メタノールのあたらしい作り方
メタノールのあたらしい作り方
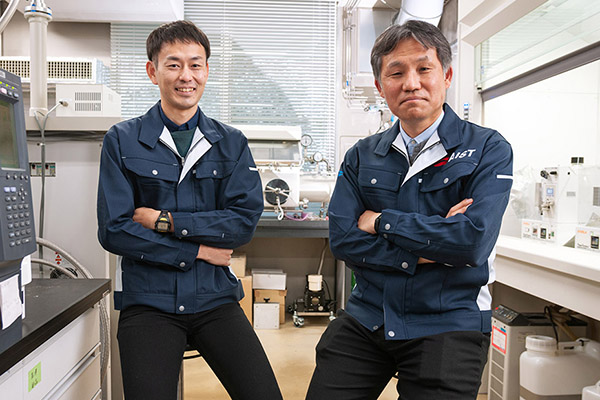
2022/02/28
メタノールのあたらしい作り方 低温・低圧でのCO2資源化をアイデアで乗り越える
日本政府が2050年の達成を国内外に宣言したカーボンニュートラル。その国家方針の下、さまざまな分野の研究開発が推進されている。その一つが、二酸化炭素(CO2)を炭素資源と捉えて有効利用するカーボンリサイクル技術の開発だ。中でもさまざまな化成品の原料や燃料として利用できるメタノール(CH3OH)へ転換する技術開発が活発に行われてきた。しかし、熱力学的に安定な物質であるCO2をメタノールに転換するには、従来の方法では大量のエネルギーが必要な「高温・高圧」反応条件が不可欠だった。有用なカーボンリサイクル技術として実用化するには、より穏やかな条件で合成し、投入エネルギーを抑えることが必要になる。今回産総研では、高性能触媒によりこれまで不可能だった「低温・低圧」条件下でのCO2からのメタノール合成に成功した(2021/1/14 プレスリリース記事)。カーボンニュートラル社会を実現する有効な手段として、今後の展開が注目されている。
実用化を目指し低温・低圧でのメタノール合成にチャレンジ
地球温暖化防止に向けて、CO2排出削減が世界的な課題となって久しい。再生可能エネルギーや省エネなどのCO2を排出しない技術とともに、どうしても排出せざるを得ないCO2を転換し有効利用するためのCO2資源化技術の研究開発が進められている。この技術が実用化できれば、CO2を排出しない技術とCO2を資源として再利用する技術の両輪によって、CO2に起因する地球温暖化の問題を解決できる可能性が高まる。
CO2から転換できる物質として注目されているのがメタノールである。年間約1億トン製造されているメタノールは、代替燃料として利用できるだけでなく、プラスチックなどの化成品原料として利用されており、CO2からメタノールを効率的に合成するための触媒や製造技術の開発が行われてきた。
化成品や燃料に変換されるメタノール
「既に、地熱発電を利用した水の電気分解で得られる水素(H2)とCO2から年間4000トンのメタノールを合成し、販売している企業も海外では存在しています。ただし、従来の反応プロセスで必要となる250 ℃、5 MPa以上という高温・高圧条件下での製造には、安定的に得られるエネルギーが必要となります。また、高温条件下ではメタノールへの転化率が低く、一酸化炭素やメタンなども副次的に生成するという課題がありました。発電出力が変動しやすい再生可能エネルギーを用いて、メタノールを効率よく合成するためには、反応の低温・低圧化は以前から大きな課題となっていました」
そう話すのは、ゼロエミッション国際共同研究センター首席研究員の姫田雄一郎だ。姫田率いる研究チームは、かねてより「低温・低圧条件で駆動するCO2変換触媒」の研究開発を行ってきた。
CO2資源化への長年の取り組み
今でこそ気候変動対策としてCO2の排出量削減と資源化は世界的共通課題と認識されているが、姫田がCO2変換触媒の研究を開始した1990年代には、化石資源の枯渇や価格高騰に対する原油代替資源としての開発要素が大きかった。
「CO2資源化の研究は、カーボンリサイクル技術として期待が高まっていますが、2000年前後は原油価格が比較的安定していたこともあり、CO2変換触媒に携わる研究者は、世界中を見渡しても、片手の指で数えられるほどにまで減っていたこともあるのです」と姫田は当時を振り返る。姫田自身も所内外の研究者から「別のテーマに変えたほうがいいのでは」と何度かアドバイスされたが、「CO2の問題は、人類が本腰を入れて取り組まねばならない時期が必ずやって来る」と信じ、この研究に注力し続けた。
