独立行政法人 産業技術総合研究所【理事長 吉川 弘之】(以下「産総研」という)先進製造プロセス研究部門【研究部門長 三留 秀人】先進焼結技術研究グループ【研究グループ長 渡利 広司】安岡 正喜 主任研究員および白井 孝 特別研究員らは、マイクロ波技術の利用によってセラミックス製造工程を統合し簡略化した新規なプロセスを開発した。本技術によりセラミックスの製造時間を従来の半分以下に短縮できる。また、製造に要するエネルギーも削減でき、低環境負荷型製造プロセスである。
今回新規に開発した崩壊式成形型を用いることにより、脱型工程と脱脂工程が省略できるようになった。本プロセスでは、崩壊式成形型にセラミックススラリーを流した後、乾燥から焼成までの一連の加熱工程を、マイクロ波加熱炉内にて行う(図1)。
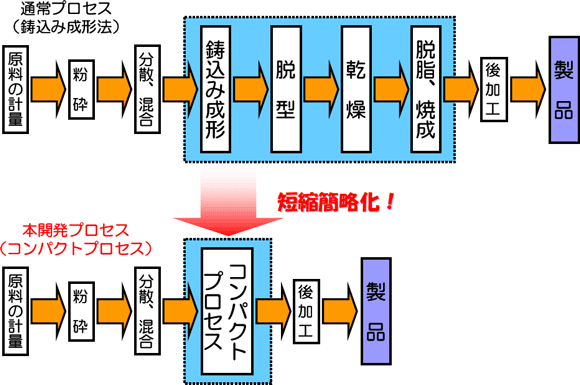 |
図1 開発したプロセスのコンセプト |
人類は地球温暖化やエネルギー資源の枯渇といった大きな課題を抱えている。わが国ではエネルギー消費によって生じる温室効果ガスの約4割が、産業部門によって排出されている。とりわけセラミックス産業は、部材製造の際、高温かつ長時間の焼成が必要とされるため、単位製品あたりの消費エネルギーが大きく、また製造工程において二酸化炭素等の温室効果ガスを大量に排出するなど、環境に対する影響は大きい。一方、ナノテクノロジーやエレクトロニクス、通信分野の急速な発展に伴い、近年のセラミックス産業の動向は、高機能化、新規機能性付与を目指した高付加価値製品の開発に向かっており、次世代セラミックスを見据えた製造プロセスの抜本的見直しが必要である。これらの社会的要請を踏まえ、経済性、低環境負荷性を加味した上で、工程に要する時間の短縮化、使用する資源の減量化、投入エネルギーの低減化、工程数の最少化を導く新たな高効率製造プロセス技術の開発が強く求められている。
産総研先進製造プロセス研究部門先進焼結技術研究グループでは、セラミックス製造プロセスの環境負荷低減を目指し、成形から焼成までの製造工程の簡略化、短縮化に取り組んでいる。その研究の一環として、マイクロ波により生じる電磁場環境の特異な反応場を、セラミックス製造プロセスに有効利用する技術の開発を進めている。マイクロ波による加熱は、内部加熱や選択的加熱など様々な特徴を持ち、効率的なエネルギー投入による省エネルギー効果が期待できる。
一般にセラミックスは、原料の粉砕、分散・混合、乾燥、成形、脱脂、焼成、加工といった多くの工程を経て製造される。通常の製造プロセスは、(1)工程時間が非常に長い、(2)コストが高い、(3)投入エネルギーが非効率である等の問題点がある。そこで当グループでは各工程を単純化、短縮化し、(1)量産性の向上、(2)経済性(特に時間の短縮)、(3)環境への適合等を考慮して、セラミックス部材の生産性の向上を目的とした、コンパクトプロセス技術の開発を目指し研究に取り組んでいる。
代表的なセラミックスの成形法として鋳込み成形法があり、複雑形状物や衛生陶器などの大型形状物の成形などに用いられている。 鋳込み成形法には低濃度のスラリーを、石膏に代表される吸水性の多孔質鋳型に流し込み、型壁に着肉層を形成させた後、排泥する排泥鋳込み成形と、濃厚なスラリーを型に流し込みそのまま固化させる固形鋳込み法がある。どちらの手法も、脱型後乾燥し、成形体を焼成炉内にて脱脂、焼成工程を行い、後加工を経て製品となる。非常に汎用性の高い成形手法と言えるが、成形体の乾燥に長時間を要する。また複雑な形状を有する成形体を作製する場合、有機バインダーの添加が不可欠となるが、加熱によりバインダーを除去する脱脂工程は数十~数百時間にも及ぶため、投入エネルギー削減及び生産性向上の観点から、工程の見直しが必要である。また脱型時における成形体への損傷や、乾燥、脱脂工程における欠陥の生成などが問題となる。
