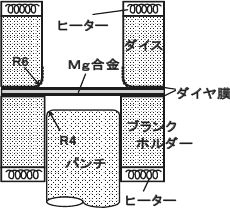
プレス(絞り)加工の概念図 |
独立行政法人 産業技術総合研究所【理事長 吉川 弘之】(以下「産総研」という)サステナブルマテリアル研究部門【研究部門長 中村 守】副研究部門長 坂本 満、環境適応型合金開発研究グループ 佐藤 富雄 研究グループ長、上野 英俊 客員研究員と地方独立行政法人 東京都立産業技術研究センター【理事長 井上 滉】(以下「都産技研」という)と株式会社不二越は共同で、熊本県産業技術センター、鹿児島大学、日本工業大学の協力を得て、CVDダイヤモンドコーティング金型を用いたマグネシウム合金板材の完全な熱間ドライプレス加工技術を確立した。
今回開発した技術は、熱間加工でしかできないマグネシウム合金のプレス成形において、CVDによりダイヤモンドをコーティングした金型を用いることで、320℃程度までの熱間加工でも、潤滑油を用いることなく完全なドライ条件での加工を可能とするものである。
本技術により、一般的なマグネシウム
AZ31合金材はもとより、より加工が困難な
難燃性マグネシウム合金板材のプレス加工についても潤滑油が不要となるため、マグネシウム合金のプレス加工が抱えるコストや洗浄水処理など環境面の問題が解決できる。これにより、マグネシウム合金のプレス成形技術において、従来に比べて低コストで高生産性、環境負荷の低減が期待される。
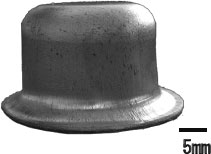
AZ31材(板厚0.8mm) |
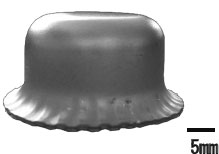
難燃性Mg材(AMX602)板厚0.8mm) |
左右ともに、ダイスとブランクホルダーの両面にダイヤモンドコーティングした金型を使用 |
電気・電子、IT分野をはじめ自動車や産業機械分野では、鉄鋼やプラスチックに替わる素材として、資源量が豊富でリサイクル性に優れ、高強度で軽量なマグネシウム合金への期待が大きいが、マグネシウム合金は室温での塑性加工性に乏しいことから、現状ではダイカスト等の鋳物が主流であり、原材料高と相まって高コストとなっている。軽量性を生かしたマグネシウム合金の普及のためには、生産性が高く低コストな塑性加工技術の確立が急務となっている。
マグネシウム合金は、熱間加工での塑性加工が避けられないため、従来のプレス加工では高温に耐える特殊な潤滑油が不可欠であった。しかし、潤滑油によるオイルミストの発生による作業環境の劣悪化や、加工後の製品洗浄に必要な水の処理など環境面での問題があった。また、潤滑油の焼き付きによる製品の表面性状の悪化に加え、金型のメンテナンスや製品洗浄と潤滑油そのもののコストなど、潤滑油の使用による多くのコストアップ要因があった。
本技術のコスト改善効果により、自動車部材へのマグネシウム合金の実用化が進み、車体の軽量化による燃費向上につながることなども期待される。
マグネシウム合金は燃えやすいことが弱点であるが、産総研では大気中で燃えにくい難燃性マグネシウム合金を開発し、これを基幹材料として産業界へ普及させるために、材料創成から各種の加工技術開発まで総合的に取り組んできた。特に、具体的な実用化につなげるための効率的な研究手法として、産学公の適切な連携による有機的な研究の進め方をとることにより、我が国でもトップクラスの知見と研究ポテンシャルを有している。
