世界最高速クラスの砂型造形用3Dプリンターを開発、商品化
世界最高速クラスの砂型造形用3Dプリンターを開発、商品化
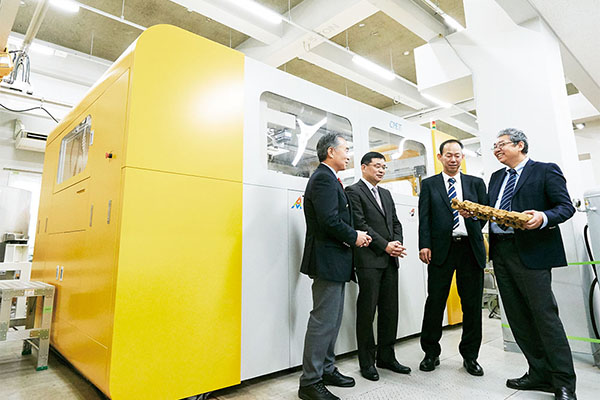
2019/01/31
世界最高速クラスの砂型造形用3Dプリンターを開発、商品化 毎時10万 cm3!で自動車部品の量産化にも対応
鋳造用砂型を世界最高レベルの速度で造形できる3Dプリンターが企業と産総研の連携によって完成、販売が始まった。従来の砂型造形用3Dプリンターの10倍の速度で大型の鋳型が作れるこの製品は、新開発の材料により後処理の簡便化も実現。自動車部品などの量産への道を拓くと期待されている。
大量生産できる造形速度と後処理の簡素化を目指して
岡根3Dプリンターというと、世間一般ではここ数年ででてきた新技術という認識かもしれません。でも実はこの技術自体は1980年代からあるもので、製品開発の試作手法のひとつとして用いられていました。
その状況が近年大きく変わったのは、3Dプリンターにより造形した、樹脂や金属部品の品質が向上して、従来の製法に比べて遜色ない特性が得られるようになってきたことによります。実際の部品を直接造形して使用することができるようになり、3Dプリンターは試作用ツールから、ものづくりの道具に変わってきたのです。しかし、これら樹脂や金属の部品を直接造形する3Dプリンターは、作製にかかる時間が長すぎるという課題があり、大量生産には向いていません。
そこで粉末にバインダー(砂を固めるための糊)をインクジェットする「バインダージェッティング」という3Dプリンター技術に目をつけました。鋳造の砂型の造形に利用されていたこの方法は、他の3Dプリンターに比べて高速造形が可能であることが知られています。この特徴を生かしてさらなる高速化を実現すれば、従来のプロセスと変わらない生産性で、3Dプリンターの特徴を生かしたより複雑な鋳造品を量産することができると考えたのです。
こうした状況の中、私たちは技術研究組合次世代3D積層造形技術総合開発機構(TRAFAM)という産学官連携プロジェクトで、鋳造に使う砂型を高速で造形する3Dプリンターを開発しました。
今回のプロジェクトでは、小岩井さんは実際にこの装置を使って砂型をつくる立場からのニーズのすり合わせを、大場さんにはこの装置・ハードづくりを、永井さんにはこの装置で使われる砂型の材料の開発を担当していただきました。まずは小岩井さんから、ユーザーとしてのご意見をいただけますか。
小岩井金属製の自動車部品などは鋳造でつくられますが、鋳造というのはまず砂で型をつくり、その砂型の中に溶かした金属を流し込んで固め、最後に型を壊して部品を取り出す方法です。型さえ作ってしまえば複雑なデザインの製品や小さな製品でも簡単に作ることができます。ただし、従来の砂型ではあまり細かい形はつくれないので、複雑な部品が必要な場合は複数のパーツに分けて砂型をつくり、それぞれで鋳造し、できたパーツを組み合わせて1つの部品にしていました。
しかし、3Dプリンターを使えば複雑な砂型でも一体造形でき、それによって1つの部品をそのまま鋳造できます。これは多数のパーツを組み立てる従来の方法より、完成後の部品自体の精度が上がりますし、部品を薄肉化できるので軽量化にもつながります。3Dプリンターの造形速度が上がって大量生産が可能になれば、現状より高品質の部品をつくれるようになるということです。
岡根私たちはそのような可能性に注目し、6年前から鋳造の砂型造形用3Dプリンターの開発を始めました。当時の造形速度は最も早い製品でも1時間あたり1万 cm3程 度でしたが、私たちは目標を10万 cm3/hの高速かつ大型の装置と定めました。これは、自動車用エンジンのシリンダーヘッドを鋳造するための中子(内側の砂型)100個を13時間で造形できる速度です。中子をひと月に3000個つくれる速度であれば、日本の自動車の生産量から逆算して、 1種類のシリンダーヘッドを作製するのに3Dプリンターを数台導入することで十分量産化に対応できると考えました。
小岩井3Dプリンターには熱溶解積層方式、光造形方式、パウダーベッド方式、インクジェット方式など、いくつかの種類があります。鋳物の試作・量産を行う当社は、2008年に海外のインクジェット方式3Dプリンターを日本で初めて導入したのですが、成形・固化後の後処理に、成形と同じだけ時間がかかり、機械の性能はよくても生産性の面では満足できませんでした。
