Update(MM/DD/YYYY):04/02/2009
Bench Plant for Manufacturing Bio-ethanol without Sulfuric Acid
- Environment-friendly ethanol manufactured from various biomass resources not competing with food -
Points
-
A bench plant for manufacturing bio-ethanol without sulfuric acid and with a small environmental load that does not affect food supply was developed and constructed (processing 200 kg of wood at once).
-
All manufacturing processes to produce bio-ethanol from raw materials were substantiated through trial production.
-
This method will be verified by actual operation, and a scenario will be drawn for creating a new energy industry contributing to a sustainable society.
Summary
The Biomass Technology Research Center (Director: Kinya Sakanishi) of the National Institute of Advanced Industrial Science and Technology (AIST) (President: Hiroyuki Yoshikawa) has constructed a bench plant at AIST Chugoku (Kure, Hiroshima) for the manufacture of ethanol fuel and has started the verification of manufacturing processes under the “Development and verification of medium- and small-scale plants for manufacturing a woody biomass ethanol fuel”, which is one of collaborative industry-academia-government projects, the “AIST Industrial Transformation Research Initiative” (the Industrial Transformation Initiative).
We developed and set up a bench plant (processing 200 kg wood at once) for manufacturing ethanol fuel without sulfuric acid and with a small environmental load that is based on a pretreatment technology for biomass raw materials developed by AIST. We confirmed the ability to manufacture ethanol fuel from raw materials. We plan to operate on a full scale, and verify the technologies for manufacturing ethanol fuel from various types of cellulosic biomass (conifers, broadleaf wood, and straw; referred to as woody biomass) that will not compete with food crops.
We intend to evaluate the economic efficiency and conduct a life-cycle assessment based on the verification data obtained in this plant, and draw up a scenario for commercializing the plant for a sustainable society by improving the overall process and optimizing the design and development for larger-scale plants.
This project covers a period of about three and a half years from December 2007 to March 2011.
Moreover, the results of research supported by the New Energy and Industrial Technology Development Organization have been used for part of this bench plant.
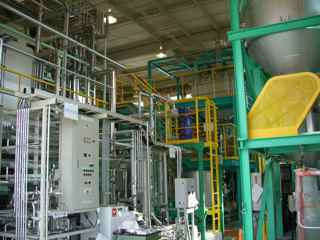 |
Fig. 1 Manufacturing plant for bio-ethanol without sulfuric acid
|
Social Background for Research
Expectations for a bio-fuel, which is renewable energy that can replace part of the demand for crude oil, have increased worldwide under the rising demand for oil due to recent economic growth in Asia, the unstable supply of crude oil, and the deteriorating global warming, etc.
The target value for introducing a bio-fuel is stated in Japan’s “Kyoto Protocol Target Achievement Plan,” and is one of the measures for controlling global warming. The necessity of the strategy for introducing a bio-fuel from a long-term viewpoint is pointed out in Japan’s “Biomass Nippon Strategy” and “The New National Energy Strategy.” Moreover, securing biological resources will become an important issue for future energy policies as each country in Asia develops and introduces bio-fuels.
The effectiveness of reducing CO2 by substituting bio-ethanol, which is one type of bio-fuel, for gasoline has been clearly shown by life-cycle assessment (LCA). However, the manufacturing of ethanol from sugarcane, corn, etc. is rapidly increasing, and the price of food and fodder is rising in Brazil and the United States, causing social problems. The manufacture of bio-ethanol from a cellulosic resource such as wood and straw that does not compete with food crops is attracting attention as a viable solution.
History of Research
Substantiation of the concentrated sulfuric acid method, the dilute sulfuric acid two-step saccharification method, and the dilute sulfuric acid and enzymatic saccharification method have already advanced as technologies for converting cellulosic resources into ethanol fuel. However, reducing the cost of waste management and decreasing the environmental load are indispensable as these methods use sulfuric acid, and there is a limit to reducing the cost and to improving the efficiency of energy conversion. Therefore, it is important to develop and verify a plant technology for manufacturing ethanol using cellulosic biomass without sulfuric acid.
