独立行政法人 産業技術総合研究所【理事長 吉川 弘之】先進製造プロセス研究部門【部門長 三留 秀人】機能モジュール化研究グループの 山口 十志明 研究員らは、ファインセラミックス技術研究組合および日本ガイシ株式会社【代表取締役社長 松下 雋】と共同で、600℃程度の低温でも高出力が期待されるミクロハニカム構造の固体酸化物型燃料電池(SOFC)の製造プロセス技術の確立に成功した。
SOFCは高効率で信頼性が高く、取り扱いも容易という優れた特徴があるが、これまでは800℃以上の高温で連続運転できる用途に限られていた。用途を拡大するためには、低温作動化や発電モジュールの省スペース化、及び急速起動・停止性能の付与などが望まれていた。今回開発された技術は、室温から数分以内の急速起動・停止運転にも対応でき、自動車の補助電源、小型コジェネ、あるいはポータブル電源等へ適用可能なSOFCの実現が見通せるようになった。
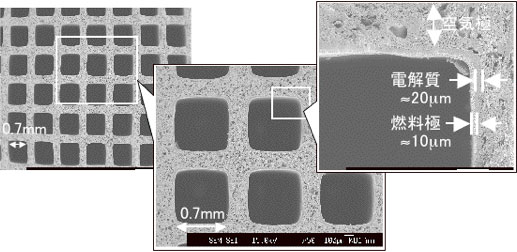 |
マンガン系ペロブスカイト材料(LSM)ミクロハニカム全体/3層構造拡大 |
本成果は、独立行政法人新エネルギー・産業技術総合開発機構 プロジェクト「セラミックリアクター開発」で得られたもので、2007年1月22日から米国フロリダ州で開催予定の“Cocoabeach Conference”他で発表される予定である。
電力を消費する家庭および工場、さらには自動車等の移動体において、必要な場所で必要な時に利用できる小型高効率のエネルギー変換システムとして燃料電池が注目されている。その中でもSOFCはトータルでのエネルギー変換効率が高く将来性が期待されている。しかし、材料の特性からSOFCは800-1000℃の高温での作動が必要であり、また複数のユニットセルを集積して用いるため、高温で連続運転する大型機器に用途が限られていた。家庭や自動車などの応用では、数分で急速作動と停止できる数KWレベルの小型で高効率のSOFCが必要であり、発電モジュールを小型化し、単位体積あたりの発電出力を向上させるための製造プロセス技術の確立が望まれていた。
セラミックハニカムはガス流体中での反応面積が大きいことと構造的な安定性より、自動車等の排ガス処理用の触媒坦持体として利用されている。セラミックハニカムの規則配列した空間へSOFCのような燃料電池セルを構築すれば、小型高密度なSOFC集積モジュールが製造可能である。従来、発電モジュールとしては、セルを1つ1つ製造し集積する工程が必要なため、製造時間は数週間が必要であった。一方、ハニカム型セラミック基材では多数の微細なチャンネルが規則配列した構造体を押出プロセスにより一度に形成できる。これを燃料電池に利用するには技術的な課題として、多数のチャンネルへSOFCとして必要なポーラス電極と緻密電解質の積層構造を高精度に作製することが重要である。これらの技術的課題の解決のために、押出法で作製したマンガン系ペロブスカイト材料(LSM)ポーラスハニカム基材へ様々な電解質ならびに電極を形成する高度スラリーコーティング技術を検討した。
図1左図に示すような15x15mm角のマンガン系ペロブスカイト材料(LSM)ハニカム構造体を混練押出により製造した。スカンジア安定化ジルコニア(ScSZ)やセリア系酸化物(GDC等)等の電解質スラリーにて特別な治具を用いてハニカム中の256個のサブミリ角チャンネルを同時にコートして乾燥後、1300℃で焼成した。その後、セリア系酸化物を含むニッケル(50vol%Ni-GDC)スラリーをコートし1100℃以上で焼成した。その結果、ポーラス電極ハニカム基材中のチャンネル壁面上へ厚さ20µmの緻密な電解質膜と、ポーラス電極としてNiO-GDC層が形成できた。256個のどの空間においても同様な構造が形成できた。形成したハニカムSOFCにおいて数分での急速加熱・冷却試験を行った結果、セル構造の破壊がみられず、急速加熱・冷却が可能であることが分かった。
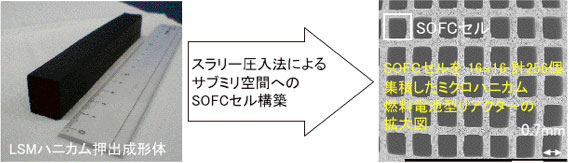 |
図1:LSMハニカム押出成形体およびSOFCセル構築後のミクロハニカム拡大写真 |
製造したセルについて加湿水素での発電試験を行ったところ、LSM-GDC系で中温域における世界最高レベルの発電性能(単位面積当たり)0.23W/cm2(700℃)が実証でき、小型高密度のSOFCセルの形成技術として利用可能なことが分かった。
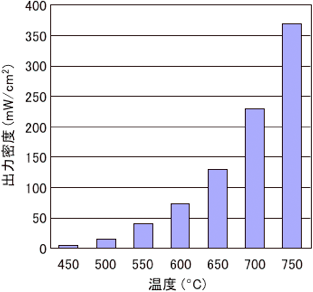 |
図2:セルの出力密度の温度依存性(単位面積当たりの出力密度) |
今回得られた、単一キューブユニットでの高性能化についてのさらなる向上を検討すると共に、ハニカム内での流体拡散制御や熱的制御の検討を進め、複数のキューブユニット連結時の電気エネルギー的な損失を抑制するための技術開発により、最終的に2kW/L以上の発電出力が可能なセラミックリアクターのプロトタイプモジュール創製を目指す。