- Construction of Ultra-High Capacity Hydrogen Storage System for Fuel Cell Accelerated -
The Energy Technology Research Institute (ETRI), the National Institute of Advanced Industrial Science and Technology (AIST), an independent administrative institution, has developed a new melting process with high accuracy control ensuring designed composition for hydrogen storage alloys containing low-boiling metals such as magnesium, calcium and lithium to be used as a medium for storing hydrogen in fuel cell-driven vehicles in collaboration with Japan Metals and Chemicals, Co., Ltd. (JMC, hereinafter).
Up to now, it was very difficult to fuse alloys consisting of low-boiling and -melting metals such as magnesium, calcium and lithium, and high-melting metal such as nickel, because of massive evaporation of low-boiling metal in the smelting furnace to hamper realizing alloys of designed composition, and security problem causing dust explosion with floating metal dust.
The ETRI-AIST and JMC focused attention on inert gas used as atmosphere within the furnace. With bottleneck problems resolved by replacing argon with mixed helium gas, the technology for melting alloys and compounds including low-boiling and -melting metals precisely in the designed composition has been developed successfully.
The outcome of this study will accelerate the development of hydrogen storage alloys, and provide a great stride toward the implementation of a hydrogen loading system for fuel cell-driven vehicles.
The details of this research work will be reported at the 136th Spring Meeting of the Japan Institute of Metals to be held at the Yokohama National University from March 29th to 31st, 2005.
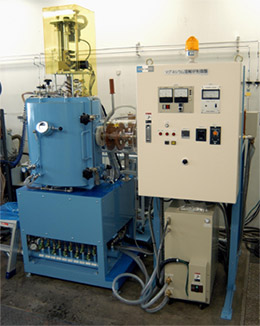
Photo 1 Outer view of a smelting furnace for low-boiling alloys
|
|
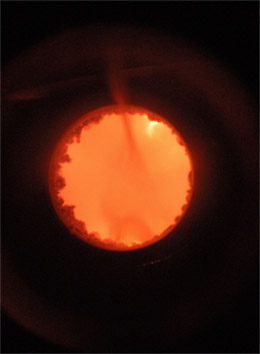
Photo 2 Melted metal in the smelting process
|
For bringing a hydrogen energy-based society to reality, it is essential to develop technology for safe and massive storage of hydrogen. One of promising technologies is the development of large capacity hydrogen storage alloys with light metals such as magnesium, calcium and lithium as major ingredients.
Light metals to be used for the hydrogen storage alloys are characterized by low melting and boiling points, and high vapor pressure of melted metal. When casting alloys consisting of light metals and high melting metals such as nickel, it has been very difficult to prepare alloys of designed composition because of massive evaporation of low-boiling metals within the furnace. Fume made of fine metal powder resulting from the evaporation blocks out the field of view to prevent visual check for melting state or stirring effect. Moreover, accumulated metal powder causes problems in workability and safety, such as need for clean-up works and induction of dust explosion. For this reason, technology for suppressing the emission of fine metal powder caused by evaporation during melting has been required.
The research work has been carried out under the project "Development for Safe Utilization and Infrastructure of Hydrogen: Development of High Capacity Metal Hydrides and Hydrogen Storage Tanks" (fiscal years 2003-04), entrusted form the New Energy and Industrial Technology Development Organization (NEDO), another independent administrative organization.
In order to solve these problems, the ETRI-AIST and JMC focused their attention to inert gas used for atmosphere within the furnace, and checked with a number of inert gases. Consequently, an innovative melting process has been developed, to suppress the emission of fine metal powder during smelting by replacing argon with helium mixed gas, and to ensure designed composition of alloys and compounds.
On applying the newly developed melting process to Laves phase hydrogen storage alloys based on calcium and magnesium under development, casting of alloys with exactly designed composition has been achieved with high yield (Photo 3).
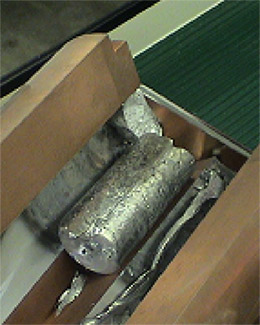 |
Photo 3 5% large capacity calcium-based Laves phase hydrogen storage alloy
prepared by the newly developed melting process |
The achievement will accelerate the development of hydrogen storage alloys as a medium for loading the furl cell-driven vehicles with hydrogen safely and in large capacity.
The new melting method will be very useful also for stable mass production of ultra-high performance alloys for Ni-MH Nickel Metal Hydride Rechargeable battery used in digital camera and other appliances.
Furthermore, the process will contribute to the development and commercialization not only of hydrogen storage alloys, but also of structural and functional materials containing elements of low melting point, low boiling point and high vapor pressure.