積層セラミックコンデンサとは?
積層セラミックコンデンサとは?
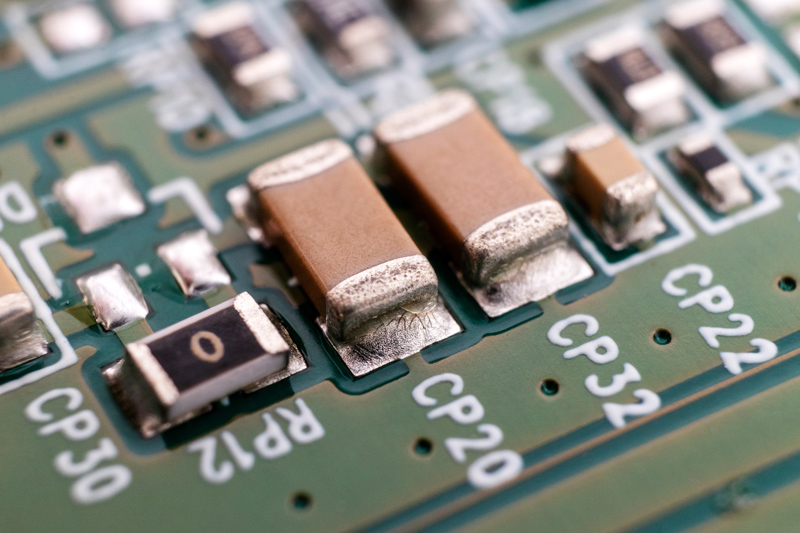
2025/04/16
積層セラミックコンデンサ
とは?
科学の目でみる、
社会が注目する本当の理由
積層セラミックコンデンサとは?
積層セラミックコンデンサとは、電気回路に使われている素子の一つで、半導体集積回路の働きをサポートするものです。セラミック製の誘電体層と電極層を交互に複数積み重ねた構造からなり、電気を一時的に蓄えたり、貯め込んだ電流を放出したりと電流を制御するために使われます。スマートフォンやパソコン、車載機器などに活用され、これら電子機器の普及につれて役割がさらに注目されています。特にスマートフォンなどの電子機器には常に小型化や高性能化などが求められており、このようなニーズに応えるためには、積層セラミックコンデンサを小型化すると同時に大容量化する必要があります。
パソコンやスマートフォンなどの高性能化を実現するカギは、半導体の集積度にあります。半導体の集積率向上にあわせて、周辺部品にも微細化による集積率向上が求められます。半導体集積回路の働きをサポートする機能を果たす積層セラミックコンデンサは、約10年周期で小型化・高性能化が進んでいます。小型化しながらも性能を高めるためには、1層を薄くすると同時に数多く積み重ねる「積層化」が求められます。積層セラミックコンデンサの開発の現状や新規の積層技術について、マルチマテリアル研究部門の板坂浩樹主任研究員に聞きました。
積層セラミックコンデンサとは
小型化・高性能化の求められる電子機器に不可欠な部品
電気を一時的に蓄え、電流の流れを制御するなどさまざまな機能を持つコンデンサは電子機器に不可欠な部品で、セラミック製のものが多く使われています。なかでも積層セラミックコンデンサ(Multi-Layer Ceramic Capacitor、以下「MLCC」)は、スマートフォン1台あたりに約1000個も使用される重要な電子部品です。スマートフォンやタブレット端末などの電子機器が小型になり、性能が向上するにつれて内蔵される電子部品にも小型化が求められるなかで、MLCCの小型化にむけた技術開発が注目されています。
MLCCは、金属の電極層と誘電体層を交互に積み重ねたミルフィーユ状の層状構造をもちます。MLCCが貯められる電気の容量である静電容量を増やすためには、誘電体層を薄くして積層数を増やす必要があります。誘電体層をより薄くしながらも、MLCCの性能をいかに高めていくか。求められるのは、誘電体層と電極層をナノスケールに薄層化する、新たな積層プロセス技術の開発です。
積層セラミックコンデンサの内部構造
現状の積層セラミックコンデンサの課題
現在使われているMLCCでは、誘電体層の材料となるチタン酸バリウム(BaTiO3、以下BTO)粉末と電極層の原料となる金属粉末を交互に積層し、高温で焼き固めることで積層構造を作っています。この誘電体層の厚みは薄いもので0.5 μm程度であり、原料粉末の粒子サイズに近づきつつあり垂直方向に積み重ねられるBTO粒子は4~5個に限られます。
現在主流になっているBTO粒子を原料から粉砕して作る方法では、BTO粒子をこれ以上微細にすることや粒径をそろえることが難しく、性能向上を阻む壁となっています。またこの方法は、素材を粉砕することで粒子がダメージを受けるため、欠陥の導入により結晶性が低下する、粒子の大きさや形にばらつきが出る、といったデメリットがあります。さらに、積層化する際の焼結工程でも誘電体層の厚みにムラが出るのも避けられません。結果、誘電体層の絶縁性が低下するなどの課題があります。誘電体層をより薄くしながら、MLCCの性能を高める技術が求められています。
産総研の取り組み
独自の交互積層プロセス技術の研究開発
結晶性の高い粒子を生成する水熱合成法を進化させる
産総研では、十数年前からBTOによる原料粒子の合成法研究に取り組み、2012年にはナノキューブと呼ばれるサイコロ状の粒子を合成する技術を開発しました。これにより、1辺のサイズが15~20 nmと非常に小さいながら、粒径のそろった結晶性の高い粒子を作製することが可能になりました。用いられるのは、耐圧容器の中に原料を入れて煮て作る「水熱合成法」です。従来のトップダウンの粉砕法と異なり、原料原子を積み上げることで求める構造を作製するボトムアップの合成法といえます。
