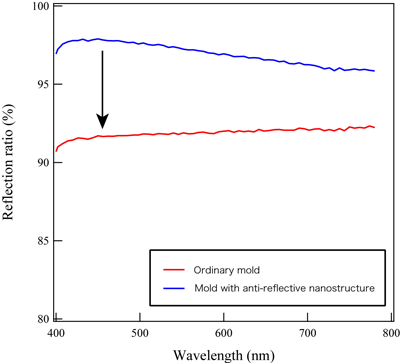 |
figure 6 optical properties of casted lenses
|
Future Schedule
We are planning to conduct sample shipment of plastic molds manufactured from the die developed in this research from around summer, 2007. Also, research and development is going on in the field of mold press die for glass. In addition, we aim to contribute in the revival of high-performance, low-cost manufacturing technology.