国立研究開発法人 産業技術総合研究所【理事長 中鉢 良治】(以下「産総研」という)物理計測標準研究部門【研究部門長 中村 安宏】応用電気標準研究グループ 天谷 康孝 主任研究員、藤木 弘之 研究グループ長は熱電材料の性能を示す「ゼーベック係数」を簡便にかつ精度良く測定できる手法を開発した。
金属や半導体に温度差を与えると、内部の電子が移動し、温度差に応じた電圧が生じる。この原理を利用して熱エネルギーを電気エネルギーに変換する熱電材料は、従来、有効利用が難しかった工場や自動車などからの廃熱(未利用熱)を電気に変換して利用するための材料として期待されている。優れた熱電材料を開発するには、熱-電気変換の性能指標であるゼーベック係数を正確に求める必要があるが、通常、ゼーベック係数を求めるためには、複雑な装置による長時間の測定が必要であった。
産総研では、これまで、電圧、抵抗など電気量の精密測定技術を開発し、国家計量標準として確立してきた。今回、これらの技術を活用し、直流電流だけでなく交流電流を用いることで、熱物性値を測定せずに、ゼーベック係数を求める新たな測定手法を開発した。今回開発した手法により、従来、1日がかりであった測定時間が10分の1以下に短縮され、また、10 %程度であった精度も2 %まで向上できた。
今後、熱電材料の生産効率や品質の向上、新材料の探索への貢献が期待される。
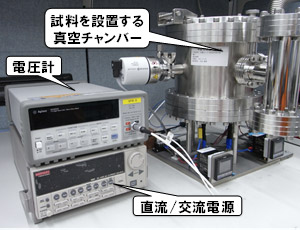 |
今回開発したゼーベック係数測定装置のプロトタイプ機 |
近年、工場や自動車などからの廃熱(未利用熱)を積極的に利用しようとする取り組みがなされてきたが、未だ十分とは言えない。熱電材料は熱エネルギーを電気エネルギーに変換できる特殊な合金や半導体で、廃熱を電気に変換して、有効活用できる材料として期待されている。優れた熱電材料を開発するには、熱-電気変換の性能指標であるゼーベック係数を正確に測定する必要がある。ゼーベック係数が大きいほど熱電材料の性能は高く、最先端の材料開発では、ゼーベック係数にして1 %単位で性能向上を競っているので、正確で迅速なゼーベック係数の測定手法が求められている。しかし、従来の絶対測定法では、高度で複雑な装置で長時間の測定を行い、熱伝導率や放射率などの熱物性値を正確に測定する必要があり、得られるゼーベック係数の精度は10 %程度であった。このため、熱電材料の開発や製造現場では、より簡便に、かつ、より高い精度でゼーベック係数を測定できる手法が望まれていた。
産総研では、これまで、電圧、抵抗などの電気量の精密測定技術を開発し、国家計量標準として確立してきた。これらの精密測定技術を活用し、熱電材料のゼーベック係数を短時間、かつ高い精度で測定できる手法の開発に取組んだ。
なお、本研究開発は、埼玉県先端産業創造プロジェクト「未利用熱発電のための高耐久型熱電発電モジュールの開発」(平成28~30年度)による支援を受けて行った。
金属や半導体に温度差を与えると、内部の電子が移動し、温度差に応じた電圧が生じる。温度差と電圧の比例係数であるゼーベック係数の測定では、通常、測定試料の両端に温度差を与え、直流電流を流し、電子が運ぶ熱によって生じる試料の温度変化を測定する(図1左)。その際、試料の長さ、断面積といった寸法に加え、試料の熱伝導率、放射率などの熱物性値が必要となる。熱物性値の測定には、高度な熱制御系を持つ複雑な装置が必要であり、測定にも時間を要していた。
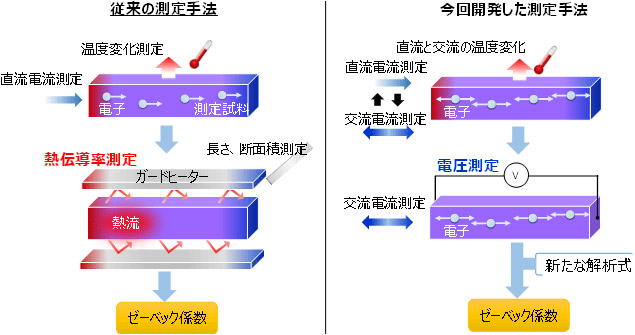 |
図1 従来のゼーベック係数の測定手法(左)と今回開発した手法(右)の原理図 |
一方、今回、開発した手法では、両端に温度差を与えた試料に直流電流を流して、試料の温度変化を測定し、次にスイッチなどで切り替えて交流電流を流して、温度変化に加えて電圧を測定する(図1右)。交流電流の場合、電子の移動方向の変化に応じた熱の吸収・放出が繰り返されるため、電子が熱を運ぶことによる温度変化は生じない。ここで、交流と直流を流した際の試料の温度変化の差と試料両端の電圧の測定値を、熱解析より新たに導き出した式に代入することで、試料のゼーベック係数が得られる。すなわち、熱伝導率などの熱物性値を測定せずにゼーベック係数を求めることができる。
図2に、今回開発した手法を用いて、代表的な熱電材料であるビスマス・テルル合金のゼーベック係数の温度依存性を、試料両端の温度の平均温度が50 ℃から150 ℃の温度範囲で測定した結果を示す。熱物性値を測定しなくてよいため、従来、1温度あたり1日程度要していた測定時間を約1時間に短縮することができた。また、従来の絶対測定法では測定精度は10 %程度であったが、今回の絶対測定法では約2 %の測定精度に向上していることが確認できた。
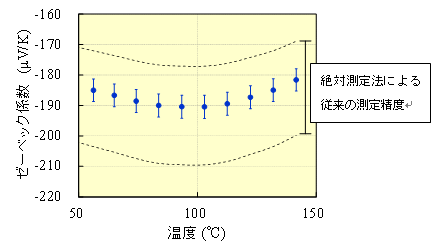 |
図2 ビスマス・テルル合金のゼーベック係数の測定結果 |
今後は、より広い温度範囲でゼーベック係数を計測できるよう測定装置の改良を進める。また、自動計測できる支援ソフトウェアなどを構築し、より使いやすい計測システムを開発する。また、従来の手法では困難であった薄膜材料の測定にも取組み、新材料の探索に寄与する。