バイオエタノールからタイヤゴムをつくる
バイオエタノールからタイヤゴムをつくる
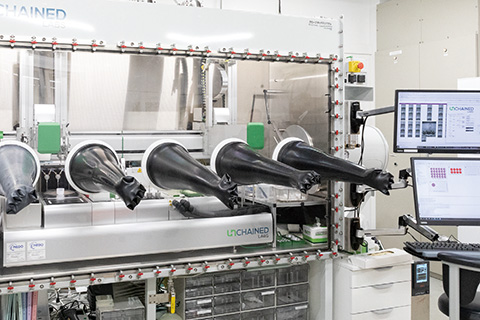
2020/01/31
バイオエタノールからタイヤゴムをつくる インフォマティクスで超高速の材料開発
2016年にスタートした「超先端材料超高速開発基盤技術プロジェクト(超超プロジェクト)」。産総研はこのプロジェクトで、インフォマティクス(情報科学)、計算科学や人工知能技術(AI技術)を活用したアプローチで、新しい機能性材料の超短期間での開発に成功した。2019年には横浜ゴムとの共同研究により、バイオエタノールを原料とした合成ゴムを完成させ、非石油原料を使ったタイヤの実用化が動き出している。
材料開発にインフォマティクスを活用
新しい機能性材料を開発するには、一般に、とても長い時間がかかる。どの物質をどう配合し、どのような触媒を使って、どのような条件で反応させるのか。もっと活性の高い触媒はないのか。これまでの化学合成の世界では、そういった原料選びや条件設定は、すべて技術者の経験や勘に基づいて行われていた。
さまざまな試行錯誤を経てよい反応が起こる物質が見つかっても、そこから最適な構造や組成を見いだすまで、少しずつ条件を変えて実験を繰り返し、評価・検証を行っていかねばならない。材料開発は、地道な作業の積み重ねなのだ。一つの機能性材料を開発するために10年かかることも珍しくはない。
これまで材料開発は日本の得意分野とされてきたが、他の国が追い上げてくる中、日本が国際競争力を維持し、強化していくには、いかにスピーディーに新しい機能性材料を開発し、確実に実用化につなげていけるかが勝負となる。しかも、常に社会から求められる材料を次々に創出し続けていかなくてはならない。社会の変化が激しい今、これまでのように開発に長い時間をかけているわけにはいかないのだ。
では、どうしたら短期間で新しい機能性材料を開発できるだろうか。現在、期待されているのが、材料開発の分野でインフォマティクス(情報科学)を活用する方法だ。すでに世界中で、計算科学や人工知能技術(AI技術)を用いた新しい材料開発手法の創出が試みられている。
もちろん日本も例外ではない。材料メーカーが個別に取り組んでいるだけではなく、2016年に立ち上がった「超先端材料超高速開発基盤技術プロジェクト(超超プロジェクト)」*1では、産総研と先端素材高速開発技術研究組合(ADMAT)が先頭に立って、3年間、開発手法と機能性材料の実際の開発に関して研究を進めてきた。ここで紹介するバイオエタノールからブタジエンを生成する世界最高の生産性をもつ触媒システムも、このプロジェクトが生んだ成果である。
バイオマスからタイヤ用の合成ゴムをつくる
自動車のタイヤに使われるゴムには天然ゴムと合成ゴムがあり、現在はほぼ半々の割合で使用されている。合成ゴムの原料は石油精製時の副産物であるブタジエンという物質で、合成ゴムをつくるには石油系原料を大量に使う必要がある。
「バイオ系原料から合成ゴムがつくれるようになれば、世界で生産されるタイヤの半分を、石油系原料を使わず、CO2も排出しないゴムで製造できることになります。そう考えると需要は大きい。私たちはバイオエタノールからブタジエンをつくることを開発のターゲットと決めました」
プロジェクトで実際に材料を試作するプロセス技術チームの取りまとめ役を担う、触媒化学融合研究センターの藤谷忠博は言う。藤谷はこれまで化学メーカーと共同でバイオエタノールからポリプロピレンを合成するなど、バイオマスから化学製品をつくる研究を行ってきた。今回、共同でこのテーマに取り組むのは、ADMATに参加している横浜ゴムだ。産総研と新しい機能性材料の超高速開発に取り組んでいるADMATは、18社から出向してきた研究員が集まる組織で、そこから新家雄をはじめ数名の横浜ゴムの研究者が加わった。
