The Energy Technology Research Institute (ETRI) of the National Institute of Advanced Industrial Science and Technology (AIST), one of independent administrative institutions, has successfully developed high performance fuel electrode catalyst which plays key roles in cost reduction and durability enhancement of reformed gas-based fuel cells. Among various types of polymer electrolyte fuel cells, reformed gas-based one has been expected to be a promising candidate of that for domestic applications.
In the domestic fuel cell, fuel gas such as city gas is reformed into hydrogen, which is fed into the cell to generate electric power. When the concentration of byproduct impurity in reformed gas, carbon monoxide (CO) exceeds a few parts per million (ppm), (1 ppm = 1/1,000,000), the fuel electrode catalyst, Pt, is adversely affected to degrade the cell performance drastically.
While it has been known that Pt-Ru alloy catalyst is resistant to CO, it is expensive and fails to protect the electrode when the concentration of CO becomes higher than 25 ppm.
The newly developed catalyst is characterized by use of low cost materials, organic metal complex as an auxiliary catalyst for platinum, and by much better performance than that of the conventional catalyst. The catalyst is prepared by mixing platinum precursor with organic metal complex, incorporating the mixture over carbon particles and baking in inert gas. This provides adequately stable catalyst.
In Fig. 1, output current of fuel cell at the normal operational potential is plotted against the concentration of carbon monoxide in hydrogen, with that for pure hydrogen set to 100. The catalyst is tolerant to CO at the concentration higher than 100 ppm. Such a high resistance to CO is world first achievement, and the practical application of this catalyst will mitigate strict requirements of fuel reformer for reducing CO and bring forth a spin-off effect of saving cost of the reformer itself.
The future R&D efforts will be directed to understanding the mechanism of catalyst action of organic metal complex, and to further improvement in view of commercializing domestic fuel cell as a promising clean energy source.
The present research has been carried out under a contract project entitled “Development of Polymer Electrolyte Fuel Cell System” (FY2000~04) with the New Energy and Industrial Technology Development Organization (NEDO), another independent administrative institution. The results will be reported at the Meeting of International Society of Electrochemistry to be held September 14~24 in Greece.
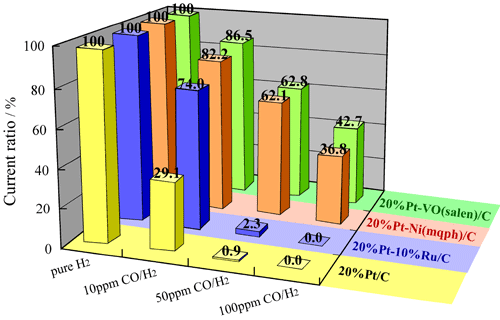 |
Fig. 1. Performance of the newly developed catalyst Pt-VO(salen)/C and Pt-Ni(mqph)/C as compared with that if the conventional catalyst Pt-Ru/C and Pt/C. Retention of output current for CO-containing hydrogen from the level of pure hydrogen.
|
The fuel cell is a new breed of power plant characterized by silent operation, and much less emission of greenhouse gas, carbon dioxide (CO2), and other atmospheric pollutants such as nitrogen oxides (NOx) and sulfur oxides (SOx), in comparison to the internal combustion engine. It has been urgently requested to develop and commercialize the fuel cell as early as possible as one of “clean” energy sources.
In the fuel cell, chemical energy release by the reaction of hydrogen combining with oxygen to form water is efficiently converted to electrical power by feeding hydrogen to the fuel electrode, and air (oxygen) to the air electrode.
Usually, in case of domestic fuel cell, hydrogen is made from household fuel such as city gas and fed into the cell to generate electric power. This type of fuel cell is called reformed gas type.
However, this type of fuel cell has a demerit: when reforming city gas to hydrogen a small amount of carbon monoxide (CO) is formed as a byproduct and exercise adverse effect to Pt catalyst for fuel electrode (catalyst poisoning). The poisoning causes serious degradation of fuel cell. To overcome this demerit, CO-tolerant catalyst materials are sought for. So far, expensive Pt-Ru alloy catalyst has been regarded as a sole remedy. Ruthenium is a hard-to-find resource, much scarcer than platinum, and its use is restricted in terms of resource availability and cost. Even with Pt-Ru alloy, the practical upper limit of CO concentration to avoid poisoning is in the order of 25 ppm, and hydrogen derived from a reforming equipment at the time of starting a fuel cell contains more than 100 ppm CO.
For this reason, catalysts superior to Pt-Ru alloy have been sought for worldwide in these two decades unsuccessfully.
The AIST has been engaged in R&D of polymer electrolyte fuel cell for a decade, and potential of studies on materials science and system construction has been accumulated. In particular, the development of high performance catalyst to replace existing one by using organic metal complex which allows molecular design and synthesis readily has been pursued in succession, leading research organizations in this area, both domestic and overseas. The newly developed catalyst is prepared by mixing platinum compound with organic metal complex, an auxiliary catalyst, incorporating carbon particles with the mixture and baking in an electric furnace under inert gas. This is one of AIST’s original technologies.
The newly developed catalyst consists of organic complexes called “salen” or “mqph” which have simple molecular configurations. Organic metal complex is synthesized by combining these compounds with various metal salts, such as nickel, iron or vanadium.
The catalyst is prepared through the following steps: (1) mixing platinum precursor with organic metal complex in a solution, (2) incorporating the mixture on to carbon powder support, and (3) drying and baking in inert gas. The mixed catalyst is proved to be effective after the heat-treatment.
In a half cell test at 70 °C with membrane-electrode assembly to constitute a fuel cell, it has been demonstrated that the new catalysts are tolerable to CO poisoning up to 100 ppm, far better than the performance of conventional Pt-Ru alloy catalyst (patent pending).
Using organic metal complex for catalyst has a number of merits such as reduced cost of raw materials, and higher degree of freedom for molecular design to expand the scope of catalyst search extensively, opening the way to develop high performance catalysts in the future.