独立行政法人 産業技術総合研究所【理事長 野間口 有】(以下、「産総研」という)先進製造プロセス研究部門【研究部門長 村山 宣光】エンジニアリングセラミックス研究班 平尾 喜代司 研究班長、周 游 主任研究員らは、電気化学工業株式会社【代表取締役社長 吉高 紳介】(以下、「電気化学工業」という)ならびに日本ファインセラミックス株式会社【代表取締役社長 若林 俊克】(以下、「日本ファインセラミックス」という)と共同で、窒化ケイ素(Si3N4)セラミックスの熱伝導率を従来品に比べて飛躍的に高めることにより、高熱伝導率、高強度、高靱性を兼ね備えたセラミックスを開発した。
パワーモジュール用の回路基板には放熱のために高い熱伝導率が必要である。窒化ケイ素は高強度、高靭性であるが、従来の製造技術では、高い熱伝導率と優れた機械特性を併せ持つ窒化ケイ素材料を製造することは極めて困難であった。
今回、1400 ℃付近でシリコン粉末の成形体を窒化させたあと、高温で緻密化を行う、いわゆる「反応焼結・ポスト焼結手法」を用いることによって、177 W/(m·K) という世界で最も高い熱伝導率を持つ窒化ケイ素セラミックスを作製することに成功した。パワーモジュール用の放熱基板として汎用的に用いられている窒化アルミニウムセラミックスの熱伝導率は、おおよそ170~230W/(m·K)であり、この範囲内に窒化ケイ素焼結体の熱伝導率を向上させることができた。また、材料の強度は窒化アルミニウムより高く、粘り強さを示す破壊靱性は窒化アルミニウムの3倍以上であった。柱状粒子が絡み合った構造を持つことが優れた機械特性に寄与している。
なお、この研究内容の詳細は「Advanced Materials」誌にオンラインで発表される予定である。
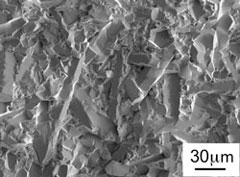 |
開発した高熱伝導率窒化ケイ素の破断面の電子顕微鏡写真
|
近年、パワーエレクトロニクスの進歩により、電力の変換と制御を高効率で行うパワーデバイスが急速に普及してきた。高出力のデバイスとしては産業用ロボット、電車など輸送機器のモーター制御に活用されている。さらに、自動車動力のハイブリッド化、電気モーター化の流れが急速に進み高出力パワーモジュールの市場が急速に広がりつつある。
パワーモジュールは、数十から数百kWの大電力の変換・制御を行うため、その回路基板には高い絶縁性、放熱性、耐熱性が要求される。窒化アルミニウム (AlN) 基板は約200 W/(m·K) の高い熱伝導率を持ち、車載用インバーターなど出力密度の高いパワーモジュールの回路基板に使用されてきた。しかし、パワーモジュールの出力密度は年々高くなっており、また、自動車などに搭載される場合、大きな温度変化にさらされ、さらに、接合部分には高い応力が発生するため、回路基板には高い熱伝導率に加えて優れた機械特性も強く求められるようになってきた。
図1に、現在市販されているアルミナ基板、窒化アルミニウム基板、窒化ケイ素基板の強度と熱伝導率(図1-a)および破壊靱性と熱伝導率(図1-b)の関係を示す。窒化アルミニウム基板は高い熱伝導率を持つものの窒化ケイ素と比べて、機械特性(強度と破壊靱性)が低い。一方、窒化ケイ素は優れた機械特性を持つものの、熱伝導率が窒化アルミニウムの半分以下である。しかし、窒化ケイ素の理論熱伝導率は200 W/(m·K)を超えると予測されており、優れた機械特性と高熱伝導率を併せ持つ次世代の回路基板材料として、窒化ケイ素セラミックスの熱伝導率向上が強く求められていた。
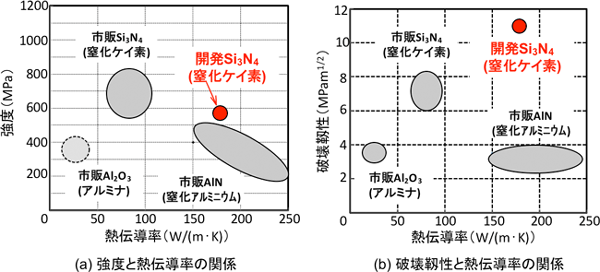 |
図1 市販のセラミック放熱基板及び開発窒化ケイ素の特性比較
|
産総研は、窒化ケイ素セラミックスの製造プロセス、微細構造、熱伝導率の関係について長年にわたり基礎的な研究を行ってきた。2001年には、窒化ケイ素マグネシウム(MgSiN2)を窒化ケイ素の焼結助剤として用いて約150 W/(m·K)の熱伝導率を持つ焼結体の作製に成功している(2001年7月9日産総研プレスリリース)。
しかし、窒化ケイ素マグネシウムの添加で高熱伝導が達成されたものの、150 W/(m·K)の高熱伝導窒化ケイ素焼結体においては焼結過程で極めて粗大な粒子が成長し、強度と破壊靱性が大きく低下するという課題があった。
