独立行政法人 産業技術総合研究所【理事長 野間口 有】(以下「産総研」という)ナノシステム研究部門【研究部門長 山口 智彦】グリーンテクノロジー研究グループ 川本 徹 研究グループ長は、株式会社東和製作所【代表取締役 菅谷 篤廣】(以下「東和製作所」という)、関東化学株式会社【代表取締役社長 野澤 学】(以下「関東化学」という)と共同で、量産が容易な印刷技術を用いてプルシアンブルー型錯体ナノ粒子を使用したエレクトロクロミック色変化素子を製造する技術を開発した。
今回開発した量産が容易な印刷法は、プルシアンブルー型錯体ナノ粒子インクをスプレー印刷するものである。また素子を完成させるために必要となるゲル電解質や封止材は、それぞれ別の基板にスクリーン印刷法を用いて塗布した後、基板を貼りあわせて成膜・パターニングを行った。これらの手法により、素子の量産性を高めるともに、パターニングの簡便化や素子形状の柔軟性なども実現した。また、1,000個以上の10 cm角の色変化素子を装備するオブジェを作製した。
この研究成果は、平成24年11月21日~11月26日に東京都渋谷区の渋谷ヒカリエCreative Lounge MOVで開催される「Prussian Blue Device」(東和製作所主催、産総研共催)において発表される。
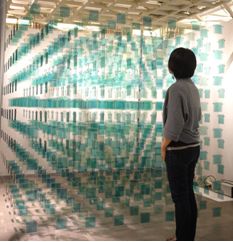 |
今回の印刷法で製造した1,000個の色変化素子を使用したオブジェ |
近年、物体の色を変える技術が注目を集め、さまざまな場所で使用されつつある。例えば、電子ペーパーでは、発光の色を変えるのではなく、物体自体の色を変えて表示しているものがある。発光体がないので、表示を継続させるだけではエネルギーは消費されない。また、調光ガラスという、窓ガラスの色を変える技術も実用化が進み、例えば航空機の窓ガラスでは既に実用化されている。調光ガラスは、入射光を制御することで、空調を効率化できる点が大きな利点の一つとされ、省エネルギーの観点からも注目されている。ほかにも温湿度などの外部状況により色が変わる材料を使用したセンサーや、鏡の反射率を変えた防眩ミラーなども実用化されている。
物体の色を変える技術の一つに、エレクトロクロミック技術がある。材料を電気化学的に酸化もしくは還元して色を変化させる技術で、色変化の度合いが大きいこと、電気による色変化なので制御がしやすいことなどが利点である。原理的にはコストも安いと考えられているが、工程の複雑さや歩留まりの悪さなどの問題があり、実際に大面積の素子を安価で提供できているわけではない。コストの問題を解決する一つの方法として、各部材を塗布や印刷によって成膜し、素子化する塗布法や印刷法が期待されている。大気中で操作できることから、低コスト化が期待できる。また、印刷法はパターニングを施すことなどが容易であることから、多機能な素子の開発も可能とみられており、塗布法や印刷法によるエレクトロクロミック素子の製造技術の確立が期待されている。
エレクトロクロミック材料の一つであるプルシアンブルーは、1704年に初めて合成された長い歴史を持つ顔料である一方、エレクトロクロミック材料としても、高い耐久性などが知られていた。産総研は、このプルシアンブルーやその類似体をナノ粒子化し、溶媒に分散させてインク化する技術を開発し、それを用いて透過型エレクトロクロミック素子である調光ガラスを開発している(2007年8月8日 産総研プレス発表)。また、素子製造の大半を低コストの印刷・塗布で行うため、ゲル状の電解質を用いた素子を開発した。白色ゲル電解質を用いることで電子ペーパーに利用可能な反射型エレクトロクロミック素子も作製できる(2010年3月26日 産総研プレス発表)。一方、これらの素子の導電性基板については、印刷メッシュ状金属配線の利用も進めている(2011年2月15日 産総研プレス発表)。
今回、ナノ粒子インクの量産化に取り組むとともに、素子の量産性を向上させることを目指して、ナノ粒子インクについてはスプレー塗布、ゲル電解質と封止材についてはスクリーン印刷による素子製造技術の開発を行った。
なお、この研究開発の一部は平成22年度戦略的基盤技術高度化支援事業「真空封止技術を利用したモジュール連動型電子ペーパーの製造」の支援を受けて行った。
これまでは、エレクトロクロミックナノ粒子インクはスピンコート法で塗布し、パターニングが必要な際には、レジスト法を用いてきた。これらの方法は、ロールツーロール法などの量産性の高い連続製造にするのが難しいことや、パターニングの際の工程が多くなってしまうことなどの課題があった。また、ゲル電解質と封止材の塗布には、主としてディスペンサー塗布を用いてきたが、塗布速度の向上が難しいことやゲル電解質の種類によっては均一な塗布が難しいことが課題であった。
