産総研とダイセルが挑むカーボンニュートラル実現!
産総研とダイセルが挑むカーボンニュートラル実現!
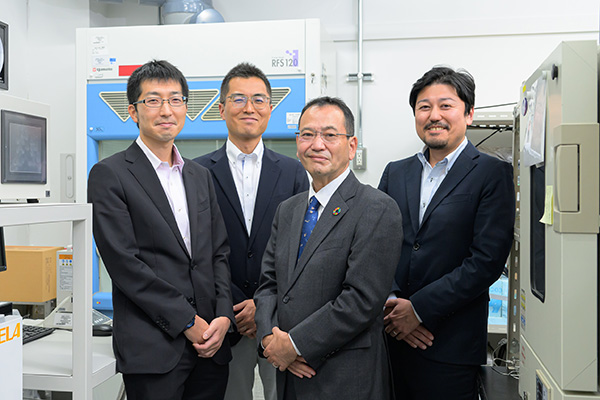
2024/01/31
産総研とダイセルが挑むカーボンニュートラル実現! 「イオン液体」と「中空糸膜技術」でCO2を分離回収
2050年にカーボンニュートラルを実現するためには、CO2排出を抑制する技術だけでなく、排出されたCO2を分離・回収して固定化するネガティブエミッション技術が必要だ。産総研と株式会社ダイセル(以下、ダイセル)は、大気中のCO2を直接回収する「直接空気回収技術、DAC(Direct Air Capture)」を実現するための手法として、大気中の希薄なCO2を選択的に分離・回収する膜を共同で開発した(2022/11/11プレスリリース記事)。これは、産総研が長年取り組んできた「イオン液体」の研究成果と、ダイセルが培ってきた「膜・フィルムの形成」に関する技術が一つの形になったもので、企業と研究所の共同研究が結実した成果といえる。産総研とダイセルの連携がどのように生まれ、どのような困難を乗り越えてきたのか、その経緯をたどった。
混合イオン液体を多孔質膜へ含浸させCO2を分離
2050年のカーボンニュートラルの実現に向け、大気中に排出されたCO2を分離回収して、地中に貯留するなどして固定化し、排出量をマイナスにするネガティブエミッション技術が注目されている。この技術の起点となるのが、大気中からCO2を分離回収するDAC(Direct Air Capture/直接空気回収技術)だ。近年は、化学吸収や化学吸着を用いた方法について、欧米を中心に実証研究や商用化が進められてきた(産総研マガジン「DACとは?」)。しかし現在、研究が進められているDAC技術は、CO2を回収するために多量の熱エネルギーを消費することが大きな課題となっている。
産総研とダイセルは、両者のこれまでの研究開発成果を持ち寄って議論を積み重ね、分離回収に投入するエネルギーがより少ない方法を求めて、「『イオン液体』を使った膜分離法でのCO2分離回収の実用化」を研究ターゲットとすることを決定した。
イオン液体は、室温付近に融点を持つ液体の塩(えん)のことで、その発見は20世紀初頭にさかのぼる。当初、イオン液体は熱的・化学的に安定したものではなかったが、1980年代以降、多くの改良を加えることで安定性が高まった。近年では帯電防止剤やリチウムイオン電池の電解液をはじめ、さまざまな反応溶媒、潤滑剤などとして使うための応用研究が進み、すでに商用化されたものもある。
2000年代に入って注目されてきたイオン液体の用途の一つが、CO2の分離回収である。イオン液体はCO2と親和性が高く、多量のCO2を溶解できるという特性を持つ。一方、窒素(N2)などのガス類はイオン液体にはほとんど溶解しない。この溶解性の差を利用することで、CO2やN2などが混合した気体からCO2だけを選択して取り出すことができるのだ。このイオン液体をフィルムなどに含ませることで、CO2を分離する「膜」として使用できる。膜を用いたCO2分離回収法(膜分離法)では、膜の一方に大気や排気ガスを供給し、真空ポンプを使って他方を減圧してCO2を選択的に分離するので、原理的に熱エネルギーを必要としないのが特徴だ。だが、DAC用のCO2分離膜につかうイオン液体には、大気中の希薄なCO2を強力に捉えながらも、捉えたCO2は容易に放出できるという、相反する能力が求められる。
イオン液体を含ませた分離膜による大気中CO2の分離・回収イメージ
