- ガラス表面へのナノ加工時の欠損率を従来法と比べて約30分の1に低減
- 光学シミュレーションによりナノ周期構造形成時のガラスの透過率が高くなる原因を解明
- 低反射などの機能を必要な部分に位置選択的に付与した光学部品製造に貢献
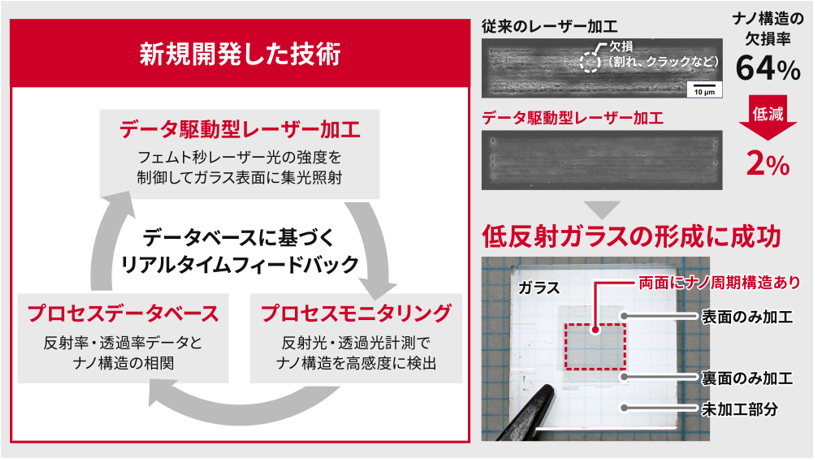
データ駆動型レーザー加工によるナノ周期構造形成の実証
国立研究開発法人 産業技術総合研究所(以下「産総研」という)電子光基礎技術研究部門 奈良崎 愛子 総括研究主幹、高田 英行 主任研究員、吉富 大 主任研究員は、国立大学法人 東京農工大学(以下「農工大」という)大学院工学研究院 先端物理工学部門 宮地 悟代 教授、同大学院学生兼同研究所リサーチアシスタント 長井 大輔 氏(当時)、三善 武碩 氏と共同で、レーザー加工によりガラス表面にナノメートルサイズの周期構造(ナノ周期構造)を低欠損で形成するデータ駆動型レーザー加工技術を開発しました。
ガラスの表面へナノ周期構造を形成することで、低反射表面などの効果を付与することができ、高機能なディスプレイや光学機器などへの応用が期待されています。近年、フェムト秒レーザーパルスを用いてガラス表面をナノ加工する技術や、形成されたナノ周期構造をリアルタイムにモニタリングする技術が開発されました。しかし、ガラス表面へのナノ加工はガラスの表面状態やレーザーの照射条件に大きく依存するため、クラックなど欠損のないナノ周期構造を安定に形成することは難しいという技術課題がありました。
今回、ガラス表面へのナノ加工をリアルタイムにモニタリングしたデータをもとに、フェムト秒レーザーパルスの強度を高速にフィードバック制御できるデータ駆動型レーザー加工システムを構築し、ガラス表面へのナノ加工の欠損率を30分の1に低減しました。この成果は、光の反射・吸収・透過量などが制御された高い機能を、必要な部分に位置選択的に付与した光学部品製造へ貢献します。
なお、この技術の詳細は、2025年2月13日に「Light: Advanced Manufacturing」にオンライン掲載されました。
ガラスは透明で硬い性質を持った材料ですが、表面に光の波長と同程度のナノ構造を形成すると、光の反射・吸収・透過量などの光学特性を自在に制御することができます。例えば、光の反射を抑えたり、波長によって透過率を変えたりする光学表面を実現でき、表面反射を抑えた高機能なディスプレイや可視光を選択的に透過させる窓ガラスなどへの応用が期待されています。
近年、フェムト秒レーザーパルスを複数照射するだけで、ガラス表面にナノ周期構造を直接形成できる現象が報告され、上記の光学表面に応用しようと精力的に研究されてきました。しかし、レーザーの照射条件やガラスの表面状態によっては、加工途中に脆性破壊が起きてしまい、クラックなどの欠損のないナノ周期構造を安定に形成することは難しいという技術課題がありました。
