超薄型圧電センサで製造プロセスの異常を検出
超薄型圧電センサで製造プロセスの異常を検出
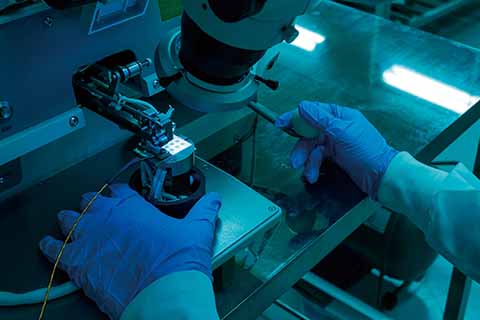
2020/09/30
超薄型圧電センサで 製造プロセスの異常を検出 AIとの組み合わせで生産効率を大幅にアップ
製造現場では、"歩留まりの向上"は永遠の課題だ。例えば、半導体デバイスの製造工程におけるプラズマの異常放電はまさにこの歩留まりに大きく影響するため、その検知技術が求められていた。産総研は耐熱性を有する圧電薄膜を用いた薄型構造のAEセンサを開発、これを製造装置の内部に取り付けることでプラズマ異常放電の検出に成功した。さらに、このセンシング技術をAIによる異常診断技術と組み合わせることで、製造工程での異常検出率を大きく向上させ、製造現場の歩留まり向上に貢献している。
製造プロセスの異常放電をプロセス中で早く捉えたい
IT技術の進展で多くの機器に使われているLSIやMEMSデバイスの製造時には、ドライエッチングやスパッタリングなどのプラズマを使うプロセスが不可欠だが、このプロセス中にプラズマの異常放電が発生することがある。するとウエハ上につくりこむデバイスの配線がショートしたり装置内の部品が損傷したりするため、デバイスの歩留まりが悪くなってしまう。さらにこのような異常放電は他の不具合も引き起こす恐れがあり、できるだけ早く発見し、修復を図りたい、それが製造現場の願いだった。
「デバイス製造時のプラズマ処理工程は30回以上に及ぶこともあります。欠陥に気づかずに後工程に進み、多くの時間を費やし、付加価値がついてから不良品だとわかった場合の損害は小さくありません。そのため、異常放電があったらすぐにそれを検知し、製造プロセスへの影響を抑えられる技術が求められてきました」と生産プロセス評価研究チームを率いる田原竜夫は説明する。
中でも必要とされているのが、ウエハの損傷に直結するウエハ周辺部の異常放電を検出する技術だが、これまで有効な検出手法は存在しなかった。その理由は、半導体デバイスの量産装置は非常にコンパクトかつ精密に設計され、センサの設置が困難だったからだ。
材料が変形あるいは破壊されると、内部に蓄えていたひずみエネルギーを弾性波として放出するAE(アコースティック・エミッション)という現象が生じる。異常放電が起こると、そのときの衝撃も弾性波として伝播するため圧電素子を用いたAEセンサで検知することが可能だ。しかし、半導体デバイスの量産装置内は狭く、電磁波が飛び交い、かつ熱が加わるため、厚みがあり耐熱性も高くない汎用AEセンサは設置できない。装置の外にセンサをつける方法もあるが、さまざまなノイズが入ってくるため、センサの反応が異常放電かどうかを判別することが難しい。
田原は検知センサの研究を進める中で、圧電性セラミックスの中で最も高い耐熱性(1,200 ℃)を有する窒化アルミニウムを使って薄型AEセンサにすれば、デバイス製造装置にセンサを内蔵できると考えた。
窒化アルミニウムは力が加わると電荷を発生する圧電材料で、薄膜化しても圧電センサとして使えることが知られていた。田原は窒化アルミニウムの圧電センサをウエハ製造装置内部に入れられるよう、薄型AEセンサとしての機能化に挑戦した。
「開発したセンサは、素子の厚さ3 μm、検出部の厚さ1 mmという超薄型です。これを実際のデバイス製造プロセスで試してみたところ、ノイズに邪魔されずにプラズマの異常放電を検出できました。これでようやく、これまで困難だったプロセス中の異常検出が実現できたのです」
AIによる異常診断と組み合わせることで診断精度が大幅に向上
この窒化アルミニウム薄膜センサはほかにも量産用ワイヤボンダや自動車部品加工など、センサによる検知が有効でも汎用AEセンサを設置するスペースがないというプロセスに用いることができる。