産総研は約20年前から、各種のガスからCO2を取り出す分離材料として、イオン液体を活用する方法を研究してきた。基礎研究としても、さまざまな陽イオンと陰イオンからなるイオン液体の合成や、CO2吸収量など各種の性能評価技術を開発。その中で最も重要といえる研究成果の一つが、役割の異なる2種類のイオン液体を混合することで、吸収と放散の各ステップが高速化されるという発見だ(2022年発表)。産総研の化学プロセス研究部門で研究グループ長を務める牧野貴至は、この成果について次のように語る。
「まず単一のイオン液体の分子構造をあらゆる角度から研究しました。そこには長年にわたる研究で培った経験と勘の積み重ねがありました。『2液を混ぜるとどうなるか』というアイデアは以前からあったものの、どこまで性能が上がるのか、実はあまり期待はしていませんでした。ところが実際に混ぜてみると、わたしたちの予想していた以上に性能が高まることを発見したのです。その実験結果に、わたしたちも驚きました」
ダイセルと共同で開発した、この「混合イオン液体膜」は、大気中と同じ濃度(0.04 %)のCO2を用いた試験で、CO2/N2の選択率が従来の高分子膜の約500倍に相当する性能を発揮した。これは、現在のDAC用分離膜の材料としては最高クラスだ。
混合イオン液体膜のCO2透過係数およびCO2/N2選択率(膜分離性能は、温度40 ℃、分離対象ガス中のCO2分圧0.04 kPa、無加湿条件で評価)。IL1'はIL1の陰イオンを最適化したイオン液体を示す。(実線は従来高分子膜の性能上限のライン)(Kohno, Yuki, et al. 2022より引用・改変*1)
「距離」と「ステイホーム」を乗り越えて進めた共同研究
産総研とタッグを組んだダイセルは、大阪市に本拠を置く大手総合化学メーカーで、大正末期から昭和初期の創業期には、社名の一部に残るセルロイドの製造・販売で会社の基礎を築いた。現在も自動車エアバッグ用インフレーターや各種フィルターで、世界有数のシェアを誇っている。これまでも産総研とは幅広い分野で共同研究を行っていたが、イオン液体膜の研究で牧野らのチームと協業を開始したのは2017年のことである。同社事業創出センター・主席部員の織田博史は、この共同研究が始まったきっかけを次のように語る。
「ダイセルは、スマートフォンの保護フィルムや液晶テレビのフィルムなど、基材のフィルムの上に機能層を塗工した製品も製造・販売しています。当社の社員が、産総研の研究者と学会で話す機会があり、『当社のフィルムの上に産総研のイオン液体を含浸させることで、新たな用途が開発できないか』と提案したのがきっかけで、共同研究が始まりました」
織田は、フィルムと「イオン液体」を組み合わせた開発について、こう続ける。
「混合イオン液体自体が、CO2分離回収技術として大きな可能性を秘めていますが、分離効率を上げるためには、含浸させる『膜』が重要です。まずは、シート状の膜にセラミックスで構成された多孔質の機能層をいかに薄くつけるかを検討しました。当初は薄くするほど効率が上がると考えたのですが、機能層の薄さに対して分離性能がなかなか追随してこない。『機能層をコーティングする技術は十分なはずなのに』と、よくよく調べたところ、実は機能層がCO2分離膜として使うには薄くなりすぎてしまっていたことが原因とわかりましたが、わかるまでにかなりの時間がかかりました」
ダイセルは、新しい膜のサンプルをいくつも作って産総研に持ち込み、混合イオン液を含浸させては分離膜の性能を測る――そうした作業が何度も繰り返された。牧野らのグループの拠点がある産総研東北センター(宮城県)と、織田が在籍するダイセル事業創出本部がある東京、新素材の企画・開発に取り組む兵庫県姫路市の協創拠点、さらにフィルム量産・製造を担う神崎工場、離れた4拠点を相互に行き交う共同作業が続いた。ところが2020年初頭に新型コロナウイルス感染症が発生し、その影響が拡大する中で対面の作業ができなくなってしまったのである。