今回の開発にあたっては、ひとつの製品を生産するサイクルタイムを考え、造形速度だけではなく造形物の取り出し時間短縮、熱処理の省略、材料のリサイクルなどの後処理の問題も解決してほしいと最初からお願いしました。私たちの困りごとがすべて解決できれば、世界最高峰の3Dプリンターができると確信していました。
岡根コイワイさんが2008年にインクジェット方式の3Dプリンターを導入し、経済産業省の事業支援を受けたことが、後にこのプロジェクトにつながったのですよね。
小岩井はい、当社(コイワイ)はインクジェット3Dプリンター導入に当たって産総研に技術的な支援をお願いし、岡根さんにアドバイザーとして加わっていただきました。その中で「どうして国産装置がないのだろう」という話になり、事業支援終了後、再度経済産業省の事業支援を得て、大型の砂型用量産3Dプリンターの開発を始めました。
岡根性能も信頼性も高いものをつくることで量産機のニーズは広がっていくと、私も実感するようになりました。そこで小岩井さん、早稲田大学の吉田先生とも相談し、2013年に「超精密3次元造形技術開発プロジェクト」としてプロジェクトをスタートさせたわけです。それが技術研究組合次世代3D積層造形技術総合開発機構(TRAFAM)の設立に発展し、材料と装置で力を合わせて世界最高を目指すチームをつくりました。
小岩井砂型造形用3Dプリンターとしては、樹脂をコーティングした砂をレーザー加熱して造形するタイプが歴史的に先行していました。先に述べた経済産業省支援事業に先立ち2007年にその国内導入機第1号を当社が導入しました。非常に便利なので、すぐに2台目を導入して、そのレーザータイプ2台と、海外のインクジェット方式3台の計5台を稼働させました。しかし、海外製はトラブルが多くよく止まりますし、副資材も高額で、量産用に何台も導入するのはハードルが高い。そう岡根さんに話していて、「それならインクジェット方式で世界最高スペックの装置を国産でつくりたいですね」という話になり、プロジェクトが立ち上がったのです。
岡根長く鋳造の研究をしてきた私がプロジェクトリーダーを務め、ニーズや社会背景など全体を見ながら、最終的な目標の実現に向けてルートや方向性を示していきました。装置メーカーやユーザーと議論しながら開発を進めていく体制をつくり、必要な装置は産総研に集中的に設置し、バインダーのテストなどができる体制を整えました。
レーザータイプは砂をレーザーで加熱して砂型として固めた後、熱を逃がして工程を終えるのですが、セラミックス製の砂は保温性が高く、放熱しにくいという問題がありました。余熱がまわり、本来固めたくないところまで固まってしまい、型の精密度が下がるのです。将来的には熱を使わない方式が伸びるだろうと、今回はインクジェット方式を最終目標にしました。
小岩井2タイプとも稼働させていた当社は、両方のプロセスの長所も欠点もわかっており、それぞれの欠点を補うかたちで開発コンセプトを決定しました。また、当社では各自動車メーカーの部品の試作だけでも月平均で60点ほどを新規に立ち上げます。この新規開発品では従来にない形状を求められるため、これまでの3Dプリンターでは時間がかかりすぎました。だからこそ世界最高スペックのマシンがほしい、生産性も操作性も向上させてほしいとお願いしました。
大場当社(シーメット)がプロジェクトに参加した時点では、すでに装置のスペックは決まっており、「大場さん、これをつくってください」と(笑)。しかし当社は光造形の3Dプリンターメーカーで、これまで砂型をつくったことも、インクジェットの制御もしたことがありません。材料の砂は1.8 m×1 mの面にきれいに敷き詰めなくてはならないのですが、その技術もありませんでした。
小岩井それでもシーメットさんに入っていただいたのは、ユーザーとしてそれがベストだと考えたからです。ユーザーにとって装置は、購入して終わりではなく、アフターサポートの面で信頼できることがとても重要です。海外製の場合、部品が壊れても「今から空輸するので1カ月待ってください」などと平気で言われますが、自動車関連部品を量産していれば、1秒だって装置を止められません。国内で販売実績のあるシーメットさんはサポート体制も確立しており、最も信頼できると考えました。