2009年からは産総研の基礎的な知見を基に、総合素材メーカーであり非酸化物セラミックスにも高い技術を有する電気化学工業ならびにセラミック基板や産業機械用セラミックス部材などの製造・販売を行っている日本ファインセラミックスと共同で、優れた機械特性と高熱伝導率を併せ持つ窒化ケイ素セラミックスの研究開発を進めてきた。
絶縁体セラミックスの中では、熱は結晶の格子の振動(フォノンと呼ばれる)によって伝わる。このため、結晶中の格子欠陥(空孔、異種元素の置換など)があるとフォノンが散乱され熱伝導率が著しく低下する。ダイヤモンド(理論熱伝導率:2000 W/( m·K))や窒化アルミニウム(理論熱伝導率:320 W/(m·K))のように、原子間の結合が強く、軽い元素で構成され、対称性の高い結晶は、フォノンが伝わりやすく高い熱伝導率を持つ。同様に、純粋な窒化ケイ素結晶の熱伝導率は200 W/(m·K)を超えると予想されている。
窒化ケイ素は、それ自身では焼結が難しい難焼結材料として知られている。従来の製造技術では窒化ケイ素粉末を原料とし、焼結助剤として主に酸化イットリウム(Y2O3)などの希土類酸化物を添加し、高温で焼結して柱状粒子の発達した緻密なセラミックスが作製される。しかし、市販の高純度窒化ケイ素粉末には、粒子表面の酸化により約1 重量% 程度の酸素が不純物として含まれている。この不純物酸素が、焼結の過程で窒化ケイ素結晶内部にも移動、固溶してフォノンの散乱要因となって、熱の伝導を阻害するため熱伝導率が高くならない。出発原料中の酸素量を低減させれば窒化ケイ素粒子内部の固溶酸素量を低く抑えられるが、不純物酸素は、窒化ケイ素粒子の表面酸化によるものであり、焼結性に優れた微粉末では不純物酸素量の低減は困難である。この問題を克服するため、今回の開発では、希土類酸化物を主体とする焼結助剤を含む高純度シリコン粉末の成形体を1400℃付近で窒化させたあと、高温、高圧の窒素中で緻密化を行う「反応焼結・ポスト焼結手法」に着目し、熱の伝導を阻害する粒子内部の不純物や粒界相の量を低減させて粒成長を抑制するプロセスを検討した。この手法では、1)原料粉末として不純物酸素の少ないシリコン粉末を使用できること、2)シリコン粉末成形体は寸法変化なしで窒化が進むため、反応焼結後には比較的高い相対密度(約80%)の窒化体が得られ、その後のポスト焼結による緻密化が容易であること、3)シリコン粉末と窒素との反応による窒化ケイ素への転換とその後の緻密化を、一連の工程で空気に触れさせずに行うことができるため、粉末の酸化を抑えて、最終的に得られる焼結体の窒化ケイ素粒子内部の不純物酸素量を大きく低減させることができる、といった利点が考えられる。
熱の伝導を阻害する粒子内部の不純物や粒界相の量を最小にするように、窒化反応やポスト焼結などのプロセス因子を最適化した結果、177 W/(m·K) の高い熱伝導率の窒化ケイ素セラミックスを作製することに成功した。機械特性の評価が可能な約40×40×5 mm程度の大きさの焼結体を作製することができ、焼結体について強度と破壊靱性の評価を行った。図1の赤丸印で示したように、今回開発した材料は、高い熱伝導率に加えて窒化アルミニウムを超える強度(3点曲げ強度:約550 MPa)をもち、破壊靭性(11 MPam1/2)は窒化アルミニウム(3 MPam1/2程度)の3倍以上であり、世界最高の高い熱伝導率と優れた機械特性を併せ持っている。図2に開発した材料の破断面の走査型電子顕微鏡写真(SEM写真)を示す。柱状に発達した窒化ケイ素粒子が絡み合った微細構造を持ち、これが高い破壊靱性をもたらしている。また、柱状粒子の大きさは比較的揃っており、極端に粗大な粒子は見られない。柱状粒子の成長を制御できたこと、ならびに高い破壊靱性が本材料の適切な強度の維持に寄与している。
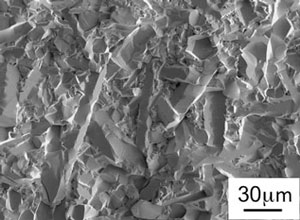 |
図2 開発した高熱伝導率窒化ケイ素の破断面の電子顕微鏡写真
|
今後は、今回開発したプロセスを基に、高い熱伝導率と優れた機械特性を兼ね備えた窒化ケイ素回路基板の製造プロセスを確立し、パワーモジュール用など放熱性と優れた機械特性に基づいた信頼性が求められる基板材料としての実用化を図る。