「毎月リモート会議を行いました。ただ、実際のサンプルに触れながら、みなで集まって検討する“手合わせ”ができないため、『どうして性能が上がってこないのか。どうしたらいいんだ』とそれぞれ悩むばかりで、もどかしさばかりが募る日々でした」と、織田は当時を振り返る。
この開発を前に進めるため、2022年度から織田と一緒にCO2の分離回収膜の開発に取り組んでいるのが髙尾翔太だ。髙尾はもともと、ダイセルが得意としている水処理膜の技術者である。
「『なにが課題なのか。すべてを網羅して確かめることができない』という開発における壁は、水処理技術の場面でもよくあることです。今回の分離回収膜の開発に携わって、問題整理、要点把握、その深掘りと解決がいかに大切か、あらためて実感しています」と、織田の話に、髙尾はうなずく。産総研側も、新たなメンバーを加えて、この研究をさらに推し進めた。それが、アメリカの大学在籍時からイオン液体を使ったCO2分離膜の研究を行っていた主任研究員の河野雄樹だ。
「アメリカにいた2013年頃、現地では石炭ガス化複合発電所の排ガスなど、30 %を超える高濃度CO2を含む気体からCO2を分離する手法の研究が一般的でした。高濃度ガスからの分離と大気中程度の400 ppm(0.04 %)という薄い濃度からの分離は、本質的にイオン液体の性質が異なります。そのため、新たな発想でイオン液体の合成を進める必要がありました。たとえイオン液体のほうがうまくいったとしても、膜の技術は大丈夫なのか……。気の遠くなるほどの試行錯誤を重ねなければ、最適解が見つからなかったのです」と、当時を振り返る。
ダイセルと産総研は、膜の試作と測定を繰り返し行った。
難航する分離装置開発―中空糸膜という発想で再挑戦
2017年の共同研究着手から5年目、ついに産総研は混合イオン液体を使った分離膜の改良を進めて、先に紹介したCO2選択率を従来比500倍に向上させたイオン液体の開発に成功した。一方の、ダイセルは、工場で膜厚を一定にコントロールした分離膜のシート見本を完成させることに成功した。これで、混合イオン液体を染み込ませた分離膜を層状に積み重ねたパーツを作り、分離膜モジュールの開発をいっきに進められると期待が膨らんだ。
ダイセルが開発したシート状の分離膜のサンプル。浮きそうなほど薄く軽い。
しかし、そう簡単にはいかなかったのである。「単体の膜の性能は少しずつ向上していたとはいえ、当初想定した製品として必要なレベルを達成できていませんでした。『それなら、このシート状の膜を何層にも積層するしかない』と考え、その方向で装置の試作品を設計しましたが、うまくいかなかったんです。CO2を分離するために膜の片方を減圧しますが、そのためには装置全体の気密性を担保しなければなりません。性能が目標のレベルになるまでシート状の膜を積み重ねようとすると、気密を保つために金属の枠でがっちり密封する必要があって、装置全体のサイズが非常に大きなものになってしまう。当社の研究所に試作品が届いた時、一人ではとうてい持ち上げられない装置の重さと大きさにがくぜんとし、『これでは使えない……』と失敗を認めざるを得ませんでした」(織田)
ダイセル側の分離膜モジュール開発は、ここでいったん頓挫するかに見えた。実際、シート状の膜を積層する方法のモジュール開発は、ダイセル社内の公式な研究テーマとしては認められず、中止せざるを得なくなったのだ。しかし織田らは、“アンダーグラウンド”で研究開発を続行する。
「この研究を社会実装できるまでに持っていければ、これからの脱炭素社会において、インパクトは計り知れないほど大きい。やはり諦めたくないという思いがありました。当社内の正式な研究テーマとしては認められないものの、自分の頭の中で考え続けるのは自由ですから」と、強い意志を持って織田は挑み続けた。
