半導体製造の常識を変える!
半導体製造の常識を変える!
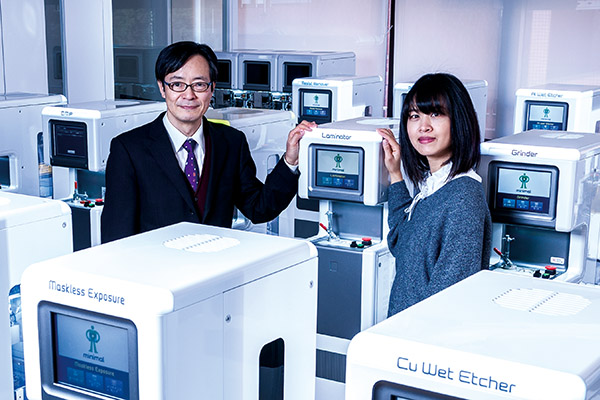
2017/03/31
半導体製造の常識を変える! クリーンルームなしで1個からのデバイス製造も可能にする「ミニマルファブ」
❶ デバイス製造の概念を変えうる新たな半導体製造装置。
❷ クリーンルームなしで、1個からデバイスを製造できる。
❸ AIやIoTの研究で求められる少量多品種生産の実現も狙う。
幅30 cm、奥行45 cm、高さ144 cm。小柄な女性よりも小さなこの装置は、半導体の製造装置「ミニマルファブ」だ。超小型で、たった1個からのデバイス製造がクリーンルームなしでできる“常識外”のこの装置は、2016年4月から横河ソリューションサービス株式会社が商用サービスを開始。これまでの半導体製造過程を一変させ、日本の半導体産業復活の切り札になりうると、大きな期待と注目を集めている。
その革新性に衝撃を受け、参画を即決
おしゃれなレンガ調の壁の室内に、約10機のミニマル装置が並ぶ。ここは2016年4月に、東京都武蔵野市の横河ソリューションサービス(以下、YJP)本社構内にオープンした「横河ミニマルアプリケーションラボ」だ。ここでは実際にミニマルファブ(ファブとは半導体の製造工場のこと)を見たり、触ったり、サンプルを試作したりできる。
横河ミニマルアプリケーションラボ(東京都武蔵野市)
筐体とロゴのデザインは「スバル インプレッサWRX」のデザイン開発を手がけた手島彰氏による。塗装も自動車にも使われるパールホワイトを採用。
個々のミニマル装置はフォトレジストの塗布、露光、エッチングなど、それぞれ異なる機能をもつ。対象とする半導体デバイスの製造に必要な機能をもつミニマル装置を組み合わせれば、そのデバイスを製造できる。つまりこの約80 m2に満たないラボが、実際の半導体製造工場そのものとも言えるのだ。
YJPで半導体サービスセンター長を務める西村一知氏がミニマルファブを初めて見たのは、2011年12月のセミコンジャパンの会場だった。産総研が主導して研究開発を進めていた、ハーフインチウエハを使うクリーンルーム不要の小さな装置群は、巨大な半導体製造装置が並ぶ展示会場の中で異彩を放っていた。
「強烈なインパクトでした。このビジネスに参画したいと、その場で思いました」
過去にも半導体製造装置の小型化は多くの企業が試みてきたが、いずれも中途半端な形で終息してしまっていた。それを知っていた西村氏は、このビジネスにリスクがあることもよくわかっていた。しかし、
「その革新性の前に、リスクは吹き飛びました。将来性を直観したのです」と言う。
当時、ミニマルファブの研究開発を進めていた産総研コンソーシアム「ファブシステム研究会」には、100社ほどが参加していた(現在は約140社)。西村氏はその場で入会申込書を提出。装置の導入支援から運用・保守まで、製造以外のソリューションサービスを一貫して提供できる企業は少なく、大いに歓迎されたという。
YJPの持ち味であるソリューションサービスを提供するには、ミニマルファブについて熟知している必要がある。そこで西村氏は、ミニマルファブシステム開発の中心人物である産総研の原史朗のもとに、4人の半導体製造のプロを送り込んだ。そして2012年から4年間、この4人は産総研とともに、ミニマルファブの実用化に向けて奔走する。
多品種少量のニーズに低コストで応える装置を
このミニマルファブが構想されたのは2007年のこと、産総研の原によって提案された。
