独立行政法人 産業技術総合研究所【理事長 吉川 弘之】(以下「産総研」という)先進製造プロセス研究部門【部門長 三留 秀人】先進焼結技術研究グループ 渡利 広司 研究グループ長、安岡 正喜 主任研究員および白井 孝 産総研特別研究員らは、マイクロ波照射によりセラミックス粒子の水和反応を促進することで、有機バインダーを用いることなく保形性に優れたセラミックス成形体の作製を可能にする新しい製造プロセス技術を開発した。
セラミックスの成形プロセスでは、成形体の形を保持するために、有機高分子をバインダー(結合剤)として添加する。このバインダーは焼成過程で加熱分解され、二酸化炭素などの温室効果ガスや有害ガスとして排出される。そのため、バインダー量の削減が重要な課題となっている。
本開発技術は、15分程度のマイクロ波加熱により有機バインダーを用いないで湿式成形体中の水分と粒子表面層の水和反応を促進し、粒子表面に水和物もしくは水酸化物を生成させ、粒子同士を強固に結合させる(図)。
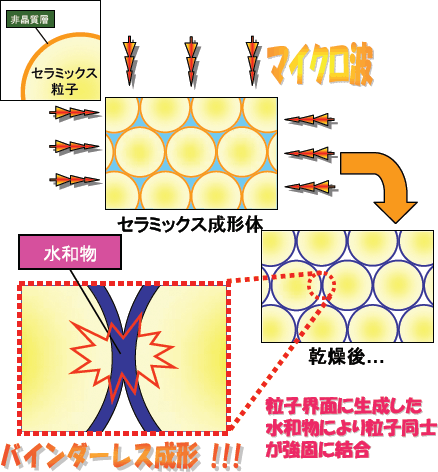 |
図 本成形技術の概念図 |
産総研では、セラミックス製造プロセスの低環境負荷を目指し、成形から焼結までの製造工程の簡略化、短縮化に取り組んでいる。その研究の一環として、マイクロ波により生じる電磁場環境の特異な反応場を、セラミックス製造プロセスに利用する技術開発を進めている。
従来からセラミックス成形体の作製時、特に湿式成形方法において、その保形性を付与するために多量(セラミックス原料に対して10-15wt%)の有機物がバインダーとして用いられている。しかし、これら成形体中の有機物はセラミックス製造工程において完全燃焼させる必要があり、多量のエネルギーを消費するとともに、有機物の燃焼に伴い有害ガスや二酸化炭素が発生するため、地球温暖化や大気汚染への環境負荷が問題となっている。このような背景から、有機物を使わずに粒子同士の強固な結合が得られ、保形性を有するセラミックス製造プロセスの開発が望まれている。
従来の湿式成形方法では、良好な成形性と成形後の保形性を確保するために、有機バインダーを多量に添加する必要があるが、有機物の使用は焼成後の工程において脱脂等の操作が必要となる。そのためバインダーレス成形技術が開発されれば、脱脂工程を省略することが可能となり、製造プロセスの簡略化がなされ、省エネルギー・省資源・低環境負荷を実現する製造プロセスへの道を切り開くことになる。
本研究では、マイクロ波を試料に照射することにより、湿式成形体中の水分と粒子表面の水和反応を促進し、表面水和物生成過程をコントロールできる事を見出した。この技術を利用して、粒子間の接触面に水和物もしくは水酸化物を生成させ、粒子同士を強固に結合させる事に成功した。写真は本研究によって作製されたアルミナ成形体を焼成前に水中に常温で30日間放置したものである。通常工程によりバインダーレスで作製した試料では、粒子間の結合力が弱いために水中で崩壊するのに対し、本開発手法により作製した試料では水中においても30日間の長期にわたってその形状が保持された。
本技術により有機バインダーを用いる事なく保形性に優れた成形体の作製が可能となり、機械的強度が高く、有機物に起因する欠陥(ボイドやクラック)が少ない高品質のセラミックス焼結体が得ることができる。またセラミックス製造時における投入エネルギーの削減化や、二酸化炭素、有害ガス発生に起因する環境負荷の低減も期待できる上、結合要素にセラミックス材料自身の表面水和物もしくは水酸化物を用いるため、不純物の混入を減らせるという利点もある。
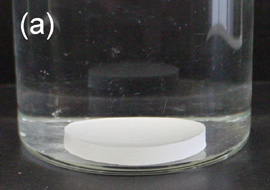 |
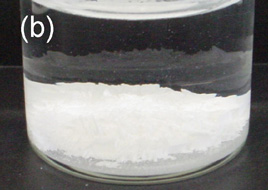 |
写真 作製したアルミナ成形体を焼成前水中に静置し30日間経過したもの。
(a) 本開発手法、水和反応処理済試料:水中で形状を保持している
(b) 通常手法、バインダーレス試料:形状を保たないで崩壊している
|
当該技術の汎用性・取り扱いの簡便性の向上、コストの低減などを目指して更なる検討を進める。また、成形から焼成までの単一化したプロセスの中での応用を目指していく。