独立行政法人 産業技術総合研究所【理事長 吉川 弘之】(以下「産総研」という)エネルギー技術研究部門【部門長 大和田野 芳郎】は、固体高分子形燃料電池の中でも家庭用燃料電池として期待の大きい改質ガス型燃料電池に関連して、コスト削減と耐久性向上の鍵をにぎる高性能燃料極触媒の開発に成功した。
家庭用燃料電池では、都市ガスなどの燃料を燃料改質器によって一旦水素に変え、これを燃料電池に送り込んで発電する。しかし、その際改質ガス(水素)中に副生物である一酸化炭素(CO)が不純物として混入し、この濃度が数ppm(数/10,000 %)以上になると、燃料極触媒である白金に対し非常に有害な作用を及ぼし、燃料電池性能が著しく低下するということが問題となっていた。これまで、燃料電池側の対策として、COに耐性を有する白金・ルテニウム合金触媒が用いられてきたが、高価である上に、同触媒でも25 ppm以上のCO混入には対応できなかった。
今回開発した触媒は、白金の補助触媒として有機金属錯体という廉価な材料を用いるという製造方法に特徴があり、しかも従来の実用触媒に比べ性能が格段に優れるという利点を持っている。本触媒の製造方法は、白金の化合物と補助触媒である有機金属錯体を混合し、カーボン粒子の上に担持した状態で「蒸し焼き」することによって作製されるもので、これにより安定な材料を得ることができる。
【図】は燃料電池の運転条件の電位において、COを含む水素ガスを使った時に取り出せる電流値を純水素の場合を100として表したものである。本触媒は100 ppm以上のCO耐性を有しているが、この様な高レベルのCO耐性を有する触媒は世界でも初めてであり、本触媒が実用化されれば、CO低減に対する燃料改質器の厳しい性能基準を緩和することができ、改質器自体のコスト削減という波及効果も有する。
今後、有機金属錯体による触媒の作用機構を解明し、さらに検討・改良を重ねることにより、クリーンエネルギーとして期待されている家庭用燃料電池の実用化に貢献していく予定である。
本研究開発の成果は、独立行政法人 新エネルギー・産業技術総合開発機構【理事長 牧野 力】(以下「NEDO技術開発機構」という)の委託事業「固体高分子形燃料電池システム技術開発(平成12~16年度)」により得られたものである。この成果はギリシャで行われる国際電気化学会(9/14-24)で発表される。
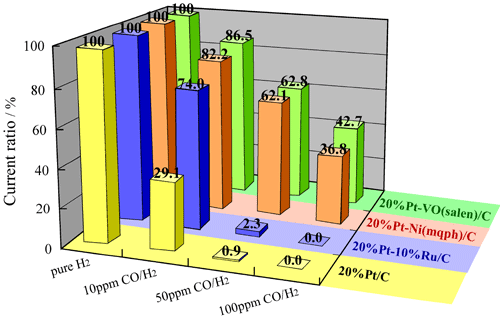 |
図.開発した触媒PtVO(salen)/C、Pt-Ni(mqph)/Cと実用触媒Pt-Ru/C、Pt/Cとの性能比較。COを含む水素燃料での電流値を純水素燃料からの低下率で表示。
|
新しい「発電装置」である燃料電池は、従来の内燃機関に比べ、静粛性に優れており、二酸化炭素(CO2)や大気汚染の原因となる窒素酸化物(NOx)及び硫黄酸化物(SOx)の排出を大きく削減することが可能であるなどの特徴を有することから、クリーンエネルギー源として早期の開発、普及が求められている。
燃料電池では、水素を燃料極に、酸素(空気)を空気極に導入することにより、水素と酸素が結合して水になる反応の化学エネルギーを効率良く電気に変換することができる。
通常家庭用燃料電池などでは、都市ガスなどの燃料から一旦水素を作り出し、この水素を燃料電池に送り込んで発電する、という方式がとられる(これを改質ガス型燃料電池という)。
ところが、都市ガスから水素を作り出す際に、一酸化炭素(CO)という物質が少量生じ、これが燃料極に用いられる触媒である白金に対し非常に有害な作用を及ぼすことが問題となっている(触媒被毒現象という)。燃料電池の著しい性能低下に繋がるこのような被毒現象に対処するためには、COに対する耐性の優れた触媒材料が必須であるが、従来は白金・ルテニウム合金触媒のような高価な材料しか有効でないとされてきた。ルテニウムは白金以上に希少な金属であり、資源的な制約(及びコスト)が問題となっている。しかも白金・ルテニウム合金触媒においても、耐CO被毒性の実用上の限界は25 ppmオーダー程度であり、燃料電池運転開始時に燃料改質器から出てくる水素中の高CO濃度(100 ppm以上)には耐えられないことも問題であった。