さまざまな代替案を模索する中で、現在、有力視されているのが中空糸膜だ。これはストローやマカロニのように中心が空洞になっている膜で、単位容積中の膜面積を広く取ることができるため、不純物除去や精製を目的として家庭用浄水器から産業用、浄水場などで広く利用されてきた。ダイセルには、水処理技術のノウハウがある。中空糸膜にセラミック機能層を塗工した前例はないものの、海外企業には先行事例もあり、ダイセルの技術をもってすれば実現できると見込んだ。
「シート状の膜での研究開発を進めている企業は他にもあるようなので、むしろ中空糸膜で勝負することは差別化につながります。この方法はコストの問題はあるものの、それを乗り越えるだけの価値はあるはずです」と、これまでも中空糸膜をあつかってきた髙尾は確信している。
産総研側は、ダイセルが平膜積層型の装置開発に苦労している間、イオン液体の耐久性能の向上やコスト低減のためのさまざまな方策を検討していた。そこにダイセルから中空糸膜を使うアイデアがもたらされた。この中空糸膜で一定の性能評価が得られれば、より軽量で小型の、空気からCO2を取り出すための装置開発が進められる可能性が出てきたのである。
ダイセルの水処理技術から発想された中空糸膜に突破口を見いだす
カーボンリサイクル技術確立を目指して
DACがカーボンニュートラルを実現するために不可欠な技術であるという認識は、広がりつつある。しかし、世界的に見ても商用化まで至った例はごくわずかで、回収効率やエネルギー効率の向上、あるいは吸収材や分離膜の開発などに多くの課題が残る。
「わたしたちが新しい方法を試みようとする時、『この技術とこの技術を組み合わせたらどうなるか』と産総研に相談すれば、産総研内にはほとんどの場合、当該分野の研究者がいます。所内にいなくても、研究者のネットワークで、詳しい研究者や時には企業なども紹介してもらえる。産総研内外のネットワークの豊富さにはいつも驚かされるし、助けられています」と、織田は語る。産総研とタッグを組むことが、企業としての技術追求の幅と奥行きを広げるチャンスと捉えている。
一方の産総研にとっても、企業との協業が技術の社会実装や事業化を進める上での重要なアクセルになっている。「わたしたちには事業化に向けた経験や知見が少ない。とりわけ市場性、商品コスト、安全性などについては、研究室内ではなかなか見えてこないところです。それらについて、企業の視点で課題を提起し、実際にものづくりに取り組んでいただけることはわたしたちだけではとてもできないことで、ありがたく思っています」と牧野もこの協業に大きな価値を見出している。
経済産業省のロードマップでも、DACの実用化は2040年以降のターゲットであり、まだまだ先は長い。だが、確実に実現するためには産総研のような研究機関と企業とが試行錯誤しながら協業し、さまざまな困難を乗り越えていかなければならない。産総研の研究者とダイセルの技術者は、カーボンニュートラルの実現という共通の目標に向かって、一歩ずつ、前進し続ける。
技術力の社会実装・事業化には「よきパートナー」が不可欠
*1: Kohno, Yuki, et al. "Ionic Liquid Mixtures for Direct Air Capture: High CO2 Permeation Driven by Superior CO2 Absorption with Lower Absolute Enthalpy." ACS omega 7.46 (2022): 42155-42162.[参照元へ戻る]
株式会社ダイセル
事業創出本部
事業創出センター
主席部員
織田 博史
Oda Hiroshi
化学プロセス研究部門
化学反応場設計グループ
研究グループ長
牧野 貴至
Makino Takashi
株式会社ダイセル
事業創出本部
事業創出センター
研究員
髙尾 翔太
Takao Syota
化学プロセス研究部門
化学反応場設計グループ
主任研究員
河野 雄樹
Kohno Yuki
株式会社ダイセル
産総研
材料・化学領域
化学プロセス研究部門