当時、半導体デバイスの製造は巨大な工場(メガファブ)で大量に安く作る方式が主流だった。しかし、メガファブの建設には5000億円もの費用がかり、そのような巨額投資ができるのは、世界でもごく一部の企業に限られていた。DRAMビジネスで競争に敗れた日本企業は、その後の半導体市場でも劣勢に立たされ、いくつかの企業は市場から撤退し、残る企業も苦戦を強いられていた。
「本当に大量生産しなくては勝てないのだろうか?本当に多品種少量の需要はないのだろうか?」と原は考えた。
その答えを見つけるため、約5年間、研究から離れて徹底的に市場を調査、1000人を超える関係者に会い、本音を聞いて回った。こうして自らの眼で半導体デバイス市場を見直すとともに、国内外の市場情報に注意を払い、半導体の実需動向を見定めた原は、一つの結論にたどり着いた。「多品種少量需要は、決して少なくはない」ということである。
「例えば、パソコンや家電、カーエレクトロニクスの市場は大きいと言われますが、実際は多くの品種で細分化されているので、個々の機種の市場自体は大きくありません。全体で1000億円の市場でも、1000種の商品で構成されていれば、1種類では1億円の市場でしかないのです。大量生産の対象と思われていた市場は、実は少量生産デバイス市場を束ねたものだったのです」
ここから原は、低コストで多品種少量生産を実現できれば、半導体産業の世界を変えられると考えた。
この考えを後押しする理由がもう一つあった。半導体は将来においても有望なデバイスである。しかし、膨大な投資を必要とする。これではよい技術やアイデアがあってもリスクを恐れてなかなか一歩を踏み出しにくい。しかし、少額投資で少量を生産し、ビジネスが成り立つとすればどうだろうか?その答えが、1個からデバイスをつくれる「ミニマルファブ」だった。
「大量生産から多品種少量生産に切り替えれば、対象の市場は小さくても少ない投資で採算がとれます。投資が少なければ同時にリスクも小さくなりますから、ユニークな新しいデバイスを数多く市場に出しやすくなるでしょう」
目指すは標準化 サイズもユーザーインターフェースもすべて統一
こうして生まれた「ミニマルファブ」は、まったく新しい半導体製造装置だ。幅30 cm、高さ144 cmという、半導体製造装置の既存概念を覆す小ささも、クリーンルームがいらないのも“常識外”である。必要な投資額は従来のメガファブの1/1000(約5億円)の規模に抑えられる。50種類もの装置が一つの部屋に入り、装置の並べ替えも自由だ。省電力で有害な排気もない。
このミニマルファブ構想に多くの企業が賛同し、2010年「ファブシステム研究会」が発足。その中の約30社の中小企業が得意な技術をもちより、ミニマル装置群のプロトタイプの開発に取り組んだ。しかし、単にそれぞれの装置を小型化すればよいというわけではない。システムとしての統一性も必要だ。原は、装置群のサイズをすべてそろえることにこだわった。
しかし、サイズの統一は困難を極めた。「この機能を求めるならどうしても部品がはみ出てしまう」と諦めの声が出ても、原は、例外を認めなかった。まるで箱庭をつくるように、限られたスペースに必要な機能をもつ部品を配置する技術は、海外に対抗できる日本企業の強みであると原は考えていた。
さらに筐体デザイン、ユーザーインターフェースも統一した。エラー表示の出方も共通にし、使いやすさを工夫した。
「目指したのは標準化です。サイズが同じだからこそ、装置を自由に配置できます。また中小企業にとって、筐体デザインやディスプレイの表示設計は、普通は相当な負担になりますが、標準化すれば装置内部の開発だけに注力できます。筐体自体、標準化されていれば低コストで製造でき、あらゆる効率が上がるのです(原)」
優秀でハイセンスな人材が実現させた実用化への道