In response, AIST, under the Industrial Transformation Initiative, has developed a technology for manufacturing ethanol fuel using cellulosic biomass without sulfuric acid on a small to medium scale.
Features of the Plant
To validate the original technique developed by the Biomass Technology Research Center of AIST, we constructed a bench plant for manufacturing ethanol fuel without sulfuric acid, on a small to medium scale (processing of 200 kg of wood at once).
In this bench plant, we attempted to confirm the manufacturing of ethanol fuel using low-cost, highly effective, and low environmental load processes based on original techniques without the problematic sulfuric acid in the ethanol yield and the on site enzyme production, etc. by optimizing an energy efficient type pretreatment technology without sulfuric acid and elemental technologies for saccharification and fermentation.
We combined hydrothermal process with wet-type mechanochemical process as an energy-efficient pretreatment technology. In this pretreatment, contact with the cellulose saccharification enzyme (cellulase) is improved by changing the structure of biomass constituents such as cellulose at the nanometer level, and the enzymatic saccharification rate improved significantly.
To improve the cost performance of the enzymatic saccharification process, which greatly influences the economic efficiency of the entire process, the saccharification enzymes were produced using filamentous fungus in the plant. The filamentous fungus used is high cellulase-producing funguses such as Acremonium cellulolyticus that has been isolated and bred by AIST.
Thus, we combined the best technologies of Japan with our original technologies, and executed all processes from the acceptance of raw material chips to the manufacturing of dehydrated ethanol on a scale of 200 kg of biomass raw material per batch in this bench plant.
Composition of the Plant
This plant consists of five categorized processes: coarse pulverizing processes, a hydrothermal process, fine pulverizing processes, saccharification and fermentation processes, and distillation and dehydration processes.
- Coarse pulverizing processes
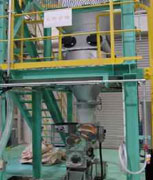
Coarse grinder
|
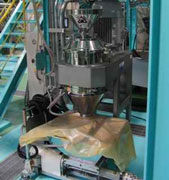
Wet-type cutting mill
|

Materials processed with a wet-type cutting mill
|
Wood chips and straw, which are the raw materials, are crushed to about 3 mm with coarse grinders. Then they are pulverized to 0.8 mm or less using a wet-type cutting mill.
- Hydrothermal process
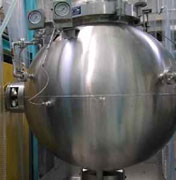
Hydrothermal processing device
|
After the wet-type cutting mill process, the raw materials are subjected to heat and pressure in a hydrothermal processing device, which softens the wood. In this plant, reaction occurs at conditions from 150 to 180°C and about 0.5 MPa.
- Fine pulverizing processes
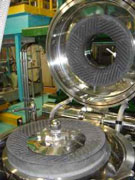
Wet-type disk mill
|
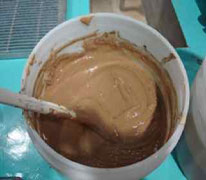
Materials processed with a wet-type disk mill
|
After the hydrothermal process, the raw materials are more finely pulverized with a wet-type disk mill. Raw material fibers become untangled in this process, and are easy to hydrolyze with enzymes. The raw material is similar to paste after this process, and contains only about 5% dry solids. The concentration is too low for the saccharification and fermentation processes. Then, they are dewatered to about 20% dry solids using a centrifugal dryer. The processed material after the dehydration becomes like clay.
- Saccharification and fermentation processes

Main saccharification and fermentation tank
|
A cultivating tank for a filamentous fungus that produces cellulase to hydrolyze cellulose and a cultivating tank for yeast that ferments ethanol are set up as an annex to the main 2000-L saccharification and fermentation tank.
Raw materials finely pulverized and dewatered are mixed with a filamentous fungus culture solution in the main saccharification and fermentation tank, and are hydrolyzed by cellulase and hemicellulase those are produced by the fungus. Then a yeast culture solution is added to the hydrolyzed solution, and ethanol is produced.