「横浜ゴムはタイヤメーカーで、原料開発は主要ビジネスではありませんが、タイヤの材料であるゴムの脱石油化は大きな課題であると考えてきました。原料メーカーの開発を待つだけでなく、まずユーザーである自分たちから動く必要があるのではないかと、これまでもゴムの原料を石油系原料からバイオマス原料へ転換する方法を模索してきたのです」(新家)
バイオマスから化学材料をつくる産総研の技術シーズと、バイオマス由来のゴム原料を開発したい横浜ゴムのニーズがうまく合致したかたちだ。
「自動車メーカーは今、CO2排出量削減のために車体の一部をバイオプラスチックからつくっています。タイヤもバイオマスからつくることができれば、さらに自動車関連のCO2排出量を削減することにつながります」(新家)
2016年、地球環境にも貢献する最先端の材料を開発することを目指して、ブタジエンをバイオエタノールから高効率に生成する触媒開発がスタートした。
触媒の候補物質をシミュレーションで短期間で発見
まず行うのはシミュレーションやデータ解析を駆使した物質探索だ。このプロセスは機能材料コンピュテーショナルデザイン研究センターの崔隆基が担当した。崔は量子化学の専門家で長く化学反応のシミュレーションの研究開発に携わっており、触媒候補となる活性物質を探すのにうってつけの人材だった。
「バイオエタノールからブタジエンをつくる触媒であれば、金属酸化物から候補物質が見つかると考えられました。そこで、さまざまな金属酸化物の原子構造や原子の振動エネルギーなど、あらかじめわかっている情報をシミュレーションソフトに入力し、それらのデータをもとにバイオエタノールとそれぞれの金属酸化物の一連の反応を計算、金属酸化物の遷移状態や表面の状態などをシミュレーションし、触媒の反応条件や分子構造を検討していきました」(崔)
触媒反応をシミュレーションしていくと、ディスプレイに反応活性の強弱を示すグラフが現れる。その形状から、触媒としての性能が高いのはどの物質なのかを判断していく。
「このような物質の活性の強弱についての情報は、化学反応の遷移状態の構造を知ることが必要ですが、この情報は実験では決して得られないもので、現在は計算で得られるようになったわけです」
■化学反応における物質のエネルギーの状態と触媒反応
物質が化学反応を起こすために、反応物質は一旦原子間の組み換えを起こしやすい状態(活性化状態)になる必要がある。触媒を用いると、活性化状態ではなく触媒と反応物質とで反応中間体を形成し、反応中間体を介して反応が進行する。この反応中間体の形成と分解がエネルギーの低い状態で進行するため、活性化エネルギーが下がり化学反応が進行しやすくなる。
慎重にシミュレーションを進めた結果、触媒としての性能が高そうな物質を複数見いだすことができた。その中で実際にどれを候補とするのかについては、過去の文献なども参照しながら当たりをつけ、成果の出そうないくつかの物質に絞り込んだ。
研究開発をスタートしてから有望な候補物質を見いだすまでの期間は約1年半。従来の方法に比べ、この段階で、すでに大幅な時間短縮をはかることができた。
自動触媒合成装置を使いハイスループットを実現
シミュレーションで導き出された候補物質を高効率の触媒にするためには、実際に装置を使って実験し、触媒ができたら特性を評価するというプロセスに移る。
「シミュレーションによって高い活性が出ると示されたからには、実験して活性が出なかったというわけにはいきません。最適なつくり方を確実に選んで、世界最高レベルの活性を出さなくてはと、かなりのプレッシャーがかかりました」と藤谷は笑う。
触媒の調製と評価のプロセスは、横浜ゴムの新家が担当した。ポリマーの研究者である新家は、ブタジエンからゴムをつくった経験はあるが、触媒を扱うのは初めてだった。
当初、プロジェクトの重点はシミュレーション手法の確立に置かれており、触媒作成は手作業で条件を変えながら行っていた。合成できる触媒は1日1〜2個、1カ月にせいぜい20個程度。遅々たる歩みだった。しかし2019年からは、新たに触媒自動合成装置が導入され、これが大いに力を発揮した。