2011年、原の研究グループにタイ出身のクンプアン ソマワンが加わった。国内外のいくつもの機関で研究に携わってきたソマワンは、ミニマルファブ実用化の強力な推進力となった。
ソマワンの着任時、目途がついていた装置は露光用の3種だけだったが、いずれも実用化にはほど遠い段階だった。ソマワンには、カンチレバー型デバイスを実際に製造するという課題が与えられた。当時まだ、ミニマルファブの実効性に懐疑的な空気もあり、まずは本当にデバイスがつくれることを証明するため、装置を改良する必要があった。そんな中ソマワンが、1度もやり直しせずミニマルファブでカンチレバー型デバイスをつくりあげたのは、始めてからわずか1年目のことだった。5年でできればと思っていた原は舌を巻いた。
ソマワンが手にしているのは、超小型局所クリーン化搬送システム「ミニマルシャトル」。紫外線をカットする赤い容器にウエハを格納して、ミニマル装置間を移動させる。シャトルの中だけをクリーンに保てば、クリーンルームは不要。防塵服もなく普段着で入室できる。
「彼女には、高い集中力や実験センス、強い研究者マインドがあります。ミニマル装置は彼女のおかげでできたようなものです(原)」
ソマワンは装置の開発にも力を発揮した。
「まず、構造を把握するため、既存の試作品をすべて分解しました。それにより、例えば現像装置では、バルブを小型の注射器の筒(シリンジ)に置き換えればスペースを節約できるなど、いくつもの改善点を洗い出しました」
改善する中で、ソマワンは独自の技術も開発した。わずか0.5 ccの現像液をウエハの表面全体に行きわたらせて現像する方法である。まずシリンジから滴下した1滴を表面に広げるため、ウエハを回転させる。ウエハが小さい分、強い表面張力が働き、4 mmも盛り上がっても液がこぼれないという現象が起こる。この性質に着目し、こぼれずウエハ上に留まる0.5 ccほどの液だけで現像してしまう技術を開発。現像液を大幅に節約でき、装置をミニマルファブの規定サイズ内に収めることに成功したのだ。
産総研ナノエレクトロニクス研究部門ミニマルシステムグループラボ内(茨城県つくば市)
人が装置の前に並んで立つことを前提に、圧迫感を与えない最小幅。小柄な人でもタッチパネル画面を操作しやすい高さ。原が考え抜いた新しい生産スタイルと美意識が、あらゆる部分に反映されている。
YJPが事業化をスタート!大きかった海外からの反響
装置メーカーがつくった試作品を、原やソマワンらが徹底して磨き上げていった。YJPから来ていた4人もそれらすべてのプロセス開発を一緒に行い、ミニマルファブがシステムとして完成し、全機種のサービスに対応できる体制が整った。
こうしてYJPは、ミニマルファブのサービス事業の推進を決定し、導入前のコンサルティングから販売、設置環境の構築、立ち上げ、導入後の運用・保守まで、すべてをワンストップで行うサービスの提供を始めた。その基幹となるのが「横河ミニマルアプリケーションラボ」である。現在導入済みの装置は15機種(2017年3月現在)だが、それでも工程の少ないMEMSやトランジスタなら製造できる。
ラボの設置はYJPの山本順二取締役が決断した。山本氏は製品のライフサイクルの短期化や半導体の使用形態の多様化から、多品種少量生産が進むと考えていた。IoT時代には多種多様な半導体が必要になる。山本氏は、ミニマルファブは時代のニーズに対応できる、これがあれば大量生産とは異なる、付加価値の高い多品種少量市場が生まれる、と感じたという。
「クリーンルーム不要でハーフインチウエハを、というコンセプトも素晴らしいと思いました。それ以上に、日本人の高い技術力を生かせる分野への投資は、日本の産業を支えていくという意義もあると考えたのです。その後、原さんにお会いして話を聞き、徹底した市場調査から練られたコンセプトであることを知り、さらに、原さんの熱意に触れて成功を確信しました」
