国立研究開発法人 産業技術総合研究所【理事長 中鉢 良治】(以下「産総研」という)触媒化学融合研究センター 触媒固定化設計チーム 深谷 訓久 主任研究員、崔 準哲 研究チーム長、佐藤 一彦 研究センター長、化学プロセス研究部門 化学システムグループ 片岡 祥 主任研究員、Nguyen Thuy研究員らは、コルコート株式会社【代表取締役社長 野口 由美子】(以下「コルコート社」という)と共同で、ケイ素化学の基幹原料であるテトラアルコキシシランを、砂や植物燃焼灰、産業副産物などから、従来よりも短時間に高効率で直接合成する技術を開発した。
テトラアルコキシシランは、現状ではケイ石を金属ケイ素に還元するプロセスを経由して工業的に製造されており、製造プロセスのエネルギー消費の多さと高いコストが課題となっている。今回、シリカを多く含み、安価で豊富に存在する砂、植物燃焼灰、産業副産物などをケイ素源としてアルコールと反応させて、テトラアルコキシシランを一段階で高効率に直接合成できる技術を開発した。この技術では、汎用されている無機脱水剤のモレキュラーシーブで、反応によって副生する水を吸着除去することで、以前に産総研が報告した有機脱水剤を用いる従来の技術よりも反応の効率を大幅に向上させるとともに、砂や灰など、適用できるケイ素源の範囲を拡大した。この技術は、安価で豊富に存在するさまざまなケイ素源を有効活用し、有機ケイ素原料の省エネルギー・低コスト製造に新たな道を拓くものである。
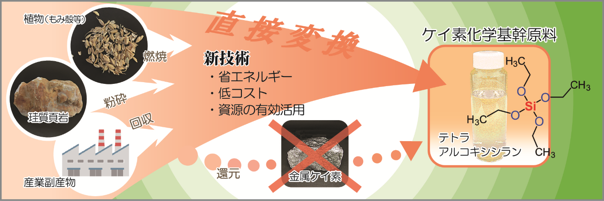 |
もみ殻、砂、産業副産物など安価なケイ素源からケイ素化学基幹原料を製造 |
テトラアルコキシシランは、セラミックスや電子デバイス用の保護膜・絶縁膜の原料として利用されている。また幅広い産業分野で使用されているシリコーンをはじめとするさまざまな有機ケイ素材料の原料としても有望である。現在、テトラアルコキシシランの製造では中間原料として金属ケイ素を経由する必要がある。これには大量の電気エネルギーを用いて高温でケイ石(シリカが主成分)の還元反応を行う必要があるため、エネルギーを多く消費し、高コストとなることが課題である。したがって、安価なシリカ原料から直接合成する技術の開発が望まれているが、その技術的難易度の高さから、半世紀以上に渡って、金属ケイ素を経由したプロセスで工業的な生産が行われている。
産総研は、有機ケイ素機能性化学品製造プロセスの研究開発を行っている。その一環として金属ケイ素を経由しない新たな有機ケイ素化学品製造方法の開発を目指しており、これまでにシリカとアルコールを原料とし、有機脱水剤、二酸化炭素、少量の触媒を共存させるテトラアルコキシシランの合成法を開発した(2014年5月20日 産総研プレス発表)。今回、産総研とコルコート社は共同で、従来よりも短時間に高効率でテトラアルコキシシランを合成できる技術の開発に取り組んだ。
なお、本研究開発は、経済産業省未来開拓研究プロジェクト「産業技術研究開発(革新的触媒による化学品製造プロセス技術開発プロジェクト/有機ケイ素機能性化学品製造プロセス技術開発)」(平成24~25年度)と国立研究開発法人 新エネルギー・産業技術総合開発機構「有機ケイ素機能性化学品製造プロセス技術開発」(平成26~33年度)(プロジェクトリーダー:佐藤 一彦)の一環として行われた。
