国立研究開発法人 産業技術総合研究所(以下「産総研」という)マルチマテリアル研究部門 中島佑樹 研究員、福島学 研究グループ長、古嶋亮一 主任研究員、丸山豊 主任研究員、NGO MINH CHU特別研究員、大司達樹 招聘研究員らは、窒化ケイ素セラミックスの壊れにくさを高精度で予測するAI技術を使って、求める特性をもつ窒化ケイ素セラミックス組織のモデル画像を敵対的生成ネットワーク(GAN)による仮想実験によって生成することに成功しました。窒化ケイ素セラミックスは電力の変換と制御の高効率化を可能とすることから次世代電気自動車などのパワーモジュール基板への普及が期待されています。しかし、窒化ケイ素セラミックスはセラミックス材料の中でも特に複雑な微細組織から構成されており、従来の測定手法では目的とする物性値を迅速に得ることは難しいため、材料開発には多くの時間を要します。今回開発した技術は、窒化ケイ素セラミックスの微細な組織画像と破壊靭性に関する実験データを学習させた人工知能(AI)を使ってコンピューター上で壊れにくさの指標である破壊靭性を高い精度で予測すると共に、窒化ケイ素セラミックス組織のモデル画像を生成する技術を開発しました。この技術の一部は、2022年9月26日(現地時間)に「Journal of the American Ceramic Society」誌に掲載されました。
自動車や鉄道のモーター駆動制御、太陽光発電などでは、電力の変換と制御を高効率で行うパワーモジュールが必要とされており、破壊靭性はパワーモジュールの壊れにくさに繋がるため重要な特性です。絶縁放熱基板として各種のセラミックスが利用されていますが、中でも高い破壊靭性で知られる窒化ケイ素セラミックス(Si3N4)が注目されています。窒化ケイ素セラミックスは加熱するだけでは緻密な組織は形成されないので、融液を形成する焼結助剤とともに高温で加熱する必要があります。窒化ケイ素セラミックスの微細組織は、焼結助剤の種類や添加量・焼結温度・焼結時間で大きく変化し、得られる材料の強度、破壊靭性、熱伝導率には数倍の差が生じます。半導体素子の高い発熱と寒冷地での使用を模擬したパワーモジュールの冷熱サイクル試験では、1 GPaの曲げ強度を有する窒化ケイ素セラミックスであっても、数サイクル後には初期強度の約70%まで低下します。しかし産総研では、10 MPa・m1/2と高い破壊靭性を持つ窒化ケイ素において、1000サイクルを超える冷熱サイクル試験後でも高い曲げ強度が維持されることを見出しました。
高い破壊靭性を得るためには、技術者の長年の経験に基づいた焼結条件や助剤の選択に加え、網羅的な試作と物性の評価が必要となります。このような背景から、近年の窒化ケイ素セラミックの需要拡大に対応し材料開発を加速するためには、破壊靭性の評価を迅速化し、技術者の経験や勘に頼らずに無数にある製造条件に指針を与える技術が求められていました。これらを解決する技術として、マテリアルズ・インフォマティクスやプロセス・インフォマティクスにおけるディープラーニング(深層学習)など、AI技術の活用研究が想定されますが、窒化ケイ素セラミックスのような複雑な組織構造をもつ材料にも適用できるAI技術の報告は皆無でした。
高い破壊靭性を持つ窒化ケイ素はパワーモジュール用セラミックス基板として有望です。産総研は窒化ケイ素セラミックスの高熱伝導率化、絶縁耐圧測定、メタライズを行った基板の温度サイクル試験等の寿命評価技術など、次世代パワーモジュール用セラミックス基板に関する研究開発を一貫して行ってきました。現在セラミックス基板として、窒化アルミニウムが高熱伝導率(170~250 W/(m·K))であることから汎用的に使用されていますが、破壊靭性が低いことが課題となっています。そこで、2011年に産総研は、窒化アルミニウムの3倍以上の破壊靱性を有し、177 W/(m·K) という世界で最も高い熱伝導率を持つ窒化ケイ素セラミックスを開発しました(2011年9月6日 産総研プレス発表https://www.aist.go.jp/aist_j/press_release/pr2011/pr20110906/pr20110906.html)。