- Distillation and dehydration processes
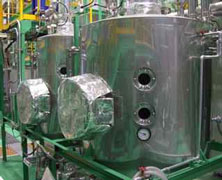
First distilling device
|
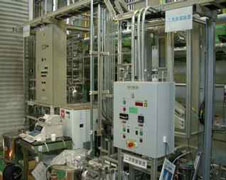
Second distilling device and membrane dehydration device
|
The fermented solution is moved straight to the first distilling device, and distilled. Bio-ethanol of 99.5% or more concentration is manufactured through a second distilling device and a membrane dehydration device.
We studied the use of lignin contained in the distillation residue as a raw material of chemical products and an alternative to carbon black (AIST press release, February 9, 2009).
Evaluation of Economic Efficiency
In designing this plant, the economic efficiency was evaluated especially for selecting a pretreatment technology. Figure 2 shows the required energy for the concentrated sulfuric acid method, the dilute sulfuric acid and saccharification method, which are preceding technologies, and the fine pulverizing (with ball mills or wet-type disk mills) and saccharification method, which is a non-sulfuric acid method.
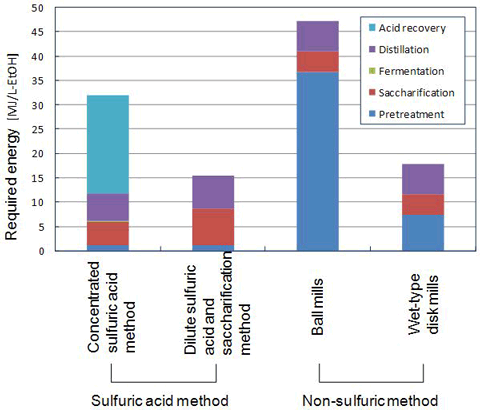 |
Fig. 2 Required energy for each pretreatment technology
(Energy utilization for heat recovery and energy residue is not included.)
|
In Figure 2, the energy required for acid recovery accounts for two-thirds of the total energy in the concentrated sulfuric acid method, one of the two kinds of sulfuric acid methods that are preceding technologies. Acid recovery is not summed up in the dilute sulfuric acid and saccharification method, and the required energy is about half that of the concentrated sulfuric acid method, because dilute sulfuric acid after processing is neutralized to gypsum with lime, and is discarded.
On the other hand, the energy required for pretreatment is overwhelmingly high in two of the non-sulfuric acid methods compared with the sulfuric acid methods. In particular, the energy required for pretreatment is about 80% with ball mills. We adopted the wet-type disk mills for this plant because the required energy could be greatly decreased by using wet-type disk mills instead of ball mills.
The pretreatment technology using wet-type disk mills requires almost the same amount of energy as the dilute sulfuric acid and saccharification method, and does not exhaust the gypsum because sulfuric acid is not used. In addition, the economic efficiency of the system is improved by on-site production of the enzymes.
Schedule of the Project
We designed the scenario for bringing this plant to the market through close cooperation with private companies specifically involved in plant systems and operations. At the same time, we evaluated elemental technologies, etc. through cooperation with external organizations, with the goal of implementing plants for practical use after FY2011. We are aiming to contribute to the creation of a renewable energy industry using cellulosic biomass as raw materials with potential for overseas development.
 |
Fig. 3 Development of research in each fiscal year
|
Future Schedule
It is important to use various types of cellulosic biomasses as raw materials to ensure a stable and abundant supply because regions where cellulosic raw materials can be secured are limited, and because they tend to be produced in certain seasons such as rice straw in Japan.
We plan to develop the processes of the manufacturing plant such as by carrying part of the plant to the source of raw materials and manufacturing ethanol fuel there locally, and also to manage the kind and accumulation of biomass raw materials flexibly in this verification test.
In addition, we will establish a model for providing and utilizing raw materials in cooperation with the Forestry and Forest Products Research Institute, and try to reduce various costs from manufacturing ethanol to consuming it by evaluating the economic efficiency and performing life cycle assessment, will manufacture a high-quality, efficient ethanol fuel, and evaluate the fuel performance. Through these activities, we are aiming to create a renewable energy industry based on cellulosic biomasses.