シリカから直接テトラアルコキシシランを収率良く合成するためには、アルコールとの反応によって副生する水を反応系から除去する必要がある(図1)。砂や灰などの反応性の低いさまざまなケイ素源を活用するためには、高い効率で反応系から水を除去できる脱水剤が必要であり、さらに製造プロセスの低コスト化のためには、脱水剤は反応終了後に目的物であるテトラアルコキシシランから容易に分離でき、回収・再利用が可能であることが望まれる。
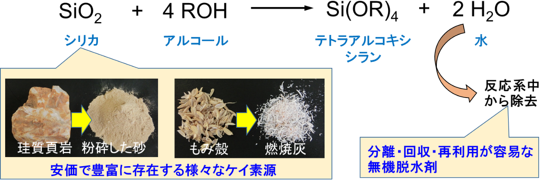 |
図1 さまざまなケイ素源とアルコールからテトラアルコキシシランを合成する反応式 |
今回、シリカを含有する原料とエタノールに、触媒として少量の水酸化カリウム、脱水剤として固体状無機物質であるモレキュラーシーブを加えて加熱し反応させた。触媒として加えた水酸化カリウムは、シリカの分解すなわちケイ素-酸素結合の切断を促進する働きがある。また無機脱水剤であるモレキュラーシーブは、反応によって生成した水を吸着して反応系から取り除き、反応が逆方向に戻ってしまうことを防いでおり、従来の技術の有機脱水剤よりも水を取り除く効率が高く、ケイ素源に含まれる不純物の影響も受けにくいため、砂や灰などの反応性が低く、シリカ純度の高くない天然のケイ素源を用いても高収率にテトラアルコキシシランを合成することが可能になった。さらにモレキュラーシーブは固体状であるため、反応後には容易に回収して、加熱や減圧で再生して繰り返し使用できるため、製造プロセスの低コスト化に対しても有利である。この結果、反応時間3時間でテトラエトキシシランが高い収率で得られた(図2)。
珪質頁岩を粉砕した砂では、含有するシリカに対して51 %の収率でテトラエトキシシランが生成した。またシリカを多く含む植物燃焼灰として、もみ殻の灰を原料とした反応では収率は78 %であった。合成石英製造時の産業副生成物を原料とすると収率は72 %であった。
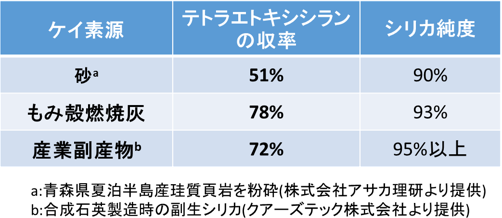 |
図2 さまざまなケイ素源からのテトラエトキシシランの合成 |
今回の技術と以前に産総研が開発した技術との反応効率の比較を図3に示す。無機脱水剤を用いる今回開発した反応プロセスは、大幅に短時間に高収率で合成できた。
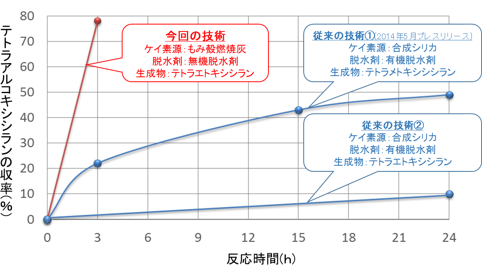 |
図3 今回開発した技術と従来技術との反応効率の比較 |
今回開発した技術は、豊富に存在するさまざまなシリカを含有する原料に適用でき、金属ケイ素を経由しないので、有機ケイ素原料の省エネルギー・低コスト製造につながり、今後の有機ケイ素材料の利用拡大に貢献することが期待される。
今後は、反応条件や触媒の改良とともに、より低コストな製造方法を目指し、化学工学的な視点から反応プロセス全体を最適化する。さらにスケールアップなどの事業化に必要な技術課題の解決をコルコート社と共同で取り組み、数年後の実用化を目指す。