大場開発においてハードルが高かったのは、インクジェットヘッドをどう制御していくのか、それから10万 cm3/hという速度をどう実現するのかでした。まずは他社の装置を分析するところから始めましたが、いきなり10万 cm3/hは無理なので、まずは見よう見まねで1万 cm3/hの装置を開発、製品化もしてユーザーからのフィードバックを得ながら、翌年には5万 cm3/hの装置を開発しました。1年で設計から製造まですることを毎年繰り返し、その中で今回の装置ができたわけです。
国産インクジェット方式3Dプリンターで造形した砂型
(左)インペラ(中央)シリンダーヘッド(右)油圧バルブ
高速化を実現するドライな砂づくりに挑戦
小岩井今回の装置でつくった砂型は、触っても手に砂がつきません。材料の砂が乾燥しているからで、これだとできた型の剥離性がよく、困っていた後処理が短時間ですむのも大きな特徴の一つです。海外製の装置は、砂が湿っているので、造形後、できた型から余分な砂を落とすのが大変でした。型は砂の中に埋まっていて、これを取り出すには、化石の発掘作業のようにおそるおそる刷毛で砂を落としていかなくてはなりません。上から刷毛が入らない箇所には、型を壊さないようそっと回転させ、どこに刷毛を入れるか考えながら作業していく。複雑な形でも一体造形できることが3Dプリンターのメリットですが、そうした複雑な形状のものほど後処理に手間がかかっていました。
永井当社(群栄化学工業)は材料の砂だけではなく、プロセス全体の開発にかかわっています。なぜ砂同士が接着するのかがわかっていないと、3Dプリンターは成り立たないからです。
そもそも3Dプリンターの歴史は長く、しかもそれらは海外勢の特許でがっちり固められており、私たちは海外の特許に抵触せずにそれを上回る方法を考えなければいけない。当時、そのような技術は国内にはなく、この点で非常に苦労しました。
また、高速化には流動性の高い乾いた砂の方が濡れた砂より適しているわけですが、砂をドライにするというのは簡単なことではありません。というのは、接着させるための化学反応を起こすには、加熱するか触媒を使うかしますが、今回は加熱しない方式を目指していたので触媒を使わなくてはなりません。一般に触媒は液体です。しかしドライな砂にするには液体の触媒は使えませんし、触媒として機能する材料も限られてしまいます。触媒を固体にする方法も、固体の状態で安定させて砂に留め置く方法も見つけなければなりません。これらの課題をすべてクリアしないとうまくいかない、厳しい条件下での開発でした。
岡根触媒とバインダー、2つの液体が合わさると砂が固まるわけです。海外製の3Dプリンターで採用されている従来の方式は、砂に硬化剤といわれる液体の触媒を入れて練っているのでウェットになっています。触媒が含まれたウェットな砂を一面に敷き詰め、その後、固めたいところにだけインクジェットでバインダーを吐出し、触媒とバインダーが混ざったところだけが固まるという仕組みです。こうした方式と比べたドライ式の利点として、ウェットだと砂を敷くのに抵抗が大きいのですが、ドライは流動性が高いのでより速く敷き詰められるというとことがあります。また、ドライは液体が含まれない分、密度が上がります。高密度の方が砂型になったときの強度も上がり、刷毛で“発掘”するときに、より取り出しやすくなるメリットがあるわけです。
永井さらに、ウェットの方は触媒が揮発して性質が変わるので、固まらなかった砂についても、新しい砂と混ぜるなどの処理をしないと再利用できませんが、ドライだと余った砂をそのまま再利用できます。それも優れた特性ですね。
材料メーカーと装置メーカーががっちり組んだから完成できた
大場当社が特に悩まされたのは、高速できれいに砂を敷き詰める方法を開発することと、バインダーとインクジェットのプリンターヘッドの相性の問題でした。この相性というのは、ヘッドはデリケートな金属部品なので、酸やアルカリのバインダーを入れると腐食して壊れてしまうのです。群栄化学工業さんには、インクジェットで吐出でき、かつヘッドに影響がでないバインダーを開発していただく必要があり、私たちと永井さんとの格闘が始まりました。
永井今、大場さんがおっしゃったように、金属製のプリンターヘッドに強アルカリや強酸のバインダーを入れると、腐食してすぐに使えなくなるので、バインダーは中性である必要があります。なおかつ表面張力や粘性も低くないと、インクジェットから吹き出せません。それらの条件を満たした上で、触媒と混ざったときに化学反応を起こすことが求められました。難問ばかりが積み重なっていましたね。