田原が所属する生産プロセス評価研究チームの強みは、このような新しい高精度なセンサを開発することに加え、さまざまなセンサやデータの解析方法を組み合わせ、それぞれの現場に適したかたちで有効な異常検知システムとして機能させる提案ができるところにある。
「現在は、センシングと機械学習を組み合わせ、いかに異常診断を高精度化するかに取り組んでいます。センサ自体は既存のものでも、それらと情報技術を組み合わせることで、それまで応えられなかった課題を解決できるのです」(田原)
人工知能(AI)にビッグデータを学習させ、何らかのソリューションにつなげていくための研究開発は、近年盛んに行われている。製造業においてもIoT化が進み、毎秒毎秒、さまざまな情報が取得され、処理が試みられている。
「しかし製造現場においてはデータの量が確保できないことが多く、価値や質に注目して進めています」
そう語るのは、製造プロセスのセンシングデータと機械学習を組み合わせ、診断精度を向上させる研究に取り組む石田秀一だ。センサで得られた信号が不具合につながるものか、そうではないものかを診断し、より診断の正答率を上げていくことに取り組んでいる。
「機械学習ではAIに良品をしっかり覚えさせ、それ以外を不良品として診断させるわけですが、実は製造現場では、これが正解だとAIに学習させる教師データがとても少ないのです」
通常、デバイスを製造するとき、ラインから出てくる最初のいくつかをチェックし、問題がなければ本格的にラインを稼働させる。つまり“良品”と確定されるのは最初のいくつかだけで、その後のデバイスは良品とみなされるものの厳密には良品であると判断されてはいないのだ。しかも、現在の製造現場では多品種を切り替えながら製造しているため、同じ種類の製品から良品と確定したデータを得る機会は少なくなってしまう。
確実に“良品”と認められたものだけを教師データとするなら、教師データは少ししか確保できず、診断精度は向上しない。この問題を乗り越えるため、石田は少ない情報をいかに有効活用するかを考えなければならなかった。
「製造ラインでつくられているものは、良品だと厳密に判定されていないだけで、ラインによって多少のばらつきはあっても、実際にそのラインで作られているものはほとんどが良品です。つまり、確実に良品判定を受けていなくても、現場から聞き取った情報から、教師データとして取り込む価値のある情報だと判断して良いと考えました。データ数をそろえるため、未検査の製品から価値のあるデータ、すなわち多少の質のバラつきのある中で、品質が高いと判断できる製品を選別し、教師データとして取り込むことにしたのです」
学習するデータ数が増えたことでAIのパターン推論能力は強化され、実際に異常診断に使えるレベルの指標を獲得することができた。センサでの異常検知とこのような機械学習の成果を組み合わせたことで、ある製造現場では、30%程度だった異常検出率を96%まで高めることに成功したのである。この適切なセンシングと情報処理の組み合わせという手法は、単なる異常検出率の向上にとどまらず、異常そのものの発生原因解明やプロセス改善提案にもつながっている。
「生産プロセス評価研究チームは、今後、異常の予兆を正確に把握するための研究をさらに進め、予防保全に有効な技術を開発して、製造現場の生産性向上に貢献していきたいです」田原はそう語った。
産総研で開発された薄型AEセンサ
エレクトロニクス・製造領域
センシングシステム研究センター
生産プロセス評価研究チーム
研究チーム長
田原 竜夫
Ishida Shuichi
エレクトロニクス・製造領域
センシングシステム研究センター
生産プロセス評価研究チーム
主任研究員
石田 秀一
Tabaru Tatsuo
産総研
エレクトロニクス・製造領域
センシングシステム研究センター