多数の触媒を全自動で合成することができるハイスループット触媒合成装置。一度に数十サンプルの触媒を調製できる。
「ロボットが少しずつ条件を変えながら、液体でも固体でも自動計量し、混ぜ、乾燥させるまでの作業を連続的にしてくれるので、1日につくれる触媒は40〜50個、月に1000〜1500個にも上ります。これだけの触媒を試せるようになり、触媒探索の効率は飛躍的に上がりました」と、新家は喜ぶ。
ハイスループットを実現するための設備投資はそれだけではない。これまでは一度に8個の触媒反応を実験できる装置を使っていたが、2020年2月には一度に16個を反応・評価できる装置を導入する予定となっている。これにより、どのような条件で最も触媒反応が大きくなるかを、さらに短期間で見いだせるようになる。
実験のハイスループット化でAIに大量のデータを供給
ロボットを使った自動合成装置、反応装置を使った触媒探索は、この条件がよさそうだと事前に当たりをつけることなく、0.5 gからという小スケールで、次々と合成しては反応を試していくというものだ。いわば“手当たり次第”なのだが、ここではあえてこのような方法をとっている。そのねらいについて藤谷はこう説明する。
「人間が試せる数には限りがあるので、これまではどうしても、 “うまくいきそうなもの”を試していました。しかし、こんな常識的な形から出てくる結果は、どうしてもそれまでの延長上にあることが多くなります。それに対して、数をこなせるロボットであれば、人間が考えもしない組み合わせも次々に試し、次々に失敗することができます。そのような人間が考えもしない中から、これまでとはまったく違う触媒が見つかるのではないかと期待しているのです」
“手当たり次第”の理由はもう一つある。2018年からは人工知能(AI)による触媒の自動探索を進めているが、AIによる予測がよい結果になるかどうかは、学習させたデータの量と質にかかっているのだ。
「AIを使うには大量のデータが必要ですが、成功時のデータだけあってもよい結果を出せません。どのようなときに活性が出て、どのようなときに出なかったか、それぞれの反応は条件によってどう違ったかというデータもなくては、パターンをとらえて分析し、支配因子が何かを見つけることができないわけです。論文からは成功例しか見つからないので、失敗例を蓄積することにも意義があります」(崔)
そのようなプロセスでつくった触媒でよい反応が出たものについては、すぐに物理的・化学的に解析できるように、赤外分光計、 X線回折装置をはじめ、多数の評価・測定装置を用意している。これらの装置で分析した結果と活性の関係などのデータも、すべてシミュレーターやAIに送られる。計算で得られたデータと実際の実験データを組み合わせて評価することが、ここではとても重要となる。
分析装置の中で注目すべきは、DNP-NMRという化学物質の構造を超高感度で解析できる装置だ。まだ日本に2台しかないこの装置は、通常のNMRの6000倍もの高感度である。
「解析時間は1/6000に短縮され、これまで1週間かかっていた分析が1時間ですむほか、今まで見ることのできなかった構造や重合(ポリマーを合成する化学反応)のプロセスも観察できるようになりました。見えなかったものが見えるようになったことで、これから新しい展開も可能になるでしょう」(藤谷)
タイヤで使えるバイオゴムが完成
2019年、新しい触媒を用いてバイオエタノールからブタジエンを効率よくつくり、そのブタジエンを用いてゴムを合成することに成功した。しかし、新家はそれからが大変だったと言う。
「材料というのは、形ができたから“完成”ではありません。それまで使われてきた材料、この場合は従来の石油系の合成ゴムと比較し、同等以上の性能であると実証できなければ、できたとは言えないのです。そうでなければ実際の製品に使えないわけですから」