大場バインダーの粘性などが変われば、インクジェットの吐出条件も変わるので、新しいバインダーが試作されるたびに、私たちは最適なパラメータを探してヘッドを調整する必要がありました。開発中は非常に密なやりとりが続きました。
永井しかも砂は天然物なので品質は一定ではありません。品質のばらつきをどこまで私たちがカバーするかというような、一見目立たない部分にもハードルがありました。
岡根鋳造の場合、3Dプリンターでつくった砂型が完成品ではありません。砂型はあくまで製品をつくるプロセスに必要なもので、そこに金属を流し込んでつくる部品が実際の製品となります。部品の材料となる金属も、アルミ合金、銅合金、鉄などさまざまで、鋳鉄や鋳鋼の場合は溶かす温度は非常に高温になりますし、性質も多様です。それらに幅広く適応できる砂型材料が必要だったのです。つまり、装置をつくるだけではなく、材料開発も非常に重要で、材料メーカーと装置メーカーががっちり組まなければ、とても完成はできなかったのです。TRAFAMという場を用意し、密にやりとりする中で、全体の軌道修正もかけていく。それを5年間繰り返し、この3Dプリンターが完成したのです。
3Dプリンターで砂型ができるまで
環境に左右されないタフな装置を目指して
小岩井この3Dプリンターでつくった砂型でできた金属部品の品質をエンドユーザーに評価していただけてこそ、装置の意味があります。ですから早くよい装置をつくり、海外勢に追いつけ追い越せと取り組んできました。今回できた装置については、ユーザーとしては生産性、砂型の寸法精度や強度、ハンドリングには満足しています。最高のスペックのものができて一安心ですが、これからはさらによいものをつくる一方、価格面の課題を解決していただきたいですね。
岡根これからさまざまな条件や環境で使っていただき、ユーザーの意見をフィードバックさせながら全体的な信頼性や性能を高めていく段階に入ります。故障などで作業が中断することなく、環境が多少変わっても同じ性能を出せるタフなシステムにすることを目指していきます。
大場当社は鋳造のことも砂型のことも知らないところからのスタートでしたが、岡根さんが説明やフォローをうまくしてくださったことで、開発を進めることができました。このメンバーをよくまとめてくださり、感謝しています。産総研の力がなければプロジェクトは成功しなかったでしょう。
永井私は鋳造の型をつくる砂と樹脂の研究を20年以上してきたが、これまでは鋳物メーカー以外の方と出会う機会は多くありませんでした。今回はこのような出会いの場を提供していただけて、視野を広げることができました。今後は使用時の制約が少なく、多種の金属に対応できる、汎用性のある材料の開発が必要だと思っています。
小岩井鋳物について、装置開発から材料に至るまでの幅広い専門知識をお持ちの方は国内ではあまりいませんが、その点において私は産総研に絶対的な信頼をおいています。岡根さんとは10年のお付き合いになりますが、「困ったときの岡根さん」と思っています。このような個性豊かなメンバーをまとめるのは産総研だからできたこと。これからもぜひお付き合いしたいと思っています。
岡根現在の鋳造業には手作業の部分がまだかなり残っています。それも大事にしていく一方、オンリーワンの技術としてまとめ上げていくには、デジタルデータ信号をアナログ出力する3Dプリンターを使いこなし、手作業の勘所をいかに数値化、デジタル化していくかが肝となります。この装置を起点に、そのような「デジタルものづくり」の観点で取り組んでいける仲間の輪を広げていきたいですね。
小岩井鋳造には2000年の歴史がありますが、3Dプリンターを用いたプロセスはデジタルネイティブの世代にも扱いやすく、若手が即戦力になれる技術でもあります。3Dプリンターをキーワードに鋳造の面白さに気づいてもらえることは、技術の伝承の面でも重要だと思っています。ぜひ、コスト面・性能面のバージョンアップを続けていきましょう。
エレクトロニクス・製造領域
製造技術研究部門
総括研究主幹
岡根 利光
Okane Toshimitsu
株式会社コイワイ
専務取締役
小岩井 修二
Koiwai Shuji
シーメット株式会社
取締役 開発部部長
大場 好一
Ooba Yoshikazu
群栄化学工業株式会社
開発本部
商品技術部長
永井 康弘
Nagai Yasuhiro
製造現場で壁に突き当たって困っていることがあれば何でもご相談ください! …お気軽にお問い合わせを
産総研
エレクトロニクス・製造領域
製造技術研究部門
技術研究組合次世代3D積層造形技術総合開発機構(TRAFAM)