水熱法を用いて作製されたナノキューブの透過電子顕微鏡写真
積層を行う際、球形に近い従来の粉砕粒子を使った場合には可能な限り緻密に充填しても密度は最高で74 %ほどにとどまりますが、ナノキューブを使うと積層した際の粒子密度を理論上100 %にまで高めることができます。
産総研では、BTOナノキューブの合成に加えて、低速ディップコート法と呼ばれる技術によるBTOナノキューブ規則配列膜の形成法の開発にも取り組んできました。この手法では、ナノキューブを分散させた液体に基板を漬けて、ゆっくりと引き上げることで、基板上に粒子が自己組織的に配列していき、緻密な膜を作ることができます。
ナノキューブを用いた低速ディップコート法の模式図
ただしこの形成法には、溶媒が乾燥する際にマイクロクラックと呼ばれる微細なヒビが入ってしまう問題点があります。そこでこれを解決すべく、粒子をきれいに集積させつつクラックが発生しない製法の開発に取り組みました。基板上に単層膜を集積させる低速ディップコート法と異なり、新たな製法では水面にキューブの単層膜を集積させます。
まず水面に界面活性剤の分子膜を作ります。その後、溶媒にナノキューブ粒子を含んだ液体(分散液)を滴下することで、界面活性剤の分子膜の方からキューブを圧縮する方向へと、常に表面圧がかかります。この圧力をかけ続ければ、クラックの発生を抑制したきれいな単層膜を作ることができます。
界面活性剤の表面圧を利用し、クラックを抑制した集積方法
絶縁性を確保するためにグラフェンを積層
密度100 %の単層膜が作製できることが理想的ですが、現実問題としてはキューブ間に発生する微妙なサイズや形状の違いにより、ナノスケールの隙間が発生します。このような隙間のある状態で金属製の電極を乗せると、金属が隙間に入り込んで上部電極と下部電極の間でショートが起こり、コンデンサとして作動しなくなるリスクがあります。
そこで次の課題となったのが、膜の絶縁性を担保しつつコンデンサの構造を作製する技術開発です。課題解決策として、二次元炭素素材のグラフェンに着目しました。グラフェンをバリア層としてBTOナノキューブ単層膜の上に重ねることで、金属電極を形成した際にナノキューブの単層膜に金属は一切入り込まなくなり、誘電層の厚みが約20 nmと極めて薄いにも関わらず、絶縁性の担保されたコンデンサ構造を得ることができます。性能を確認すると、グラフェンありの場合はグラフェンなしに比べ、低電圧で漏れ出る電流値が大きく下がり、一定程度の電圧領域までは絶縁性が確保されることが明らかになっています。
グラフェンをバリア層としたコンデンサ構造
また、優れた導電性を持つグラフェンを電極とし、BTOナノキューブ単層膜と組み合わせることで、極めて薄い電極層と誘電体層からなる交互積層構造を作製できます。
この積層構造では従来のMLCCの積層構造と比べて、誘電体層の厚みを10分の1以下、電極層の厚みは100分の1以下にすることができました。(2023/09/01プレスリリース)
グラフェンとBTOナノキューブ単層膜の交互積層構造
実際の交互積層構造の断面観察像
量産化に向けた今後の課題
今回作製した交互積層構造はまだコンセプトモデルの段階であり、コンデンサとして動作可能な回路構造とはなっていません。ただし極限まで薄層化した時にどのようなものができるのか、これからの可能性は提示できたと考えています。
今後、実用化に向けた課題は材料面とプロセス面の2つに分けられます。まず材料面では、BTOナノキューブの粒径をいかに小さくし、同時に結晶性を高めるかが課題となります。プロセス面では、ナノキューブ膜と多層グラフェン電極をいかに均一かつ薄く積み重ねるかも重要です。さらに、現時点ではあくまでもラボスケールでの技術であるため、量産化するためのスケールアップが必要となります。より効率的に、広い面積で均一な薄膜を作成するためには、ラボスケールとは次元の異なるプロセスを新たに創出する必要があります。
産総研では、この新たなプロセスの開発について企業との共同研究に取り組み、革新的なMLCCを早期に実現したいと考えています。ご関心のある方はぜひお問い合わせください。