- A Practical Thermoelectric Power Generation Module for Higher Temperatures Developed Using Ceramic Materials -
The Research Institute for Ubiquitous Energy Devices (RIUED) of the National Institute of Advanced Industrial Science and Technology (AIST), an independent administrative institution, has successfully developed a thermoelectric conversion module made of ceramic materials without performance degradation resulting from oxidation. While there have been thermoelectric modules (TEM) operable at higher temperatures, that newly developed is characterized by the absence of performance degradation even after operation at 800 °C in the air, and use of neither toxic substance nor precious rare elements. The new TEM is found much better than the existing ones in respect to economy and safety.
When the new TEM is used in waste incinerators, industrial furnaces and automobiles, electrical power may be recovered from untapped waste energy, which constitutes around 70 % of total consumed energy, In this way, the new TEM may be regarded as a promising means for alleviating energy saving and global warming issues. Furthermore, as the TEM has high power density, it can be applied as power source for emergency use or for mobile devices at disaster sites where only heat sources are available.
|
Figure: High temperature waste heat can be effectively utilized by use of the ceramics thermoelectric conversion module.
|
It is expected that the oil output will show a peak around 2010 to 2020, and Japan is requested to find best solutions for the stable supply of energy and the global- environmental issues, while keeping the economic growth. The annual consumption of primary energy in Japan is hundreds thousands kiloliters crude oil equivalent. About 70 % of consumed energy is dissipated untapped into the atmosphere. As an enormous amount of energy is wasted, much interest is focused on technologies to recover and effectively utilize the waste energy. However, in spite of enormous amount of total waste energy, heat released from individual source, such as an automobile is very little. For this reason, it has been very difficult to implement technologies collecting diluted waste energy efficiently and at low cost. Under such a circumstance, the most promising technology for reclaiming waste heat is the thermoelectric power generation (Fig. 1), owing to the following merits:
1. No moving part.........maintenance-free, long service life.
2. Direct conversion.......clean and silent operation, simple construction, best suited for emergency power supply at disaster site.
3. High power density...small size, lightweight, best suited for powering mobile systems and portable devices.
4. No scale merit........heat energy, however little in amount, is converted into electricity.
Among these merits, the absence of scale merit. is advantageous for collecting sparsely distributed waste heat. However, there have been very few examples of waste heat retrieval through the thermoelectric conversion in the daily life despite its high expectancy, because appropriate thermoelectric materials have not been available. Previous thermoelectric materials have been made from metal and not suited for areas in consumer application, because of performance degradation due to melting or oxidation at higher temperatures, and inclusion of lead or other toxic elements.
Fig. 1. Mechanism of thermoelectric power generation
|
|
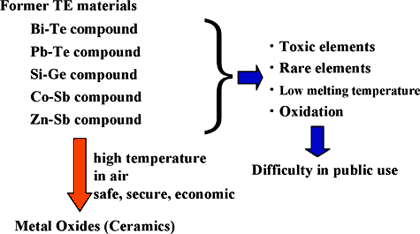
Fig. 2. Problems of thermoelectric materials
|
The newly developed thermoelectric module is made from oxide thermoelectric materials, or ceramic materials, which are not degraded at higher temperatures and do not contain toxic element. Since 1998, a research group of the AIST has started studies on the ceramic thermoelectric system, achieving some outstanding results such as the discovery of p-type layered cobalt-based thermoelectric oxide with 10 % conversion efficiency at 500 °C operational temperature difference, and the establishment of technologies for synthesizing and characterizing 2,000 species or more thermoelectric materials per day (Figs. 3 and 4). The group has been engaged in the fabrication of thermoelectric power generation module based on the newly found materials.
Fig. 3. Layered cobalt-based thermoelectric oxide, with around 10 % conversion efficiency in single crystal.
|
|
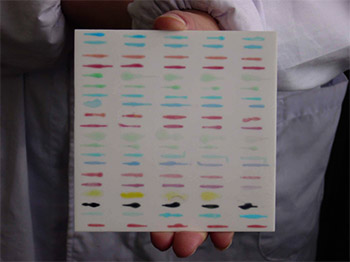
Fig. 4. Combinatorial library preparation makes it possible to synthesize and characterize 2000 or more samples per day.
|
The thermoelectric module is made of p- and n-type oxides connected alternately in series, as illustrated in Fig. 1. Connecting a lot of materials is inevitable as a unicouple generates a voltage 100 mV or so at the highest, however great the temperature difference may be. The most difficult problem in the module fabrication is how to connect the materials with electrical resistance as small as possible. For instance, in order to fabricate a 4-V module needed for recharging a mobile phone it is necessary to connect 40 or more pairs in series, requiring to create 80 junctions. A disconnection or enhanced electrical resistance at any of these junctions may reduce electrical energy deliverable from the module. As the thermoelectric module generates electric power on the basis of temperature differences, failure may be caused by the difference in coefficient of thermal expansion between thermoelectric materials and metal electrodes linking them. The TEM developed by the RIUED-AIST is designed to operate at temperatures as high as 800 °C in air, and conventional technique such as soldering cannot be used for its fabrication. It has been requested, therefore, to develop innovative techniques for joining electrodes, junctions and other components.
The construction of TEM ultimately developed by the RIUED-AIST after a series of trials-and-errors is shown in Fig. 5. Recharging a mobile phone with the TEM by use of temperature difference between flame of a small gas stove and a pan filled with water is illustrated in Fig. 6. In this way, it has been demonstrated that the conversion efficiency of the TEM is stable and unaffected by repeated operations at temperatures as high as 800 °C in air, supplying electric power whenever and wherever a heat source is available.
The oxide TEM fabricated in this study consists of 7 to 280 pairs of p-n junction, and a palm-size unit can generate around 10 W power with hot and cold sides kept at 800 °C and 300 °C, respectively. The TECM developed by the RIUED-AIST is made from materials free from toxic and rare elements, and characterized by low cost, junction resistant to heating-cooling cycles, massive power generation with small size and lightweight device. In this way, the TEM has been proved to have excellent performance as a thermoelectric module for recovering waste heat.
Fig. 5. TEM composed of 140 pairs of thermoelectric junctions.
|
|
Fig. 6. TEM recharging a mobile phone while heating water to boil.
|