独立行政法人産業技術総合研究所【理事長 吉川弘之】(以下、「産総研」という)先進製造プロセス研究部門【部門長 神崎修三】は、日本ガイシ株式会社【代表取締役社長 松下 雋】との共同研究において、新規な発生気体分析装置を開発し、焼成炉内でのバインダー等分解生成物の精密同定法を開発した。
従来の発生気体分析装置はTG-MS(熱重量分析法-質量分析法)が一般的に使用されるが、本新規装置は産総研で開発したスキマーインターフェース【写真参照】とイオン付着質量分析法【図参照】を組み合わることにより、熱分解ガス成分を分析部へ導入する際の変性およびイオン化時のフラグメンテーションの双方を除外したデータ取得が可能であることに特徴があり、より効率的な処理を設計し製造プロセスの低エネルギー化を図るための手段となる。
今後、本分析装置による焼成炉内のon-site分析として、より詳細な検討を進める予定である。
尚、当該成果については、平成16年7月9日、名古屋・栄ナディアパークにて開催される産業技術総合研究所・先進製造プロセス研究部門主催のワークショップ「低環境負荷セラミックスプロセス」で発表する。
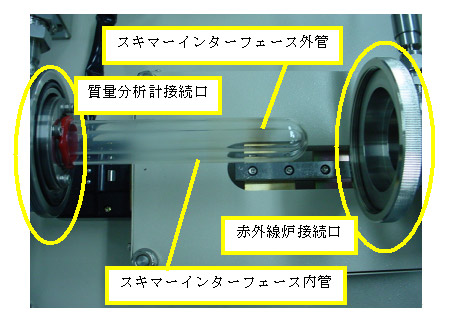 |
写真1 スキマーインターフェース
|
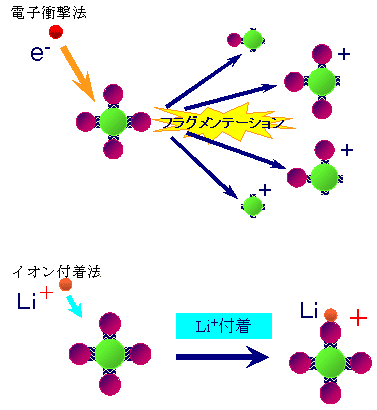 |
図1 イオン付着質量分析法の概念図
一般的な電子衝撃法では分子のフラグメンテーションが起こるが、イオン付着イオン化法では分子イオンのみを生成する
|
現在のファインセラミックス製造工程において、バインダーや助剤といった様々な有機物を添加することは必要不可欠である。これらの有機添加物質は焼成プロセスにて焼き出され、分解生成物として排出される。この分解生成物は悪臭など大気汚染源となり、また高分子種によっては環境ホルモン物質が生成することも懸念され、アフターバーナー等で処理される。より効率的な処理を実現し製造プロセスの低エネルギー化を図るためには、高温となっている焼成炉内での精密な同定が不可欠であるが、GC-MSに用いられる分離カラムやインターフェースにおける熱分解物の変成を検討した事例はほとんどなかった。
産総研と日本ガイシ株式会社は、セラミックス製造プロセスの低エネルギー化実現のため、平成15年度より資金提供型共同研究を行っている。その中で焼成炉における排ガスの精密同定とその有害ガスの浄化技術についての開発を重要テーマとして取り組んでいる。
従来のキャピラリーインターフェースでは熱分解ガス成分の変性という問題点が見いだされていたが、産総研では、旧セラミックス研究部門にて開発されたスキマーインターフェースを用いた分析手法により、さらにイオン化の際のフラグメンテーションにより質量スペクトルピークが重なり合うガス成分でも、イオン付着質量分析法を組み合わせることでフラグメントフリーとなり、バインダー種に応じた特有の熱分解生成物の検出を可能とし、焼成炉内発生ガスの精密な同定を実現する本分析装置の開発に至った。
今回本装置により、ポリビニルアルコールとアクリル樹脂の熱分解挙動もそれぞれ区別して同定できることを実証した。
検出した発生ガスの分子量の情報より、詳細な定性について検討を進める。その結果を炉内ガス成分の無害化処理の設計にフィードバックさせる予定である。
また、各種材料への適用範囲の拡大も図り、本新規手法のデータベース構築も予定している。