ラボのオープン以来、見学者は引きも切らず、すでに数社から受注もある。ラボの責任者である西村氏は語る。
「これからのミニマルファブの主力ユーザーは半導体のプロではないでしょう。設置環境や法規制もわからない、場合によっては薬液の購入先もわからない。お客様から思いがけない質問が出るたびにサポートの重要性を実感し、私たちの方向性は間違っていないと実感しています」
うれしい誤算は、国内以上に海外からの反響が大きいことだ。国内企業が実績のない装置への投資に二の足を踏むのに対し、海外の政府や有力大学は、研究開発設備として最適で、かつ産業構造を変える可能性をもつミニマルファブの導入に積極的だという。
現在ミニマルファブシステムの一部は、歩留まりなどを引き続き改良中で、YJPではそれに代わるものとして、同社がもつ既存のメガファブと組み合わせたプロセスサービスを提供している。まずはユーザーに完成したプロセスから使ってもらい、ミニマルファブの特徴と利点を実体験してもらうことが目的だが、最終ゴールはもちろんすべての工程をミニマルファブに置き換えることだ。
YJPにとって2017年度は、2016年度に受けた多数の引き合いを、受注につなげる時期となる。今後もミニマルファブの新機種のラボ導入は続く。2017年度中には20の装置がそろい、2020年には現在開発中の種類すべてが完成し、70種のミニマルファブがラインナップされる予定だ。
デバイス製造の概念を変え半導体産業の復活を
産総研との共同開発を、YJPの山本氏は振り返る。
「同じ目的に向かう中で常に緊張感があり、エンジニアも現場で鍛えられました。今後もともに利益を出せるような事業を追求していきたいと考えています」
西村氏はこれまでの産総研のイメージが覆ったという。
「これまでは共同研究したら終わりというイメージがありました。しかし原さんはこれをビジネスとして立ち上げようとしています。だから企業もついていくのです。画期的な製品が事業化される一歩前から一緒に関われたことを、幸運に思っています」
すでに製造プロセスができあがったデバイスの試作サービスは、YJPを通じて提供する一方、産総研では、今後本格生産システムへのステップアップを進めるために、製造プロセスの高度化などに取り組むとともに、2019年には臨海副都心センターに協力企業との研究・実証拠点の設置を予定している。新しい少量デバイスの製造プロセス開発を企業と試みる場であり、YJPもサービス窓口企業として参加する。AI / IoT時代のデバイスに不可欠な少量多品種生産を、日本発ミニマルファブで実現することが狙いだ。
「既存のデバイス製造の概念を変えうるこの装置で、日本の半導体産業を復活させたい」という強い想いで、ミニマルファブのビジネス化を推進していく。
ナノエレクトロニクス研究部門
ミニマルシステムグループ
研究グループ長
原 史朗
Hara Shiro
横河ソリューションサービス株式会社
取締役 専務執行役員 コーポレート本部長
山本 順二
Yamamoto Junji
ナノエレクトロニクス研究部門
ミニマルシステムグループ
主任研究員
クンプアン ソマワン
Khumpuang Sommawan
横河ソリューションサービス株式会社
半導体サービスセンター長
西村 一知
Nishimura Kazutomo
お気軽にお問い合わせください
産総研
エレクトロニクス・製造領域
ナノエレクトロニクス研究部門
- 〒305-8568 茨城県つくば市梅園1-1-1 中央第2
- nanoele-web-ml*aist.go.jp
(*を@に変更して送信してください)
横河ソリューションサービス株式会社