また、窒化ケイ素セラミックス基板は32 μmと超薄型であっても2.8 kVの高い絶縁耐圧をもち、次世代電気自動車の作動電圧である850 Vよりも十分に高い値であることを世界で初めて実証しました(2021年11月25日 産総研プレス発表https://www.aist.go.jp/aist_j/press_release/pr2021/pr20211125_2/pr20211125_2.html)。窒化ケイ素セラミックスの破壊靭性値は、パワーモジュールとして使用するときに重要となりますが、破壊靭性の予測、求める破壊靭性を持つ微細な組織画像を予測した例は皆無でした。そこで、本研究では、1)測定にノウハウが必要かつ長時間を要する破壊靭性を組織画像からAIで正確に予測することと、2) 高破壊靭性な窒化ケイ素セラミックス組織のモデル画像をAIにより生成することに着手しました。1)についてはノウハウを必要とせずにコンピューター上で簡便かつ精度よく破壊靭性を予測することが可能になります。2)については、無数に存在する製造条件の中から最優先で検討すべき事項を抽出でき、経験と勘に頼って実験をせずに、最適な成形手法や焼結条件を提案することが可能になるため、材料開発を迅速化できます。
気孔・粒界ガラス相・微細粒子・成長した柱状粒子からなる窒化ケイ素セラミックスの複雑な微細組織は、力学特性と強い相関関係を有していると考えられています。今回開発した手法は、AIに組織画像と破壊靭性に関する実験データを学習させ、(1)AIが着目する部位を確認しながら未学習の組織画像に対する破壊靭性を高精度で回帰予測する技術、および(2)条件付き敵対的生成ネットワーク(C-GAN)により高破壊靭性な窒化ケイ素セラミックス組織のモデル画像を生成する技術です。6~10 MPa・m1/2の破壊靭性を有する窒化ケイ素セラミックス45検体を作製し、取得した組織画像(図1a)から小画像を並進、回転、転置を組み合わせて複数切り出し、畳み込みニューラルネットワーク(CNN)により学習させました。学習に用いていない検体に対して破壊靭性を回帰予測・検証したところ、サンプル数が数百から数千を必要とする通常のAI学習と比べて、少ないサンプル数でも、高い予測精度を得ることが出来ました(図1b)。加えて、AIが着目する部位を可視化(Grad-CAM)したところ、AIが破壊靭性の予測において、粗大な柱状粒子に着目していることを明らかとしました(図1cの赤色で示した部位)。なお学習に使わなかったデータに対する更なる成績の向上やさまざまな焼結助剤への適用が今後の課題です。
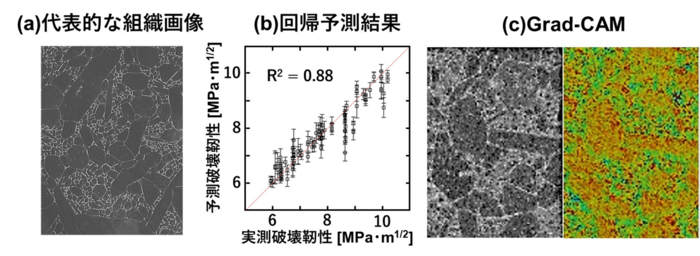
図1 窒化ケイ素セラミックスの(a)代表的な組織画像と(b)破壊靭性の実測値とAIによる予測値の相関関係、
および(c)Grad-CAMによる着目箇所の可視化
次に組織画像の実験データの特徴を学習し、ある特定の破壊靭性を持つ組織のモデル画像を生成させました。窒化ケイ素セラミックスを構成する複雑で微細な組織画像(図2a)を学習し、細部まで忠実に再現したAI生成画像を得ることが可能となりました(図2b)。AI生成画像は、気孔がほぼ存在しない緻密な組織が特徴的であるため、緻密化が最優先で検討すべき事項であり、製造プロセス検討の指針が得られます。現段階では、技術者の経験と擦り合わせて画像を判断し材料開発へ展開する必要があるため、今後の課題は、技術者の経験や勘に頼らずに、生成した組織画像から検討すべきプロセス条件を自動的に抽出するプロセス・インフォマティクスに発展させることです。
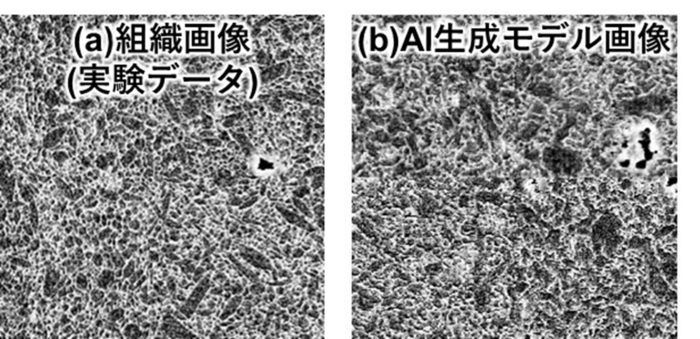
図2 (a)代表的な窒化ケイ素セラミックスの組織画像(実験データ)
(b)今回の技術によってAIが生成した窒化ケイ素セラミックス組織のモデル画像(AI生成画像)
開発した新規AI技術を元に、未学習データに対する破壊靭性の予測精度の向上、並びに破壊靭性からモデル画像の生成のみでなくプロセス条件も抽出可能な技術開発に取り組み、放熱基板、構造材料、マルチマテリアルといった窒化ケイ素をベースとしたマテリアルズ・インフォマティクスおよびプロセス・インフォマティクスを推進します。本技術をさらに発展させて、製造工程の高速・効果的な探索を通して、材料開発の革新に貢献します。