実験室でつくる触媒はせいぜい数gの量だが、実用化するには大量に合成した場合の評価をする必要がある。500 g、1 kgと大量に合成したときの活性性能はどうなのか、そのブタジエンからつくるゴムの性能は十分であるのかを確かめなくてはならなかった。
新家は当初、楽観視していたという。ところが、実験室のスケールでブタジエンからポリマーをつくると、なかなか分子が長くつながらないという課題が出てきた。タイヤに使うゴムには強度が求められるが、ブタジエンが長くつながらなければ十分な強度が出せない。原因の一つは生成したブタジエンに不純物が多量に含まれていたことだったが、よい精製方法がなかなか見つからなかった。
さらにブタジエンは沸点が-4℃と低く、すぐに気化してしまうため濃度調整が行いにくい。通常は有機溶剤と混ぜて液体状で冷蔵保存しているが、これを使うとき、濃度が薄いままだとポリマーの長さのコントロールが難しくなることがわかった。試行錯誤の末、適切な精製法と保存状態が見つかり、2019年7月、ついに石油由来の合成ゴムと同等の性能を持つバイオゴムが完成した。
開発期間はわずか3年。インフォマティクスの活用と高機能な装置の導入は、ハイスループットを実現するのに有効であることが実証できた。
「計算からプロセス開発までのすべてを産総研内でできた意義は大きいですね。どのメンバーとも密に話ができ、すぐにフィードバックができる。それがこのような超高速の開発につながったと思います」
藤谷は崔を見ながら、顔をほころばせた。
触媒開発のプラットホーム化を目指して
バイオエタノールからブタジエンを生成する技術の橋渡しは、すでに完了したといえる。これからは横浜ゴムが中心となって、ブタジエンの精製方法の改善などを行い、原料メーカーの参画も得ながら量産化技術の開発を進めていく。横浜ゴムは石油系と同等のコストに抑えるため、触媒のさらなる効率化やバイオエタノールの高効率な製造法の開発も進め、2030年をめどに実用化につなげていく予定だという。
産総研は今後、触媒開発およびマテリアル・インフォマティクスの基盤技術を確立し、触媒開発のプラットホームを構築していく計画だ。
「こんな触媒をつくりたいという企業のニーズに対し、計算で候補物質を見つけ、網羅的に合成して反応を調べ、AIにかけて、より活性の上がる構造を見つける。そのような仕組みを、プロジェクトの残り2年で確実なものとしていき、多くの企業の材料開発で使えるプラットホームを作り上げたいと思います」藤谷はそう結んだ。
*1: 超先端材料超高速開発基盤技術プロジェクト(超超プロジェクト)。国立研究開発法人新エネルギー・産業技術総合開発機構(NEDO)が革新的な材料開発手法の構築を目指して2016年に立ち上げた6年間のプロジェクトで、機能性材料の試作回数や開発期間を1/20に短縮させる基盤技術の開発を目指すもの。2018年までは主に有機系材料を対象に、構造や組成から材料の機能を推測するシミュレーション手法の開発を進め、その後、2021年まではAI技術を活用し、求める機能を実現する最適な構造や組成を導き出す材料探索手法の確立に取り組んでいる。[参照元に戻る]
触媒化学融合研究センター
総括研究主幹
藤谷 忠博
Fujitani Tadahiro
機能材料コンピュテーショナル
デザイン研究センター
多階層分子シミュレーション手法
開発チーム
主任研究員
崔 隆基
Choe Yoong-kee
先端素材高速開発技術研究組合
(ADMAT)
技術部
出向元:横浜ゴム株式会社
新家 雄
Shinke Yu
革新的な材料開発手法の構築を目指し、実際の成果物もできてきました!
先端素材高速開発技術研究組合(ADMAT)
- 〒305-8568 茨城県つくば市
東1-1-1つくば中央第5
産総研
材料・化学領域
触媒化学融合研究センター
産総研
材料・化学領域
機能材料コンピュテーショナル
デザイン研究センター