加熱時に高重力場を粉末粒子に加えることが可能な遠心焼結技術の開発により以下を満たした
-
厚膜・積層セラミックスの微細構造欠陥(亀裂、粗大気孔、膜剥離)を抑制
-
界面接着強度の向上
-
高重力場の付加によるセラミックスの収縮方向及び収縮率の制御
独立行政法人 産業技術総合研究所【理事長 吉川弘之】(以下「産総研」という)先進製造プロセス研究部門【[部門長 神崎修三】 先進焼結技術研究グループと新東工業株式会社のグループ会社でセラミックス事業を担当する新東ブイセラックス株式会社【代表取締役社長 松浦卓也】は共同で、セラミックス膜・積層セラミックスの新しい焼結技術の開発に成功した。
当該技術の特徴は、加熱時の高重力の負荷により、材料における収縮方向及びその収縮率を制御するものであり、基板とセラミックスの収縮差によって生じる膜の亀裂や剥離の抑制、積層セラミックスの亀裂の低減に有効である。開発した技術は、セラミックスセンサー、圧電素子、固体燃料電池といったセラミックスデバイスの製造技術において、デバイスの性能向上および長寿命化に貢献する。
本研究は、経済産業省からの交付金を原資とし実施する「エネルギー使用合理化技術戦略的開発事業」の一つとして、独立行政法人 新エネルギー・産業技術総合開発機構の委託契約に基づき実施した。
今回の成果は、平成16年2月2日にプレス発表した「遠心力を利用した焼結装置を開発」の焼結装置を使用して開発に至った。
今日のファインセラミックス産業の多くの製品は、その80%以上が電子材料である。特に小型携帯電話の急速な普及や電子機器のダウンサイズ化に伴い、コンデンサー、圧電体、半導体、基板などの各部品等の小型化・集積化が進み、基板上の薄膜セラミックスや厚膜セラミックス、セラミックス/金属積層体や小型形状セラミックスの焼結技術の確立が急務とされている。また、基板への成膜技術や基材への接合技術は、デバイスの性能および寿命に大きく影響をおよぼすため、デバイス製造におけるキーテクノロジーと考えられる。
従来のセラミックス焼結技術では、通常、粉末粒子を原料として用い、粉末粒子を基板にパターニングした後、加熱により粉末粒子同士を結合し、セラミックス膜を形成する。粉末粒子同士の結合にともない、膜は大きく収縮し、その収縮率は一般に10から20%にも及ぶ。しかし、膜の収縮に比べて基板の収縮は小さいため両者の収縮率のミスマッチにより、膜内に粉末粒子の結合を妨げる引張応力が発生する。しかも、この引張応力は界面において最大となり、亀裂の発生・進展、膜の剥離、界面接着強度の低下を引き起こす。
この問題を解決するため、粉末粒子の焼結収縮の方向性、とくに基板界面近傍での粒子の焼結挙動を制御する必要がある。そこで、高重力場を粉末粒子に加えることが可能な遠心焼結により、面方向(界面に対して平行方向)の収縮を低下させる(膜厚方向(界面に対して垂直方向)には大きく収縮させる)焼結技術を開発し、上述の問題を解決することに成功した。
図1に、遠心焼結の原理図を示す。試料をローターの内部に設置し、ローターを高速回転させることにより、粉末粒子に高重力場を加える。重力場は、基板に対し垂直に加えるが、これにより粒子が圧縮される。また、この力は界面で最大となる。この重力場のもとで、試料を加熱し、粉末粒子を焼結させる。現在、1200℃において、780km/s2 (およそ80,000g。gは重力加速度)の重力場を発生させることが可能である。この重力場の制御により、粉末粒子を膜厚方向に収縮させ、面方向での収縮を数%に抑えた。特に、界面近傍ではこの効果が大きく働くため、亀裂の発生を抑制することが可能となる(図2)。また、当該技術は積層セラミックスの焼結にも有効であり、セラミックス内部に含まれる欠陥(粗大気孔、亀裂)への抑制効果も確認している(図3)。
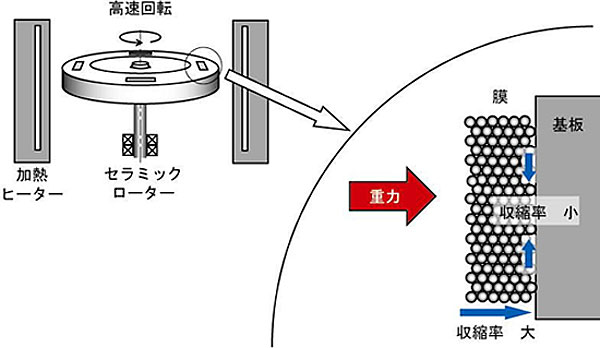 |
図1 原理図
|
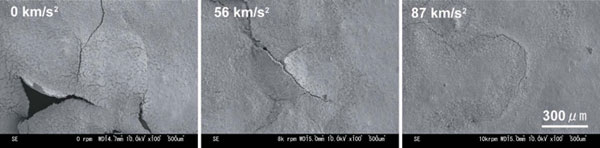 |
図2 厚膜成膜における亀裂発生抑制効果。数値は重力場の大きさ。いずれも成膜温度850℃。
|
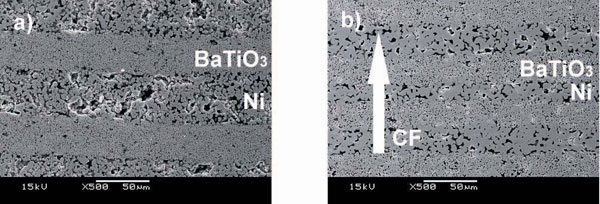 |
図3 積層セラミックスにおける欠陥抑制効果。a)は通常法によるもの。b)は本方法によるもの。図b)中矢印は、重力場負荷方向(重力場は87km/s2)を示している。いずれも焼結温度1000℃。
|
各種セラミックスデバイスへの適用をはかり、同焼結技術のさらなる優位性の確保、デバイス製造技術への実用化を目指す。