産総研はこれまで、より加工性の良い高品質の板材の製造法として熱間加工押し出しによる板材の開発を企業と共同で進めてきた。産総研と都産技研は、この板材を用いて熱間プレス加工による鉄道車両用実部材の成形に取り組み、テフロンシートを潤滑剤として用いた熱間プレス成形技術を確立してきた。
これまでの技術をベースに、産総研の難燃性マグネシウム合金の材料開発と都産技研のプレス加工技術、(株)不二越の金型コーティング技術を融合し今回の技術開発に至った。
なお、本研究は熊本県産業技術センター、鹿児島大学、日本工業大学の協力も得て行った。
マグネシウム合金のプレス成形は現状では熱間加工しかできず、一般的なマグネシウム合金AZ31合金で160~180℃、展伸用AM60合金(アルミニウム 6%、マンガン 0.4%合金)に2%のカルシウムを添加した難燃性合金AMX602合金では280~300℃の高温を必要とする。従って、加工に際して高温に耐える特殊な潤滑油が不可欠となることが大きな問題であった。
今回の技術は、研磨したダイヤモンド表面の摩擦係数が極めて小さいという性質を利用して、潤滑剤が不要の完全ドライプレス加工技術を確立したものである。プレス金型の加工面にCVDによるダイヤモンドコーティング膜を付けて、その膜の潤滑効果によってプレス加工を行う技術である。ダイヤモンドは耐熱性に優れることから、難燃性合金の加工温度である320℃程度までの熱間加工でも問題なく潤滑性能を発揮し、コーティング膜の耐久性も十分にあることが確認された。
開発した技術は、以下の2点である。
-
金型表面へのダイヤモンドコーティング
-
超硬金型への成膜の最適化
CVDダイヤモンド膜をメタン1% と水素99% を原料に熱フィラメント法で作製した。
-
膜質の評価
膜質と成膜条件を詳細に調査し、良好な結晶性および粒度で、膜厚約10μmの成膜に成功した。
-
摩擦特性改善のための研磨技術の確立
素結晶からなる膜表面の研磨により、表面あらさ約0.5μmRz MAX以下を達成した。
-
難燃性マグネシウム合金の開発
-
技術移転による量産化と板材の製作
大気中で燃えにくい難燃性マグネシウム合金の技術移転による量産化を進め、圧延板材の供給を可能とした。
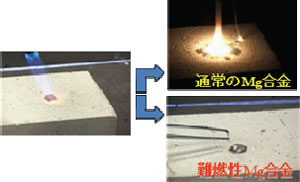
通常のMg合金と難燃性Mg合金の燃焼実験 |
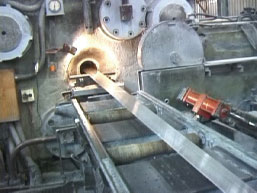
熱間押し出しによる難燃性Mg合金板材の製造
|
また、以下の基礎的な試験評価を行った。
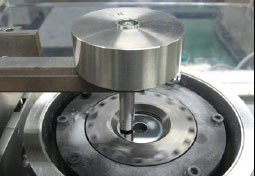 |
ピンオンディスク式摩擦試験装置 |
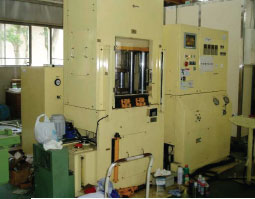 |
熱間サーボプレス成形機 |
-
材料の機械特性評価
圧延板材の機械的性質および圧延材の異方性を系統的に調査し、加工特性を把握する基礎データを整備した。
-
摩擦特性評価
ピンオンディスク式摩擦試験装置を用いてマグネシウム合金とCVDダイヤモンドの摩擦特性を20℃(室温)、100℃、200℃、および300℃の広範な温度で評価し、高温で十分な潤滑性を持つことを明らかにした。
-
熱間プレス成形性評価
熱間サーボプレス成形機による無潤滑(ドライ)加工試験を系統的に行い、加工条件を確立した。従来のテフロン潤滑シートとダイヤモンドコーティング膜による成形性の比較を行い、十分な加工品質を確認した。