このため、白金・ルテニウム合金触媒以上の性能を有する触媒が必要とされ、ここ20年間世界中の研究者が探索を行ってきたが実現できなかった。
産総研ではここ10年ほど固体高分子形燃料電池の研究に取り組んでおり、材料物性研究、システム構成法研究などに関するポテンシャルを蓄積してきた。特に分子設計及び合成の容易な有機金属錯体を用いることにより、従来のものに替わる高性能な触媒の開発を継続して行っており、この分野では国内外の他の機関をリードする実績を有している。今回開発に成功した触媒は、白金の化合物と補助触媒である有機金属錯体を混合し、カーボン粒子の上に担持した状態のものを原料とし、不活性ガス中電気炉で熱処理するという産総研独自の技術開発によってなされた。
なお、本研究開発の成果は、NEDO技術開発機構の委託事業「固体高分子形燃料電池システム技術開発(平成12~16年度)」により得られたものである。
今回原料として用いた錯体はsalenあるいはmqphの略称で呼ばれる、分子形の簡単な化合物である。これらの化合物を種々の金属塩と反応させることにより有機金属錯体を合成した。中心金属としては、ニッケル、鉄、バナジウムなどを選んだ。
触媒作製に際しては、白金の原料となる化合物と有機金属錯体を溶液中で混合した後、カーボン粉末担体に担持させ、乾燥後に熱処理を行い新規混合触媒を合成するという手法によって得られた「蒸し焼き」状態の混合触媒が有効であることが分かった。
燃料電池の構成要素である膜・電極接合体において70℃での半電池試験を行った結果、白金・ルテニウム合金触媒の性能を遙かに上回る、100 ppmオーダーの耐CO被毒性を有する触媒開発に成功した(特許出願中)。
有機金属錯体を原料として用いる利点は、合金触媒に比べ原料価格が大幅に低減できること、分子設計の自由度が高いことから触媒探索の範囲が圧倒的に広いことであり、今後も高性能触媒開発の可能性が期待される。
本触媒の耐久性に関して予備的に行った試験では、純水素を用いた連続100時間運転において、従来の白金・ルテニウム合金触媒と変わらない性能を維持しており、有機金属錯体を用いたことによる耐久性低下は見られなかった。今後引き続き本格的な耐久性試験を行うことにより、実用化の問題をクリアしていく予定である
触媒の製造コストの削減に関しては、ルテニウムの不使用、白金使用量の軽減により、従来の1/3以下に低減可能なことが試算されているが、それ以上に、CO低減に対する燃料改質器の性能基準が緩和されることで、システム全体の大幅なコスト削減が可能となることが期待される。
本触媒がなぜ白金・ルテニウム合金触媒のような従来触媒を大幅に超える性能を発現したのか、その作用機構についてはまだ明らかになっておらず、現在詳細な解明を急いでいるところである。1つの仮説として、有機金属錯体が熱処理の過程で白金と複合体を形成し、白金の電子状態を変えたのではないかと考えている。もしこれが正しければ、従来の白金・ルテニウム合金触媒におけるCO被毒回避機構に代わる新しい作用機構の発見に繋がるもので、今後の基礎研究による解明が期待される。
今回産総研で行った有機金属錯体を原料とする触媒製造技術に関する成果は、燃料電池において必須とされる、安価でかつ大量生産を可能とする技術である点が注目される。また、有機金属錯体の組み合わせによるバリエーションが広がることにより、新たな触媒探索に大きな弾みがつくと予想される。
家庭用燃料電池は「省エネルギー発電」、「環境負荷低減技術」として、今後国民生活になくてはならないものとなるであろうが、現在は材料コスト高、耐久性などその普及までに乗り越えなければならない多くの課題を抱えている。産総研における本触媒技術に関する成果は、燃料電池における材料技術のイノベーションとして大きな一歩となることが期待されている。
今後、高性能燃料極触媒の実証試験を行い、家庭用燃料電池の普及に向けた技術移転を行うとともに、更に安価で性能の優れた触媒探索を推進していく予定である。