フェムト秒レーザーパルスを用いた材料表面へのナノ周期構造形成技術は、例えば金属材料などに対して産業用途に応用されています。産総研は農工大と共同で、その技術をガラス表面に応用し、精密加工技術の開発に取り組んできました。近年、フェムト秒レーザーパルスによってガラス表面にナノ周期構造を加工する際に、光を用いてガラスの透過率と反射率を計測することで、ナノ周期構造をリアルタイムにモニタリングする技術を開発しました。*1
今回、ガラス表面のナノ周期構造をリアルタイムにモニタリングしたデータをもとに、フェムト秒レーザーパルスの強度を高速にフィードバック制御できるデータ駆動型レーザー加工システムの構築に取り組みました。
ガラス表面に光の波長以下の大きさのナノ周期構造があると、モスアイ効果により、表面の反射率は減少し、透過率が増加します。私たちはこの現象をレーザー加工中のナノ周期構造形成の検出対象として着目しました(図1a)。実験では、フェムト秒レーザーパルスを合成石英ガラス表面に対物レンズで集光照射しながら、合成石英ガラスを一定の速度で動かすことでレーザー加工しました。そして、このガラス表面に、波長660 nmと850 nmの発光ダイオードをそれぞれ同軸落射、透過照明光源として使用し、レーザー加工表面の波長ごとの顕微画像を2台のCMOSカメラで取得しました。得られた顕微画像を、あらかじめ取得しておいたレーザー加工をしていない領域の顕微画像と比較することにより、未加工領域からの反射光強度に対するレーザー加工領域からの反射光強度の比(相対反射率)と、未加工領域からの透過光強度に対するレーザー加工領域からの透過光強度の比(相対透過率)を求めました。さらに、加工後の合成石英ガラス基板の表面と断面を走査型電子顕微鏡(SEM)で観察し、レーザー加工時にモニタリングした相対反射率と相対透過率とを紐づけたプロセスデータベースを作成しました(図1b)。その結果、図1bの赤丸で示す相対反射率・透過率において、周期が約200 nm、深さが約1 µmの直線状のナノ周期構造が均一に形成されることを見いだしました。
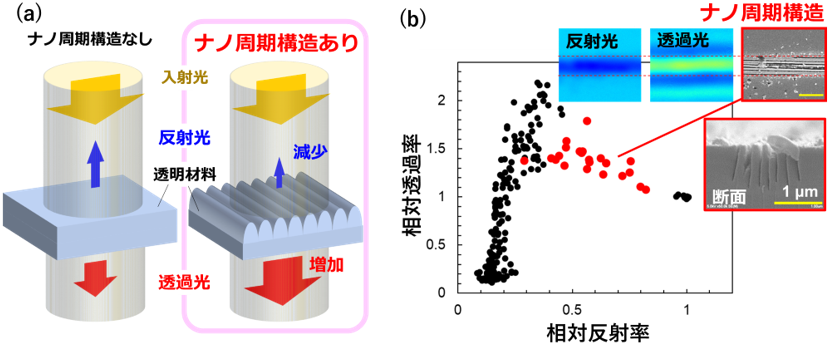
図1 (a)ナノ周期構造の検出原理と(b)レーザー加工時モニタリングデータ(相対反射率・相対透過率)と加工表面の相関
※原論文の図を引用・改変したものを使用しています。
次に、レーザー照射中の相対反射率と相対透過率が所望のナノ周期構造を形成する値となるように、フェムト秒レーザーパルスの強度をフィードバック制御すると、1ライン照射領域内(長さ1 mm)でのナノ周期構造の欠損率は2.4%となり、制御しない場合の24.4%と比較して、約10分の1に低減できることを示しました。さらに、横100 µm、縦20 µmの領域をレーザー加工したところ、制御しない場合ではナノ周期構造の欠損率は約64%であった一方で、制御した場合では約2%であり、データ駆動型レーザー加工システムによるフィードバック制御によって欠損率を約30分の1に低減することができました(図2)。本フィードバック制御を用いて合成石英ガラス両面にナノ周期構造を形成することで、光の透過率が大きい低反射ガラスの形成に成功しました(概要図)。