転機は、2010年代前半に米国ブルックヘブン国立研究所との国際共同研究によりイリジウム(Ir)を用いた高性能触媒を開発し、世界で初めて常温・常圧条件の水中でCO2と水素からギ酸(HCOOH)の製造に成功したことである(2012/3/19プレスリリース記事)。さらに、ギ酸分解触媒を開発し、これを利用した高圧水素製造技術へ展開している(産総研LINK No.29)。これらの研究成果は、CO2から合成できるギ酸を用いた新しい水素キャリア技術として評価を受けたが、姫田はギ酸の先にメタノールの合成を見据えて研究を行っていた。メタノールは既にサプライチェーンが確立し、社会的需要が高いと考えていたからだ。目標を低温・低圧条件下でのメタノール合成と設定し研究を進めていたが、その実現は容易ではなかった。実際、スイス連邦工科大学ローザンヌ校との国際共同研究では、高圧条件下のCO2水素化でも、主としてギ酸が生成され、メタノールの生成はわずかであることがわかっていた。
「複数の活性点をもたせる」アイデアが突破口
徐々にCO2変換触媒の研究が認められ、広く知られるようになり、異なる研究分野のメンバーが本研究に加わり始めたことで、さらに技術開発は進展していった。
前述のとおり、CO2からのメタノール製造は、銅系固体触媒を用いれば技術的には可能であるが、通常5 MPa以上の圧力、200 ℃以上の高温・高圧条件が必要で、製造工程で大量のエネルギーを消費する。さらに、高温条件下では「平衡」と呼ばれる制約によりメタノールへの転換率が低く、加えて一酸化炭素やメタンなどの目的外の生成物ができてしまうという問題があった。
一方で分子触媒を用いて80~150 ℃でのメタノール合成が報告されるようになった。しかし、分子触媒は生成物と触媒が液体に均一に溶解した状態(液相)で反応するため、液相に溶け込んだメタノールと触媒を反応後分離する必要があり、効率が悪い。製造プロセスのエネルギー消費と効率性を考えると、実用化は困難であった。
より低温・低圧の条件だけでなく、製造プロセス全体のエネルギー消費を考えた、まったく新たな生成方法が求められていたのである。
姫田らは当初、改良を重ねたイリジウム触媒を使って、これまで反応を制御しやすいとされてきた液相で、CO2水素化によるメタノール合成に取り組んでいた。しかし、メタノールを合成するまでの多段階反応のうち第一段階として生成されるギ酸が得られるだけで、次の段階で生成されると踏んでいたメタノールの姿はどこにも見当たらなかった。研究チームは、ギ酸生成が進まない原因を、化学反応の宿命とも言える「平衡」と呼ばれる制約によるものと推定していたが、その解決方法を見いだせないでいた。
最初の突破口となったのが、反応が起こる部位である「反応活性点(この場合、イリジウム原子)」を二つ持つ「複核触媒」の開発だった。2014年からチームに加わっていた若手研究者、尾西尚弥が開発した「複核触媒」を使えば、それぞれの反応活性点の協働作用で、反応活性点が一つの触媒では実現できない反応がもたらされるのではないかと考えたのである。実はこの複核イリジウム触媒は、別用途に使用するために開発されていたが、複数の活性点による協働作用で多段階反応の平衡を乗り越える手段として、メタノール合成に用いることになった。
常識外!低温でのガス相反応?