図1に今回開発したエレクトロクロミック素子の量産対応印刷法による製造工程と最終的な素子構造の概要を示す。エレクトロクロミック素子は、ナノ粒子を塗布した透明導電膜基板2枚の間にKTFSI、炭酸プロピレン、PMMAからなるゲル電解質を挟み、封止材で封止してある。
ナノ粒子インクの塗布には、ナノ粒子インクをスプレーして塗布する方法を用いた。全面に塗布する場合には、スプレーで霧状にしたインクを基板に付着させる。超音波の利用などにより、液滴をさらに微小にして、より平滑に塗布することもできる。また、穴の開いたマスクで基板を覆ってインクをスプレーすれば、インクはマスクの穴が開いた部分だけに付着し、パターニングを施すことが可能となる。マスクを変えて、異なったインクを重ねてスプレーすることで、一枚の基板上に多種類のインクを印刷することもできる。さらに、スピンコート法のように基板を高速回転させる必要がないため、基板の形状の自由度が高く、複雑な形状の基板に塗布することもできる。図2(a)にスプレー印刷法でナノ粒子インクを透明導電性フィルムに塗布し作製した、V字型のエレクトロクロミック素子を示す。これまでのスピンコート成膜では、このような形状の素子作製は困難であった。
図2(b)に、実際にプルシアンブルーナノ粒子インクを塗布した透明導電膜基板(ITO基板)の電子顕微鏡写真を示す。プルシアンブルーナノ粒子の一次粒径を10~20 nm程度、二次粒径も100 nm以下とすることで、スプレーノズルでの詰まりもほとんどなく、連続的なスプレー印刷が可能となった。ナノ粒子を塗布した基板を0.1 mol/LのKTFSI/炭酸プロピレン電解液に浸し、基板の電位を変化させた際の色変化挙動を調べたところ、基板の電位を+0.4 Vから-0.4 Vに変化させると青色から無色透明に変わり、電圧を逆に変化させると青色に戻った。また、スプレー塗布膜は従来のスピンコート法よる塗布膜と同様の色変化を示すが、色変化の速度が8~12 %高速化していた。これは、スプレー塗布膜の方がナノ粒子膜内の空隙が大きく、色変化に必要なカリウムイオンのナノ粒子と電解液の間の移動速度が上がったためと推測される。
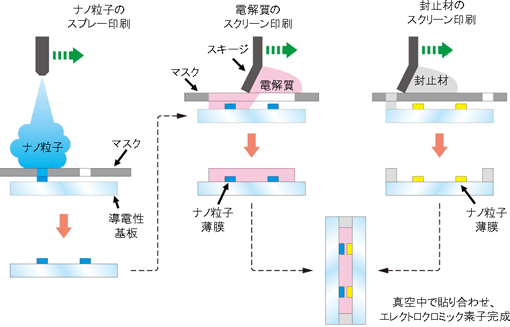 |
図1 量産対応印刷法によるエレクトロクロミック素子の製造工程 |
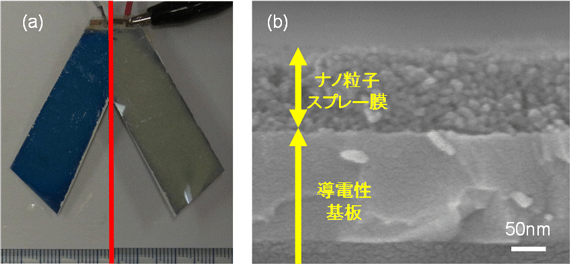 |
図2 スプレー印刷法により塗布されたプルシアンブルーナノ粒子薄膜
(a) スプレー膜で作製したV字型のフィルム状色変化素子。左側:青色状態、右側:消色状態。
(b) 塗布基板の断面電子顕微鏡写真。 |
素子を完成させるために必要となるゲル電解質や封止材については、材料の粘度が高いため、スプレー印刷ではなく高粘度材料の塗布に適したスクリーン印刷を使用した。スクリーン印刷は、図1のように、版を基板に押し当て、その上に滴下した材料をスキージと呼ばれる器具で押しこみ印刷する方法である。版にあるメッシュ状の穴の部分だけ材料が通過して基板に塗布される。ゲル電解質と封止材を同一基板に膜厚を制御して塗布することが難しいことから、スクリーン印刷による素子の作製は困難だと考えられていたが、今回、ゲル電解質と封止材をそれぞれ別の基板に塗布してから、それらを貼りあわせる工程を開発し、ゲル電解質と封止材のどちらもスクリーン印刷で製造できるようにした。図3に今回開発した印刷法により作製した青-黄の色変化を示すエレクトロクロミック素子と、その光学特性を示す。色変化挙動はスピンコート法とディスペンサー塗布を使用した従来の印刷法で作製したものと同様である素子が作製できた。
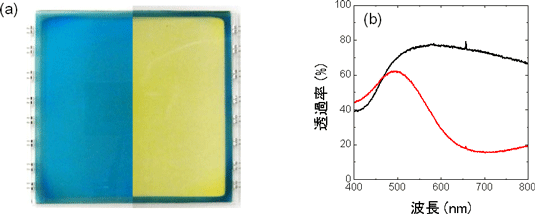 |
図3 量産対応印刷法により作製したエレクトロクロミック素子とその光学特性
(a)量産対応印刷法により作製したエレクトロクロミック素子。
左側、右側はそれぞれ0 V、1.2 Vの電圧をかけた時の素子の色。
(b) 電圧をかけた素子の可視光透過スペクトル。
赤線、黒線はそれぞれ0 V、1.2 Vの電圧をかけた時のスペクトルを示す。 |
産総研で開発したこれらの技術の量産性を実証するため、色変化するオブジェを制作した(図4)。このオブジェは、10 cm角のエレクトロクロミック素子 1,000個からなり、すべての素子の色を変化させることができる。なお、使用したエレクトロクロミック素子は、関東化学が製造した量産化ナノ粒子インクを用い、東和製作所が開発したナノ粒子塗布用スプレー装置を用いて製造した。
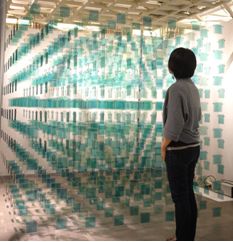 |
図4 今回の印刷法で開発した1,000個の色変化素子を用いたオブジェ |
今後は素子の量産化検討などをさらに進め、数年以内の実用化を目指すとともに、他の色のプルシアンブルー型錯体や、フィルムなど、別種の基板についてもこの技術を適用した量産手法を開発し、用途の多様化を図る。