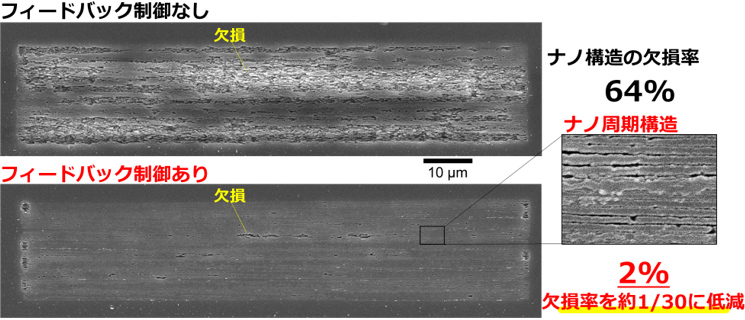
図2 フィードバック制御によるナノ周期構造の欠損率の違い
さらに、本手法中のプロセスモニタリングにおいて重要な要素となるナノ周期構造形成と透過率の関係をより詳細に調べました。レーザー加工で表面にナノ周期構造を形成することで反射率が低減されますが、プロセスモニタリングでは、そこから計算される透過率を大きく超えた値(約1.5倍)が観測されます。その原因を解明するため、ナノ構造を有するガラス表面を透過したLED光の電場の振幅と位相の分布を、有限差分時間領域法により数値計算シミュレーションしました。その結果、ナノ周期構造を持つガラス表面を透過した光の電場振幅(明るさ)は低下しないことがわかりました(図3左)。さらに、ナノ周期構造形成領域で波面がゆがむ結果(図3右)、光の干渉が生じ計測カメラ上で透過光強度が上昇しているように見えることがわかりました。これは今後、本手法の高速化といった、さらなる効率化のための重要な知見となります。
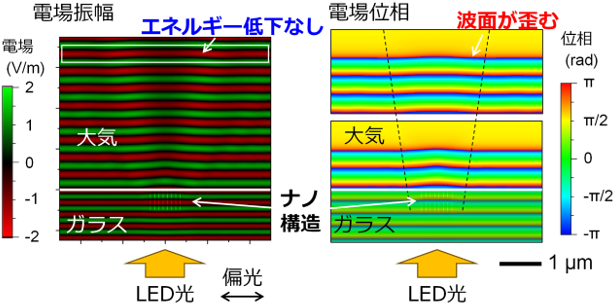
図3 ナノ周期構造を有するガラスを透過する光電場の振幅と位相の分布シミュレーション結果
※原論文の図を引用・改変したものを使用しています。
開発したデータ駆動型レーザー加工システムは、多成分ガラスを含む多様なガラスの他に、サファイアなどにも適用可能なことから、多様な硬脆透明材料において、複数の工程や薬剤が不要で高品位な表面ナノ構造形成技術としても期待できます。また、レーザーパルスを照射する位置を変えるだけで加工部分を移動できるため、加工材料の大きさに制限がなく、メートルサイズの領域へのナノ加工も容易です。現在、このような大面積領域にナノメートルサイズの微細加工を行える技術はなく、例えば、メタマテリアル表面形成、構造色表面加工、広帯域の無反射表面形成、照明光源の指向性表面形成、などへの応用も期待されます。今回の成果は、安定形成のためのプロセスモニタリング速度に制限がある装置での基礎実証であり、今後は、より高速・大面積に対応可能な装置構成の検討を進め、本技術を製造ラインで実際に適用するための技術開発に努めていきます。
掲載誌:Light: Advanced Manufacturing
論文タイトル:Stable fabrication of femtosecond-laser-induced periodic nanostructures on glass by using real-time monitoring and active feedback control
著者:Godai Miyaji, Daisuke Nagai, Takemichi Miyoshi, Hideyuki Takada, Dai Yoshitomi, and Aiko Narazaki
DOI:10.37188/lam.2025.003