複合素材プラスチックを循環利用するケミカルリサイクルの新たな技術
複合素材プラスチックを循環利用するケミカルリサイクルの新たな技術
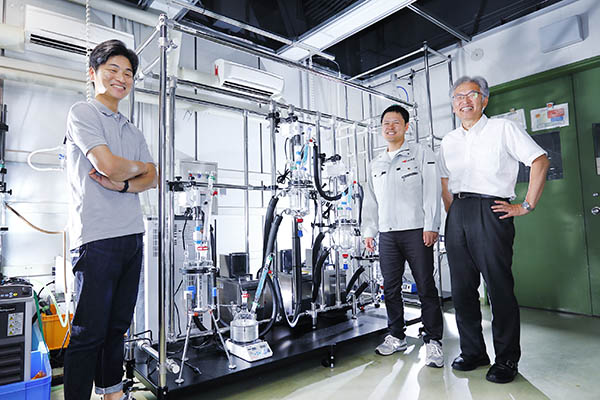
2025/07/09
複合素材プラスチックを循環利用する ケミカルリサイクルの新たな技術
プラスチックごみによる環境汚染は、世界中で大きな問題となっています。産総研では、ペットボトルやポリエステル繊維など現代社会で非常に多く使われているポリエチレンテレフタレート(PET)樹脂に着目し、低エネルギー・低コストのケミカルリサイクル技術を開発しました。そして今、研究者、エンジニアリング人材、AISolがタッグを組み、社会実装に向けて進んでいます。
常温でPETを分解できる技術を開発し複合繊維のリサイクルという難題に挑む
日本で1年間に廃棄されるプラスチックは約824万トンにのぼり、ケミカルリサイクル、マテリアルリサイクル、エネルギーリカバリーの3つの方法で約86%がリサイクルされています。しかし、エネルギーリカバリーを含めないEUの定義では、日本のリサイクル率は25%にすぎません。そのため、ケミカルリサイクルとマテリアルリサイクルをもっと増やす必要があり、基盤技術の開発が急務となっています。
プラスチックごみの多くは複合素材であり、それを循環式で有効に再利用するにはケミカルリサイクルが適しています。しかし、従来の手法では200 ℃以上の高温で反応させるため、エネルギーコストの面で課題がありました。それを克服する画期的な技術を開発したのが田中真司です。
「メタノールを使って化学的にPETを解重合(分解)するのは、アルコール同士を交換するエステル交換反応です。問題は正反応(分解)と逆反応(重合)が両方起こる平衡反応であること。逆反応を抑えないと、分解効率が低下してしまいます。そこで、副生成物のエチレングリコールと反応しやすい『炭酸ジメチル』という溶媒を使い、化学的に安定な炭酸エチレンに変換することで反応を促進させるアイデアを考えました。この方法なら常温でPETを解重合できます」
ペットボトルを粉砕して検証したところ、最終的に90%以上の回収率でPETの原料であるテレフタル酸ジメチルを得ることに成功しました。2021年11月8日に論文発表およびプレスリリースをすると、予想以上に繊維業界からの反響があったといいます。その半年前には、環境省が「サステナブルファッション」のウェブサイトを公開し、洋服と環境負荷に関する情報発信をしていました。
実は田中の技術は、複合繊維でも有効です。「開発した技術を、複合繊維や染色した繊維などに展開したいと考えています。最近、ポリエステルと綿の複合繊維、ポリエステルとポリウレタンの複合繊維で実験をしたところ、ほぼ同じような条件で解重合反応が進行してテレフタル酸ジメチルを回収することができ、同時に綿とポリウレタンもそれぞれ回収できることを実証しました」
複合繊維からすべての成分を再利用可能な状態で取り出す。この極めて難しい技術を確立するため、意欲的な研究が続いています。
社会実装に向けたスケールアップで課題を洗い出し、技術を極める
2023年4月に新設された「エンジニアリング室」に所属する山本哲也は、研究成果の社会実装に向けてスケールアップの技術開発を担っています。
「2030年までにコマーシャルプラントを稼働させるという、タイトなスケジュールでプロジェクトが進行しています。ラボスケールでは最大500 g程度でしたが、今年は5 kg~50 kgまでの原料を処理できるベンチプラントで実証試験を行いました。今後はパイロットプラントの基本設計と建設、そして実証試験へと進んでいきます」
スケールアップの各段階でさまざまな課題が見つかり、山本は田中と連携しながら開発を進めています。
「未反応の布成分が反応器内部に残ってしまうと、どう回収するかが問題となります。一方、反応器での撹拌がうまくいき、ラボスケールよりも良い結果が出ることもあります。今まではPET100%で反応しやすかったのですが、これから綿やポリウレタンなどの成分が混ざった原料にも適応できるよう技術を極めていく必要があります」
サーキュラーエコノミーのエコシステム形成を見据えて
産総研の優れたシーズを社会実装に繋げるのがAISolの役割ですが、その目指すところは単に技術の実用化にとどまらないと中林亮は言います。
「私たちはサーキュラーエコノミー(循環経済)のエコシステムを形成しようとしています。その根本にあるのは世界的な人口増加問題であり、地球の限界(プラネタリー・バウンダリー)を超えない活動とウェルビーイングの両立をトータルに考え、技術やシステムで貢献しなければなりません。
産総研の革新的なPETケミカルリサイクル技術の社会実装は、資源循環を技術革新で達成する旗頭の1つになり得ると捉えています。田中さんの技術は、ものすごく反応がきれいで筋が良いんです。だから普通は社会実装まで10年かかるところを、大幅に短縮できる可能性があり、2030年を目標にすることができました」
中林は、既存のマテリアルリサイクルも伸ばしつつ、今まで廃棄や焼却をするしかなかった部分を田中のケミカルリサイクルで補完するというように、両方セットでプラスチック全体のリサイクルを考えています。
産総研グループによる独自の新体制で研究開発と社会実装をともに推進する
研究者、エンジニアリング人材、AISolがタッグを組んで社会実装を進める体制をどのように受け止めているか、3人の思いを聞きました。
「スケールアップをすることで初めて分かることも多く、普通はできない経験ができるので大変ありがたいです。今後別のテーマで研究開発を進める上でも、自分の糧になるでしょう。またこの体制のもとで、自分の基礎研究に専念して次の技術シーズを考えることもできます」(田中)
「社会課題に対して非常にインパクトのある技術なので、大きなやりがいを感じています。また、この体制による社会実装への取り組みは産総研において最初のケースです。良いモデルケースになるように、何としてもやり遂げたいと思っています」(山本)
「素晴らしい人材が揃い、技術レベルも高いので、産総研グループでの仕事は視座が高まるような気がします。社会全体が発展できるように考えるのは、とても面白い仕事です」(中林)
3人は社会実装を目指すチームの中で、その先に持続可能なサーキュラーエコノミーの実現を見据えて前進しています。
本記事は2024年9月発行の「産総研レポート2024」より転載しています。
触媒化学融合研究センター
ケイ素化学チーム
主任研究員
田中 真司
Tanaka Shinji
研究戦略企画部
エンジニアリング室
総括主幹
山本 哲也
Yamamoto Tetsuya
株式会社 AIST Solutions
プロデュース事業本部
事業構想部
事業プロデューサ
中林 亮
Nakabayashi Akira
産総研
材料・化学領域
触媒化学融合研究センター
株式会社 AIST Solutions