そこで本研究では、鋳込み成形法における“鋳込み(成形)”、“脱型”、“乾燥”、“脱脂”、“焼成”の各工程を1工程に統合化する“コンパクトプロセス”を開発した。このプロセスは、スラリーを鋳込み型に流して成形し、脱型することなく、乾燥から焼成までの一連の加熱工程をマイクロ波加熱炉内で行うことで、工程の単略化、工程時間の短縮、投入エネルギーの削減を達成する低環境負荷型製造プロセスである。
まず、鋳込み後焼成までの加熱工程をマイクロ波加熱炉内にて一貫して行えるようにするため、崩壊式成形型を新しく開発した(図2)。この成形型の機能は以下の通りである。
- 鋳込み、乾燥時には成形型として作用する。
- 焼成時には断熱材及びマイクロ波吸収材として作用する。
- 焼成後は崩壊し、容易に製品を取出すことができる。
崩壊式成形型を用いることにより、成形、乾燥、焼成を同一工程で行うことができ、脱型工程を省けるため、様々な複雑形状品の製作に対応できる(図3)。また着肉時における成形体内への不純物の混入が非常に少ないという特徴もある。さらに、焼成時における型材への影響は小さいため、型材粉末は繰り返し使用しても型としての特性になんら影響を及ぼさず、何度でも利用することが可能である。
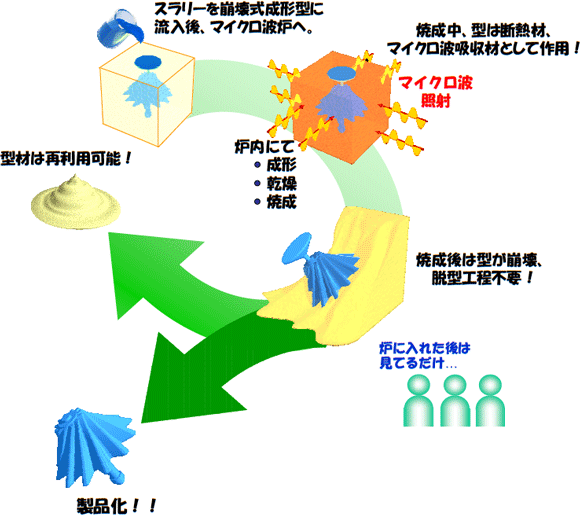 |
図2 崩壊式成形型を用いたコンパクトプロセス |
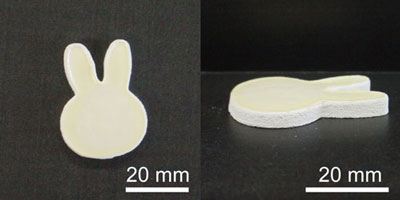 |
図3 開発したコンパクトプロセスにより作成した焼成体。様々な形状に容易に対応できる。 |
鋳込み成形による通常工程及び開発したコンパクトプロセスにおける、アルミナ焼成に必要な工程時間の比較を行った(図4)。通常工程では焼成過程までの工程(鋳込み、脱型、乾燥)にかかる時間が非常に長い。特に乾燥工程では反りや割れ、密度ムラといった欠陥が発生しやすいため、通常、乾燥雰囲気の湿度を調節しながら、なるべく低い温度でゆっくりと乾燥させる必要がある。しかし開発したプロセスでは、マイクロ波加熱により内部水分を選択的に加熱、乾燥させるので、乾燥後の成形体の欠陥を抑制し、均質な成形体構造を作製することが可能であり、大幅に工程時間を短縮できる。またこのプロセスでは成形、乾燥、焼成を同一工程で行うため脱型工程を省くことができる。そのためバインダーを使う必要が無く、脱脂工程が不要となる。バインダーを使わず脱脂工程を省略できるので、低環境負荷の観点からも優れた製造方法といえる。開発したプロセスでは通常工程(当所従来製法)に比べ、成形から焼成までの工程時間を約1/5以下に、全体の工程時間を半分以下に短縮できる。またマイクロ波加熱を用いることで、焼成温度の低温化、焼成時間の短縮化が可能であり、投入エネルギー削減効果も大きいと期待される。
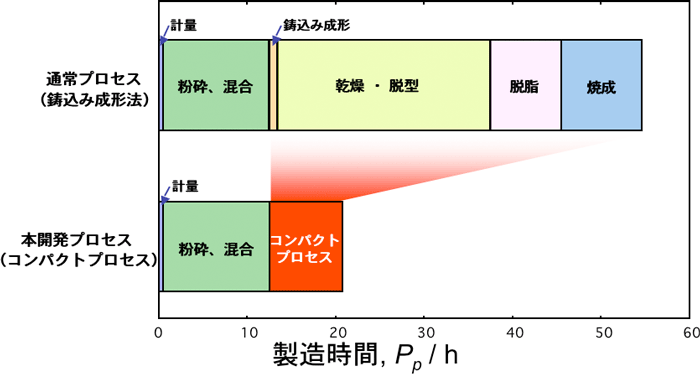 |
図4 開発したコンパクトプロセスによる製造時間短縮効果(注)
(注):当所従来製法によるアルミナ焼成体製造時間との比較 |
今回、スラリー作製は通常用いられるボールミル法で行ったが、今後、当研究グループで開発した湿式ジェットミル(産総研 TODAY Vol.7 No.3 18頁(PDF:993KB))法の適用を検討する。これにより、工程時間が短縮するだけでなく、粘度が低く再凝集しにくいスラリーを得ることができ、短時間での高品質なセラミックス製品の製造が期待できる。
また、開発したコンパクトプロセスにおける作業は、スラリー鋳込み後マイクロ波加熱炉に入れるだけであることから、セラミックス製造プロセス自動化への応用・展開を図る。