ブレークスルーのきっかけをもたらしたのが、もう一人の若手研究者、兼賀量一だった。「姫田さんから『兼賀くん、CO2から低温でメタノールができたら何か賞をもらえるよ』と言われ、とにかく前向きに実験を進めてみようと思って取り組みました」と兼賀は当時を振り返る。
「ダメ元でいいから、いろいろ試してみよう」──そう考えた兼賀は、通常液相で反応させる分子触媒を固体のまま、溶媒を用いることなく水素とCO2の混合ガス中(ガス相)で反応させた。最初はさまざまな金属中心が一つある単核触媒を用いていたが、メタノールどころかギ酸すら検出できなかった。常識的には、水素分子の結合を切断するためには、高温条件が必要であり、何ら生成物が検出できない結果は当然であった。しかし、その結果を聞いていた尾西が、既に合成していた複核触媒を試すことを軽い気持ちで提案した。
メタノール合成に使用した複核触媒
驚いたことに、複核触媒を用いるとメタノールが検出された。これがブレークスルーのきっかけとなった。「メタノールが検出されたときはすごくうれしかったですね」と兼賀は目を細める。しかし、この報告を聞いた姫田は、常識外の低温条件のガス相での反応であったため、とくに慎重に研究を進めさせた。実験操作で混入したメタノールではなく、反応で生成されたメタノールであることを確認するために、尾西にも確認実験させただけではなく、自らも実験を行って複数人で確かめたほどだった。結果的に、CO2と水素からメタノールが生成している確証が得られたが、生成量はわずかであった。
当初の実験結果と論文発表時の実験結果
ガス相ではギ酸の生成が抑えられ、メタノールが生成していることがわかる。
研究チームはその後も触媒構造や反応条件の検討を重ね、ついに30 ℃の穏やかな温度条件、あるいは0.5 MPaという比較的低圧の条件下で、CO2からメタノールを合成することに成功した。従来の銅系固体触媒と異なり、メタン、一酸化炭素などの副産物は生成しない。さらに、分子触媒を固体状態のままガスと反応させるため、生成した気体状態のメタノールと固体の触媒の分離が容易になった。また、従来の銅系固体触媒のガス相反応と比べて分子触媒は効率よく反応が進行した。特に分子触媒は金属を取り囲む有機分子(配位子)を精緻に設計・制御できるため、今後新たな展開が期待できるのも強みだ。
姫田は「この成果は、2人の若手研究員のアイデアとチャレンジ精神のたまもの。『複核触媒を使う』と『ガス相で反応させる』という二つのアイデアがそろわなければ、CO2からのメタノール合成の障害要因を取り除くことはできなかった」と兼賀と尾西らに賛辞を送る。一方で兼賀は、「姫田さんをはじめとする先輩研究者たちが整えてきた土壌があったからこそ」と感謝の気持ちを表す。経験値と柔軟な発想力、チームの力が一つとなって大きな成果を生み出したのだ。
一定の成果は達成したが、これらはすべて実験室内での出来事である。この研究成果を実用化するにはまだまだ長い道のりが残されている。姫田によれば、反応機構の詳細な解明をさらに進めることで触媒の基本性能である「活性」「選択性」「耐久性」を高め、さらに低コスト化を図る必要があるという。「私たちが今回編み出した手法をそのまま化学プラントに適用したとしても、明日からいきなりメタノールの大量生産が可能になるわけではないのです」と姫田は言う。
とはいえ、研究チームがCO2の水素化により、メタノール合成を低温・低圧下で実現するための基盤を確立したことは間違いない。「十数年後をめどに技術を実用化し、カーボンリサイクルに貢献できればうれしい」と姫田は目を輝かせる。
本成果に大きく貢献した兼賀は、さらにはるか先の未来にも思いをはせる。「人類が本格的に宇宙に進出するとき、移住先天体の候補として挙がるのが月と火星。特に火星は、大気のほとんどをCO2が占めています。この技術が、いつか火星で活躍する日が来るかもしれません。かなり先の話ですが、そんな未来に貢献できるよう、引き続き頑張ります」と、兼賀は冗談っぽく夢を語った。
エネルギー・環境領域
ゼロエミッション国際共同研究センター
首席研究員
姫田 雄一郎
Himeda Yuichiro
エネルギー・環境領域
省エネルギー研究部門
エネルギー貯蔵システムグループ
研究員
兼賀 量一
Kanega Ryoichi
産総研 エネルギー・環境領域
ゼロエミッション国際共同研究センター
産総研 エネルギー・環境領域
省エネルギー研究部門